Elevating Manufacturing Operations: The Power of Project Management Software Solutions

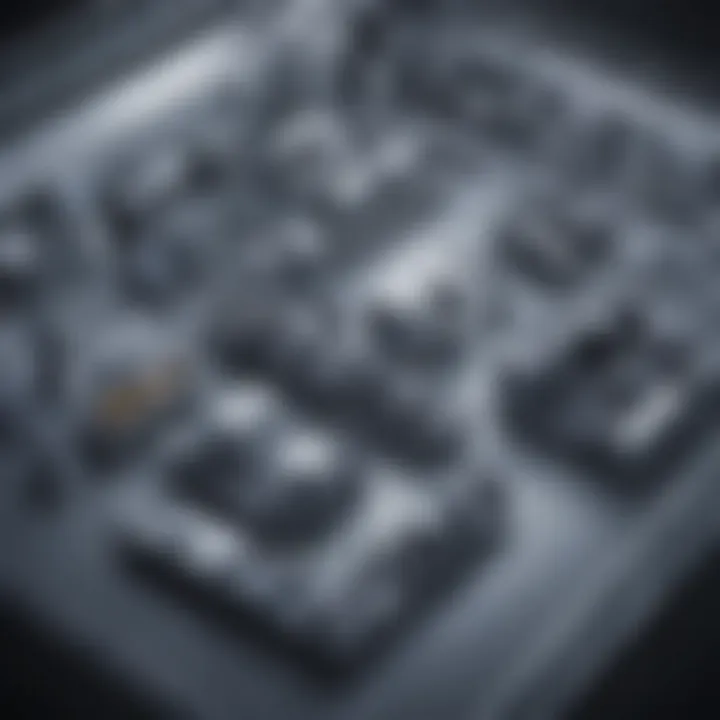
Industry Overview
In the dynamic landscape of the manufacturing industry, the integration of project management software has emerged as a pivotal factor for driving operational efficiency, optimizing resources, and ensuring project success. Faced with increasing complexities and demands, manufacturers are turning to advanced software solutions tailored specifically to their sector to streamline operations and enhance productivity. By examining the key trends, challenges, and technologies shaping the industry, businesses can gain a comprehensive understanding of the transformative impact of software solutions.
Top Software Options
As manufacturers navigate the vast array of project management software available in the market, evaluating the leading providers becomes crucial. Conducting a thorough review of the top software solutions, comparing their features, and analyzing pricing structures can aid decision-makers in selecting the most suitable option for their business needs. Delving into the specifics of each software provider empowers industry professionals to make informed choices that align with their operational requirements.
Selection Criteria
When embarking on the journey of choosing project management software, it is essential to consider a range of factors that can significantly impact its effectiveness. Understanding the important criteria for selection, avoiding common pitfalls in the decision-making process, and honing in on the right fit for specific business needs are pivotal steps in optimizing manufacturing project management. By detailing the selection process intricacies, this section aims to equip readers with the knowledge necessary to make strategic software choices.
Implementation Strategies
The successful implementation of project management software hinges on diligent planning, effective integration with existing systems, and comprehensive training and support mechanisms. Exploring best practices for seamless software deployment, strategies for integration, and available resources for training can facilitate a smooth transition for businesses. By emphasizing the importance of implementation strategies, this section aims to guide industry professionals towards a successful adoption of software solutions.
Future Trends
Looking ahead, the future of project management software in manufacturing appears promising, with the continual evolution of technology playing a significant role in shaping industry landscapes. By delving into future predictions, upcoming technologies, and recommendations for future-proofing technology stacks, businesses can proactively anticipate and adapt to changing dynamics. Navigating future trends enables organizations to stay ahead of the curve and leverage software innovations for sustained growth and competitiveness.
Introduction
In the realm of manufacturing, the utilization of project management software stands as a pivotal aspect in driving operational efficiency, optimizing processes, and ensuring the successful execution of projects. This article sheds light on the essential role of project management software tailored specifically for the manufacturing sector. By incorporating advanced software solutions, businesses can effectively navigate through intricate tasks, allocate resources judiciously, and uphold project timelines. Ultimately, the integration of such solutions culminates in heightened productivity levels and enhanced profitability, underlining the transformative potential of technology within manufacturing project management.
Understanding the Need for Project Management Software in Manufacturing
The Evolving Landscape of Manufacturing Operations
The contemporary industrial landscape has witnessed a profound shift in manufacturing operations, catalyzed by technological advancements and market demands. This evolution underscores the fundamental necessity for project management software in streamlining production processes, enhancing quality control measures, and ensuring operational cohesion. The dynamic nature of modern manufacturing necessitates a flexible and responsive approach, with software solutions offering customizable frameworks that align seamlessly with evolving industry requirements. By harnessing the power of project management software, manufacturing entities can adapt swiftly to market fluctuations, operational challenges, and technological innovations, thereby gaining a competitive edge in a rapidly changing environment.
Challenges Faced in Traditional Project Management Approaches
Traditional project management methodologies often grapple with inherent limitations that impede operational efficiency and project success within the manufacturing domain. These conventional approaches are characterized by rigid structures, limited scalability, and fragmented communication channels, rendering them ill-equipped to address the complexities of modern manufacturing processes. Furthermore, reliance on manual intervention in traditional project management poses challenges in resource allocation, task coordination, and real-time monitoring, leading to inefficiencies and operational bottlenecks. The advent of project management software transcends these challenges by offering intuitive interfaces, automated functionalities, and comprehensive data analytics, empowering manufacturing stakeholders to overcome traditional constraints and optimize performance levels effectively.
Key Features of Manufacturing Project Management Software
In the realm of manufacturing project management, software solutions play a vital role in optimizing efficiency and ensuring project success. These systems offer a host of key features that are tailored to the unique requirements of the manufacturing sector. One such crucial aspect is resource allocation and tracking, which involves real-time resource monitoring and optimization of resource utilization. By enabling real-time resource monitoring, businesses can accurately track and manage their resources throughout the project lifecycle, ensuring optimal utilization and timely adjustments. This feature aids in identifying bottlenecks, allocating resources efficiently, and maintaining project timelines.
Resource Allocation and Tracking
Real-time Resource Monitoring
Real-time resource monitoring stands as a pivotal element in the effective management of manufacturing projects. This feature provides a detailed view of resource utilization at any given moment, allowing project managers to make informed decisions promptly. The ability to monitor resources in real-time enhances project visibility, identifies potential issues early on, and supports agile decision-making. While real-time resource monitoring streamlines operations and minimizes delays, ensuring resource availability when needed; for large-scale projects, it might induce information overload and require streamlined data visualization techniques.
Optimization of Resource Utilization
Optimization of resource utilization underscores the importance of maximizing the efficiency of available resources within manufacturing projects. This feature focuses on aligning resource allocation with project requirements, minimizing waste, and enhancing productivity. By optimizing resource utilization, businesses can reduce costs, improve operational performance, and meet project deadlines effectively. However, challenges may arise in maintaining a balance between resource optimization and preventing resource exhaustion, needing constant monitoring and adjustment for sustained efficiency gain.
Task Scheduling and Automation
Automated Task Assignment
Automated task assignment emerges as a cornerstone feature in manufacturing project management software. This functionality streamlines the task delegation process by automatically assigning tasks based on predefined criteria and resource availability. Automated task assignment not only saves time but also ensures equitable workload distribution and improved task prioritization. The automated nature of this feature enhances operational efficiency, reduces the risk of manual errors, and fosters better collaboration among team members. However, customization options and adaptability for complex task structures could be areas for continuous improvement.
Scheduling Dependencies
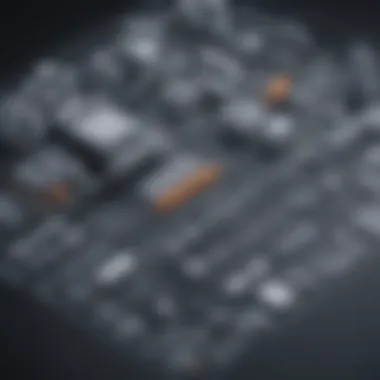
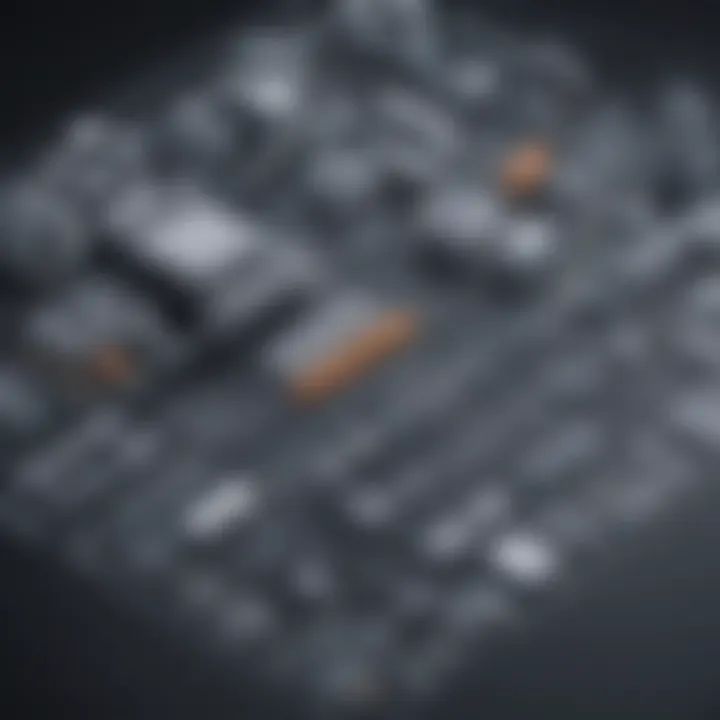
Scheduling dependencies represent a critical component of project planning and execution within manufacturing contexts. This feature allows project managers to establish interdependencies between tasks, ensuring that tasks are executed in the correct sequence. By setting up scheduling dependencies, organizations can streamline project timelines, mitigate risks, and improve overall project efficiency. Integrated dependencies play a vital role in identifying task relationships, managing critical paths, and adapting to changing project requirements. However, excessive dependencies may lead to rigid project structures, posing challenges in agile project management practices.
Financial Management Tools
Budget Tracking
Budget tracking forms the financial backbone of manufacturing project management software, enabling organizations to monitor and control project expenditures systematically. This feature tracks spending against budget allocations, identifies cost deviations, and facilitates informed financial decision-making. By implementing robust budget tracking mechanisms, businesses can avoid cost overruns, optimize resource allocation, and ensure project profitability. However, meticulous budget tracking requires consistent data input, expense categorization, and variance analysis for accurate financial insights and effective resource management.
Cost Estimation
Cost estimation functionality empowers manufacturing project managers with the capability to forecast project expenses accurately. This feature involves analyzing project requirements, resource costs, and market trends to generate realistic cost estimates for upcoming projects. Accurate cost estimations help in setting realistic project budgets, negotiating contracts efficiently, and aligning financial resources in line with project objectives. While cost estimation contributes to improved financial planning and risk assessment, the volatility of market conditions and unforeseen expenses may pose challenges in accurate cost forecasting.Readability and search visibility are essential aspects in optimizing the content for decision-makers, IT professionals, and entrepreneurs. The integration of keywords needs to be organic and strategically placed to enhance the article's SEO performance without compromising its informative value.Regular monitoring and refinement of cost estimation methods are necessary to adapt to changing market dynamics, supplier costs, or project scope revisions.
Benefits of Implementing Project Management Software in Manufacturing
In the realm of manufacturing, the significance of implementing project management software cannot be overstated. It plays a pivotal role in enhancing operational efficiency, streamlining processes, and ensuring successful project delivery. By adopting advanced software solutions tailored specifically to the manufacturing sector, businesses can effectively manage tasks, allocate and track resources, and control project timelines. These software solutions ultimately lead to improved productivity levels, driving profitability within the organization.
Enhanced Collaboration and Communication
Centralized Communication Channels
The concept of centralized communication channels rests at the core of effective project management software in the manufacturing industry. Centralization allows for seamless and efficient exchange of information within teams and across departments. This approach ensures that all stakeholders have access to necessary information promptly, facilitating quick decision-making, enhancing operational transparency, and boosting overall productivity. By utilizing centralized communication channels, manufacturing firms can align their teams, prevent miscommunications, and foster a collaborative work environment to achieve project success.
Document Sharing Capabilities
Document sharing capabilities within project management software offer indispensable benefits to manufacturing operations. This feature enables easy sharing, tracking, and management of crucial project documents, blueprints, reports, and data among team members. By providing a centralized repository for information storage and retrieval, document sharing capabilities enhance collaboration, streamline workflows, and ensure data consistency across the project lifecycle. Additionally, this feature promotes version control, reduces the risk of errors, and improves regulatory compliance by maintaining accurate and up-to-date project documentation.
Improved Decision-making Processes
Data-driven Insights
Employing data-driven insights through project management software revolutionizes decision-making processes in manufacturing. By leveraging real-time data analytics, key performance indicators, and progress reports, stakeholders can gain valuable insights into project performance metrics, resource utilization, and operational efficiency. This data-driven approach enables informed decision-making, identifies potential bottlenecks, and supports proactive problem-solving strategies to optimize project outcomes. By harnessing data-driven insights, manufacturing firms can drive continuous improvement, mitigate risks, and capitalize on growth opportunities in a competitive market landscape.
Predictive Analytics
Integrating predictive analytics capabilities into project management software empowers manufacturing organizations to forecast future trends, anticipate challenges, and make strategic decisions proactively. Predictive analytics leverages historical data, statistical algorithms, and machine learning algorithms to predict project outcomes, resource requirements, and potential risks. By embracing predictive analytics, manufacturing firms can enhance their planning processes, optimize resource allocation, and achieve operational efficiencies. This forward-looking approach enables proactive risk management, enhances cost control measures, and fosters innovation within project management practices.
Risk Mitigation and Compliance
Regulatory Compliance Monitoring
The strict regulatory landscape in manufacturing necessitates robust compliance monitoring mechanisms within project management software. Regulatory compliance monitoring ensures that projects adhere to industry standards, legal requirements, and quality certifications throughout the project lifecycle. By incorporating compliance monitoring features, manufacturing firms can track adherence to regulations, monitor audit trails, and demonstrate compliance to regulatory bodies and stakeholders. This proactive compliance management approach minimizes legal risks, enhances operational integrity, and safeguards the reputation of the organization.
Risk Assessment Tools
Integrating risk assessment tools into project management software equips manufacturing companies with the ability to identify, assess, and mitigate potential risks that may impact project outcomes. Risk assessment tools enable teams to evaluate risk factors, prioritize mitigation strategies, and develop contingency plans to mitigate adverse effects on project delivery. By utilizing these tools, manufacturing firms can proactively manage risks, improve decision-making processes, and ensure continuity in operations. This risk-aware culture fosters resilience, prepares organizations for unforeseen challenges, and bolsters project success rates.
Selecting the Right Project Management Software for Manufacturing
In the realm of manufacturing, the choice of project management software holds significant weight in steering operational efficiency and success. When selecting the right software, there are crucial elements to consider to ensure seamless integration and functionality within the manufacturing landscape. One vital aspect is the customization and scalability features offered by the software. These aspects cater to the unique requirements of the manufacturing industry, allowing for tailored solutions that align with specific needs and processes. Scalability plays a pivotal role in accommodating business growth, ensuring that the software can expand alongside evolving operational demands.
Customization and Scalability
Tailoring Features to Industry Requirements
Tailoring features to suit industry requirements is a critical component when selecting project management software for manufacturing. These tailored features are designed to address the intricacies and challenges prevalent in manufacturing operations, offering customized solutions that enhance efficiency and productivity. The ability to customize features according to specific industry demands ensures that the software aligns perfectly with the unique workflows and processes within the manufacturing environment. This tailored approach not only streamlines operations but also optimizes resource allocation and task management, leading to improved overall performance.
Ability to Scale with Business Growth
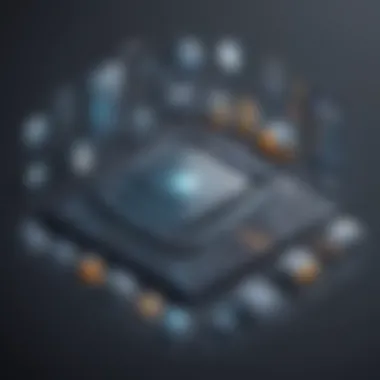
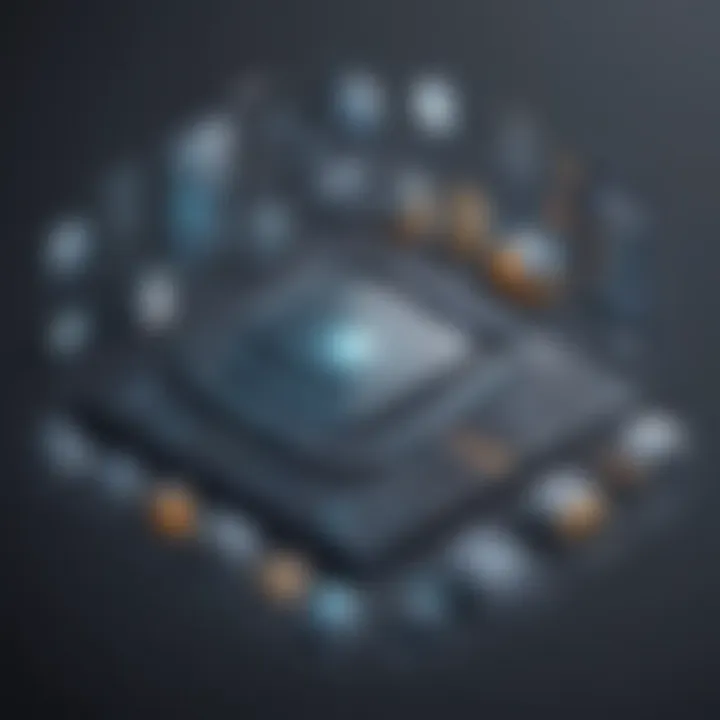
The scalability of project management software is essential for accommodating the evolving needs of a manufacturing business. A system that can scale with business growth ensures long-term viability and relevance within a dynamic industry landscape. This feature allows companies to seamlessly expand their operations without facing limitations posed by the software's capacity. The ability to scale with business growth guarantees that the software remains a sustainable and efficient solution, even as manufacturing processes and demands evolve over time.
Integration Capabilities
Seamless Integration with Existing Systems
Integrating project management software seamlessly with existing systems is paramount for ensuring smooth workflows and data accessibility within manufacturing operations. A software solution that can seamlessly integrate with current systems streamlines processes, reduces data silos, and fosters cross-departmental collaboration. This seamless integration enhances overall efficiency by providing a unified platform for managing projects, resources, and data, thereby optimizing decision-making processes across the manufacturing ecosystem.
Compatibility with Third-party Applications
The compatibility of project management software with third-party applications is a key consideration for manufacturing companies looking to enhance their operational capabilities. Compatibility ensures that the software can interact efficiently with other tools and systems commonly used in the manufacturing domain, facilitating a cohesive and interconnected IT environment. This capability enables companies to leverage a diverse range of tools and resources, ultimately improving productivity, communication, and decision-making processes within the manufacturing setting.
User-Friendly Interface and Training
Intuitive Design for Ease of Adoption
A user-friendly interface that prioritizes ease of adoption is essential for maximizing the utility of project management software in manufacturing. An intuitive design simplifies the learning curve for employees, promoting rapid adoption and usage across different operational levels. This feature reduces training time and enhances user experience, ensuring that all team members can efficiently navigate and utilize the software to its full potential, ultimately driving productivity and operational efficiency.
Training and Support Services
Comprehensive training and support services are invaluable when implementing project management software in a manufacturing setting. These services not only facilitate seamless onboarding and integration of the software but also ensure continuous user education and skill development. Training programs equip employees with the necessary knowledge and competencies to leverage the software effectively, while ongoing support services address any issues or challenges that may arise during utilization. This focus on training and support enhances user proficiency and overall satisfaction, contributing to the successful implementation and utilization of project management software within manufacturing operations.
Implementation Strategies for Manufacturing Project Management Software
In the realm of manufacturing project management, the implementation strategies play a pivotal role in ensuring successful outcomes. Efficient implementation strategies tailored to the unique needs of the manufacturing sector can streamline operations, enhance productivity, and drive profitability. Businesses must carefully consider various elements when devising implementation strategies for manufacturing project management software. Factors such as customization, scalability, integration capabilities, user-friendly interface, and training requirements need meticulous attention to align the software with industry requirements and business objectives effectively.
Top-down Organizational Alignment
Executive Sponsorship
Executive sponsorship holds a crucial position in the overarching goal of implementing project management software in manufacturing. The key characteristic of executive sponsorship lies in its role as a bridge between strategic vision and practical execution. By securing top-level endorsement and active involvement from senior management, organizations can ensure alignment of project goals with the broader business objectives. The unique feature of executive sponsorship is its ability to provide essential resources, resolve conflicts, and drive consensus within the organization. While offering numerous advantages in terms of prioritizing projects, advocating for stakeholder interests, and ensuring accountability, executive sponsorship also poses challenges related to hierarchy resistance and decision-making delays within the implementation process.
Departmental Collaboration
Departmental collaboration significantly contributes to the successful adoption of project management software in manufacturing. The key characteristic of departmental collaboration is its emphasis on cross-functional teamwork and information sharing. By fostering collaboration among different departments involved in project execution, organizations can enhance communication, coordination, and efficiency. The unique feature of departmental collaboration is its ability to break down silos, promote innovation, and accelerate decision-making processes. Despite its many benefits in promoting a culture of knowledge exchange, improving project outcomes, and fostering organizational cohesion, departmental collaboration may face challenges related to conflicting priorities, coordination complexities, and interdepartmental conflicts.
Change Management and Employee Training
Change Readiness Assessments
Change readiness assessments play a vital role in preparing organizations for the adoption of project management software in manufacturing. The key characteristic of change readiness assessments lies in their ability to evaluate organizational readiness, identify potential barriers to change, and develop mitigation strategies. By conducting thorough assessments, organizations can enhance change management planning, stakeholder engagement, and communication strategies. The unique feature of change readiness assessments is their focus on identifying resistance points, understanding cultural dynamics, and fostering readiness for transformation. While offering advantages in terms of risk mitigation, organizational resilience, and change alignment, change readiness assessments may present challenges related to resistance to feedback, cultural inertia, and change fatigue.
Skill Development Workshops
Skill development workshops are instrumental in building capabilities and competencies required for effective utilization of project management software in manufacturing. The key characteristic of skill development workshops lies in their practical orientation, experiential learning methodologies, and targeted skill enhancement approaches. By offering hands-on training, knowledge transfer, and skill-building activities, workshops can empower employees with the requisite tools and expertise to leverage software functionalities optimally. The unique feature of skill development workshops is their focus on personalized learning pathways, competency assessments, and continuous skill enhancement. While delivering advantages such as increased employee engagement, accelerated learning curves, and enhanced job performance, skill development workshops may encounter challenges related to training costs, time constraints, and skill retention.
Continuous Monitoring and Evaluation
Performance Metrics Tracking
Performance metrics tracking plays a critical role in evaluating the effectiveness of project management software implementation in manufacturing. The key characteristic of performance metrics tracking lies in its ability to quantify progress, measure key performance indicators, and assess outcomes against predefined benchmarks. By tracking metrics such as project timelines, resource utilization, and cost efficiencies, organizations can gain valuable insights into the software's impact on operations and decision-making. The unique feature of performance metrics tracking is its capacity to facilitate data-driven evaluations, identify improvement opportunities, and support informed decision-making. While offering advantages in terms of performance transparency, benchmarking capabilities, and continuous improvement initiatives, performance metrics tracking may pose challenges related to data accuracy, metric alignment, and interpretation complexities.
Feedback Mechanisms
Feedback mechanisms play a crucial role in soliciting stakeholder input, gathering insights, and fostering organizational learning in the context of manufacturing project management software implementation. The key characteristic of feedback mechanisms lies in their responsiveness, accessibility, and iterative nature. By collecting feedback from project stakeholders, end-users, and management teams, organizations can capture performance nuances, address user concerns, and fine-tune software functionalities based on real-time inputs. The unique feature of feedback mechanisms is their ability to enhance communication channels, promote transparency, and drive continuous improvement cycles. While providing advantages such as enhanced stakeholder engagement, user satisfaction levels, and software adoption rates, feedback mechanisms may encounter challenges related to feedback overload, interpretation biases, and implementation delays.
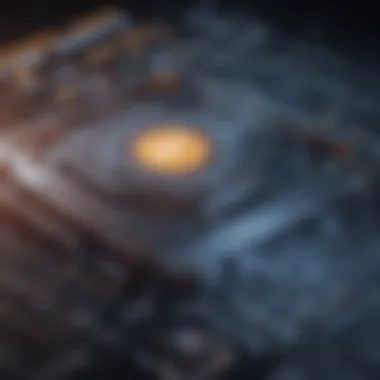
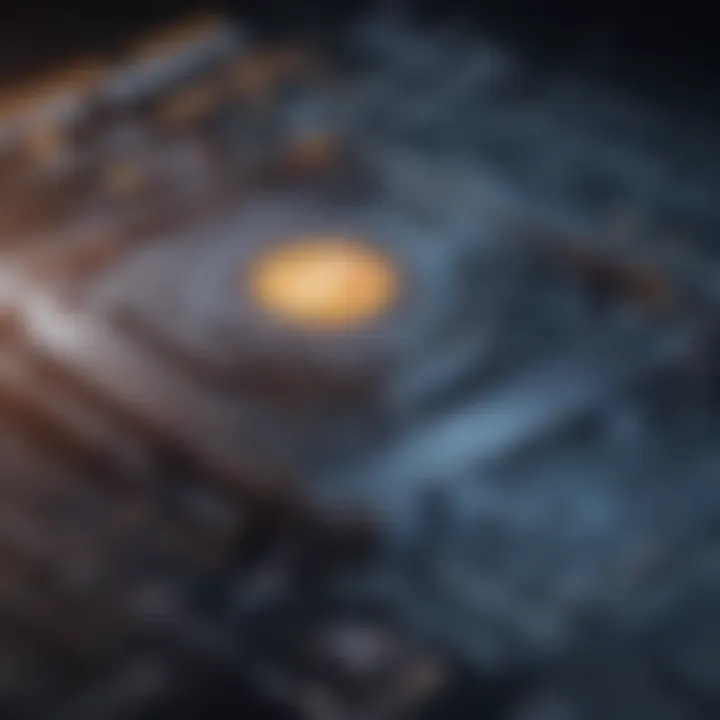
Case Studies: Success Stories of Manufacturing Companies Implementing Project Management Software
In the realm of project management software implementation in the manufacturing sector, case studies play a pivotal role in elucidating the practical benefits and outcomes. Understanding how manufacturing companies have leveraged project management software aids in grasping the tangible advantages and insights that such solutions offer. These case studies serve as exemplars of successful integration and optimization, shedding light on the nuanced application of software solutions within manufacturing contexts.
Company A: Optimization of Production Processes
Efficiency Gains:
Efficiency gains within the production processes of manufacturing companies are instrumental in enhancing operational productivity and performance metrics. The specific aspect of efficiency gains revolves around streamlining workflows, reducing idle time, and optimizing resource allocation. In the context of this article, efficiency gains are a cornerstone in achieving heightened efficiency levels and operational excellence. Their unique feature lies in their ability to identify bottlenecks, improve workflow sequences, and maximize output capacity, thereby bolstering overall production efficiency.
Cost Reductions:
Cost reductions stand as a crucial aspect impacting the financial health and sustainability of manufacturing operations. Within the purview of manufacturing project management software, the focus on cost reductions underscores strategies to cut unnecessary expenditures, optimize resource allocation, and enhance budget efficiency. The key characteristic of cost reductions is their ability to drive profitability through streamlined processes and reduced operational costs. However, the challenge lies in balancing cost reductions without compromising quality or operational integrity in the manufacturing landscape.
Company B: Streamlined Supply Chain Management
Inventory Optimization:
Inventory optimization is pivotal in ensuring smooth and efficient supply chain operations, minimizing excess inventory, and meeting consumer demand effectively. This optimization facet encompasses strategic inventory planning, efficient storage solutions, and real-time inventory tracking. Its unique feature lies in its capacity to synchronize supply and demand dynamics, reduce holding costs, and enhance operational agility within the supply chain. The advantage of inventory optimization is its ability to prevent stockouts, improve inventory turnover rates, and optimize working capital utilization.
Supplier Relationship Enhancements:
Supplier relationship enhancements in the context of streamlined supply chain management aim to fortify collaboration, communication, and efficiency in supplier interactions. The key characteristic of supplier relationship enhancements is nurturing mutually beneficial partnerships, ensuring timely deliveries, and fostering trust within the supply chain network. This feature's advantage lies in improving supplier performance, quality assurance, and reducing lead times, thus optimizing supply chain reliability and operational efficacy.
Company C: Enhanced Quality Control Measures
Defect Reduction:
Defect reduction strategies are paramount in bolstering product quality, reducing rework costs, and enhancing customer satisfaction levels. The unique feature of defect reduction lies in its proactive approach through implementing robust quality control protocols, root cause analysis techniques, and continuous improvement initiatives. This aspect's advantage is in ensuring compliance with quality standards, minimizing defects, and enhancing overall product reliability in manufacturing processes.
Compliance Standards Alignment:
Compliance standards alignment encompasses adhering to industry regulations, quality standards, and ethical practices within manufacturing operations. The key characteristic of compliance standards alignment is ensuring legal conformity, regulatory compliance, and environmental sustainability practices. Its advantage lies in mitigating risks, avoiding penalties, and upholding brand reputation through transparent and accountable manufacturing practices.
Future Trends in Manufacturing Project Management Software
In the dynamic landscape of the manufacturing sector, staying abreast of emerging trends is paramount to sustained success. The integration of AI and Machine Learning into project management software represents a significant advancement that holds great promise for streamlining processes and improving efficiency. Predictive Analytics Advancements within this context play a crucial role by harnessing data to forecast trends and anticipate potential issues. By leveraging predictive analytics, manufacturers can make informed decisions, optimize resource allocation, and enhance overall project outcomes. This feature not only offers insights into future performance but also empowers stakeholders to proactively address challenges before they escalate.
One distinctive characteristic of Predictive Analytics Advancements is its ability to analyze vast amounts of data with remarkable accuracy, leading to precise forecasts and strategic recommendations. This predictive capability enables manufacturers to allocate resources judiciously, mitigate risks, and capitalize on opportunities effectively. While the advantages of predictive analytics are numerous, including improved operational efficiency and cost savings, potential disadvantages may arise from the complexity of algorithms and the need for specialized expertise. Nonetheless, the benefits of predictive analytics far outweigh the challenges, making it an indispensable tool for driving success in manufacturing project management.
Automated Decision Support Systems constitute another key aspect of AI and Machine Learning integration that significantly enhances project management processes. These systems utilize algorithms to aid decision-making by processing data, identifying patterns, and offering actionable insights. The primary characteristic of Automated Decision Support Systems lies in their ability to expedite decision-making processes, ensure consistency, and reduce human errors. This feature is particularly advantageous for complex manufacturing projects where real-time decision support is essential.
The unique feature of Automated Decision Support Systems is their capacity to handle vast datasets efficiently, facilitating timely and informed decision-making. While the advantages of these systems encompass increased productivity, enhanced project outcomes, and improved strategic planning, potential disadvantages may arise from over-reliance on automated recommendations and the need for continuous monitoring. Nevertheless, the invaluable role played by Automated Decision Support Systems in optimizing manufacturing project management underscores its relevance and importance in driving operational excellence and agility.
IoT and Smart Manufacturing
The advent of IoT and Smart Manufacturing heralds a new era of interconnected systems and real-time data analytics in the manufacturing domain. Real-time Data Monitoring emerges as a key element in this progression, offering manufacturers the ability to capture, analyze, and act upon data instantaneously. The essence of Real-time Data Monitoring lies in its capacity to provide up-to-the-minute insights into production processes, equipment performance, and inventory levels. This feature empowers decision-makers by enabling timely interventions, resource optimization, and performance tracking.
The unique feature of Real-time Data Monitoring is its seamless integration with existing infrastructures, ensuring minimal disruption and enhanced data visibility throughout the manufacturing ecosystem. While the benefits of real-time data monitoring encompass enhanced operational efficiency, improved quality control, and streamlined decision-making, challenges may arise from data privacy concerns and the need for robust cybersecurity measures. Despite these considerations, the transformative impact of real-time data monitoring on manufacturing project management is undeniable, making it an indispensable tool for driving innovation and competitiveness.
Interconnected Production Processes represent another pivotal aspect of IoT and Smart Manufacturing, revolutionizing manufacturing operations through enhanced connectivity and collaboration. This concept emphasizes the integration of disparate production systems, IoT devices, and data streams to create a cohesive and responsive manufacturing environment. The key characteristic of Interconnected Production Processes lies in their ability to synchronize operations, automate workflows, and optimize resource utilization across the production lifecycle.
The unique feature of Interconnected Production Processes is their capacity to facilitate real-time communication, data exchange, and feedback loops, fostering agility and adaptability in manufacturing operations. While the advantages of interconnected production processes encompass increased scalability, improved production efficiency, and enhanced product quality, potential challenges may arise from interoperability issues and the complexity of integrating diverse technologies. Nevertheless, the transformative potential of interconnected production processes in optimizing manufacturing project management underscores its significance in driving operational excellence and innovation.
Blockchain Applications in Supply Chain Management
Blockchain technology is redefining supply chain management by offering enhanced transparency, traceability, and security across manufacturing operations. Enhanced Transparency emerges as a critical feature of blockchain applications, enabling stakeholders to access immutable records of transactions, product histories, and compliance certifications. The key characteristic of enhanced transparency lies in its ability to foster trust, accountability, and integrity across the supply chain ecosystem.
The unique feature of enhanced transparency is its decentralized nature, which eliminates the need for intermediaries and reduces the risk of fraudulent activities. While the benefits of enhanced transparency encompass improved traceability, reduced counterfeiting, and enhanced customer trust, potential challenges may arise from scalability limitations and regulatory compliance complexities. Nonetheless, the transformative impact of enhanced transparency in supply chain management underscores its value and relevance in driving efficiency and sustainability.
Secure Transactions represent another fundamental aspect of blockchain applications, ensuring the integrity and confidentiality of transactions within the supply chain network. The key characteristic of secure transactions lies in their encryption mechanisms, digital signatures, and distributed ledger technology, which collectively safeguard sensitive data and assets. This feature plays a pivotal role in mitigating cybersecurity threats, enhancing data privacy, and reducing transactional risks.
The unique feature of secure transactions is their tamper-resistant nature, which prevents unauthorized alterations or access to transaction records, guaranteeing transactional integrity and trust. While the advantages of secure transactions encompass enhanced data security, fraud prevention, and streamlined transactions, potential disadvantages may include implementation costs and usability challenges. However, the critical role played by secure transactions in blockchain applications for supply chain management underscores their significance in fostering transparency, accountability, and trust within the manufacturing ecosystem.
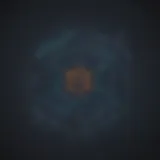
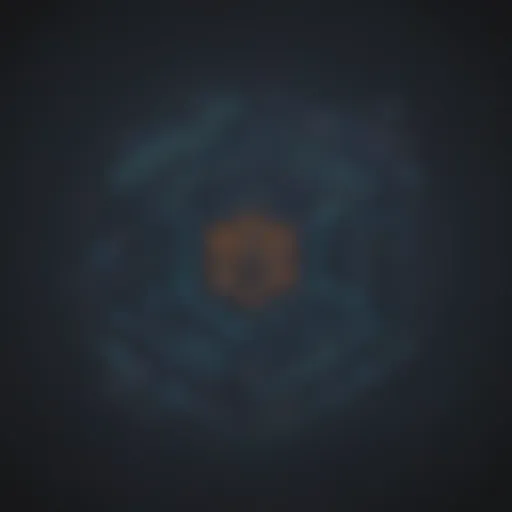