Top ERP Solutions for Food Manufacturing Success
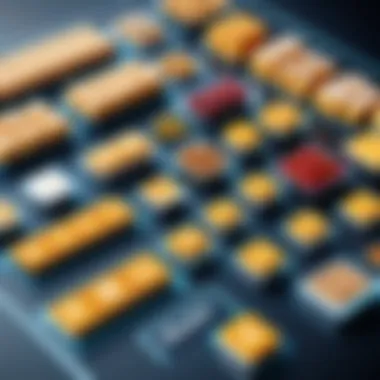
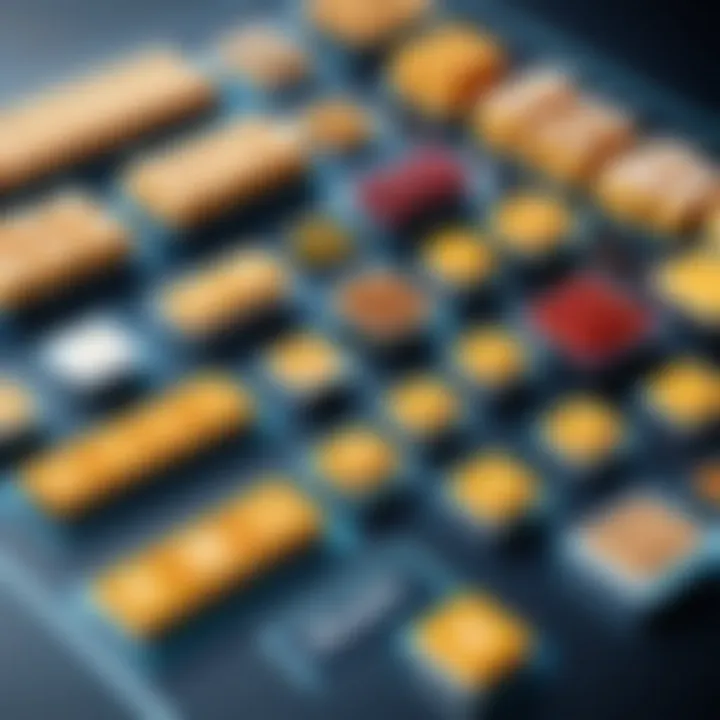
Intro
In the food manufacturing sector, the intricacies of production, quality control, supply chain management, and regulatory compliance present unique challenges. As the industry continues to evolve, the need for robust systems to streamline operations becomes increasingly essential. Enterprise Resource Planning (ERP) solutions offer the potential to address these challenges by centralizing data, improving operational efficiency, and enhancing decision-making capabilities.
This article delves into the best ERP solutions tailored to the food manufacturing industry. It outlines the current landscape, examines key features of leading systems, and highlights factors to consider when selecting the right software. Furthermore, it provides insights into implementation strategies and future trends, aiming to equip decision-makers, IT professionals, and entrepreneurs with the knowledge to make informed choices in a competitive environment.
Understanding ERP in Food Manufacturing
Enterprise Resource Planning (ERP) is a critical component for the food manufacturing industry. This sector faces unique challenges such as stringent regulations, supply chain disruptions, and the need for precise quality control. An effective ERP solution can centralize operations, streamline processes, and provide valuable insights that contribute to better decision-making and efficiency.
By adopting an ERP system, food manufacturers can enhance their capabilities in not only tracking raw materials but also in managing inventory levels in real-time. The efficiency gained through proper utilization of an ERP system ultimately translates to improved productivity and cost savings.
The importance of evaluating ERP solutions within food manufacturing cannot be overstated. Understanding the specific requirements of the sector, such as compliance with safety regulations and traceability needs, is vital when selecting the right ERP system. This article focuses on key aspects of ERP in food manufacturing, its roles, and how to navigate the selection process to choose the most suitable solution.
Definition and Scope of ERP
ERP stands for Enterprise Resource Planning. It is a type of software used by organizations to manage day-to-day activities such as accounting, procurement, project management, risk management, and supply chain operations. In the context of food manufacturing, the scope of ERP expands to include additional features that cater specifically to the industry's demands.
An ERP system for food manufacturing integrates various business processes into a unified system, enabling manufacturers to acquire a holistic view of their operations. This is essential for optimizing production flows, meeting regulatory requirements, and ensuring product quality. Moreover, ERP systems can offer functionalities for managing recipes, batch tracking, and ingredient sourcing, which are crucial for compliance and quality assurance in food production.
The Role of ERP in Food Manufacturing
The role of ERP systems in food manufacturing extends far beyond mere automation of processes. Effective ERP solutions facilitate better communication among departments, consolidate information, and enable real-time data access. This real-time access allows for prompt decision-making, which is essential in a fast-paced industry where consumer preferences and regulatory standards can change rapidly.
ERP systems can also improve planning and forecasting abilities, allowing manufacturers to respond adeptly to market demands. By leveraging data analytics and reporting functionalities, companies can gain insights into operational efficiency and identify areas for improvement.
Key functions an ERP system can offer include:
- Inventory management: Helps in tracking products and ingredients throughout the supply chain.
- Quality control: Ensures that products meet legal and safety standards.
- Regulatory compliance: Aids manufacturers in adhering to food safety regulations effectively.
In summary, ERP systems are pivotal in ensuring that food manufacturers operate efficiently, maintain quality standards, and satisfy regulatory requirements.
Challenges in Food Manufacturing
The food manufacturing industry is fraught with various challenges that can significantly impact the operational efficiency of businesses. Understanding these challenges is crucial for ERP system selection. Each element discussed below can affect not only daily operations but also long-term business viability. As food manufacturers navigate the complexities of their industry, addressing these challenges is paramount in ensuring compliance, consistency, and cost-effectiveness.
Regulatory Compliance
Regulatory compliance is a cornerstone of food manufacturing. Businesses must comply with strict guidelines set by organizations like the FDA or USDA. These regulations ensure that food products are safe for consumption. Non-compliance can lead to severe penalties, including fines and product recalls.
Having an ERP system that supports adherence to regulations is critical. A well-designed ERP enables manufacturers to track ingredient sources, production processes, and quality assurance steps. For instance, it can automatically generate compliance reports or alert management to potential violations. This can save time and resources, allowing firms to focus on producing quality products instead of worrying about legal issues. A robust system facilitates regular audits, ensuring manufacturers meet all necessary standards.
Supply Chain Complexity
Supply chain complexity is another major hurdle. Food manufacturers deal with numerous suppliers, each providing raw ingredients that must be coordinated to maintain inventory levels. Additionally, this supply chain is dynamic and prone to disruption due to various factors like weather, market fluctuations, and geopolitical events.
An effective ERP system simplifies this complexity. It provides a unified view of the entire supply chain, allowing for better decision-making. With real-time data, managers can respond quickly to disruptions, modifying orders or reallocating resources as needed. Moreover, ERP systems can enhance communication between suppliers and manufacturers, fostering stronger partnerships and reducing lead times.
Quality Control and Traceability
Quality control and traceability are significant components in the food manufacturing sector. Ensuring product quality is vital for maintaining customer trust. Traceability is equally important, as it allows manufacturers to track products back to their source in case of quality issues or recalls.
An ERP system equipped with strong quality control features can streamline inspection processes. It can automate quality checks at various production stages and maintain records of these checks. This ensures that quality is not only maintained but easily verifiable. Furthermore, if a product needs to be recalled, the ERP system can help trace the offending batch back through the supply chain rapidly. This capability minimizes risks and protects the brand's reputation, highlighting the critical role of ERP solutions in overcoming challenges in food manufacturing.
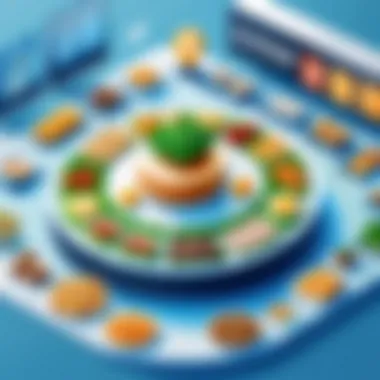
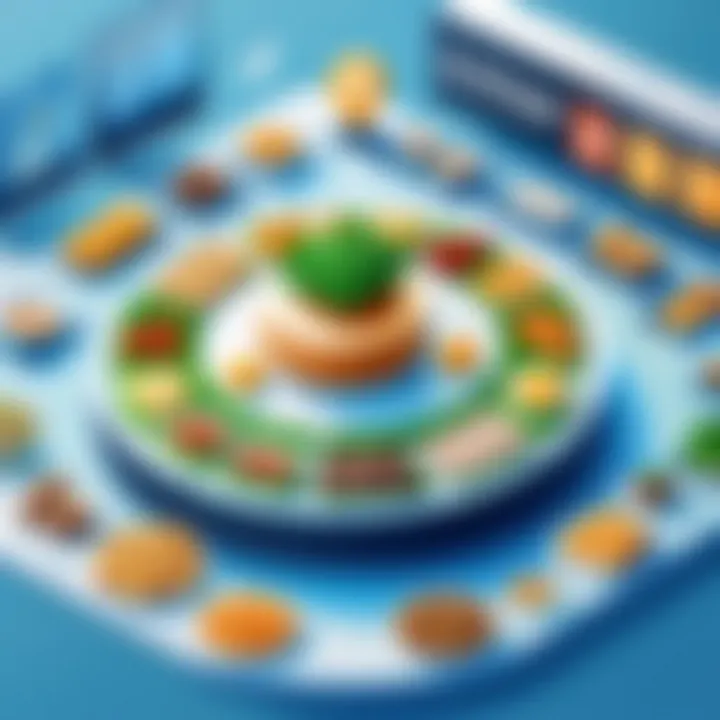
Key Features of ERP for Food Manufacturers
Evaluating ERP solutions for food manufacturers requires a keen understanding of essential features that can enhance operational efficiency and compliance. In the highly regulated food industry, companies must ensure that their ERP systems can address specific challenges while delivering value through streamlined processes. Each key feature plays a critical role in facilitating daily operations, enabling companies to improve productivity, maintain quality, and ultimately satisfy consumer demands.
Inventory Management
Effective inventory management is key for food manufacturers. This functionality allows businesses to keep track of raw materials, work-in-progress, and finished goods in real-time. With a robust ERP system, food manufacturers can avoid issues related to stock shortages or overstock situations. It minimizes waste by optimizing stock levels according to the fluctuating demand for perishable goods.
An efficient inventory management system can:
- Reduce food waste, thus lowering costs
- Provide visibility into stock levels, aiding in timely production decisions
- Enable better forecasting and demand planning
It is necessary for businesses to choose an ERP with advanced inventory features to sustain this critical aspect of their operations.
Batch Tracking
Batch tracking is indispensable in the food manufacturing sector. This feature ensures complete traceability of products from the raw ingredient stage to the finished product. In times of recall, having a comprehensive batch tracking system aids companies in identifying sources of contamination promptly. This capability protects brand reputation and ensures regulatory compliance.
Hereโs what batch tracking can help with:
- Regulatory Compliance: Adhering to stringent regulations requires businesses to know exactly where their products have come from and where they are going.
- Quality Assurance: Track each batchโs journey and quality control measures. Any problem in one batch can be isolated.
Companies should focus on ERP solutions that offer sophisticated batch tracking functionalities to enhance safety and accountability in their operations.
Production Planning and Scheduling
Production planning is a crucial component that empowers food manufacturers to maximize efficiencies. An ERP solution that integrates production scheduling can provide insight into machine availability, labor allocation, and overall workflow efficiency. This level of planning helps prevent bottlenecks and allows for heightened responsiveness to demand shifts.
Considerations for this feature include:
- Optimized Resource Use: Ensures equipment and manpower are effectively utilized.
- Flexible Scheduling: Adapts quickly to changes in order volume and ingredients availability.
In selecting an ERP, companies must prioritize those that offer comprehensive production planning features to sustain competitiveness.
Financial Management
Financial management capabilities within ERP systems help food manufacturers gain better control over their financial processes. This includes managing budgets, forecasting revenues, and maintaining compliance with accounting standards. When manufacturers can see their financial data in real-time, they can make informed decisions about investments and operational adjustments.
Key benefits of financial management features are:
- Cost Control: Monitor expenses and identify areas for cost savings.
- Reporting and Analysis: Generate reports for better visibility into financial performance.
Having robust financial management within an ERP is essential for food manufacturers to strive towards profitability while facing industry-specific challenges.
Evaluating ERP Solutions
Evaluating ERP solutions for food manufacturing is a critical step that determines the long-term success of any food production operation. This process involves a thorough analysis of various systems available in the market, ensuring that they align with the specific needs of the business. Understanding these solutions in detail can help decision-makers enhance productivity and maintain compliance with the regulations unique to the food industry.
The right ERP system not only streamlines operations but also provides the necessary data insights that contribute to informed decisions. Considering the rapid advancements in technology and changing market demands, this evaluation must consider both current functionalities and future-proofing capabilities.
Integration with existing systems is another key aspect during evaluation. A well-integrated ERP system can reduce redundancy, minimize manual errors, and maximize efficiency across departments. Furthermore, aligning the evaluation process with a clear understanding of business goals ensures that the selected ERP will facilitate growth and adapt to future challenges.
Criteria for Selection
When evaluating ERP solutions, specific selection criteria must be clearly defined. The criteria can vary based on organizational goals, but some fundamental aspects remain consistent:
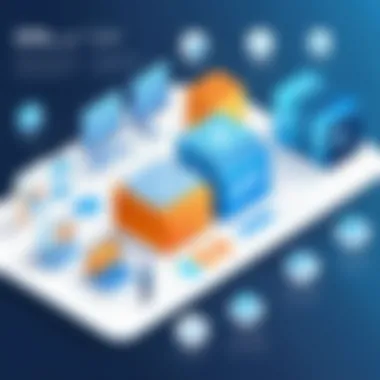

- Functionality: Ensure that the ERP offers essential features tailored for food manufacturing, such as batch tracking and compliance management.
- User Experience: The usability of the ERP interface is crucial. A user-friendly system can lead to quicker training times and higher efficiency among staff.
- Scalability: As the business grows, the ERP should be able to scale with it. Flexibility in user capacity and additional modules is essential.
- Vendor Support: Consider the type of support offered by the vendor. Reliable support can ease the implementation process and provide essential assistance post-deployment.
- Customization: Different food manufacturing operations may require varied processes. Customizable ERP solutions can cater to these specific needs.
Total Cost of Ownership
Understanding the total cost of ownership (TCO) is vital when evaluating ERP solutions. TCO encompasses not only the initial procurement cost but also ongoing expenses.
- Licensing Fees: Include costs associated with purchasing ERP licenses. Some licenses may be a one-time purchase, whereas others might require regular renewal.
- Implementation Costs: This can frequently exceed the purchase price. Implementation involves planning, configuring the software, and training users, which can be resource-intensive.
- Maintenance and Updates: Ongoing software maintenance fees must be assessed. Regular updates are necessary for compliance and security.
- Operational Costs: Consider the expenses connected to hardware, IT personnel, and other resources needed to operate the ERP efficiently.
When evaluating the total cost of ownership, potential hidden expenses must be taken into account. This attention to detail will provide clarity for budgeting and resource allocation, ensuring that the chosen ERP system can deliver quality value over its lifecycle.
"A well-planned ERP evaluation can minimize risks and maximize return on investment in food manufacturing."
By adhering to these criteria and considering the overall cost structure, organizations can make informed choices that best suit their operational needs.
Top ERP Solutions for Food Manufacturing
SAP S/4HANA
SAP S/4HANA is a comprehensive ERP solution that integrates various business functions into a single platform, tailored for food manufacturing processes. Its strength lies in real-time data processing, which allows manufacturers to respond swiftly to market changes. This system offers robust modules for financial management, production planning, and inventory control, making it ideal for companies that prioritize efficiency and compliance.
Additionally, SAP S/4HANA supports traceability, crucial for food safety regulations, enabling manufacturers to track ingredients throughout the supply chain. The centralization of data fosters collaboration among different departments, enhancing decision-making.
Microsoft Dynamics
Microsoft Dynamics 365 stands out due to its flexibility and user-friendly interface. It provides tools that assist in managing production, inventory, and quality control efficiently. The platform is adaptable, allowing customization based on specific needs of food manufacturers. This is particularly valuable in an industry where requirements may evolve frequently due to regulations.
Dynamics 365 also features AI capabilities, offering insights through predictive analytics. This can help in making informed decisions about production schedules, optimizing inventory levels, and enhancing customer service. Furthermore, its cloud deployment makes it accessible from anywhere, accommodating the increasingly remote working environments.
Oracle NetSuite
Oracle NetSuite serves as a cloud-based ERP platform designed for businesses of various sizes, including those in food manufacturing. One of its notable strengths is the integrated financial management system, which enables real-time visibility into financial performance. This is essential for food manufacturers who must monitor costs closely while adhering to budgetary constraints.
NetSuite's innovative supply chain management tools streamline processes from procurement to fulfillment. The system further allows for batch tracking, which is critical for managing food safety and quality assurance. Its comprehensive reporting features provide actionable insights, empowering manufacturers to respond effectively to market demands.
Infor CloudSuite Food & Beverage
Infor CloudSuite Food & Beverage is specifically built for the food industry, catering to the intricate needs of manufacturers within this sector. The solution emphasizes industry-specific functions, addressing areas like recipe and formula management, which are crucial for product consistency.
Furthermore, this ERP solution promotes collaboration among different departments, fostering a culture of transparency and shared objectives. The cloud-based nature of Infor's solution ensures scalability, allowing manufacturers to adapt easily as their operations grow. The built-in analytical tools can enhance decision-making by providing insights based on real-time data.
ProcessPro
ProcessPro offers a specialized ERP solution focusing exclusively on process manufacturing, especially in the food industry. It provides features such as batch control, inventory management, and regulatory compliance tracking. These functionalities are tailored to ensure that food manufacturers can optimize production while adhering to stringent industry standards.
The solution also supports traceability, crucial for recalling products efficiently and ensuring consumer safety. By integrating all relevant processes into one platform, ProcessPro enables manufacturers to streamline operations and reduce operational costs, ultimately enhancing profitability.
In summary, evaluating these top ERP solutions presents a roadmap for food manufacturers seeking to optimize their operations. Each of these systems offers distinct advantages tailored to meet the industry's complex demands, ensuring compliance while improving efficiency.
Implementation Considerations
Implementing an ERP solution in food manufacturing is not just about choosing the right software. Implementation considerations play a critical role in ensuring the system's success and achieving maximum value. Various factors must be evaluated to meet the unique demands of this sector. Understanding these considerations can help organizations navigate the complexities involved, leading to smoother transitions to new systems.
Change Management
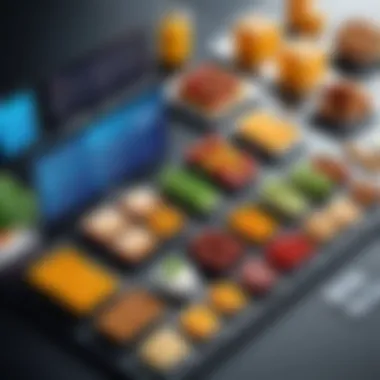
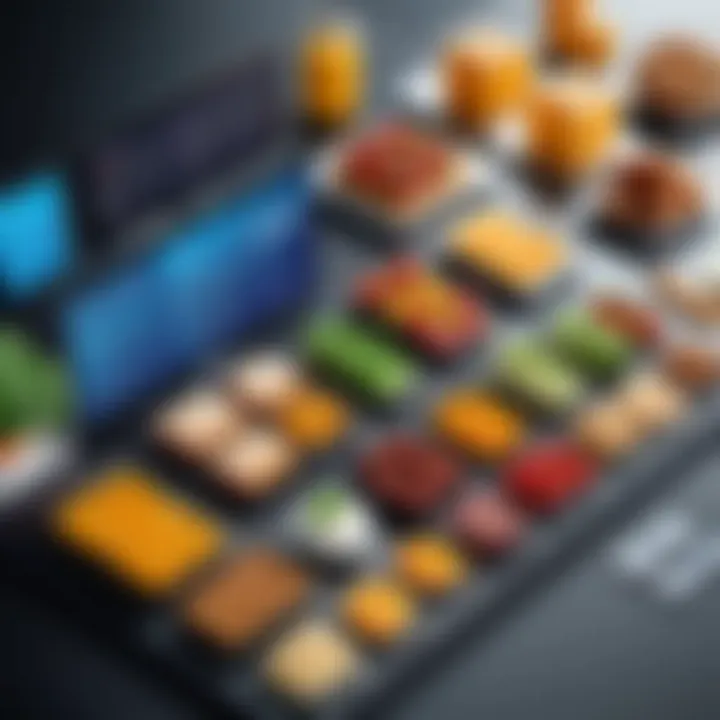
Change management is fundamentally about guiding people through the transition. When a food manufacturing facility decides to implement a new ERP system, employees will face shifts in practices and tools. A clear strategy to manage this change is essential. This not only involves training staff but also fostering a culture that embraces change.
- Communication is Key: Employees need to understand why the ERP is being implemented and how it benefits them. By addressing concerns and outlining the advantages, resistance can be minimized.
- Training Programs: Custom training sessions tailored to different user roles enhance user competence and confidence in utilizing the new system. Continuing education around system updates is also critical.
- Feedback Mechanisms: Establishing avenues for ongoing feedback allows employees to voice their concerns and suggestions. This can lead to faster adaptation within the workplace.
Strong change management practices can reduce anxiety among staff, ensuring a more seamless integration of the ERP system into daily operations.
Integration with Existing Systems
Integration with existing systems is another vital consideration. Many food manufacturing organizations rely on established software for various functions, such as accounting and inventory management. Ensuring that the new ERP solution integrates smoothly with these systems is crucial to maintaining operational continuity.
- Assessing Existing Infrastructure: Understanding the current system components helps identify potential challenges and areas for optimization.
- Data Migration Planning: Migrating data from legacy systems presents risks. Proper planning and execution ensure data integrity and reliability in the new ERP environment.
- APIs and Middleware: Utilization of APIs or middleware can facilitate communication between the new ERP and existing software, creating a cohesive ecosystem that supports business processes.
- Testing Before Go-Live: Conducting thorough testing can reveal issues before full-scale implementation. This can mitigate costly problems after the ERP goes live.
Integrating a new ERP system requires careful consideration of existing tools, ensuring that the new solution enhances rather than disrupts current operations.
Future Trends in ERP for Food Manufacturing
The landscape of food manufacturing is continuously evolving. ERP systems are crucial in helping companies to adapt to these changes. Recognizing future trends in ERP can greatly inform the decisions of decision-makers, IT professionals, and entrepreneurs within the industry.
A few key elements are shaping the future of ERP in food manufacturing. These include Artificial Intelligence, Machine Learning, and Cloud Computing. Understanding these trends is vital for those looking to enhance their operations and achieve better efficiencies.
One significant benefit of these trends is the ability to harness data more effectively. With advanced technologies, food manufacturers can make informed decisions based on real-time data and predictive analytics. Additionally, these trends can help improve regulatory compliance, enhance customer satisfaction, and drive cost reductions.
As companies evaluate their ERP solutions, they must consider the implications of these technologies on operations and strategy. To stay competitive, food manufacturers must not only adopt these advanced solutions but also understand how to leverage them for maximum benefit.
"The future of ERP in food manufacturing is not just about software; it's about transforming processes through innovation and intelligent technology."
Artificial Intelligence and Machine Learning
Artificial Intelligence (AI) and Machine Learning (ML) are transforming how food manufacturers operate. These technologies enable systems to learn from data, subsequently improving decision-making processes. This means that ERP systems can analyze historical data, predict future trends, and automate routine tasks. The result is a more agile and responsive operation.
The application of AI in ERP solutions can enhance:
- Demand forecasting: By analyzing trends, companies can predict what products will be in demand.
- Quality control: AI can monitor production lines for anomalies, ensuring every product meets safety standards.
- Supply chain optimization: Machine learning algorithms can identify inefficiencies in the supply chain, leading to better resource allocation.
With these developments, businesses can not only improve productivity but also achieve a higher level of compliance with industry regulations.
Cloud Computing
Cloud Computing is another trend reshaping ERP solutions for food manufacturing. Cloud-based ERP systems offer flexibility and scalability that on-premises solutions cannot match. Food manufacturers can access their ERP systems from anywhere, enabling collaboration across teams and departments. This is especially valuable for businesses with multiple locations or suppliers.
Key advantages of cloud computing in ERP include:
- Cost-effectiveness: Reduced need for physical infrastructure lowers costs for food manufacturers.
- Increased security: Cloud providers often have advanced security measures, protecting sensitive data effectively.
- Automatic updates: Cloud systems are regularly updated with the latest features and security enhancements, ensuring that businesses are always using the most current software.
Culmination
In the context of this article, the conclusion serves as a crucial component that encapsulates the entire discourse on the best ERP solutions for food manufacturing. It synthesizes the insights gathered from various sections and reflects on the significance of evaluating ERP systems tailored specifically for the unique demands of the food industry. Such evaluations lead to better operational efficiencies and improved compliance with industry regulations. Notably, the selection of the right ERP system is not a trivial task; it requires a multifaceted assessment that takes into account specific operational needs and strategic goals.
Summary of Findings
The exploration of ERP solutions reveals several key insights. First, food manufacturers face unique challenges such as stringent regulatory compliance, complex supply chains, and quality control measures. These challenges necessitate robust ERP systems that can integrate various functions such as inventory management, batch tracking, and financial oversight.
Additionally, the article identified critical features essential for food manufacturers when evaluating ERP solutions. Effective ERP systems facilitate traceability, enhance production planning, and support real-time data analysis, which are crucial for maintaining operational integrity in food production environments.
Moreover, leading solutions like SAP S/4HANA, Microsoft Dynamics 365, and Oracle NetSuite were examined, showcasing their individual strengths while highlighting the importance of aligning an ERP solution with specific business processes and objectives.
Recommendations for Food Manufacturers
Based on the findings detailed in this article, food manufacturers should consider the following recommendations:
- Clear Requirements Definition: Before selecting an ERP system, engage in a thorough needs assessment. Identify operational inefficiencies and articulate specific requirements.
- Comprehensive Evaluation: Use a systematic evaluation process. This includes assessing key features, total cost of ownership, and potential return on investment. Consider scalability and flexibility to adapt to future growth.
- Vendor Selection: Choose vendors with industry-specific experience. A provider familiar with the food sector will understand the intricate demands and provide better tailored solutions.
- Implement Change Management Strategies: Implementing a new ERP system can be disruptive. Establish change management practices to facilitate smooth transitions and training for staff.
- Focus on Technology Trends: Keep an eye on emerging technologies like artificial intelligence and cloud computing. These can enhance data management and improve decision-making processes.

