Mastering Bill of Materials Inventory Management: A Comprehensive Handbook for Efficiency
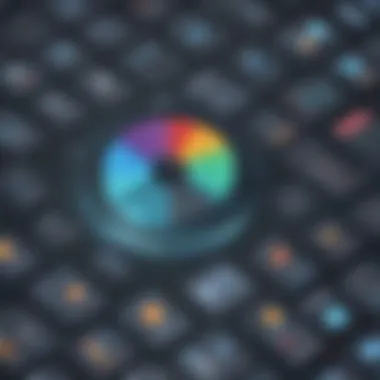
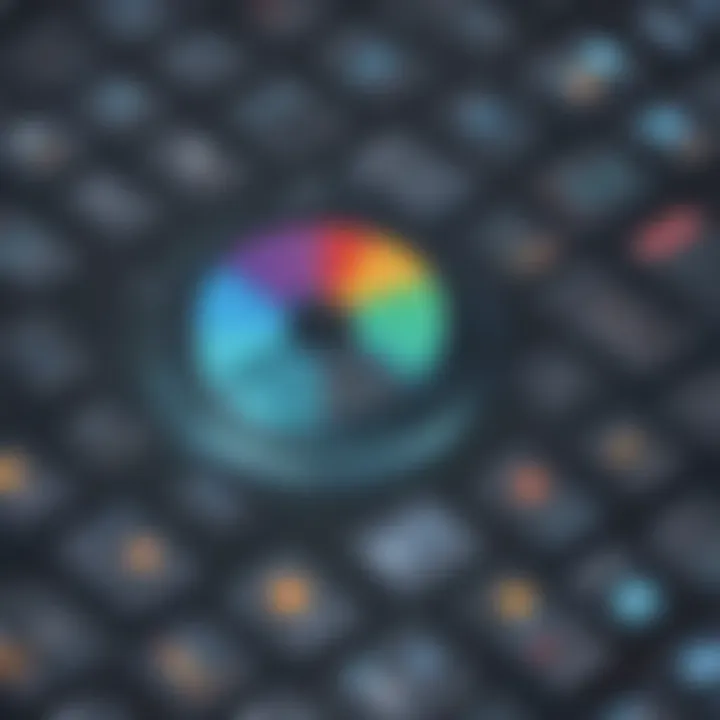
Industry Overview
In this section, we delve into the current trends in industry-specific software market in the realm of optimizing bill of materials (BOM) inventory management. Understanding the landscape we operate in is imperative to making informed decisions. We highlight key challenges faced by buyers, shedding light on the sophisticated demands of the industry. Additionally, we explore the emerging technologies impacting the industry, paving the way for advancements and innovation.
Top Software Options
Moving forward, we conduct a detailed review of leading software providers specializing in BOM inventory management. By comparing features and functionalities, we provide a comprehensive analysis of the top software solutions available in the market. Furthermore, we dissect the pricing structures of these software options, offering a transparent view of the financial aspects associated with each solution.
Selection Criteria
In this section, we emphasize the crucial factors that should be considered when selecting software for optimizing BOM inventory management. By illuminating the importance of due diligence, we highlight common mistakes that should be avoided during the selection process. Moreover, we elucidate on how to determine the right fit for unique business needs, ensuring a harmonious integration of the chosen software into existing operations.
Implementation Strategies
Detailed insight into the implementation strategies for software solutions to streamline BOM inventory management is provided here. We outline best practices that pave the way for a smooth implementation process, minimizing disruptions and maximizing efficiency. Additionally, the integration of the chosen software with existing systems and processes is explored, along with elucidating on the importance of training and robust support resources for successful deployment.
Future Trends
Finally, we delve into the future trends shaping the landscape of industry-specific software for optimizing BOM inventory management. By making informed predictions and insights, we provide readers with a glimpse into upcoming technologies that are set to revolutionize the industry. Recommendations for future-proofing technology stacks are also offered, ensuring businesses stay ahead of the curve in an ever-evolving market.
Introduction
In the realm of modern supply chain management, mastering the intricacies of optimizing bill of materials inventory holds paramount importance. A well-structured approach to bill of materials (BOM) can significantly influence overall operational efficiency and cost-effectiveness. In this comprehensive guide, we delve deep into the significance of efficient inventory management and explore a gamut of strategies, best practices, and tools to elevate your inventory control endeavors to new heights.
Defining Bill of Materials (BOM)
The foundation of streamlined inventory management lies in a comprehensive understanding of the bill of materials (BOM). The BOM serves as a detailed blueprint outlining all components required to manufacture a product, encompassing raw materials, sub-assemblies, and finished goods. By clearly defining each element within the BOM, businesses can orchestrate a coherent production process and ensure optimum resource allocation.
Significance of Inventory Management
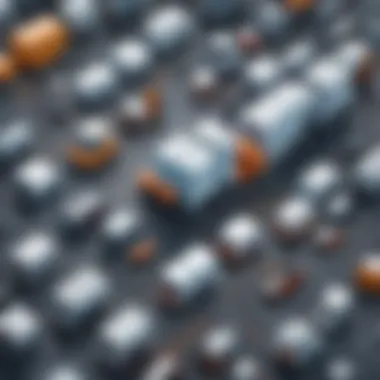
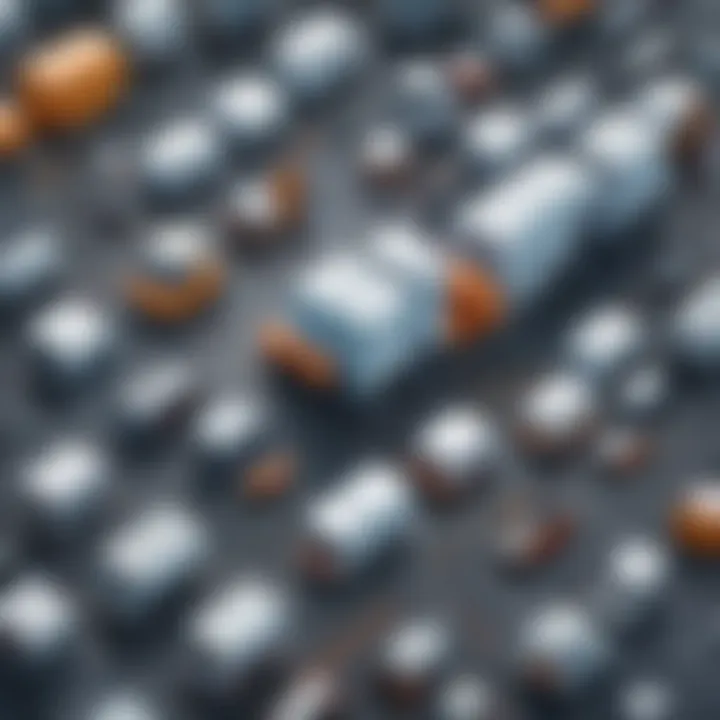
Effective inventory management stands as the linchpin of operational success for enterprises across sectors. It facilitates enhanced transparency and accuracy in tracking stock levels, minimizing the risk of understocking or overstocking. Furthermore, adept inventory management practices lead to notable cost reduction and optimization, as organizations can streamline procurement processes and minimize excess inventory. By acknowledging the pivotal role of inventory management, businesses can fortify their supply chain resilience and bolster their competitive edge in the market.
Importance of Efficient Inventory Management
Efficient Inventory Management is the cornerstone of successful supply chain operations. In this article, we delve deep into the intricacies of streamlining inventory processes to maximize operational efficiency and drive overall profitability. By focusing on specific elements such as transparency, accuracy, and optimization, businesses can achieve a competitive edge within their respective industries. Effective inventory management not only ensures smooth production cycles but also fosters customer satisfaction through timely deliveries and quality products.
Enhancing Transparency and Accuracy
Ensuring transparency and accuracy in inventory management is paramount for mitigating risks and maintaining operational fluidity. By leveraging advanced tracking systems and real-time data analytics, businesses can establish a clear line of sight into their inventory levels and flows. Transparency enables teams to spot potential bottlenecks or discrepancies swiftly, allowing for prompt resolution and enhanced decision-making processes. Moreover, accuracy in inventory management leads to minimized errors, reduced waste, and improved forecast accuracy, all of which are crucial for maintaining a lean and cost-effective supply chain.
Cost Reduction and Optimization
Cost reduction and optimization are primary objectives of efficient inventory management practices. By implementing lean principles and proactive inventory control strategies, businesses stand to minimize holding costs, reduce overstock situations, and improve cash flow management. Cost reduction initiatives such as Just-In-Time (JIT) practices and demand forecasting play a pivotal role in optimizing inventory levels and ensuring optimal resource allocation. Ultimately, achieving cost efficiency in inventory management enhances a company's bottom line, frees up capital for strategic investments, and strengthens its competitive position in the market.
Components of Bill of Materials
In the realm of optimizing bill of materials (BOM) inventory management, understanding the components of a Bill of Materials plays a pivotal role. The BOM serves as a roadmap of all the raw materials, sub-assemblies, and finished goods required for a specific product, ensuring a streamlined production process. By delving into the intricacies of each component, businesses can enhance efficiency, reduce errors, and improve overall cost-effectiveness. Raw materials form the foundation of any BOM, encompassing the basic elements needed for production. Sub-assemblies, on the other hand, represent the intermediate components or modules that come together to create the final product. Lastly, finished goods signify the end products that result from the assembly of all raw materials and sub-assemblies, ready to be shipped to customers. By gaining a comprehensive understanding of these components, organizations can optimize their inventory management strategies and drive operational excellence.
Raw Materials
Raw materials are the fundamental building blocks of any product. They are the basic components that are transformed or used as-is in the manufacturing process. It is crucial for businesses to accurately document and track raw materials in the BOM to ensure a seamless production flow. Factors such as quality, availability, and cost-effectiveness of raw materials heavily influence the overall product quality and profitability. By carefully managing raw materials within the BOM, businesses can mitigate supply chain risks, maintain consistent production output, and uphold quality standards.
Sub-Assemblies
Sub-assemblies play a crucial role in the production process, representing individual components or groups of components that are assembled to create larger modules. Efficient management of sub-assemblies within the BOM is essential for optimizing production efficiency, reducing lead times, and minimizing production costs. By strategically organizing and tracking sub-assemblies, businesses can streamline their production lines, enhance product customization capabilities, and respond swiftly to market demands. Attention to detail and accuracy in documenting sub-assemblies within the BOM is key to fostering greater transparency, collaboration, and agility within the manufacturing process.
Finished Goods
Finished goods mark the culmination of the production process, representing the final products ready for distribution to end customers. Effective management of finished goods within the BOM is critical for inventory control, order fulfillment, and customer satisfaction. Businesses must carefully monitor finished goods levels, ensure product quality standards are met, and optimize inventory turnover rates to prevent stockouts or excess inventory. By structuring the BOM with detailed information on finished goods, organizations can align production schedules with market demand, facilitate timely deliveries, and maximize profitability.
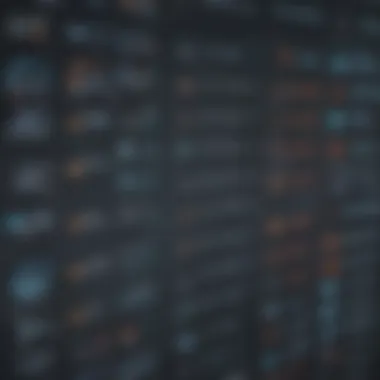
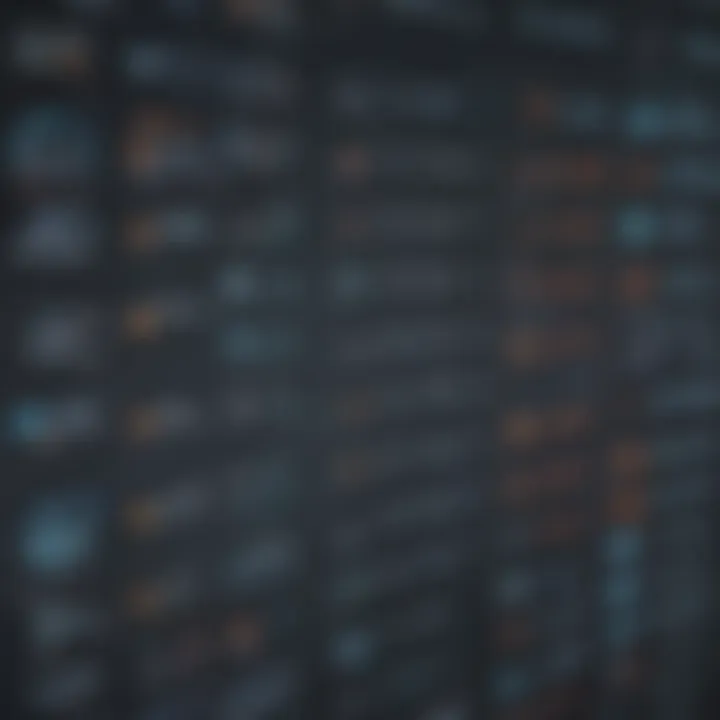
Challenges in BOM Inventory Management
In this section, we dive deep into the crucial aspect of Challenges in BOM Inventory Management in our comprehensive guide on optimizing bill of materials inventory management. Understanding and tackling these challenges are paramount for efficiently managing inventory processes within a company or organization. By delving into the specifics of these challenges, we shed light on the hurdles that professionals in the field may encounter, offering valuable insights and strategies for overcoming them.
Supply Chain Disruptions
Supply Chain Disruptions stand out as a major challenge in BOM inventory management, significantly impacting operational efficiency and financial stability. These disruptions can arise from various factors such as natural disasters, political instability, or even unexpected supplier issues. Mitigating the impact of these disruptions requires a proactive approach, robust risk management strategies, and agile response mechanisms to ensure continuity in supply chain operations.
Data Accuracy and Integrity
Data Accuracy and Integrity pose critical challenges in BOM inventory management, emphasizing the importance of reliable and precise data for effective decision-making. Inaccurate data can lead to inventory errors, procurement delays, and financial losses. Hence, implementing stringent data validation processes, periodic audits, and adopting advanced data management technologies are essential to maintain data accuracy and integrity throughout the inventory management cycle.
Lead Time Variability
Lead Time Variability is a significant challenge impacting inventory optimization and production planning. Fluctuations in lead times for raw materials or components can disrupt production schedules, leading to inventory shortages or surpluses. Addressing lead time variability requires strategic coordination with suppliers, establishing buffer inventories, and leveraging predictive analytics to anticipate lead time fluctuations. By effectively managing lead time variability, organizations can enhance production efficiency and reduce operational risks.
Strategies for Effective BOM Inventory Management
In this segment of the comprehensive guide on optimizing Bill of Materials (BOM) inventory management, we delve into the significance and impact of employing robust strategies to streamline inventory processes effectively. In the realm of supply chain management, the implementation of efficient strategies can yield substantial benefits, ensuring operational smoothness, cost-effectiveness, and enhanced productivity. It is imperative to recognize that the strategic management of BOM inventory is instrumental in mitigating risks, improving overall performance, and fostering a competitive edge in the market landscape.
Implementing Automation
When discussing the theme of implementing automation in BOM inventory management, we confront a critical aspect of modernizing inventory control mechanisms. Automation presents a paradigm shift in how organizations handle inventory tracking, stock replenishment, and data management tasks. By leveraging automation technologies such as barcode scanning, RFID systems, and automated data entry processes, businesses can significantly enhance accuracy, efficiency, and speed in handling BOM inventory. The integration of automated solutions not only reduces manual errors but also optimizes inventory control, enabling real-time visibility and control across the supply chain network.
Utilizing ERP Systems
One of the pivotal components in the arsenal of effective BOM inventory management is the utilization of Enterprise Resource Planning (ERP) systems. ERP software plays a crucial role in integrating various business processes, including inventory management, production planning, procurement, and order tracking. By harnessing the power of ERP systems, organizations can centralize data, streamline operations, and improve communication within different departments. The seamless flow of information facilitated by ERP solutions enhances decision-making capabilities, resource allocation, and fosters synergy across the entire value chain.
Adopting Just-In-Time (JIT) Practices
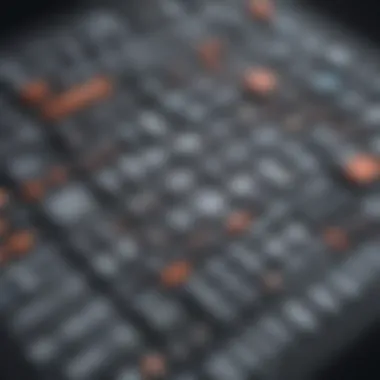
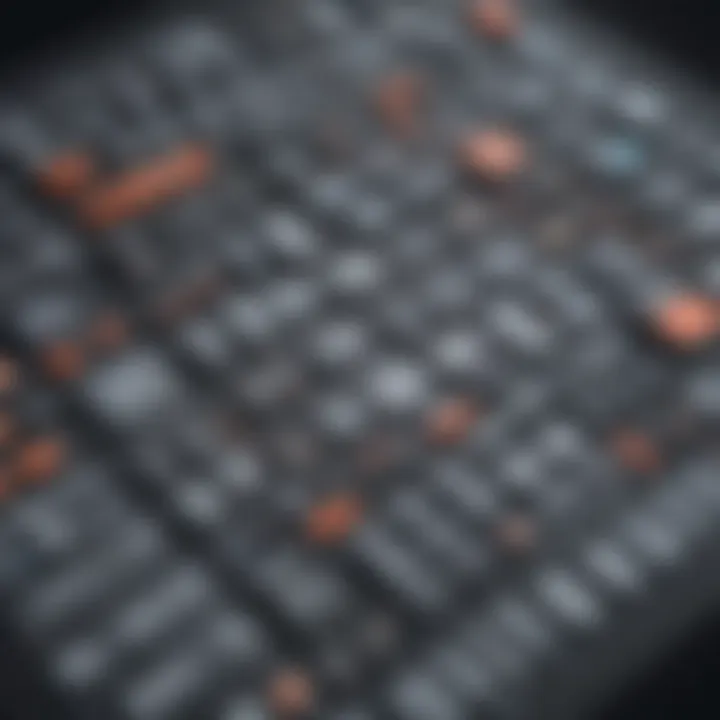
The adoption of Just-In-Time (JIT) practices is a strategic approach that emphasizes the lean management of inventory levels to reduce waste and enhance operational efficiency. By implementing JIT principles, organizations can enact a demand-driven inventory system that minimizes excess inventory holding costs, storage space requirements, and the risk of obsolete stock. JIT practices promote a responsive supply chain model, enabling companies to meet customer demands promptly, minimize lead times, and optimize production processes. Embracing JIT methodologies fosters a culture of continuous improvement, adaptability, and resilience in the face of market fluctuations and dynamic consumer preferences.
Tools and Software for BOM Inventory Management
In this section of the comprehensive guide on optimizing Bill of Materials (BOM) inventory management, we delve into the critical role that tools and software play in streamlining and enhancing inventory processes. Employing advanced tools and software is vital for ensuring efficient management of BOMs in a complex supply chain ecosystem. These tools offer a wide array of benefits, such as enhanced accuracy, real-time visibility, and automated processes that reduce manual errors and optimize inventory levels.
Inventory tracking systems are instrumental in providing real-time monitoring and control of inventory movements within the supply chain. These systems enable businesses to track the movement of materials from procurement to production to distribution accurately. By leveraging inventory tracking systems, organizations can enhance inventory accuracy, prevent stockouts, and improve order fulfillment processes.
Material Requirements Planning (MRP) software is indispensable for managing resources effectively and optimizing production schedules based on demand forecasts. This software facilitates the procurement of materials, scheduling production operations, and aligning inventory levels with customer demands. By utilizing MRP software, organizations can streamline their operations, reduce lead times, and minimize holding costs.
Warehouse Management Systems (WMS) play a crucial role in optimizing warehouse operations by automating processes, improving inventory visibility, and enhancing order fulfillment efficiency. WMS software helps in organizing warehouse layouts, tracking inventory movements, and managing storage capacities effectively. By implementing WMS, businesses can maximize warehouse space utilization, reduce picking errors, and streamline logistics operations.
Best Practices for Streamlining BOM Inventory Processes
In this section of the comprehensive guide on optimizing Bill of Materials (BOM) inventory management, we will delve into the critical aspect of implementing best practices to enhance operational efficiency and streamline processes. Effective streamlining of BOM inventory processes is paramount in today's complex supply chain landscape, where accuracy and optimization play a pivotal role in sustaining competitiveness. By emphasizing best practices, businesses can not only improve their inventory management but also reduce costs and enhance overall productivity. It is crucial to understand that implementing best practices involves a strategic approach that encompasses various elements such as process optimization, technology integration, and continual improvement.
Regular Auditing and Reconciliation
Regular auditing and reconciliation form the cornerstone of efficient BOM inventory management. This practice involves conducting periodic reviews of inventory data and comparing it against physical stock levels. By meticulously cross-referencing documented information with actual inventory counts, organizations can detect discrepancies, identify potential areas of improvement, and ensure data accuracy. Auditing also plays a crucial role in maintaining compliance with industry regulations and internal quality standards. Moreover, reconciliation aids in minimizing errors, preventing stockouts or overstock situations, and fostering a culture of accountability within the organization.
Supplier Collaboration and Communication
Supplier collaboration and communication are vital components of successful inventory management processes. Establishing transparent and effective communication channels with suppliers enables seamless coordination, proactive problem-solving, and enhanced visibility into the supply chain. By fostering strong relationships with suppliers, businesses can anticipate demand fluctuations, address potential bottlenecks, and mitigate risks effectively. Collaborative partnerships also facilitate the sharing of critical information, such as lead times, quality standards, and production schedules, leading to improved inventory forecasting and optimized inventory levels.
Forecasting and Demand Planning
Forecasting and demand planning play a pivotal role in optimizing BOM inventory processes. Accurate demand forecasting involves analyzing historical data, market trends, and customer behaviors to predict future inventory requirements effectively. By aligning production schedules and resource allocation with forecasted demand, organizations can prevent excess inventory, reduce holding costs, and improve customer satisfaction. Incorporating demand planning strategies, such as advanced analytics and scenario modeling, enables businesses to adapt quickly to changing market dynamics and maintain a competitive edge in the industry. Effective forecasting not only streamlines inventory processes but also enhances overall operational efficiency and strategic decision-making.
Conclusion
Bill of Materials (BOM) inventory management plays a pivotal role in the efficient functioning of supply chain operations within a company. As explored in this comprehensive guide, the proper optimization of BOM inventory management can lead to streamlined processes, cost savings, and enhanced productivity. By meticulously managing the components of BOMs, such as raw materials, sub-assemblies, and finished goods, organizations can ensure accurate inventory levels and timely production schedules. Effective BOM inventory management also mitigates the risks associated with supply chain disruptions, data inaccuracies, and lead time variations, ultimately resulting in improved operational efficiency and customer satisfaction.
Driving Efficiency through Optimal BOM Inventory Management
Fostering efficiency through optimal BOM inventory management involves a multi-faceted approach centered on enhancing transparency, accuracy, and responsiveness within the supply chain. Leveraging automation tools and ERP systems can automate workflows, minimize manual errors, and provide real-time visibility into inventory levels and demands. Implementing Just-In-Time (JIT) practices can further optimize inventory levels, reduce carrying costs, and enable organizations to operate with lean and agile production processes. Adopting best practices such as regular auditing, supplier collaboration, and demand planning can significantly streamline BOM inventory processes and ensure seamless operations. By integrating these strategies and practices into their inventory management framework, businesses can drive efficiency, maximize cost savings, and achieve sustainable growth in today's competitive marketplace.