Exploring Advanced Strategies in Pharmaceutical Product Manufacturing
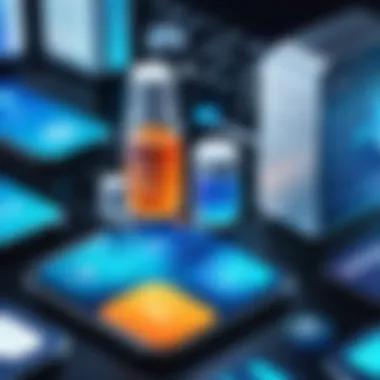
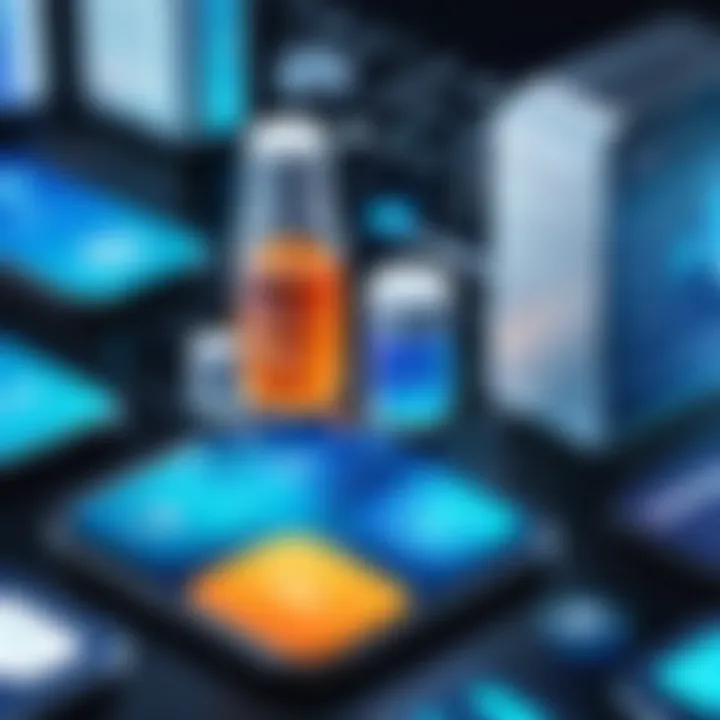
Industry Overview
In the realm of pharmaceutical product manufacturing, a landscape of innovation and precision unfolds. Here, cutting-edge techniques intertwine with stringent regulatory considerations and meticulously crafted quality assurance protocols. Each stage of the manufacturing process, from sourcing raw materials to the final delivery of products, undergoes thorough scrutiny to uphold not just safety and efficacy but also emulate industry-best standards. As the pharmaceutical industry continues to evolve, the spotlight on innovative approaches in product manufacturing shines ever brighter.
Introduction
Pharmaceutical product manufacturing is a critical component of the healthcare industry where innovation and precision are paramount. In this article, we delve into the advancements and novel approaches revolutionizing this sector, ensuring safety, quality, and compliance throughout the production chain.
Overview of Pharmaceutical Product Manufacturing
Historical Evolution
The historical evolution of pharmaceutical product manufacturing traces back to ancient civilizations, where natural remedies were utilized for healing. Over time, scientific discoveries and technological advancements shaped the industry into what it is today. Understanding the historical roots provides valuable insights into the development of modern pharmaceutical practices, highlighting the progression from traditional remedies to sophisticated drug formulations.
Current Landscape
The current landscape of pharmaceutical product manufacturing is characterized by advanced technologies, stringent regulations, and a focus on efficacy and patient safety. Industry players leverage cutting-edge equipment and processes to meet the growing demand for diverse drug products while meeting regulatory standards. Analyzing the current landscape offers a glimpse into the dynamic and evolving nature of pharmaceutical manufacturing, showcasing trends such as personalized medicine and Industry 4.0 integration.
Role in Healthcare Industry
The role of pharmaceutical product manufacturing in the healthcare industry is pivotal, as it directly influences patient outcomes and public health. By producing high-quality and effective medications, manufacturers contribute to disease management, treatment efficacy, and overall well-being. This section explores how pharmaceutical manufacturing intersects with clinical practice, regulatory oversight, and patient care, emphasizing its indispensable role in ensuring the availability of safe and reliable medications.
Regulatory Framework
FDA Guidelines
The FDA guidelines encompass a comprehensive set of regulations that govern various aspects of pharmaceutical production, from drug development to market approval. Compliance with FDA guidelines is mandatory for all pharmaceutical manufacturers operating in the United States, ensuring the safety, efficacy, and quality of marketed drugs. Adhering to these guidelines enables companies to navigate the regulatory landscape efficiently, maintaining public trust and regulatory compliance.
Good Manufacturing Practices (GMP)
Good Manufacturing Practices (GMP) are internationally recognized quality standards that dictate the manufacturing processes for pharmaceutical products. Implementing GMP principles ensures consistent product quality, safety, and efficacy, safeguarding public health. By adhering to GMP guidelines, manufacturers can minimize risks associated with product contamination, variability, and substandard quality, fostering trust among consumers and regulatory bodies.
International Regulations
International regulations harmonize standards across the global pharmaceutical industry, promoting uniformity in drug manufacturing practices and quality assurance. Compliance with international regulations is essential for pharmaceutical manufacturers engaged in cross-border trade, ensuring that products meet stringent quality and safety requirements worldwide. Understanding and adhering to international regulations empower manufacturers to access international markets, expand their presence, and uphold their commitment to producing safe and effective medications.
Raw Material Sourcing
Raw material sourcing holds a critical position in the realm of pharmaceutical product manufacturing as it serves as the foundation for the entire production process. The quality and integrity of raw materials directly impact the efficacy and safety of the final product, making raw material sourcing a pivotal aspect to be meticulously handled. In this article, we will delve deep into the significance of raw material sourcing, exploring various elements that contribute to ensuring high standards in pharmaceutical manufacturing.
Quality Assessment of Raw Materials
Supplier Selection Criteria
Supplier selection criteria play a vital role in determining the reliability and consistency of the raw materials procured. By establishing stringent criteria for selecting suppliers, pharmaceutical manufacturers can mitigate the risks associated with inferior raw materials and uphold strict quality standards. The key characteristic of supplier selection criteria lies in its ability to evaluate suppliers based on predefined parameters such as reputation, compliance with regulations, previous performance, and adherence to quality standards. This approach ensures that only suppliers meeting the necessary standards are chosen, thereby enhancing the overall quality of pharmaceutical products.
Traceability Measures
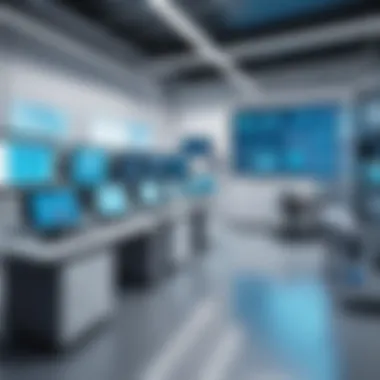
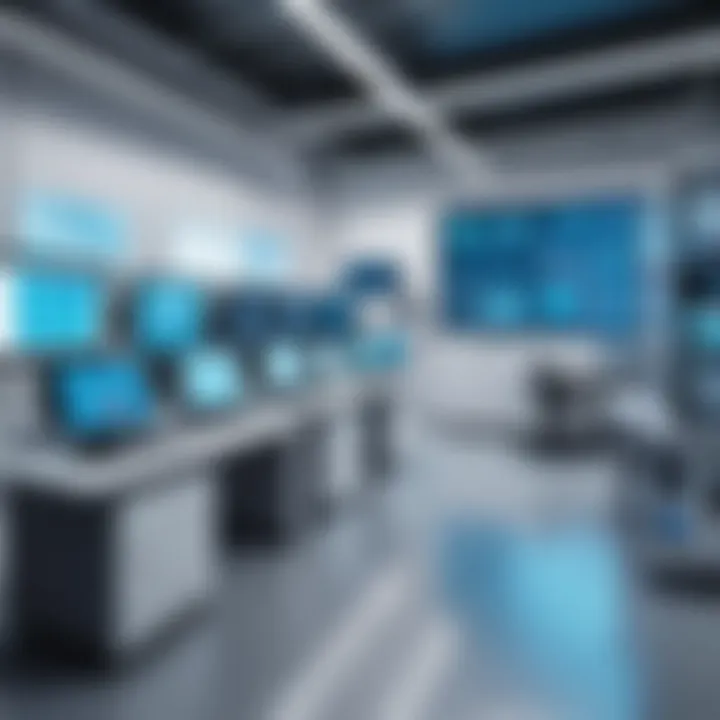
Traceability measures are essential in ensuring transparency and accountability throughout the supply chain. By implementing traceability measures, manufacturers can track the flow of raw materials from their source to the final product, enabling swift identification and resolution of any anomalies. The key characteristic of traceability measures lies in their capacity to provide a comprehensive overview of the raw material journey, including origin, handling, and storage conditions. This level of traceability enhances quality control efforts and facilitates prompt action in case of quality deviations or non-compliance.
Risk Assessment
Risk assessment forms a critical component of quality assurance in raw material sourcing. By conducting thorough risk assessments, manufacturers can identify potential vulnerabilities in the supply chain and implement preemptive measures to mitigate risks. The key characteristic of risk assessment is its proactive approach to identifying and addressing potential threats to product quality. By assessing factors such as supplier reliability, geographical risks, and market fluctuations, pharmaceutical companies can fortify their raw material sourcing strategies and uphold consistent quality standards.
Supply Chain Management
Supply chain management encompasses a multifaceted approach to optimizing the procurement, logistics, and quality control of raw materials. In the context of this article, supply chain management plays a pivotal role in ensuring streamlined operations and minimizing risks across the supply chain.
Logistics Planning
Logistics planning focuses on strategic coordination and optimization of transportation and distribution channels to enhance efficiency and minimize costs. By meticulously planning logistics operations, pharmaceutical manufacturers can avoid bottlenecks, delays, and unnecessary expenses in the raw material procurement process. The key characteristic of logistics planning lies in its ability to synchronize various elements of the supply chain, including transportation modes, route planning, and delivery schedules, to ensure timely and cost-effective raw material supply.
Inventory Control
Inventory control entails the effective management of raw material stocks to prevent shortages, overages, or quality issues. By implementing robust inventory control mechanisms, manufacturers can maintain optimal stock levels, minimize wastage, and ensure consistent production schedules. The key characteristic of inventory control is its ability to balance supply and demand dynamics, thereby preventing stockouts or excess inventory situations. Through accurate demand forecasting and inventory monitoring, pharmaceutical companies can optimize their production processes and maintain uninterrupted supply chains.
Quality Control Checks
Quality control checks form a crucial component of supply chain management, offering systematic inspections and assessments to safeguard product quality. By conducting stringent quality checks at various stages of the supply chain, manufacturers can detect defects, deviations, or contamination risks in raw materials. The key characteristic of quality control checks lies in their ability to uphold stringent quality standards and compliance requirements at every stage of the manufacturing process. Through regular quality assessments and inspections, pharmaceutical companies can ensure that only high-quality raw materials are utilized, thereby enhancing the overall safety and efficacy of their products.
Manufacturing Process
In the realm of pharmaceutical product manufacturing, the Manufacturing Process holds paramount importance. The intricate steps involved in this crucial phase determine the quality, efficacy, and safety of the final product. Manufacturers meticulously orchestrate various aspects, from formulation development to quality assurance protocols, to ensure compliance with regulatory standards and industry best practices. By focusing on optimizing every stage of the process, manufacturers aim to streamline operations, enhance product quality, and mitigate risks. The evolution of Manufacturing Processes reflects the industry's commitment to innovation and efficiency.
Formulation Development
Optimization Techniques:
Optimization Techniques play a pivotal role in refining the formulation development process. These techniques encompass a range of methodologies aimed at enhancing product efficacy, stability, and manufacturability. By utilizing advanced optimization tools and technologies, manufacturers can fine-tune formulations to meet stringent regulatory requirements and consumer demands. The key characteristic of Optimization Techniques lies in their ability to systematically analyze and improve formulation parameters, such as ingredient ratios, processing conditions, and compatibility assessments. This meticulous optimization approach not only accelerates product development timelines but also ensures consistent product performance and quality.
Dosage Form Selection:
The selection of the appropriate dosage form is a critical decision in the formulation development stage. Different dosage forms, such as tablets, capsules, liquids, and topical formulations, offer distinct advantages in terms of bioavailability, patient compliance, and manufacturing efficiency. Manufacturers must carefully evaluate the unique characteristics of each dosage form, considering factors like dosing frequency, patient preferences, and therapeutic requirements. By choosing the most suitable dosage form, manufacturers can optimize drug delivery outcomes, enhance patient experience, and differentiate their products in the competitive market landscape.
Scale-Up Process:
The Scale-Up Process marks a significant transition from laboratory-scale formulation to full-scale production. This phase involves replicating and optimizing the formulation under large-scale manufacturing conditions to ensure consistency and scalability. Manufacturers must navigate challenges related to equipment compatibility, batch size adjustments, and process validation during scale-up. The unique feature of the Scale-Up Process lies in its ability to bridge the gap between research and commercialization while maintaining product integrity and performance. Effective scale-up strategies pave the way for seamless production workflows, cost efficiency, and timely market entry.
Equipment and Facility Design
Automation Integration:
Automation Integration revolutionizes pharmaceutical manufacturing by enhancing efficiency and precision in production processes. Automated systems enable seamless data exchange, real-time monitoring, and quality control, minimizing human errors and variability. The key characteristic of Automation Integration is its capacity to synchronize equipment, instruments, and processes for optimal performance and regulatory compliance. By embracing automation, manufacturers can expedite production timelines, minimize downtime, and adapt to evolving market demands with agility.
Cleanroom Standards:
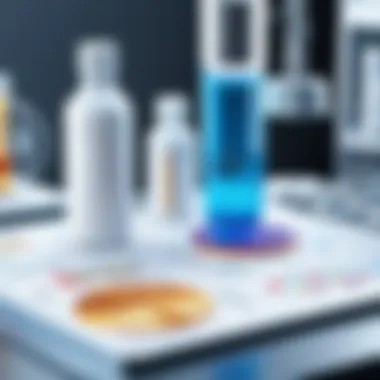
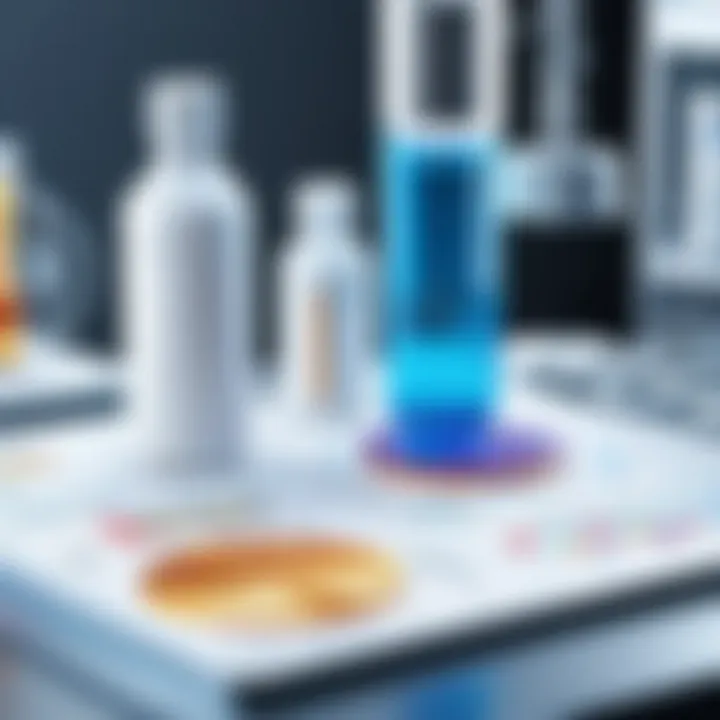
Adhering to stringent Cleanroom Standards is essential to uphold product quality and safety in pharmaceutical manufacturing. Cleanrooms provide controlled environments free from contaminants, ensuring the integrity of raw materials and finished products. The key characteristic of Cleanroom Standards lies in their ability to regulate air quality, temperature, humidity, and particle levels to meet regulatory standards. By maintaining cleanroom integrity, manufacturers can reduce the risk of product contamination, enhance worker safety, and uphold regulatory compliance seamlessly.
Environmental Controls:
Environmental Controls play a critical role in promoting sustainability and ecological responsibility in pharmaceutical manufacturing. By implementing eco-friendly technologies and practices, manufacturers can reduce waste generation, energy consumption, and environmental impact. The unique feature of Environmental Controls lies in their capacity to optimize resource utilization, minimize carbon footprint, and comply with environmental regulations. By integrating environmentally conscious strategies into facility design, manufacturers demonstrate corporate stewardship and embrace sustainable manufacturing practices.
Quality Assurance Protocols
In-process Testing:
In-process Testing serves as a proactive quality assurance measure to identify deviations and ensure product conformance throughout the manufacturing process. By conducting real-time evaluations and analyses at key stages of production, manufacturers can detect anomalies, correct errors, and maintain product integrity. The key characteristic of In-process Testing is its role in preventing defects, optimizing process efficiency, and minimizing rework. Leveraging advanced analytical techniques and instrumentation, manufacturers can verify product quality, compliance, and uniformity, fostering consumer trust and regulatory acceptance.
Final Product Inspection:
The Final Product Inspection phase signifies the culminating step in quality assurance, where finished products undergo rigorous evaluation before distribution. Manufacturers employ comprehensive inspection protocols, including visual assessments, dimensional checks, and functional tests, to validate product quality and safety. The key characteristic of Final Product Inspection is its ability to detect deviations, defects, and non-conformities, ensuring that only compliant products reach the market. Through meticulous inspection procedures, manufacturers uphold brand reputation, compliance standards, and customer satisfaction, reinforcing their commitment to excellence.
Compliance Audits:
Conducting Compliance Audits is imperative for pharmaceutical manufacturers to demonstrate adherence to regulatory requirements and quality standards. Audits involve systematic reviews, documentation assessments, and on-site inspections to validate compliance with GMP regulations, FDA guidelines, and international quality standards. The unique feature of Compliance Audits lies in their function to identify non-compliance issues, implement corrective actions, and drive continuous improvement. By proactively addressing audit findings, manufacturers can fortify their quality management systems, mitigate risks, and instill confidence among stakeholders.
Packaging and Labeling
In this crucial stage of the pharmaceutical product manufacturing process, Packaging and Labeling play a vital role in ensuring product safety, integrity, and regulatory compliance. Packaging serves as the primary protective barrier for the pharmaceutical product, safeguarding it from external contaminants, physical damage, and tampering. Moreover, proper labeling is essential for providing vital information to consumers, healthcare professionals, and regulatory bodies. Effective Packaging and Labeling not only contribute to the overall quality of the product but also help in brand identification and differentiation from competitors.
Design Considerations
-#### Child-Resistant Packaging: Child-Resistant Packaging stands out as a key component in pharmaceutical packaging design, especially when considering safety concerns, particularly for medications that may be harmful if accidentally ingested. The distinctive feature of Child-Resistant Packaging is its ability to reduce the risk of unintentional access by children or vulnerable individuals, thereby enhancing safety and preventing accidental misuse. While adding an extra layer of protection, this type of packaging may pose challenges for some users, especially those with dexterity issues. However, its benefits in preventing unintentional ingestion far outweigh any minor inconveniences, making it a preferred choice for pharmaceutical products requiring enhanced safety measures in this article.
-#### Tamper-Evident Seals: Tamper-Evident Seals are another critical element in pharmaceutical packaging design, primarily serving to ensure product integrity and safety by providing visible evidence of tampering or unauthorized access. A key characteristic of Tamper-Evident Seals is their ability to indicate if a product has been compromised, thereby enhancing consumer confidence and trust in the product's authenticity. Despite their effectiveness in detecting tampering, some advanced counterfeit methods may still circumvent these seals, highlighting the constant need for innovation in tamper-evident technologies. When considering the balance between security and ease of access, Tamper-Evident Seals prove to be a beneficial choice for pharmaceutical products seeking to enhance product security and consumer trust.
-#### Barcoding Technologies: Barcoding Technologies play a crucial role in pharmaceutical packaging and labeling, facilitating efficient inventory management, authentication, and track-and-trace capabilities throughout the supply chain. The key characteristic of Barcoding Technologies lies in their ability to store and retrieve product information quickly and accurately, aiding in the seamless identification and tracking of pharmaceutical products. This technology streamlines processes, minimizes errors, and enhances supply chain visibility, leading to improved regulatory compliance and consumer safety. Although Barcoding Technologies offer numerous benefits, challenges related to standardization and compatibility between different systems may arise, necessitating continual adaptation and integration to ensure optimal functionality in this article.
Regulatory Compliance
-#### Serialization Requirements: Serialization Requirements represent a critical aspect of regulatory compliance in pharmaceutical manufacturing, aiming to prevent counterfeiting, ensure product traceability, and protect public health. A key characteristic of Serialization Requirements is the unique identification of each product unit through assigned serial numbers, enabling precise tracking and authentication throughout the supply chain. This serialization process enhances supply chain security, reduces the risk of counterfeit products entering the market, and enables swift response in case of product recalls or quality issues. While the implementation of serialization can incur initial costs and operational changes, the long-term benefits in terms of regulatory adherence, consumer safety, and market trust make it a worthwhile investment for pharmaceutical manufacturers.
-#### Labeling Accuracy: Accurate labeling is paramount in pharmaceutical packaging, ensuring that essential information such as dosage instructions, expiry dates, and product identifiers is correctly presented to users. The key characteristic of Labeling Accuracy is its role in promoting safe and effective product usage while complying with regulatory requirements and industry standards. Precision in labeling not only helps consumers make informed decisions but also contributes to medication adherence and reduces the risk of medication errors. However, challenges such as packaging size constraints and regulatory updates may necessitate continuous monitoring and adjustment to maintain labeling accuracy in this article.
-#### Adverse Event Reporting: The systematic reporting of Adverse Events is a fundamental aspect of regulatory compliance and pharmacovigilance in the pharmaceutical industry, aiming to monitor the safety and efficacy of products post-market approval. A key characteristic of Adverse Event Reporting is the collection, documentation, and evaluation of adverse reactions or unexpected incidents associated with pharmaceutical products. This information aids regulatory authorities, healthcare professionals, and manufacturers in identifying potential risks, improving product safety profiles, and implementing necessary interventions. Despite the importance of adverse event reporting, challenges such as underreporting, incomplete data, and varying reporting standards may impact the reliability and effectiveness of pharmacovigilance systems, emphasizing the need for continual surveillance and improvement for this article.
Distribution and Logistics
Distribution and Logistics play a pivotal role in the pharmaceutical product manufacturing process. Efficient management of distribution and logistics ensures timely delivery of products while maintaining their quality and efficacy. In the pharmaceutical industry, ensuring that products are stored, transported, and handled under optimal conditions is crucial to prevent any compromise in their integrity and effectiveness. Factors such as temperature control, storage conditions, and transportation practices directly impact the safety and efficacy of pharmaceutical products.
Cold Chain Management
Temperature Monitoring
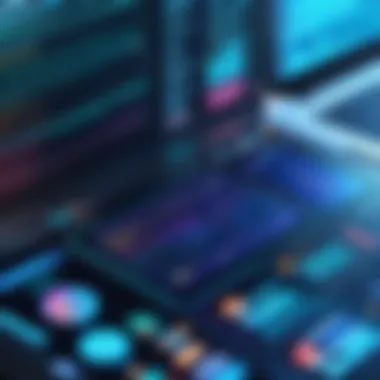
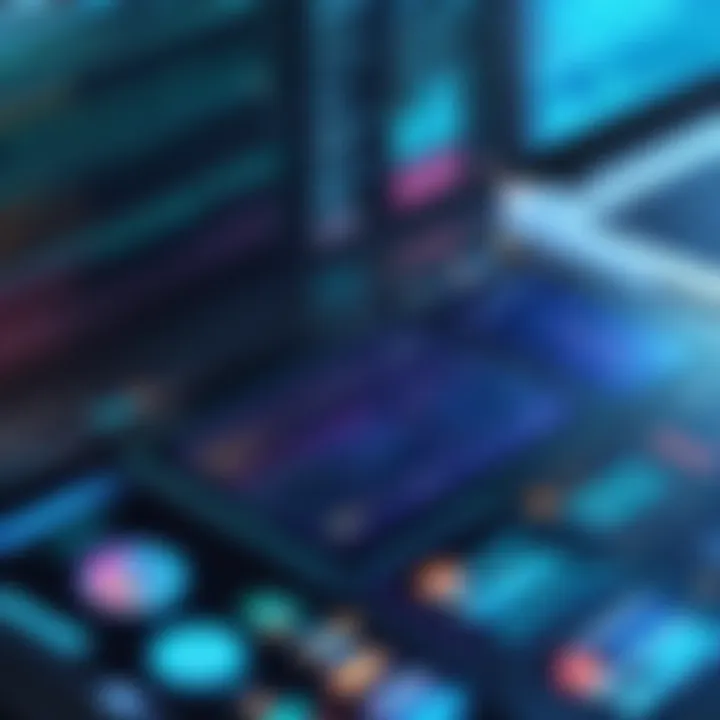
Temperature Monitoring is a critical aspect of Cold Chain Management in pharmaceutical product distribution. Maintaining the required temperature range throughout the distribution process is essential to preserve the stability and effectiveness of temperature-sensitive medications. The key characteristic of Temperature Monitoring is its real-time tracking capabilities, allowing manufacturers to monitor and adjust temperature levels to prevent product degradation. This proactive approach enhances the overall quality of pharmaceutical products and reduces the risk of spoilage.
Storage Conditions
Storage Conditions play a vital role in preserving the integrity of pharmaceutical products during distribution and storage. Proper storage conditions, including controlled temperature and humidity levels, protect the products from degradation and ensure their longevity. The key characteristic of Storage Conditions is their ability to create an environment that minimizes the interactions between products and external factors that could compromise their quality. By adhering to specific storage guidelines, pharmaceutical companies can guarantee the efficacy of their products.
Transportation Best Practices
Effective Transportation Best Practices are essential for maintaining the quality and safety of pharmaceutical products during transit. Implementing secure and efficient transportation methods helps prevent product damage and contamination. The key characteristic of Transportation Best Practices lies in their focus on adherence to strict regulations and protocols to ensure the safe delivery of pharmaceutical products. By prioritizing factors such as proper handling, packaging, and tracking, companies can mitigate risks associated with transportation and uphold product quality.
Traceability Systems
Track-and-Trace Technologies
Track-and-Trace Technologies have revolutionized pharmaceutical supply chain management by enhancing traceability and transparency. These technologies enable manufacturers to monitor the movement of products from production to distribution, ensuring authenticity and compliance. The key characteristic of Track-and-Trace Technologies is their ability to provide real-time visibility into product location and status, enabling quick response to any issues or discrepancies. This feature enhances security, reduces the risk of counterfeiting, and improves overall supply chain efficiency.
Repackaging Controls
Repackaging Controls are integral to maintaining the quality and safety of pharmaceutical products during repackaging processes. Implementing strict controls ensures that repackaged products meet regulatory standards and retain their original quality. The key characteristic of Repackaging Controls is their emphasis on accurate labeling, packaging integrity, and contamination prevention. By adhering to stringent repackaging guidelines, companies can safeguard product integrity and consumer health.
Recall Procedures
Effective Recall Procedures are crucial for responding promptly to potential safety issues or quality concerns with pharmaceutical products. Having well-defined recall procedures in place enables companies to take swift action to remove faulty products from the market. The key characteristic of Recall Procedures is their systematic approach to identifying, isolating, and resolving product issues to protect consumer safety. By conducting mock recalls and regular testing, companies can enhance their preparedness for any recall situation and maintain public confidence in their products.
Conclusion
Future Trends in Pharmaceutical Manufacturing
Industry 4. Integration:
Industry 4.0 Integration marks a paradigm shift in the pharmaceutical manufacturing landscape, revolutionizing processes through automation, data exchange, and artificial intelligence. This integration enhances efficiency, accuracy, and scalability, leading to streamlined operations and enhanced productivity. Its real-time monitoring capabilities and predictive maintenance features offer unprecedented insights for proactive decision-making and optimization. While the benefits are significant, challenges such as cybersecurity risks and high initial investment should be carefully considered to leverage the full potential of Industry 4.0 Integration.
Personalized Medicine Advancements:
Personalized Medicine Advancements signify a tailored approach to healthcare, leveraging genetic insights to customize treatment plans for individual patients. This approach enhances therapeutic outcomes, minimizes adverse reactions, and optimizes drug efficacy. The ability to target specific patient populations based on genetic markers offers a precise and impactful intervention that holds great promise for the future of pharmaceutical manufacturing. However, regulatory complexities, limited accessibility, and ethical dilemmas pose challenges that need to be addressed for widespread adoption.
Sustainable Practices:
Embracing Sustainable Practices is integral to the evolution of pharmaceutical manufacturing towards a greener and more environmentally conscious future. By optimizing resource utilization, reducing waste generation, and implementing eco-friendly technologies, pharmaceutical companies can minimize their carbon footprint and contribute to global sustainability goals. The emphasis on renewable energy sources, biodegradable packaging materials, and eco-friendly production processes showcases a commitment to environmental stewardship. Despite the undeniable benefits, the transition to sustainable practices requires significant investments and systematic changes across the industry.
Continuous Improvement Strategies
Quality Management Systems:
Quality Management Systems play a pivotal role in upholding stringent quality standards throughout the pharmaceutical manufacturing process. By establishing clear protocols, standard operating procedures, and quality control measures, companies can maintain consistency, traceability, and product integrity. The implementation of robust quality management systems ensures compliance with regulatory requirements, enhances customer satisfaction, and mitigates risks of product recalls or quality issues. While the initial implementation may pose logistical challenges and workforce training needs, the long-term benefits of enhanced product quality and market competitiveness outweigh the initial investments.
Lean Manufacturing Principles:
Lean Manufacturing Principles optimize operational efficiency and eliminate wasteful practices in pharmaceutical manufacturing. By emphasizing continuous improvement, waste reduction, and value stream mapping, companies can streamline production processes and improve resource allocation. The principles of lean manufacturing enable swift response to market demands, minimized lead times, and increased cost-effectiveness. However, adopting lean principles may require cultural shifts, organizational restructuring, and ongoing performance measurement to achieve sustained improvements and operational excellence.
Risk Mitigation Plans:
Developing Risk Mitigation Plans is indispensable in mitigating potential hazards, uncertainties, and disruptions in pharmaceutical manufacturing. By conducting thorough risk assessments, establishing preventive measures, and crisis management protocols, companies can proactively address vulnerabilities and safeguard business continuity. Effective risk mitigation plans encompass thorough contingency planning, regulatory compliance adherence, and continuous monitoring of risk indicators. While the proactive approach to risk mitigation may involve resource allocation and time commitment, the long-term benefits of operational resilience and risk mitigation outweigh the costs incurred.