Unlocking Efficiency: A Comprehensive Guide to Material Resource Planning Implementation
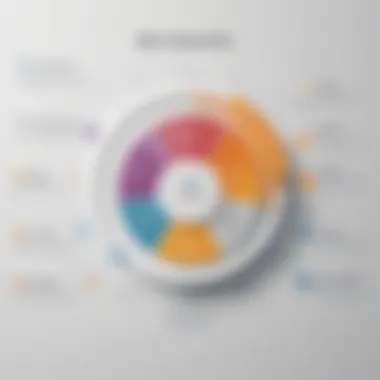
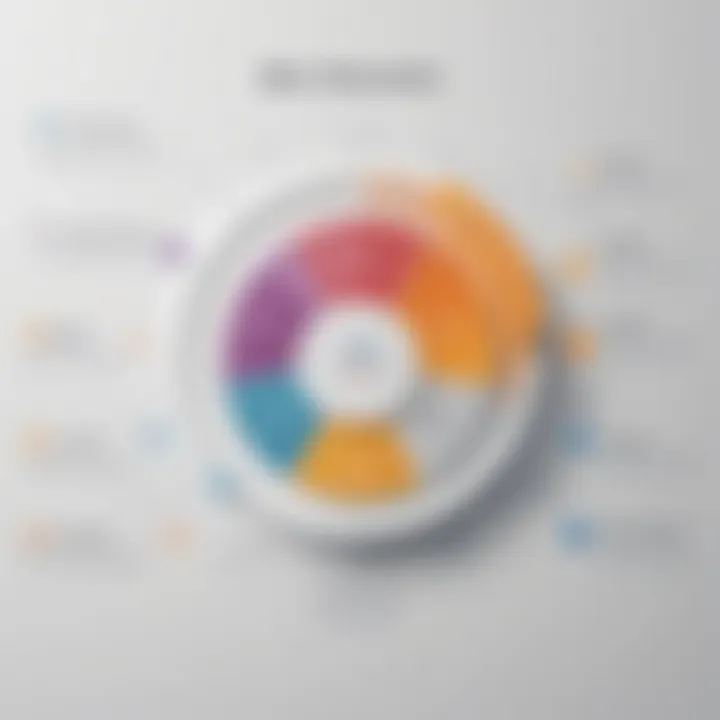
Industry Overview
Material Resource Planning (MRP) stands as a cornerstone for optimizing resource utilization and streamlining production processes within the manufacturing sector. In today's dynamic business landscape, the effective implementation of MRP can significantly enhance operational efficiency and drive sustainable growth. With advancements in technology and evolving market demands, the role of MRP has become paramount in enabling organizations to efficiently manage their material resources.
Current Trends in the Industry-specific Software Market
The industry-specific software market is witnessing a surge in innovative solutions tailored to enhance MRP functionalities. Key trends include the integration of artificial intelligence and machine learning algorithms to forecast demand more accurately, cloud-based platforms for seamless accessibility, and real-time data analytics for decision-making. These trends are reshaping how manufacturers approach resource planning and are revolutionizing traditional operational models.
Key Challenges Faced by Buyers in the Industry
Despite the transformative potential of MRP software, buyers often encounter challenges when selecting the right solution for their needs. Common issues include scalability limitations, inadequate customization options, and difficulties in integrating MRP systems with existing infrastructures. Addressing these challenges is pivotal for maximizing the benefits of MRP and ensuring a smooth implementation process.
Emerging Technologies Impacting the Industry
The convergence of emerging technologies such as Internet of Things (IoT) devices, blockchain solutions, and predictive analytics is redefining the manufacturing landscape. These technologies have the potential to revolutionize how materials are sourced, tracked, and utilized in production processes. Leveraging these innovations alongside MRP systems can unlock new levels of operational efficiency and competitiveness.
Top Software Options
In the realm of MRP software, several leading providers offer robust solutions to meet the diverse needs of manufacturers. Evaluating key players in the market, including their features, functionalities, and pricing structures, is crucial for making an informed decision. By comparing top software options, businesses can identify the most suitable solution that aligns with their operational requirements and budget constraints.
Review of Leading Software Providers in the Industry
Analyzing the performance and reputation of leading MRP software providers is essential for selecting a reliable partner. Factors such as customer reviews, vendor reliability, and software scalability should be carefully assessed to ensure a seamless implementation process and long-term satisfaction. Through a comprehensive review of software providers, organizations can mitigate risks and maximize the benefits of their investment.
Feature Comparison of Top Software Solutions
A detailed feature comparison of top MRP software solutions offers valuable insights into their functionalities and performance. Key considerations may include inventory management capabilities, production scheduling algorithms, real-time tracking features, and integration options with other enterprise systems. By identifying the distinctive features of each software solution, decision-makers can make a well-informed choice that aligns with their operational objectives.
Pricing Structures of Different Software Options
Understanding the pricing structures of different MRP software options is crucial for budget planning and cost optimization. Factors such as licensing models, subscription tiers, implementation fees, and maintenance costs should be carefully evaluated to determine the total cost of ownership. By comparing pricing structures, organizations can select a cost-effective software solution that delivers maximum value for their investment.
Selection Criteria
Selecting the most suitable MRP software involves considering a range of important factors to meet specific business requirements. From functionality and scalability to vendor support and upgrade policies, decision-makers must prioritize criteria that align with their operational goals. By establishing clear selection criteria, organizations can streamline the software selection process and choose a solution that best fits their unique needs.
Important Factors to Consider When Choosing Software
Critical factors to consider when choosing MRP software include scalability to accommodate business growth, customization options to adapt to unique processes, integration capabilities for seamless data flow, and compliance with industry regulations. These factors play a key role in determining the effectiveness and efficiency of the software in optimizing material resource planning processes.
Common Mistakes to Avoid During the Selection Process
Avoiding common mistakes during the selection process is vital to ensuring a successful implementation of MRP software. Misjudging scalability requirements, overlooking integration complexities, disregarding user training needs, and underestimating maintenance costs are frequent pitfalls that can hinder the software's performance. By learning from these mistakes, organizations can make informed decisions and avoid potential setbacks.
How to Determine the Right Fit for Your Business Needs
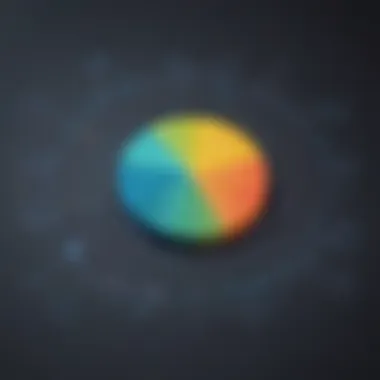
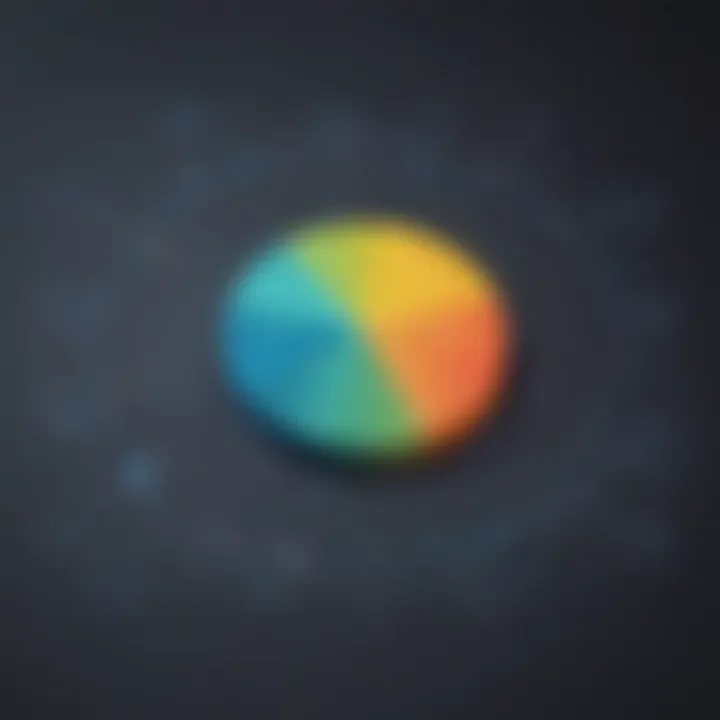
Determining the right fit for your business needs involves aligning software capabilities with operational objectives and future growth strategies. Conducting thorough assessments of vendor reputation, software features, implementation timelines, and training resources can help organizations make a well-informed choice. By aligning the software selection process with business needs, organizations can optimize their material resource planning capabilities and drive long-term value.
Implementation Strategies
Implementing MRP software necessitates adopting best practices to ensure a smooth transition and maximize the software's benefits. Strategies for successful implementation may include conducting a thorough gap analysis, engaging key stakeholders early on, establishing clear project timelines, and providing robust training resources for end-users. By following proven implementation strategies, organizations can accelerate the adoption of MRP software and realize tangible improvements in operational efficiency.
Best Practices for Smooth Implementation of Software Solutions
Adhering to best practices for the implementation of MRP software is essential for achieving positive outcomes and minimizing disruptions. Key practices may involve appointing a dedicated implementation team, conducting comprehensive data migration tests, conducting regular performance evaluations, and soliciting feedback from end-users. By embracing best practices, organizations can streamline the implementation process and drive successful adoption of MRP software.
Integration with Existing Systems and Processes
Integrating MRP software with existing systems and processes requires careful planning and execution to ensure seamless data flow and compatibility. Compatibility assessments, data mapping exercises, API integrations, and user acceptance testing are integral steps in achieving successful integration. By prioritizing integration efforts, organizations can leverage the full potential of MRP software and enhance overall operational efficiency.
Training and Support Resources for Successful Deployment
Providing comprehensive training and support resources for end-users is instrumental in the successful deployment of MRP software. Tailored training programs, user manuals, online tutorials, and dedicated support channels can empower employees to effectively utilize the software and maximize its functionality. By investing in training and support resources, organizations can enhance user proficiency, boost productivity, and drive operational excellence.
Future Trends
Anticipating future trends in the industry-specific software landscape is essential for staying ahead of the curve and embracing innovative technologies. Predictions for upcoming trends may include the proliferation of AI-powered predictive analytics, enhanced IoT-based connectivity, and the adoption of blockchain for supply chain transparency. By staying informed about future trends, organizations can future-proof their technology stack and remain competitive in a rapidly evolving market.
Predictions for the Future of the Industry-specific Software Landscape
Predicting the future evolution of industry-specific software points towards a greater emphasis on automation, real-time collaboration tools, and heightened cybersecurity measures. The integration of advanced technologies such as augmented reality for remote diagnostics and 3D printing for rapid prototyping may reshape how manufacturers approach production processes. By proactively envisioning future developments, organizations can prepare for upcoming changes and capitalize on emerging opportunities.
Upcoming Technologies Shaping the Industry
Upcoming technologies shaping the manufacturing industry offer new possibilities for enhancing operational efficiency and driving innovation. Technologies such as cloud computing for scalability, edge computing for real-time data processing, and digital twins for virtual simulations are poised to revolutionize traditional manufacturing practices. Embracing these technologies alongside MRP solutions can empower organizations to optimize resource utilization and fuel sustainable growth.
Recommendations for Future-Proofing Your Technology Stack
Recommendations for future-proofing your technology stack include investing in flexible software solutions, prioritizing data security measures, fostering a culture of innovation, and staying abreast of emerging technologies. By building a resilient technology infrastructure that is adaptable to change and scalable to future demands, organizations can navigate industry disruptions with confidence and seize opportunities for long-term success.
Conclusion
Introduction to Material Resource Planning
Material Resource Planning (MRP) plays a vital role in the manufacturing sector, optimizing resource allocation and enhancing production processes. In this article, we delve deep into the fundamental aspects of MRP, shedding light on its significance and impact on operational efficiency. Understanding MRP is crucial for businesses aiming to streamline their manufacturing operations, minimize wastage, and improve overall productivity.
Understanding MRP Fundamentals
A Brief Overview of Material Resource Planning
Material Resource Planning serves as the backbone of efficient production management. It involves the systematic planning and control of all resources required for manufacturing a product, ensuring a seamless workflow from raw materials to the finished goods. The ability of MRP to forecast material requirements and track inventory levels in real-time distinguishes it as a pivotal tool for optimizing resource utilization in manufacturing settings. Despite its complexity, MRP simplifies production planning and inventory control, thereby contributing significantly to operational success.
The Importance of MRP in Manufacturing
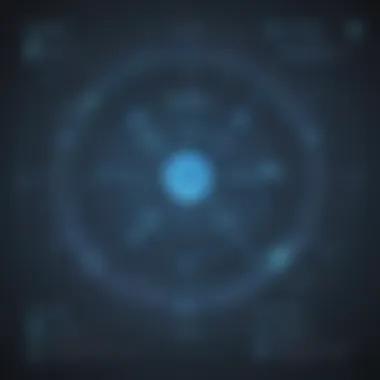
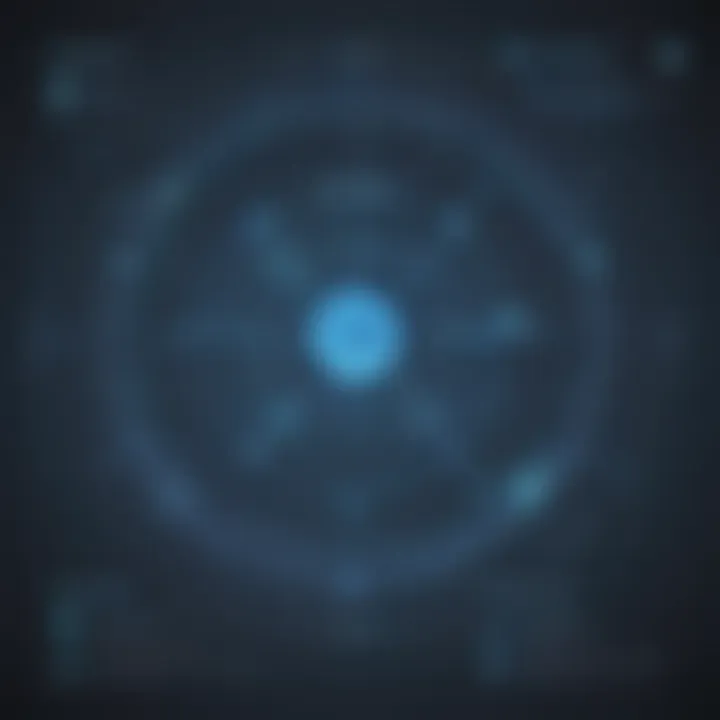
MRP holds immense importance in the manufacturing landscape due to its role in synchronizing production activities with demand forecasts. By facilitating the efficient allocation of resources, minimizing lead times, and reducing excess inventory, MRP helps organizations operate at peak efficiency. Its capability to generate accurate production schedules based on demand fluctuations makes it a valuable asset for modern manufacturing facilities. However, adopting an MRP system requires careful consideration of implementation costs, training needs, and compatibility with existing processes, ensuring a smooth integration and maximum benefits.
Key Components of MRP
Bill of Materials (BOM)
The Bill of Materials (BOM) forms the foundation of Material Resource Planning, listing all components and sub-assemblies required for the production of a finished product. By outlining the exact quantities and types of materials needed, BOM serves as a reference tool for procurement, inventory management, and production planning. Its detailed nature allows for accurate cost estimation, effective resource allocation, and smooth production workflows. However, maintaining an updated BOM poses challenges in dynamic manufacturing environments, necessitating regular revisions and thorough documentation to prevent errors and delays.
Inventory Management
Effective Inventory Management is essential for the success of any MRP system, ensuring optimal stock levels to meet production demands without incurring unnecessary costs. By implementing robust inventory control measures, businesses can prevent stockouts, minimize carrying costs, and enhance operational efficiency. Through accurate demand forecasting, real-time inventory tracking, and strategic reorder point planning, Inventory Management within MRP systems enables businesses to maintain a competitive edge in the market. Nevertheless, achieving optimal inventory levels requires a balance between demand fluctuations, lead times, and carrying costs, necessitating continuous monitoring and adjustment.
Master Production Schedule (MPS)
The Master Production Schedule (MPS) acts as a detailed plan that specifies the production quantities, schedules, and resources required to meet customer demands and maintain inventory levels. By balancing production capacity with demand forecasts, MPS serves as a linchpin for effective resource allocation and production planning within an MRP framework. Its ability to synchronize production activities across different departments, manage lead times, and optimize workforce utilization makes it a critical component for achieving operational excellence. However, creating a realistic and feasible MPS entails aligning production goals with resource availability, market demands, and unforeseen disruptions, necessitating regular updates and refinement for maximum efficiency.
Implementing MRP System
Material Resource Planning is a critical aspect of efficient resource utilization in manufacturing. Implementing an MRP system involves strategic planning and execution to streamline production processes. Companies benefit from accurate demand forecasting, inventory optimization, and synchronized production schedules. By integrating MRP software, businesses can enhance productivity and minimize operational costs.
Preparing for MRP Implementation
Data Collection and Analysis
Data Collection and Analysis play a pivotal role in MRP implementation. By gathering and analyzing relevant data, organizations can make informed decisions to drive operational efficiency. The key characteristic of data collection is its ability to provide insights into demand patterns, supplier performance, and production requirements. This process is vital for aligning production goals with market demand and optimizing inventory levels efficiently.
Defining Production Goals
Defining clear and achievable production goals is essential for successful MRP implementation. Establishing specific targets for manufacturing output, quality standards, and lead times is crucial for driving operational performance. The key characteristic of defining production goals lies in setting measurable objectives that align with business strategy. This approach ensures that the MRP system supports overall organizational objectives and enhances competitiveness in the market.
Selecting MRP Software
Evaluating Software Options
Evaluating different MRP software options is a crucial step in the implementation process. Organizations must consider factors such as scalability, user-friendliness, and compatibility with existing systems. The key characteristic of evaluating software lies in identifying a solution that meets the company's specific requirements and budget constraints. This comprehensive assessment ensures that the chosen software aligns with business objectives and can effectively enhance operational efficiency.
Vendor Assessment
Conducting a thorough vendor assessment is essential for selecting the right MRP software provider. Evaluating vendors based on their reputation, track record, and level of support is crucial for successful implementation. The key characteristic of vendor assessment is choosing a reliable partner who can deliver customized solutions and ongoing technical assistance. This partnership is vital for the long-term success of the MRP system and its integration with existing processes.
Integration with Existing Systems
Data Migration
Efficient data migration is a critical aspect of integrating the MRP system with existing systems. Ensuring seamless transfer of data from legacy systems to the new platform is essential for continuity in operations. The key characteristic of data migration is its ability to preserve data integrity, minimize disruptions, and facilitate a smooth transition. This process ensures that historical information remains accessible and usable within the updated MRP framework.
Training Staff
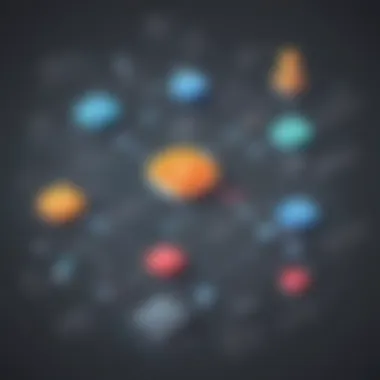
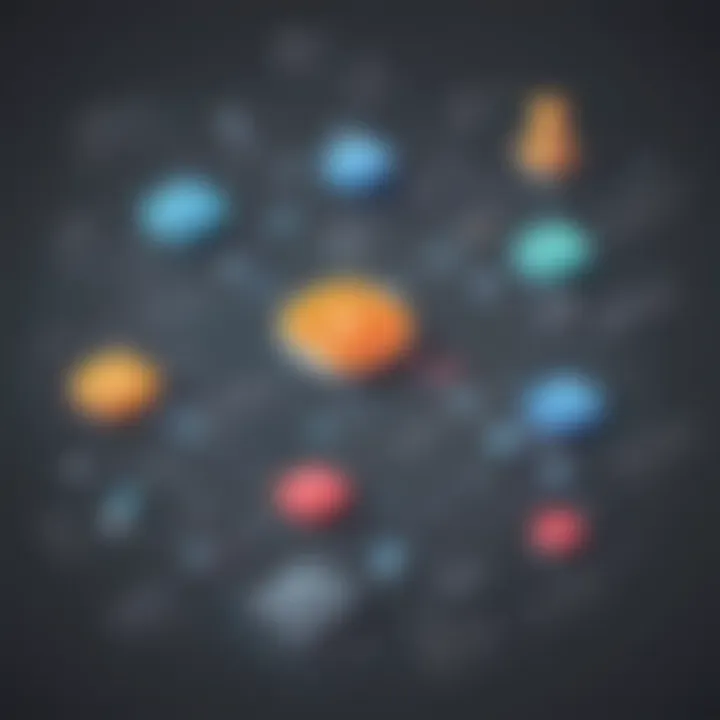
Properly training staff on the new MRP system is essential for successful implementation and adoption. Providing comprehensive training programs helps employees understand the system's functionality, features, and benefits. The key characteristic of staff training is enabling employees to navigate the MRP software confidently and perform their tasks effectively. This investment in training enhances employee productivity, reduces errors, and maximizes the system's potential for improving operational efficiency.
Optimizing Production with MRP
In this section, we delve into the critical aspect of Optimizing Production with Material Resource Planning (MRP). By focusing on maximizing efficiency and productivity within the production processes, optimizing production with MRP becomes paramount in ensuring streamlined operations and resource utilization. The importance of this topic lies in its ability to enhance overall operational performance and cost-effectiveness in a manufacturing setting. By implementing efficient MRP strategies, organizations can minimize waste, improve coordination between departments, and ultimately boost their competitive edge in the market. This discussion will outline specific elements such as workflow automation, communication enhancement, and inventory management, all contributing significantly to optimizing production with MRP.
Streamlining Processes
Automating Workflows
Automating workflows plays a pivotal role in streamlining production processes with MRP. By automating repetitive tasks and standardizing procedures, organizations can enhance operational efficiency, reduce errors, and ensure consistent output quality. The key characteristic of automating workflows lies in its ability to accelerate production timelines, minimize manual interventions, and facilitate real-time monitoring of tasks. This feature is particularly beneficial in eliminating bottlenecks, enhancing productivity, and promoting a seamless flow of operations within the manufacturing landscape. While automating workflows offers numerous advantages in increased productivity and reduced lead times, organizations must also be cautious of potential challenges such as system compatibility issues or the need for continuous updates to maintain optimal functionality.
Enhancing Communication
Enhancing communication is vital for effective MRP implementation and production optimization. By improving interdepartmental collaboration, sharing real-time data insights, and fostering transparent communication channels, organizations can streamline decision-making processes, reduce delays, and enhance overall operational agility. The key characteristic of enhancing communication lies in its ability to break down silos, ensuring timely information exchange, and promoting cross-functional alignment towards common goals. This feature is popular for its role in fostering a culture of collaboration, innovation, and adaptability within manufacturing organizations. While enhancing communication offers advantages in improved coordination and faster response times, organizations must also consider challenges such as data security concerns or the need for comprehensive training to utilize communication tools optimally.
Managing Inventory Efficiently
Just-in-Time Inventory
Just-in-Time (JIT) Inventory management is a crucial aspect of optimizing production with MRP. By implementing JIT strategies, organizations can reduce inventory holding costs, limit excess stock levels, and respond more promptly to customer demands. The key characteristic of JIT inventory lies in its focus on minimizing waste, improving cash flow, and aligning production with actual demand. This approach is popular for its ability to enhance supply chain efficiency, reduce lead times, and optimize operational performance. The unique feature of JIT inventory management lies in its 'pull' system, where inventory is replenished only when needed, reducing storage requirements and ensuring a continuous flow of materials within the production cycle. Despite its advantages in inventory cost savings and improved responsiveness, organizations must be mindful of potential drawbacks such as supply chain disruptions or the need for reliable demand forecasting methods.
Forecasting Demand
Forecasting demand is a critical component of managing inventory efficiently with MRP. By accurately predicting future demand trends, organizations can optimize production schedules, maintain ideal inventory levels, and prevent stockouts or overstock situations. The key characteristic of demand forecasting lies in its ability to inform production planning, resource allocation, and inventory replenishment decisions based on market indicators and consumer behavior patterns. This strategy is beneficial for enhancing operational flexibility, minimizing forecast errors, and meeting changing customer requirements efficiently. The unique feature of demand forecasting is its use of quantitative and qualitative methods to estimate future demand scenarios, allowing organizations to make data-driven decisions and adapt quickly to market dynamics. While demand forecasting offers advantages in inventory optimization and cost control, organizations must address challenges such as demand volatility or the need for continuous recalibration of forecasting models to ensure accuracy and responsiveness.
Measuring MRP Performance
In the realm of Material Resource Planning (MRP), measuring performance is a critical aspect that demands meticulous attention. Effective measurement not only gauges the efficiency of resource utilization but also assesses the overall operational effectiveness within manufacturing environments. By delving into Measuring MRP Performance, organizations can pinpoint strengths, weaknesses, and areas for enhancement. This section sheds light on the importance of measuring MRP performance in aligning operational strategies with performance outcomes.
KPIs for MRP Evaluation
KPIs, or Key Performance Indicators, serve as compasses guiding organizations towards achieving MRP optimization. Within the context of MRP Evaluation, examining specific key indicators becomes imperative for enhancing decision-making and operational outcomes. Two significant KPIs β Inventory Turnover Ratio and Order Fulfillment Rate β play pivotal roles in evaluating MRP performance and identifying areas for improvement.
Inventory Turnover Ratio
The Inventory Turnover Ratio showcases the efficiency of inventory management processes within the MRP framework. Calculated by dividing the cost of goods sold by the average inventory value, this ratio unveils how effectively a company utilizes its inventory. In this article, the Inventory Turnover Ratio stands out as a fundamental metric for assessing inventory management efficiency and identifying potential bottlenecks. Its unique characteristic lies in providing insights into the frequency at which inventory is replenished and sold, hence aiding in inventory optimization strategies. Understanding the nuances of Inventory Turnover Ratio equips professionals with a strategic tool to streamline inventory operations and enhance overall MRP performance.
Order Fulfillment Rate
Order Fulfillment Rate serves as a pivotal metric in the realm of MRP Evaluation, epitomizing a company's ability to meet customer demand promptly and accurately. This metric highlights the percentage of customer orders fulfilled within a specific timeframe, reflecting operational efficiency and customer satisfaction levels. Within this article, the Order Fulfillment Rate emerges as a vital indicator for assessing production and distribution capabilities while ensuring customer-centricity. Its uniqueness lies in providing a direct reflection of operational agility and effectiveness in meeting customer demands, underscoring the significance of seamless order fulfillment processes. Professionals leveraging insights from Order Fulfillment Rate can fine-tune production schedules, optimize inventory levels, and improve customer service levels effectively.
Continuous Improvement Strategies
Continuous improvement is the cornerstone of success in MRP environments, fostering a culture of innovation and adaptability. By embracing Continuous Improvement Strategies, organizations can proactively identify inefficiencies, address root causes, and enhance operational performance. This section accentuates the significance of perpetual enhancement through two key strategies: Root Cause Analysis and Feedback Loops.
Root Cause Analysis
Root Cause Analysis delves deep into identifying the underlying reasons for operational challenges and disruptions within the MRP ecosystem. By pinpointing the root causes of issues, organizations can implement targeted solutions, thereby mitigating risks and optimizing processes. Within this article, Root Cause Analysis emerges as an indispensable tool for problem-solving and decision-making, enabling professionals to address issues at their core. Its unique feature lies in promoting a systematic approach towards issue resolution, fostering a proactive and data-driven culture within organizations. Leveraging Root Cause Analysis empowers organizations to develop sustainable solutions, drive process efficiency, and elevate overall operational performance.
Feedback Loops
Feedback Loops represent a dynamic mechanism for capturing insights, experiences, and suggestions from various stakeholders involved in the MRP ecosystem. By closing the feedback loop, organizations can harness valuable information to drive continuous improvement, refine strategies, and enhance operational agility. In this article, Feedback Loops emerge as invaluable assets for fostering communication, enhancing collaboration, and fostering a culture of learning and development. Their uniqueness lies in facilitating iterative improvements based on real-time feedback, promoting adaptability and innovation within organizational processes. Integrating Feedback Loops empowers professionals to gather diverse perspectives, address pain points effectively, and drive systematic enhancements across the MRP landscape.