Unlocking Operational Excellence: Maintenance Management Systems Demystified
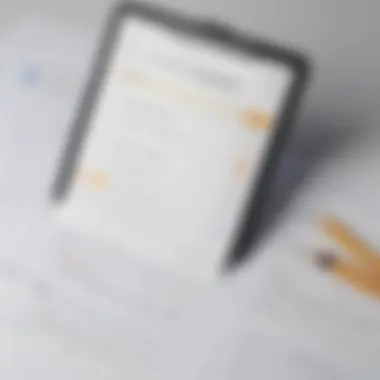
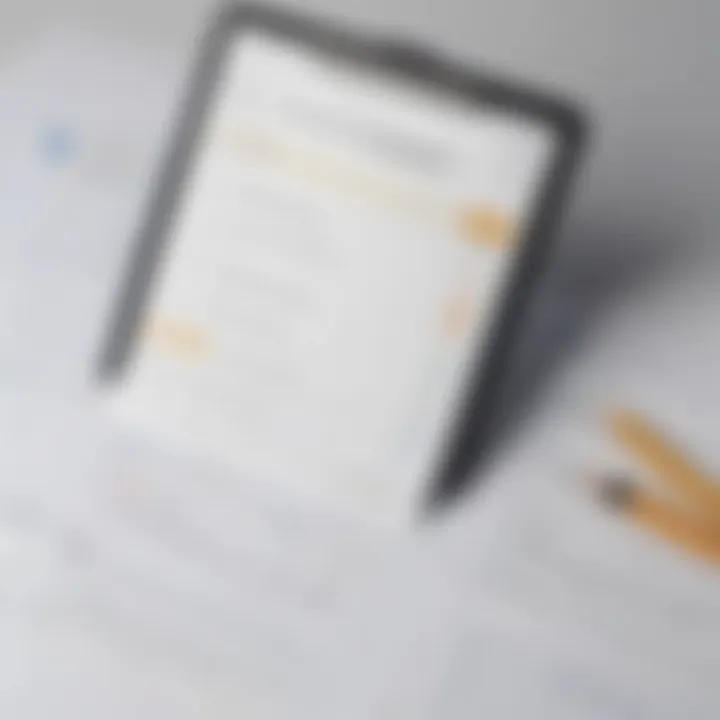
Industry Overview
Top Software Options
To optimize maintenance management systems effectively, a detailed review of leading software providers is imperative. By comparing features offered by top software solutions, businesses can determine which tools best suit their requirements. Price structures play a significant role in decision-making processes, as organizations need to assess the cost-effectiveness of different software options available in the market.
Selection Criteria
When optimizing maintenance management systems, considering various factors is essential for successful implementation. Businesses should avoid common mistakes often made during the selection process, such as overlooking specific requirements. Determining the right fit for your organization involves thorough assessment and alignment of software capabilities with your business needs.
Implementation Strategies
For enhanced operational efficiency, implementing best practices is key to the successful deployment of maintenance management software. Integration with existing systems and processes ensures a streamlined workflow and compatibility across different operational areas. Comprehensive training and support resources play a vital role in familiarizing users with the software, leading to effective utilization.
Future Trends
Looking ahead, future trends in industry-specific software solutions will shape the way organizations optimize their maintenance management systems. Emerging technologies are set to revolutionize maintenance operations, offering new possibilities for efficiency and productivity. Recommendations for future-proofing technology stacks will be essential in staying ahead of the curve and adapting to evolving industry requirements.
Introduction
In the world of operations and management, the efficacy of maintenance management systems is paramount. These systems serve as the backbone of streamlined processes, ensuring operational efficiency is achieved at optimal levels within organizations. By delving into the intricacies of maintenance management systems, businesses can revolutionize their approach to maintenance operations. This article aims to dissect the critical components and best practices associated with maintenance management systems, offering a comprehensive guide for organizations seeking to elevate their maintenance strategies.
Brief Overview of Maintenance Management Systems
Definition and Scope
One of the fundamental pillars of maintenance management systems lies in their definition and scope. This entails the comprehensive understanding of what encompasses a maintenance management system and the boundaries within which it operates. Defined by its structured approach to handling maintenance activities, the scope of a maintenance management system extends to cover preventive, corrective, and predictive maintenance, among other key areas. The flexibility of such systems allows organizations to tailor their maintenance processes to suit specific operational needs, making it a versatile and invaluable asset to enhance operational efficiency.
Importance in Operational Settings
The significance of optimal maintenance management systems in operational settings cannot be overstated. These systems play a pivotal role in minimizing downtime, reducing operational costs, and ensuring equipment reliability. By maintaining an effective maintenance management system, organizations can proactively address issues before they escalate, thereby mitigating potential disruptions to operations. This proactive approach enhances the overall operational resilience of an organization, fostering a culture of efficiency and reliability that is crucial for sustainable growth and success.
Significance of Optimal Maintenance Practices
Impact on Cost Efficiency
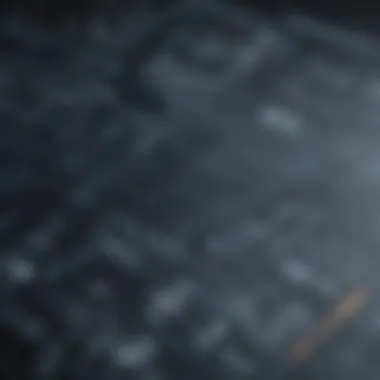
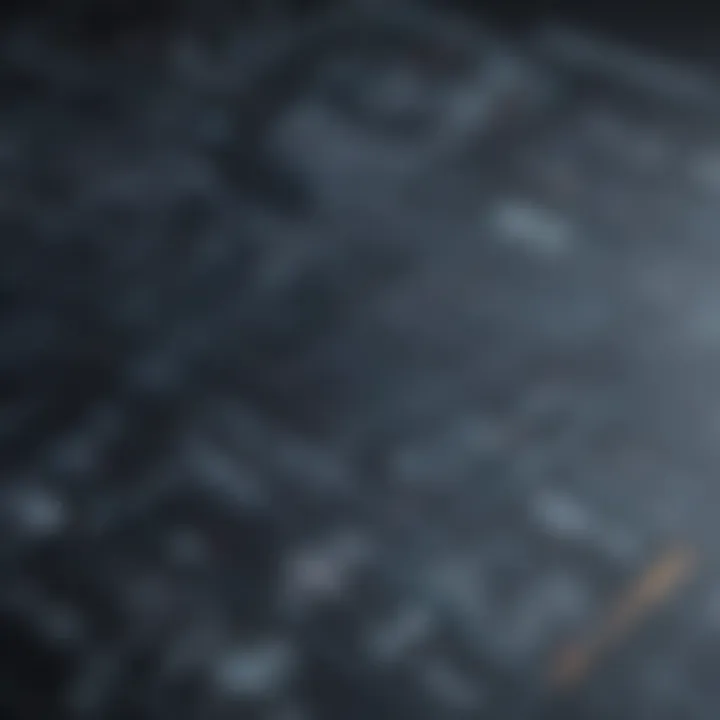
Optimal maintenance practices have a direct impact on the cost efficiency of an organization. By implementing proactive maintenance strategies, businesses can minimize unexpected breakdowns, reduce repair costs, and optimize the lifespan of their assets. This proactive approach not only decreases maintenance expenses but also contributes to overall cost savings by maximizing the operational uptime of equipment. The cost-efficient nature of optimal maintenance practices positions organizations for long-term financial sustainability and operational effectiveness.
Role in Asset Longevity
The role of optimal maintenance practices in enhancing asset longevity is pivotal. By adhering to a structured maintenance regimen that incorporates preventive and predictive maintenance techniques, organizations can extend the lifespan of their assets significantly. This approach not only safeguards investments in capital equipment but also ensures that assets operate at peak performance levels throughout their lifecycle. The longevity of assets through effective maintenance practices translates to enhanced operational efficiency and optimal resource utilization within organizations.
Purpose of the Article
Highlighting Key Strategies
One of the primary objectives of this article is to shed light on key strategies that facilitate the optimization of maintenance management systems. By identifying and highlighting these strategies, organizations can streamline their maintenance operations and enhance overall efficiency. From adopting data-driven approaches to integrating advanced technologies, an emphasis on key strategies empowers organizations to make informed decisions that drive operational excellence.
Providing Implementation Insights
Equally important is providing practical implementation insights to complement theoretical concepts. While key strategies lay the foundation for optimization, actionable insights on implementing these strategies are crucial for success. By offering guidance on effective implementation tactics, this article equips organizations with the necessary know-how to translate maintenance optimization theories into tangible results. Practical insights bridge the gap between theory and practice, enabling seamless integration of best practices into real-world maintenance operations.
Key Components of a Maintenance Management System
In the realm of maintenance management systems, understanding the key components is paramount for ensuring operational efficiency and cost-effectiveness within an organization. Asset Tracking and Inventory Management stand out as crucial elements that can significantly impact the overall effectiveness of maintenance operations. By integrating technology for tracking assets and inventory control, businesses can streamline processes, optimize resource allocation, and minimize downtime. Leveraging technology in asset tracking allows for real-time monitoring, precise inventory management, and proactive maintenance scheduling. Efficient inventory control ensures that the right parts are available when needed, reducing delays and enhancing productivity. Although incorporating technology and efficient inventory practices can be resource-intensive initially, the long-term benefits in terms of streamlined operations and cost savings make them a worthwhile investment in any maintenance management system.
Asset Tracking and Inventory Management
Utilizing Technology for Tracking
The utilization of technology for tracking assets plays a pivotal role in modern maintenance management systems, offering organizations a strategic advantage in optimizing operations. By employing RFID tags, barcode scanning, GPS tracking, or Io T sensors, businesses can accurately monitor asset location, condition, and performance in real-time. This data-driven approach enables proactive maintenance scheduling, timely repairs, and improved decision-making based on asset usage patterns. The unique feature of technology-driven asset tracking lies in its ability to provide detailed insights into asset lifecycle, maintenance history, and performance metrics. While technology advancements in tracking bring immense benefits in terms of operational visibility and efficiency, organizations must also consider the potential challenges such as data security risks, technology integration complexities, and staff training requirements.
Efficient Inventory Control
Efficient inventory control is indispensable for maintaining optimal stock levels, reducing wastage, and ensuring timely availability of spare parts and consumables. By implementing robust inventory management software, organizations can achieve inventory accuracy, minimize stockouts, and streamline procurement processes. The key characteristic of efficient inventory control lies in its ability to forecast demand, automate replenishment, and track consumption patterns for informed decision-making. This proactive approach to inventory management helps in avoiding costly breakdowns due to parts unavailability, optimizing inventory carrying costs, and improving overall operational efficiency. Despite its clear advantages, efficient inventory control requires continuous monitoring, regular audits, and effective supplier management to mitigate risks associated with overstocking, obsolescence, or supply chain disruptions.
Implementing Best Practices in Maintenance Management
Implementing best practices in maintenance management is a critical aspect of enhancing operational efficiency within organizations. By focusing on specific elements such as adopting a data-driven approach, integrating with Enterprise Resource Planning (ERP) systems, and investing in training and skill development for maintenance teams, businesses can streamline their maintenance processes to achieve optimal results. The significance of implementing best practices lies in the ability to improve maintenance operations, reduce downtime, and ultimately enhance overall productivity.
Adopting a Data-Driven Approach
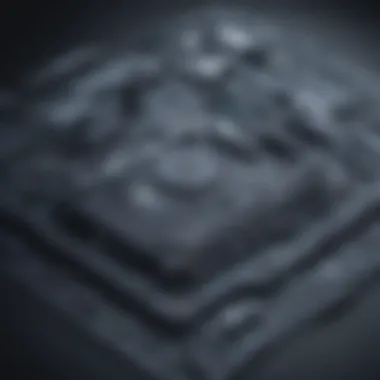

Utilizing Io
T Sensors for Monitoring
The utilization of Internet of Things (Io T) sensors for monitoring plays a pivotal role in modern maintenance management systems. These sensors enable real-time tracking of equipment performance, allowing maintenance teams to predict and prevent potential breakdowns effectively. One key characteristic of utilizing IoT sensors is their ability to collect vast amounts of data autonomously, providing valuable insights into equipment health and performance trends. This feature is highly beneficial for proactive maintenance strategies, as it enables organizations to address issues before they escalate, thereby reducing unexpected downtime and maintenance costs.
Analyzing Performance Data
Analyzing performance data is essential for organizations aiming to optimize their maintenance management systems. By examining key performance indicators (KPIs) and historical maintenance data, businesses can identify patterns, trends, and areas for improvement. One key characteristic of analyzing performance data is its ability to uncover inefficiencies in maintenance processes, guiding the implementation of targeted improvements. This proactive approach enhances decision-making processes, resulting in more informed and effective maintenance strategies within the organization.
Integration with Enterprise Resource Planning (ERP) Systems
Enhancing Collaboration Across Departments
The integration of maintenance management systems with Enterprise Resource Planning (ERP) systems facilitates seamless collaboration across different departments. This synchronization enables streamlined communication and data sharing, allowing for enhanced coordination in scheduling and executing maintenance activities. A key characteristic of enhancing collaboration across departments is the centralized access to maintenance-related information, which promotes cross-functional teamwork and efficiency. While the advantages of this integration include improved resource allocation and operational visibility, potential challenges may arise regarding data security and system compatibility.
Streamlining Data Sharing Processes
Streamlining data sharing processes is crucial for ensuring the smooth flow of information within an organization. By optimizing data sharing mechanisms within ERP systems, businesses can enhance the accuracy and accessibility of maintenance-related data. One key characteristic of this streamlining is the reduction of manual data entry and administrative errors, leading to more reliable maintenance records and streamlined workflows. While the benefits of efficient data sharing processes include improved decision-making and transparency, organizations must address data privacy and compliance considerations to mitigate potential risks.
Training and Skill Development for Maintenance Teams
Continuous Learning Programs
Implementing continuous learning programs is essential for maintaining the competency and expertise of maintenance teams. These programs enable employees to stay updated on the latest industry trends, technologies, and best practices. One key characteristic of continuous learning programs is their focus on ongoing skill development, ensuring that maintenance teams possess the knowledge and capabilities required to address evolving maintenance challenges effectively. With advantages such as increased employee engagement and retention, continuous learning programs contribute significantly to the organizational growth and adaptability.
Skill Enhancement Workshops
Conducting skill enhancement workshops is a proactive approach to upskilling maintenance teams and fostering a culture of continuous improvement. These workshops provide hands-on training opportunities, allowing employees to hone specific technical skills or competencies. One key characteristic of skill enhancement workshops is their interactive nature, which promotes knowledge sharing and collaborative problem-solving among team members. While the advantages of skill enhancement workshops include enhanced workforce competency and performance, organizations must ensure alignment with overall training objectives and strategic goals for maximum impact.
Measuring Performance and Efficiency
Key Performance Indicators (KPIs) in Maintenance Management
Mean Time Between Failure (MTBF)
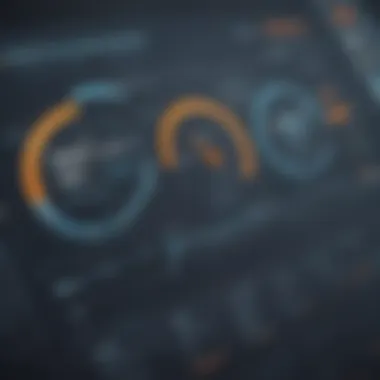
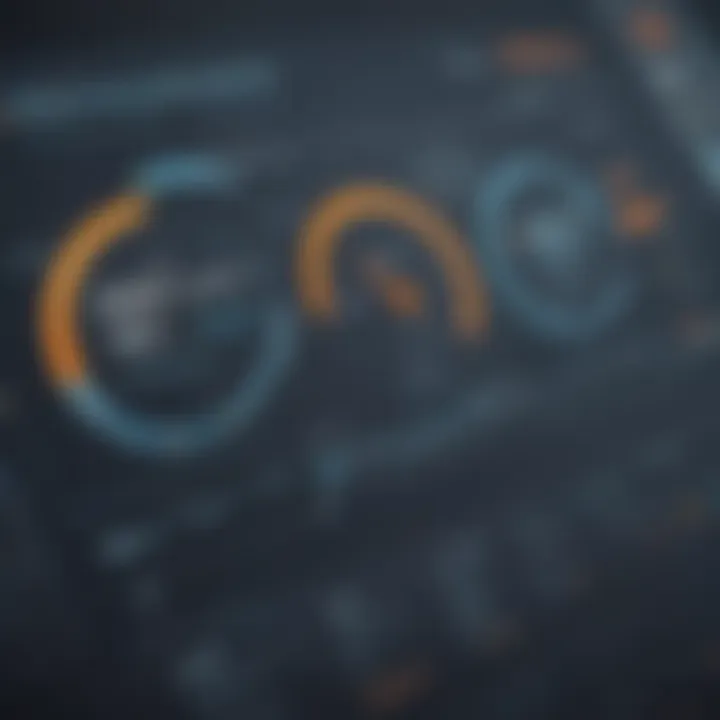
Mean Time Between Failure (MTBF) plays a pivotal role in maintenance management by providing a quantitative measure of asset reliability. It calculates the average time elapsed between failures, offering insights into the overall health of equipment and the frequency of breakdowns. The key characteristic of MTBF lies in its ability to predict potential failures, enabling proactive maintenance interventions to prevent unplanned downtime and mitigate operational disruptions. MTBF is a popular choice for this article due to its direct correlation with asset longevity and cost-efficiency. However, it's essential to note that while MTBF provides valuable insights into equipment reliability, it may not capture the full spectrum of failure patterns, leading to potential gaps in maintenance planning.
Overall Equipment Effectiveness (OEE)
On the other hand, Overall Equipment Effectiveness (OEE) serves as a holistic performance metric that evaluates the efficiency of equipment utilization in production settings. OEE considers factors such as equipment availability, performance rate, and quality output to provide a comprehensive view of operational efficiency. Its key characteristic lies in its ability to identify opportunities for process optimization and continuous improvement by pinpointing areas of inefficiency. OEE is a beneficial choice for this article as it aligns with the objective of enhancing operational efficiency through systematic performance evaluation. Despite its advantages in providing a comprehensive view of equipment effectiveness, OEE may overlook specific maintenance-related issues that could impact overall operational performance, emphasizing the need for a holistic approach to maintenance management.
Risk Management and Contingency Planning
In the pursuit of optimizing maintenance management systems, effective risk management and contingency planning play a pivotal role in mitigating potential disruptions and ensuring operational continuity. By proactively identifying potential risks associated with equipment failure or maintenance activities, organizations can preemptively implement strategies to minimize downtime and mitigate adverse effects on operational efficiency. The key characteristic of identifying potential risks lies in its ability to anticipate scenarios that could impact maintenance operations, enabling preemptive actions to mitigate risks. This proactive approach is a beneficial choice for this article as it aligns with the objective of enhancing operational resilience through strategic risk management. However, it's important to acknowledge that while proactive risk identification can help organizations prepare for potential challenges, it may also introduce complexities in decision-making processes, requiring a balanced approach to risk mitigation.
Developing Contingency Strategies
In tandem with identifying potential risks, developing effective contingency strategies is essential for organizations seeking to optimize maintenance management systems. Contingency strategies entail pre-planned responses to potential disruptions, ensuring swift recovery and minimal impact on operational efficiency in the face of unexpected events. The key characteristic of developing contingency strategies lies in its ability to provide a structured framework for responding to contingencies, fostering adaptability and resilience within maintenance operations. This strategic approach is a valuable choice for this article as it underscores the importance of proactive planning to mitigate risks and enhance operational continuity. It's vital to recognize that while contingency planning can minimize the impact of unforeseen events, overly complex strategies may hinder rapid response times, necessitating a balance between preparedness and agility.
Continuous Improvement Strategies
Moreover, continuous improvement strategies form the bedrock of sustainable maintenance management practices, facilitating iterative enhancements and process optimization. By incorporating feedback mechanisms for process enhancement, organizations can gather insights from stakeholders, refine maintenance procedures, and drive operational efficiency through continuous learning. The key characteristic of feedback mechanisms lies in their ability to capture diverse perspectives and leverage real-time data to inform improvements, fostering a culture of innovation and adaptability within maintenance teams. This systematic approach is a beneficial choice for this article as it advocates for a dynamic feedback loop to drive continuous improvement and operational excellence. However, it's essential to note that while feedback mechanisms enhance responsiveness to changing maintenance needs, an overreliance on feedback without strategic direction may lead to inefficiencies in process implementation, highlighting the importance of aligning feedback mechanisms with overarching maintenance goals.
Iterative Evaluation of Maintenance Procedures
Lastly, iterative evaluation of maintenance procedures underscores the importance of regularly assessing the effectiveness of maintenance strategies and refining processes to enhance efficiency. By incorporating structured evaluation processes, organizations can identify bottlenecks, optimize workflows, and preemptively address issues to maintain peak operational performance. The key characteristic of iterative evaluation lies in its iterative evaluation lies in its systematic approach to identifying areas for improvement and implementing targeted interventions to drive incremental enhancements. This methodical approach is a valuable choice for this article as it emphasizes the significance of continuous evaluation and adaptation in optimizing maintenance operations. Nevertheless, it's crucial to acknowledge that while iterative evaluation fosters a culture of continuous improvement, an excessive focus on evaluation without tangible action steps may result in analysis paralysis, necessitating a balanced approach that blends evaluation with swift, targeted interventions to drive sustainable operational efficiency.
Conclusion
Summary of Key Takeaways
Emphasizing the Importance of Maintenance Efficiency
Delving into the depths of maintenance efficiency unveils its pivotal role in ensuring sustained operational excellence. Focusing on the aspect of ensuring tasks are executed in a timely manner and with utmost precision, emphasizes the roots of maintenance efficiency. This spotlight on efficiency serves as a catalyst for enhancing overall operational effectiveness, thereby elevating the organizational performance trajectory. The unique characteristic of maintenance efficiency lies in its ability to act as a force multiplier, amplifying the impact of streamlined processes and proactive measures. While it presents a profusion of advantages such as cost savings, downtime reduction, and resource optimization, it also warrants careful calibration to align with the distinct operational demands of each organization.
Encouraging Continuous Improvement Efforts
Encouraging a culture of perpetual refinement in maintenance practices embodies a commitment to excellence and adaptability. Continuously seeking avenues for improvement within maintenance operations is akin to fostering a growth mindset within the organizational framework. The standout feature of such ongoing efforts is their intrinsic ability to instigate innovation and adapt to evolving industry landscapes. This concerted action not only spurs operational efficiency but also cultivates a culture of resilience in the face of dynamic challenges. While the benefits of continuous improvement efforts manifest in heightened responsiveness, enhanced agility, and optimized resource utilization, they also necessitate a balanced approach to avoid complacency and ensure sustainable progress.
Final Thoughts
Looking Towards Future Innovations in Maintenance Management
Pioneering into the realms of future innovations in maintenance management holds the promise of revolutionizing conventional practices and unlocking unparalleled efficiencies. Gazing ahead to emerging technological trends and methodologies is synonymous with staying ahead of the curve in a fast-paced industrial milieu. The standout characteristic of embracing future innovations is the adaptability it cultivates, enabling organizations to embrace change and capitalize on cutting-edge solutions. The unique feature of this forward-looking approach lies in its potential to future-proof maintenance operations, imbuing them with sustainability and relevance amidst technological disruptions. While its advantages encompass elevated competitiveness, enhanced operational capabilities, and enhanced customer satisfaction, it demands a keen eye for discerning value-driven innovation and prudent adoption strategies.
Promoting a Culture of Proactive Maintenance
Cultivating a proactive maintenance ethos signifies a paradigm shift towards pre-emptive measures and anticipatory actions within the maintenance landscape. The key characteristic of championing proactive maintenance is its proactive stance in averting potential issues and fortifying organizational assets against depreciation. This proactivity not only shields enterprises from unforeseen disruptions but also ushers in a proactive culture aimed at precluding downtimes and enhancing operational continuity. The unique feature of proactive maintenance lies in its capacity to instill a sense of preparedness and foresight, bolstering operational resilience and instilling a sense of control amid uncertainties. While its advantages encompass risk mitigation, improved asset lifecycle management, and operational stability, it requires a systematic approach and continuous vigilance to sustain its efficacy and impact.