Choosing the Right SaaS for Manufacturing Success
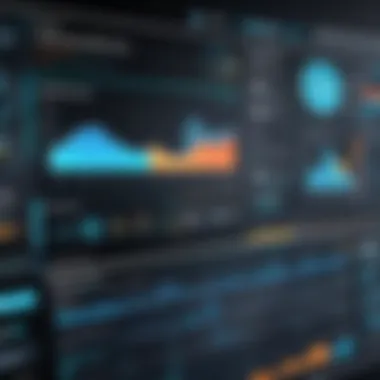
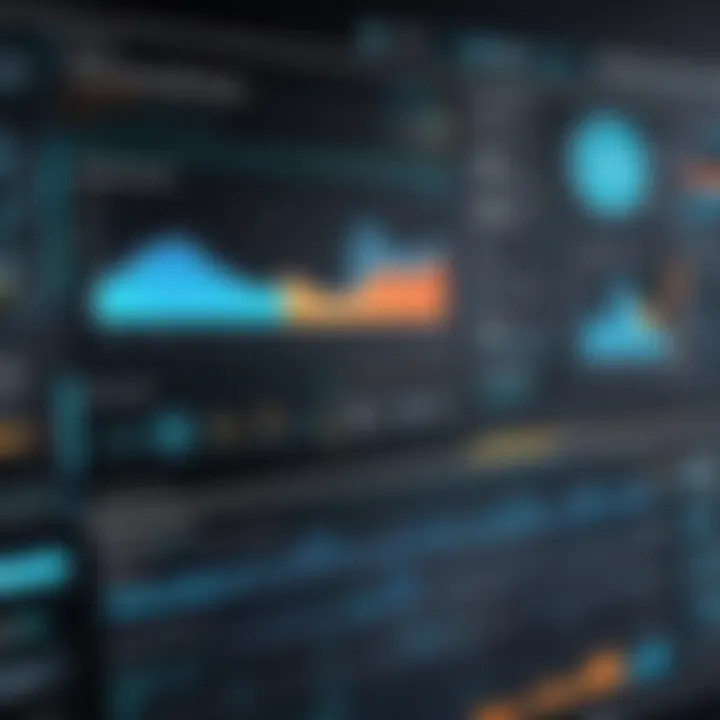
Intro
In today’s fast-paced manufacturing environment, the convergence of technology and operational efficiency is no longer optional; it’s a necessity. Software as a Service (SaaS) has emerged as a transformative force in this sector, opening doors to numerous opportunities while addressing unique challenges. The adoption of SaaS solutions enables manufacturers to streamline processes, enhance collaboration, and ultimately improve their bottom line. But evaluating these solutions is no small feat. This guide aims to provide detailed insights into the important decision-making factors that manufacturers must consider when exploring the realm of SaaS applications.
Industry Overview
Current Trends in the Industry-specific Software Market
The software market for manufacturing has seen rapid evolution over the past few years. Manufacturers are increasingly leaning towards cloud-based solutions that offer flexibility and scalability. Off-the-shelf software is becoming less common as companies seek tailored solutions that meet their specific operational needs. With the push for Industry 4.0, there's a noticeable shift towards real-time data analytics, Internet of Things (IoT) integrations, and machine learning capabilities, allowing for smarter decision-making.
Key Challenges Faced by Buyers in the Industry
When navigating the tumultuous waters of software selection, buyers encounter several roadblocks:
- Data Security Concerns: Manufacturers often sit on sensitive data. Data breaches can spell disaster.
- Integration Hurdles: It's not just about picking the right software; ensuring it meshes well with existing systems is another hurdle altogether.
- Customization Needs: Off-the-shelf solutions may lack the adaptability required for niche manufacturing processes.
Emerging Technologies Impacting the Industry
Various technologies are reshaping the landscape. Notably, Artificial Intelligence (AI) and machine learning are enhancing predictive maintenance and quality assurance processes. Moreover, robotics and automation are streamlining production workflows. As businesses adopt these technologies, the thought process surrounding software solutions will need to evolve accordingly.
Top SaaS Software Options
Review of Leading Software Providers in the Industry
When it comes to SaaS solutions for manufacturing, several providers stand out. MES, Odoo, and ProShop are notable examples, each bringing unique strengths to the table. MES specializes in real-time operational visibility, while Odoo's modular approach allows for tailored solutions, and ProShop offers an all-in-one ERP system designed for manufacturers.
Feature Comparison of Top Software Solutions
When evaluating these software solutions, consider key features:
- Customization: Ability to tailor to specific operational needs.
- User-friendliness: Intuitive interfaces that require minimal training.
- Scalability: Solutions that grow with the business.
- Support and Training: Availability of resources for troubleshooting and onboarding.
| Feature | MES | Odoo | ProShop | | Customization | High | High | Medium | | User-friendliness| Medium | High | High | | Scalability | Medium | High | High | | Support | High | Medium | High |
Pricing Structures of Different Software Options
Pricing for these SaaS solutions can vary widely based on features and service levels. Common models include subscription-based pricing, which typically involves a monthly or annual fee, as well as pay-per-use models. Understanding the total cost of ownership, which includes hidden costs like training and support, is crucial in this selection process.
Selection Criteria
Important Factors to Consider When Choosing Software
Selecting the right SaaS solution goes beyond mere functionality. Here are key factors to ponder:
- Business Needs: Clarify what you hope to achieve.
- Industry Compatibility: Ensure the software is built for manufacturing.
- User Experience: A solution that is hard to use will likely cause more problems than it solves.
Common Mistakes to Avoid During the Selection Process
Many organizations fall into traps that can be easily avoided:
- Ignoring Integration Needs: Failure to assess how well a new solution integrates with existing software.
- Overlooking Total Costs: Not accounting for future expenses can lead to budget overruns.
- Rushing the Decision: Taking the time to evaluate thoroughly is crucial.
How to Determine the Right Fit for Your Business Needs
Every organization's needs are unique. A good starting point is conducting a detailed needs assessment. Consider engaging all stakeholders to gather diverse input about operational pain points, desired outcomes, and interface preferences.
Implementation Strategies
Best Practices for Smooth Implementation of Software Solutions
Implementing a SaaS solution can be daunting, yet proper planning can ease the transition:
- Develop a Clear Plan: Map out the stages of rollout.
- Engage Stakeholders Early: Involvement ensures buy-in and smoother adaptation to change.
Integration with Existing Systems and Processes
Integrating new software with legacy systems is often a tricky business. Companies should prioritize solutions that offer standard APIs to facilitate communication between platforms. Testing these integrations in a phased manner will help identify potential hiccups before full deployment.
Training and Support Resources for Successful Deployment
Training is a cornerstone of successful SaaS integration. Investing time in educating staff on new software not only boosts productivity but also enhances user satisfaction. Many providers offer extensive training resources, often supplemented by community forums or customer support teams.
Future Trends
Predictions for the Future of the Industry-specific Software Landscape
The future of manufacturing software looks promising, with trends such as predictive analytics and increased reliance on AI for decision-making on the rise. Enhanced mobile functionality will allow for access to real-time data from anywhere, giving teams functionality outside the traditional factory walls.
Upcoming Technologies Shaping the Industry
The emergence of 5G technology is set to revolutionize IoT capabilities in manufacturing. With faster connectivity, manufacturers will experience improved automation, augmented reality applications, and enhanced tracking capabilities.
Recommendations for Future-Proofing Your Technology Stack
Future-proofing isn't just a buzzword. Incorporate flexible solutions that anticipate changes rather than just react. Avoid being hamstrung by technology that has limited upgrade paths or integration capabilities.
"Choosing the right SaaS solution for manufacturing can be like finding a needle in a haystack; take your time, and do your homework."
By considering industry-specific challenges, embracing emerging technologies, and prioritizing a strategic approach, manufacturers can position themselves for significant gains in operational efficiency and overall innovation.
Understanding SaaS in Manufacturing
In the contemporary landscape of the manufacturing sector, the integration of technologies plays a pivotal role in enhancing productivity and operational efficiency. One such technology, Software as a Service (SaaS), has emerged as a game changer, offering unique solutions tailored to meet the specific needs of manufacturers. A comprehension of what SaaS entails is fundamental for industry professionals aiming to leverage its benefits effectively.
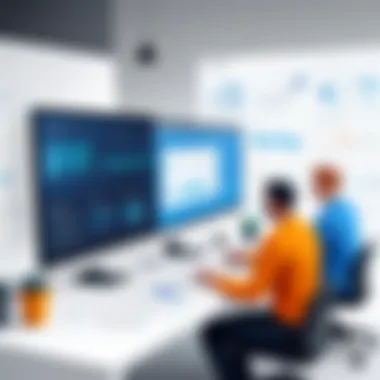
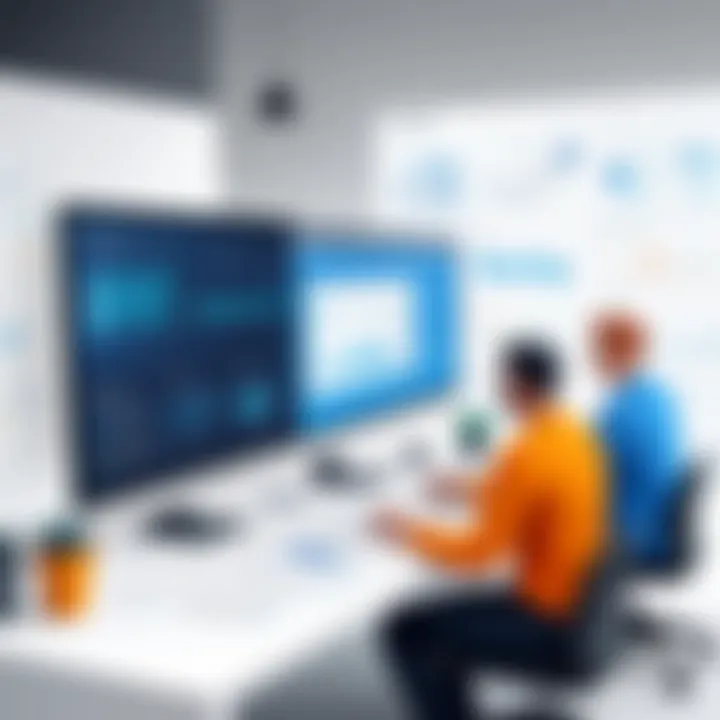
Definition of SaaS
SaaS can be thought of as a cloud-based service where instead of downloading software on your desktop, you simply access it via the Internet. For manufacturers, this means that software applications can be quickly adopted and used for various operations without extensive upfront investment in IT infrastructure. Furthermore, users subscribe to SaaS applications rather than purchasing licenses, which allows flexibility and scalability. Essentially, it’s this model of operation that enables manufacturers to pivot readily to meet ever-changing market demands and customer preferences.
Role of SaaS in Different Industries
The power of SaaS isn’t confined to the manufacturing sector alone. Across various industries—such as healthcare, finance, and retail—SaaS solutions facilitate improved collaboration and streamlined processes. For instance, in healthcare, systems like Epic’s Electronic Health Records enable seamless information sharing among providers. In manufacturing, SaaS plays a similar role, reducing silos and promoting integration among different departments. It allows for real-time visibility into operations and fosters better decision-making. The beauty of SaaS lies in its versatility; as needs evolve, so can the software used, resulting in continual enhancements across the board.
Advantages of SaaS for Manufacturing
Opting for SaaS solutions in manufacturing comes with several advantages:
- Cost-Effectiveness: With no hefty hardware investments or the need for elaborate IT staffing, manufacturers can allocate resources more wisely. Subscriptions are typically lower than traditional software licenses.
- Quick Implementation: Time is of the essence in manufacturing. SaaS apps can often be set up quickly, allowing organizations to hit the ground running without lengthy delays.
- Automatic Updates: Gone are the days of dealing with tedious manual upgrades. SaaS solutions automatically update, ensuring users benefit from the latest features and security patches.
- Accessibility: With cloud access, team members can engage with important data from anywhere. Whether on the shop floor or in a remote location, vital information is at their fingertips.
"SaaS has transformed the way we operate—eliminating downtime and ensuring that every team member is connected and informed," said a manufacturing IT director.
In summary, understanding SaaS in manufacturing is not just about recognizing its existence; it’s about appreciating how it can drastically elevate operational performance. The distinct aspects of software adoption matter, and acknowledging these facts will enable decision-makers in the field to harness technology effectively.
Challenges Faced by Manufacturers
The implementation of Software as a Service (SaaS) solutions can significantly improve various processes in manufacturing, but first, it’s essential to understand the challenges manufacturers face. Without acknowledging these hurdles, it’s easy to overlook the potential benefits SaaS can bring. Manufacturers deal with a tapestry of complexities that can stymie productivity and scalability. Thus, evaluating these challenges becomes a cornerstone in guiding manufacturers to make more informed decisions regarding SaaS deployment.
Operational Inefficiencies
Operational inefficiencies are the bane of any manufacturing floor. These can manifest in numerous ways, from machinery that sits idle for too long to bottlenecks in production lines. The root causes often trace back to outdated systems and lack of real-time insights. When data is either siloed or absent, decision-making resembles navigating a ship without a rudder—aimless and prone to errors.
For instance, imagine a factory where equipment maintenance is scheduled based on guesswork rather than hard data. A break down could lead to days of lost productivity. In a rapidly moving environment, even minor delays can spiral into larger issues, impacting supply chain integrity and customer satisfaction. Therefore, rectifying such inefficiencies not only necessitates the shift to advanced SaaS solutions but also emphasizes the importance of real-time monitoring tools that can flag potential issues before they escalate.
Supply Chain Complexities
Supply chains in manufacturing are like the veins in an intricate body; when one part falters, the entire system feels the strain. Today, supply chains are often sprawling networks that encompass various vendors, transportation modes, and even regulatory requirements. Increased globalization has added layers of complexities that didn’t exist before. This includes navigating customs laws, fluctuating raw material costs, and managing relationships with multiple suppliers.
Increased visibility across these touchpoints is paramount to overcome these complexities. SaaS solutions can provide a centralized view, yielding valuable insights into the entire supply chain—from procurement to delivery. It enables manufacturers to swiftly adapt to market changes, uncertain delivery times, or sudden supplier disruptions. Ultimately, dealing with supply chain complexities head-on ensures that manufacturers not only stay competitive but thrive in today’s fast-paced environment.
Data Management and Analytics
Today's data is akin to gold; yet, for many, it remains untapped and underutilized. Manufacturers generate mountains of data from their operations, but without comprehensive data management strategies, it can become a soup of numbers lacking context. This represents a significant barrier to harnessing analytics for informed decision-making. Manufacturers often struggle with consolidating data from different systems, and it leads to discrepancies that could skew performance metrics.
Using SaaS platforms can streamline data management. These tools can aggregate data from various sources, providing a holistic view that empowers manufacturers to analyze trends and make forecasts. For example, real-time analytics can help identify production trends, predict equipment failures, and enhance quality control procedures. In essence, insightful data management allows manufacturers to pivot with agility, minimizing risks and optimizing productivity.
Taking the time to address operational inefficiencies, supply chain complexities, and data management challenges will enable manufacturers to strategically leverage SaaS solutions for transformative growth.
Overcoming these challenges is not a walk in the park, but the journey is worth it. By tackling these issues head-on, manufacturers position themselves to fully leverage the capabilities of SaaS systems, ultimately leading to more streamlined operations and a stronger market position.
Key Features of Manufacturing SaaS Solutions
In today’s fast-paced manufacturing environment, adopting a Software as a Service (SaaS) model is no longer just a trend; it’s become an essential strategy for competitive advantage. The right SaaS solutions can greatly enhance operational efficiencies, support agile decision-making, and streamline processes. The core of any effective SaaS implementation lies in its features, which are tailored to address specific manufacturing needs. This section delves into the key features that set manufacturing SaaS solutions apart and examines how they can benefit organizations.
Inventory Management Systems
In a manufacturing setup, keeping track of raw materials, components, and finished goods is pivotal. Inventory Management Systems that fall under the SaaS umbrella can offer real-time visibility of stock levels, enabling manufacturers to avoid stockouts or overstock situations. For instance, if a facility is constantly running low on a crucial component, the system can trigger alerts to reorder automatically.
These systems harness cloud capabilities, which means updates are seamless and require minimal downtime. Adding to this, by utilizing analytics, manufacturers can forecast inventory requirements based on historical data and market trends, enhancing their proactive planning skills. This forward-thinking approach can save costs and improve cash flows significantly.
Quality Control Applications
Quality assurance, a cornerstone of manufacturing, demands stringent adherence to standards which can be cumbersome without the right tools. Quality Control Applications within SaaS solutions make it simpler to monitor production quality in real-time across various stages of the manufacturing process. They equip quality managers with tools to ensure products meet compliance regulations and quality standards effectively.
By embedding these applications, manufacturers can utilize checklists, inspections, and reporting directly linked to the production lines. The result is a streamlined process whereby deviations can be detected promptly, fostering continuous improvement. A well-implemented quality control app not only ensures product integrity but also enhances customer satisfaction and brand reputation over time.
Production Planning Tools
With the dynamics of demand fluctuating, having robust Production Planning Tools is crucial for manufacturers aiming to optimize their operations. SaaS solutions can simplify this complexity by leveraging integrated scheduling capabilities that align production with demand patterns efficiently. By employing such tools, businesses can visualize production timelines, allocate resources, and mitigate potential bottlenecks before they develop.
Moreover, these planning tools often incorporate scenario analysis options, allowing decision-makers to simulate various production paths. That foresight can be incredibly beneficial, especially in anticipating challenges and ensuring the right resources are allocated when and where they are needed most.
Financial and Performance Tracking Software
Monitoring financial performance and overall efficiency in real-time is a trend gaining traction across all sectors. Financial and Performance Tracking Software as part of a manufacturing SaaS can streamline financial reporting, budgeting, and data visualization, providing insights needed to make informed decisions. This means businesses can track KPIs and financial metrics dynamically instead of relying on end-of-month reports.
A benefit of these systems is their ability to integrate with other existing tools, offering a more cohesive view of the organization's financial health. For instance, manufacturers can assess production costs, identify waste, and pinpoint profitability by product line. By understanding these nuances, it becomes clearer where adjustments should take place for optimal performance.
Utilizing well-defined key features of SaaS solutions can be pivotal to enhancing operational effectiveness and ensuring sustainable growth within the manufacturing sector.
In summary, as manufacturing landscapes evolve, so too must the tools and solutions that support them. Embracing the breadth of features offered by manufacturing SaaS solutions can substantially transform operations, drive efficiencies, and give organizations a robust framework to tackle current and future challenges.
Benefits of Adopting SaaS
In today’s fast-paced manufacturing environment, adopting SaaS solutions can be a game changer for many businesses. It’s not just about jumping on the latest tech bandwagon; the benefits extend to cost savings, agility, and enhanced operational capabilities. Essentially, SaaS can yield a multitude of advantages that address the unique challenges faced by manufacturers, allowing them to streamline processes and remain competitive in the market.
Cost Efficiency and Budget Management
One of the standout advantages of SaaS is its potential for cost savings. Traditional software requires hefty upfront investments, ongoing maintenance costs, and sometimes even unexpected expenses for upgrades. SaaS shifts these costs to a subscription-based model. This structure helps manufacturers manage their budgets more effectively.
- Lower Upfront Costs: With SaaS, the need for extensive hardware and software investments is diminished. Users often pay a monthly fee, which can be easier to plan for in annual budgets.
- Predictable Expenses: Monthly subscriptions mean predictable cash flow, enabling easier financial forecasting. Manufacturers can allocate their resources more strategically without worrying about surprise expenses.
- Reduced IT Costs: There’s also less pressure on the IT department. Fewer resources are needed to maintain software, allowing the team to focus on growth strategies instead of daily maintenance tasks.
Scalability and Flexibility
The nature of manufacturing is ever-evolving, often requiring quick adjustments to shifts in demand or production scales. Here’s where SaaS shines, offering flexibility that traditional software often can't match.
- Scalable Solutions: Whether a manufacturer is growing or downsizing, SaaS platforms can scale accordingly. Adding users or features can typically be done within a few clicks. This makes it easier to adjust based on production needs without overcommitting resources.
- Flexible Access: Being cloud-based, SaaS can be accessed from various devices and locations. This means on-the-go access to essential data, which is particularly useful for managers who need to monitor operations across multiple sites.
Access to Real-Time Data
In manufacturing, data is crucial for informed decision-making. The ability to access real-time data is a hallmark benefit of SaaS applications.
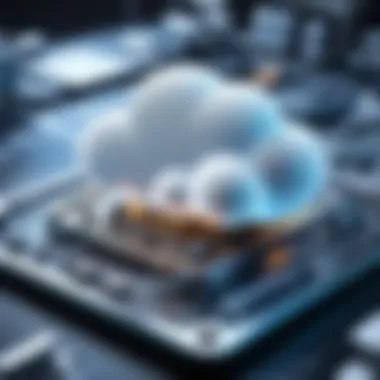
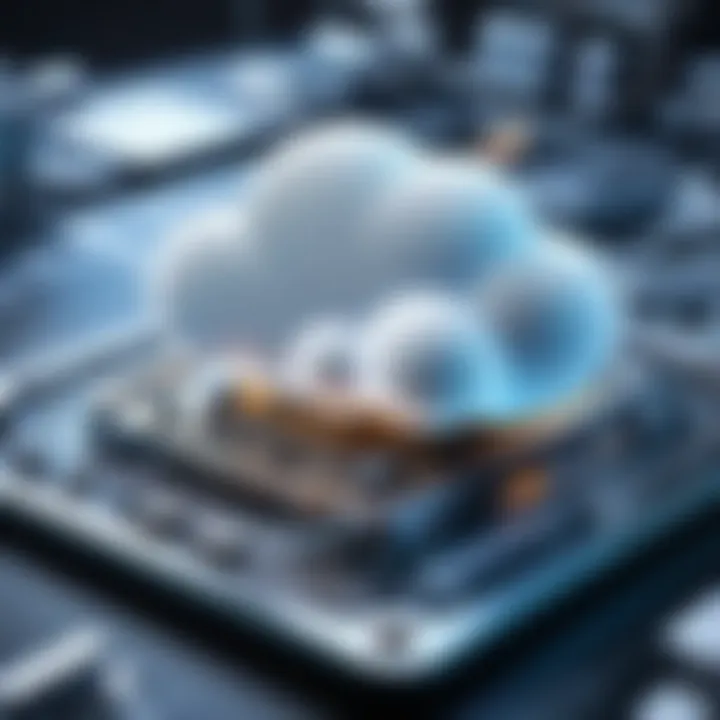
- Instant Insights: Unlike traditional software that may require manual updates and reports, SaaS solutions often provide dashboards that display current data at a glance. This can aid in rapid problem-solving and trend analysis.
- Enhancing Decision-Making: With real-time data, decision-makers can recognize patterns, bottlenecks, and opportunities swiftly. This allows for more proactive management of resources, which can lead to improved productivity and reduced waste.
Improved Collaboration and Communication
Collaboration is key in any manufacturing setting, especially in environments that require synergy between departments.
- Streamlined Communication: Many SaaS platforms include integrated communication tools. This means teams can share updates and instructions seamlessly, reducing the chances of miscommunication.
- Cross-Department Collaboration: Since SaaS applications can be accessed by multiple users at once, teams across various departments can work together more efficiently. For example, production staff can communicate directly with sales teams about inventory levels or expected delivery times in real-time.
"SaaS isn't just a tool; it's a bridge that connects different parts of manufacturing operations."
As the manufacturing landscape continues to evolve, adopting SaaS can provide a vital edge, not only in driving efficiencies but also in fostering a culture of collaboration and informed decision-making. The journey to integration may require effort, but the benefits make it well worth the investment.
Selecting the Right SaaS Solution
Choosing the right Software as a Service (SaaS) solution is crucial for any manufacturing organization. It's not just about picking software; it’s about aligning it with your specific business requirements, ensuring that it integrates smoothly with existing operations, and optimizing your overall performance. A wrong decision can set the company back weeks or months, not to mention the financial implications. So what do you need to think about when making this important selection?
Identifying Your Business Needs
Understanding what your organization requires is the first step. Each manufacturing business will have unique processes, challenges, and goals. Whether you’re looking to improve production efficiency, streamline inventory management, or enhance supply chain visibility, clarity on your objectives is paramount. Start by evaluating current workflows and pinpointing pain points.
- Do you struggle with high overhead? Look for cost-efficient tools that help minimize resource usage.
- Is data reporting taking longer than it should? Prioritize SaaS products that offer robust data analytics to speed up decision-making.
Collect feedback from stakeholders across departments like production, finance, and sales. Their insights can shape your understanding of what features matter most and what problems need addressing.
Evaluating Vendor Capabilities
Once you've pinpointed your needs, the next step is to scrutinize potential vendors. Not every provider is created equal, and the right choice often depends on how well a vendor meets your requirements. Some key factors to consider include:
- Industry Experience: Vendors who specialize in manufacturing solutions will likely have better insights into industry challenges and offer tailored features.
- Technical Support: You want to partner with a vendor who prioritizes customer support. Good documentation, responsiveness to inquiries, and helpful onboarding can make or break the experience.
- Scalability: Your chosen solution should accommodate future growth. Ask vendors how quickly you can add users or features without incurring prohibitive costs.
Ultimately, take the time to read case studies or user testimonials. Take note of how existing clients have benefited and what challenges they faced during implementation.
Understanding Subscription Models
In the world of SaaS, not all subscription models are created equal. Understanding the various pricing structures and terms is vital. Here’s a breakdown of common models:
- Monthly vs. Annual: Monthly subscriptions may seem appealing, but they can add up. Annual contracts often come with discounted rates. Evaluate which option fits your budget better.
- Tiered Pricing: Some vendors provide different tiers based on features or user counts. Make sure the tier you choose includes the functionalities your organization truly needs, without paying for extras that will go unused.
- Pay-as-you-go: This model is great for businesses with fluctuating needs. You might only pay for what you use, which can help manage cash flow.
When comparing SaaS solutions, don’t forget to quantify the total cost of ownership. Hidden fees for training, additional feature access, or customer support can chew into your budget unexpectedly. Always ask the vendor about potential extra costs before signing on the dotted line.
"The right SaaS solution can transform a manufacturer’s operations, justifying the investment through increased efficiency and streamlined communication."
Deployment of SaaS Solutions
The successful deployment of SaaS solutions is a critical aspect for manufacturers wanting to leverage the advantages of cloud technologies. This stage can often make or break the effectiveness of the software, impacting everything from efficiency to employee satisfaction. Strategically approaching deployment enhances not only how the software integrates into current systems but also how employee training and support will unfold, ultimately leading to a holistic improvement in operational performance.
Cloud Infrastructure Considerations
When selecting a SaaS provider, it is paramount to evaluate the underlying cloud infrastructure. Not all clouds are created equal—some are tailored for specific industries, while others offer generic services that may not align with a manufacturing setup. Considerations include:
- Scalability: As your manufacturing operations grow, so will your need for increased computing power and storage.
- Reliability: Look for uptime guarantees, often expressed as a percentage. A 99.9% uptime might seem impressive, but in a manufacturing context, even a small measure of downtime can have significant consequences.
- Performance: Geographic proximity of data centers can directly affect latency. A provider with centers close to manufacturing sites could improve speeds and response times.
Furthermore, security is a non-negotiable element in today's landscape. Ensure that your cloud provider meets compliance standards such as ISO 27001 or provides certifications relevant to your industry. A robust security protocol safeguards your data from breaches, which can be particularly costly in the manufacturing sector.
Migration Strategies for Legacy Systems
Many manufacturers grapple with outdated legacy systems that can hinder the transition to modern SaaS applications. A structured migration strategy is vital to ensure a smooth shift from old to new. Effective strategies may involve:
- Assessment of Current Systems: Understand the functionalities of your legacy systems and identify the gap between existing capabilities and new SaaS offerings.
- Phased Migration: Rather than a full overhaul, consider migrating in phases, starting with less critical areas. This method minimizes disruptions to daily operations.
- Integration Planning: Develop a comprehensive integration plan that outlines how new SaaS products will interface with existing systems. Compatibility is key here, as proper integration can help maintain data continuity and workflow efficiency.
- Testing: Before going live, conduct thorough testing to resolve any potential issues. In a manufacturing context, this ensures that processes remain uninterrupted by software hiccups.
Involving all relevant stakeholders during this phase will ease concerns and enhance overall buy-in.
Training and Support for Users
No matter how advanced the software, its effectiveness hinges on user adoption. Providers often offer a variety of training resources to facilitate this.
- Onboarding Programs: Tailored for different user groups, allowing for role-specific training that speaks to the software's features in the context of their work.
- Ongoing Support: This can include dedicated channels for troubleshooting, user forums, and access to understandable documentation. Good support can make users feel more comfortable, which translates into higher productivity levels.
Support shouldn’t end with deployment. Continuously fostering an environment where user feedback is encouraged will help streamline processes and improve software utility. Collecting data on user experiences can reveal pain points (e.g., slow processes or confusing interfaces) which can be addressed in future updates or training sessions.
"A robust SaaS deployment goes beyond mere implementation; it’s a key driver for operational excellence in manufacturing."
In summation, the deployment of SaaS solutions is complex but absolutely foundational for success in the manufacturing sphere. Facilities that approach this deployment thoughtfully—considering cloud infrastructure, crafting migration plans, and prioritizing user training—position themselves well for the future.
Integration with Existing Systems
When considering the implementation of SaaS solutions in manufacturing settings, one of the keystones that can determine success or failure is how well these solutions can integrate with existing systems. The reality is that many manufacturing firms have already established intricate networks of systems, processes, and practices. Thus, ensuring smooth connectivity and data flow is crucial. Integration not only aids in ensuring that operations continue without a hitch but also promotes better decision-making through comprehensive data visibility.
APIs and Interoperability
Application Programming Interfaces (APIs) play a vital role in the integration process. A well-designed API allows different software products to speak the same language. This means that manufacturers could connect their existing systems—like ERP or CRM software—with the new SaaS solutions. With proper interoperability, data can transit seamlessly between applications, reducing time spent on manual data entry.
Moreover, the speed with which APIs can facilitate real-time data sharing can’t be overstated. Manufacturers gain the ability to harness data efficiently, leading to more informed strategic decisions. The ultimate goal here is not merely operational efficiency, but creating a responsive manufacturing environment where data informs every move.
Data Migration Tools
Transitioning to a new SaaS system would be a tough nut to crack without proper data migration tools. It involves transferring historical data from legacy systems to the new platform, which could be daunting given that data integrity must be maintained. This requires careful planning to avoid data loss or corruption.
Many SaaS providers come equipped with automated migration tools that help in transferring existing data swiftly. These tools can cleanse, format, and make necessary transformations, ensuring the data transferred is not just a duplicate but usable and meaningful. Success in migration can be pinned down not just to the technical capabilities but also to the strategic considerations around timing and user training—making sure the impact on day-to-day operations is minimum.
Ensuring Data Security and Compliance
In the manufacturing world, data security is paramount. With data flowing between various systems, it’s imperative to ensure that all points of integration adhere to stringent data security protocols. This includes encryption, secure APIs, and routine security checks.
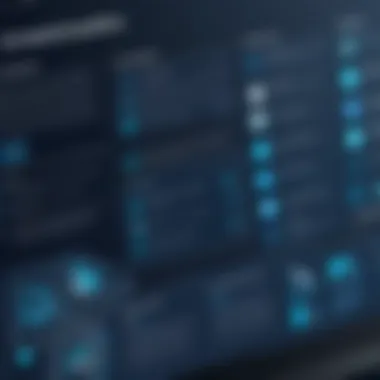
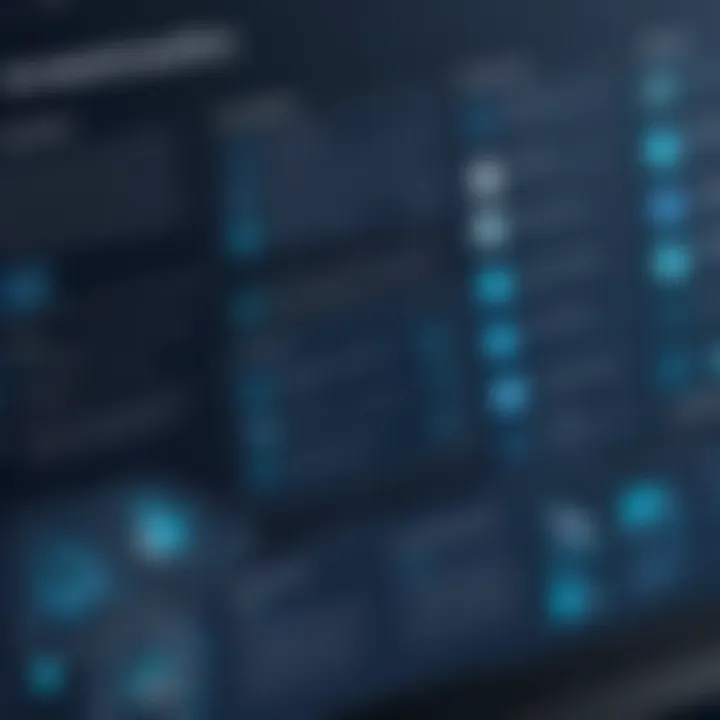
Moreover, compliance with industry regulations adds another layer to the integration equation. Various sectors operate under specific guidelines—think ISO or HIPAA—that demand rigorous data control and management. Ensuring that the integrated SaaS solution complies will not only prevent hefty fines but also bolster trust with stakeholders and clients.
"Integrating new systems is not just about connection; it's fundamentally about trust in data management and security."
Case Studies in SaaS Implementation
Diving into the intricacies of SaaS solutions in manufacturing necessitates an examination of real-world implementations. Case studies shed light on the tangible benefits, setbacks, and lessons drawn from organizations that have ventured into adopting these technologies. Analyzing these practical examples not only enhances understanding but also fosters a more strategic approach to decision-making. Case studies furnish insight into industry standards, showcase innovative practices, and unveil the complexities that various producers encountered during their SaaS journey.
Success Stories from Leading Manufacturers
When it comes to SaaS in manufacturing, some enterprises have jumped in with both feet and emerged victorious, setting benchmarks along the way. One compelling story is that of General Electric (GE). The company adopted a SaaS-based solution to transform its supply chain management. By shifting to a cloud-centric model, GE achieved substantial improvements in tracking their logistics. As a result, they were able to boost operational efficiency and reduce costs significantly.
In addition to cost savings, GE emphasizes how real-time data access through the SaaS framework facilitated more informed decision-making. No longer bound by legacy systems, they could adjust production schedules on the fly, respond promptly to market changes, and refine inventory processes. Their experience reflects the adaptability and resilience that SaaS can offer, especially to an industry as dynamic as manufacturing.
Another notable success can be observed in Boeing. The aviation titan leveraged SaaS for advanced analytics in its production lines. The platform provided insights on production bottlenecks that were often invisible with traditional methods. Streamlining operations led to heightened output and diminished downtime, thereby directly contributing to Boeing’s bottom line. The lesson here is clear: integrating SaaS solutions can significantly empower manufacturers to take control of their processes, make quicker adjustments, and in turn, enhance productivity levels.
Lessons Learned from Failed Implementations
While success stories provide a hopeful outlook, it is equally vital to examine instances where the attempt to implement SaaS solutions floundered. A critical case to discuss involves a well-known automotive manufacturer that embarked on a massive SaaS integration project intended to consolidate its operations across global plants. However, poor planning and insufficient training resulted in a disjointed deployment.
Many employees struggled to adapt to the new system, which led to resistance against the change, delayed communication, and ultimately a significant drop in productivity. Significantly, the organization did not align the SaaS implementation with clear business objectives. This misalignment became a costly mistake, as stakeholders lost sight of the initial purpose of the integration. A critical takeaway from this debacle is that proper change management is not just a fancy term; it's an essential step in ensuring that employee buy-in fosters a smooth transition.
Another instance of failure is seen in a smaller manufacturer that failed to conduct adequate vendor evaluation before signing a lengthy subscription. They eventually found that the features they had expected were either too limited or completely mismatched with their operational needs. This highlights the importance of pre-evaluation in selecting the right SaaS provider. The consequences of rushed decisions in SaaS can extend well beyond financial implications, affecting operational integrity and employee morale.
In summary, the lessons drawn from these failures emphasize the necessity of thorough planning, adaptation strategies, and coherent alignment with business goals when implementing SaaS solutions in manufacturing. Such cases serve as cautionary tales for the decision-makers, illustrating that the path to SaaS optimization is riddled with potential pitfalls if not approached with care and strategic foresight.
Future Trends in SaaS for Manufacturing
As we stand at the crossroad of technological advancement and enduring industry practices, understanding the future trends in SaaS for manufacturing isn't just beneficial; it's essential. Software as a Service is no longer a mere add-on to traditional manufacturing methods—it's becoming a cornerstone of operational success. Manufacturers who want to stay ahead of the curve need to recognize these trends, not just as challenges, but as opportunities ripe for innovation and efficiency.
Impact of IoT and Industry 4.
The Internet of Things (IoT) has migrated from being buzzword bingo to a crucial component of Industry 4.0. This transition is marking a major paradigm shift in how manufacturing processes are monitored and controlled. IoT devices enable real-time data collection from machinery and equipment, providing insights that were once only a distant dream.
For instance, think about a manufacturer of automotive parts. By incorporating IoT sensors, they can track machinery performance and detect anomalies before they lead to breakdowns. This not only saves costs but also minimizes downtime, a significant concern in manufacturing settings.
- Data-Driven Decisions: With the influx of data, manufacturers can make informed decisions based on trends and analytics instead of gut feelings.
- Enchanced Maintenance Protocols: Predictive maintenance allows for operations to be scheduled during non-peak times, optimizing labor and minimizing disruptions.
- Customer-Centric Manufacturing: Integrating IoT also opens avenues for greater customization. As clients' needs evolve, manufacturing processes can be adjusted accordingly, allowing for tailored production runs.
Role of AI and Machine Learning
Artificial Intelligence (AI) and Machine Learning (ML) have made strides that are as monumental as the invention of the assembly line. These technologies play a pivotal role in transforming manufacturing from reactive to proactive. AI algorithms analyze vast datasets to predict outcomes, identify inefficiencies, and suggest improvements in processes that a human couldn't pinpoint.
- Quality Assurance: AI can analyze product defects with a scrutiny that addresses concerns swiftly. A semiconductor manufacturer, for example, can utilize AI to assess tiny flaws that the naked eye might miss, improving overall product quality.
- Operational Efficiency: Machine learning can optimize supply chains by forecasting demand more accurately, which minimizes excess inventory and associated costs.
- Enhanced Worker Safety: AI applications also improve worker safety by monitoring environments and signaling when conditions reach hazardous thresholds, reducing accidents that plague factories.
Sustainability Considerations
In an era where environmental concerns are gaining unprecedented attention, the manufacturing sector is stepping up its game with sustainability at its core. SaaS solutions can help organizations adopt sustainable practices that don’t just yield compliance but also foster a positive brand image.
- Resource Optimization: SaaS platforms can analyze resource consumption patterns and suggest modifications that lead to reduced waste. For example, a beverage manufacturer may find that changing the packaging process can slash plastic use substantially.
- Regulatory Compliance: Staying on top of ever-evolving regulations can be daunting. SaaS solutions often include built-in compliance tracking that helps ensure that companies meet environmental standards.
- Engagement of Stakeholders: Applying sustainability features in manufacturing SaaS can enhance transparency. This allows consumers to make informed choices about brands that align with their values, fostering brand loyalty.
"Adopting future trends isn’t merely a choice but a necessity for businesses aiming for longevity and relevance in the manufacturing domain."
Assessing ROI of SaaS Solutions
Understanding the return on investment (ROI) of Software as a Service (SaaS) solutions is paramount for manufacturing companies. It provides a clear snapshot of how the software impacts their bottom line. The process of evaluating ROI can often be as intricate as deciphering a Rubik's cube, but with the right approach, it can yield essential insights on cost-effectiveness, efficiency, and value creation.
When considering SaaS investments, manufacturers must focus on specific elements that affect the overall expenses and gains. Measurement of benefits attributed to the adoption of SaaS is crucial, not just in terms of immediate financial returns but also concerning long-lasting advantages that can be garnered. Let's dive deeper into how manufacturers can navigate these waters effectively.
Metrics for Evaluation
To assess the ROI of SaaS solutions accurately, manufacturers should establish key performance indicators (KPIs) that align with their business objectives. Here are some relevant metrics:
- Cost Savings: Evaluate reductions in overhead and operational costs directly linked to SaaS adoption.
- Time Efficiency: Measure the time saved by automating processes that were previously manual.
- Employee Productivity: Track improvements in productivity through metrics like output per employee before and after the SaaS implementation.
- Customer Satisfaction: Analyze changes in customer feedback and retention rates, as better services can lead to enhanced satisfaction.
- Scalability Impact: Assess how quickly and cost-effectively the business can scale operations as per market demands.
"Understanding the metrics is like having a roadmap; it guides manufacturers through the complexity of ROI evaluation."
These metrics facilitate a more nuanced understanding of how SaaS investments translate into financial performance. By clearly defining these elements, businesses can identify trends and patterns that inform future decisions.
Long-Term Financial Benefits
While immediate ROI is vital, the potential long-term benefits of SaaS solutions often take center stage in decision-making processes. Some key aspects to consider include:
- Reduced Maintenance Costs: Traditional software requires continuous updates and maintenance, which can be both time-consuming and costly. SaaS models typically include these services, translating to lower overall costs over time.
- Enhanced Innovation Capabilities: With regular updates and new features, SaaS solutions foster a culture of innovation, keeping companies at the forefront of industry trends and usually correlating with improved market competitiveness.
- Mitigation of Risks: Subscription-based models distribute financial risk more evenly, allowing firms to evaluate software effectively before committing full resources. This incremental approach often leads to better long-term financial health.
- Asset Light Operations: Moving to cloud-based solutions reduces the need for heavy infrastructure investments, allowing businesses to divert funds into other critical areas.
Investing in SaaS has both immediate and protracted benefits that are often overlooked. Evaluating long-term returns can open a treasure trove of insights that significantly influence executives' strategic decisions.
Finale
The conclusion of this article serves as a critical reflection on the entire discussion surrounding SaaS solutions specifically tailored for manufacturing. It isn’t just about summarizing the key points but about synthesizing insights that resonate deeply with the industry's stakeholders. As manufacturing environments grow more complex, understanding the implications of adopting SaaS solutions becomes paramount.
Among the most pivotal elements is the recognition that the transition to SaaS isn't merely a technological shift; it requires an organizational mindset that embraces change. The advantages of SaaS, such as cost savings, flexibility, and accessibility to real-time data, position businesses to operate with greater agility in a market that demands quick adaptation. Moreover, the discussion around deployment strategies and integration processes highlights the necessity for careful planning and execution.
In essence, effective decision-making in this arena hinges on a holistic view of the factors at play—both the immediate benefits and the long-game considerations. It is crucial for decision-makers in manufacturing to weigh these insights against their unique operational landscapes.
"Choosing a SaaS solution is not just about software; it's about setting a foundation for future growth and efficiency."
Summarizing Key Insights
Delving back into the specifics discussed, a few key insights crystallize:
- Cost Efficiency: SaaS solutions often reduce the need for hefty upfront investments in software and hardware. Instead, manufacturers can harness subscription models that align payment structures directly with usage and value gained.
- Scalability: The inherent flexibility of SaaS systems enables manufacturers to easily scale up or down based on shifting operational demands without drastic lead times or resource allocation issues.
- Real-Time Insights: Access to data in real-time transforms decision-making capabilities. This visibility into operations lets manufacturers respond swiftly to changes, optimizing workflows and improving overall productivity.
These insights sketch a clearer picture of why SaaS solutions are becoming essential for manufacturers striving to maintain a competitive edge.
Encouraging Informed Decision-Making
Emphasizing informed decision-making is vital as businesses evaluate potential SaaS solutions. It begins with a thorough understanding of individual business needs, which can vary widely across the manufacturing spectrum. Companies must ask themselves:
- What are the specific operational challenges that SaaS can address?
- How do various SaaS features align with our long-term strategic goals?
- Are basic training and support structures in place to ease the transition?
Moreover, a careful evaluation of vendor capabilities is crucial. Not all SaaS providers offer the same level of service or support. It’s prudent to seek vendors who demonstrate a strong track record in the manufacturing sector, offering tailored solutions that speak directly to manufacturing challenges.