Manufacturing Learning: Concepts and Applications Unveiled
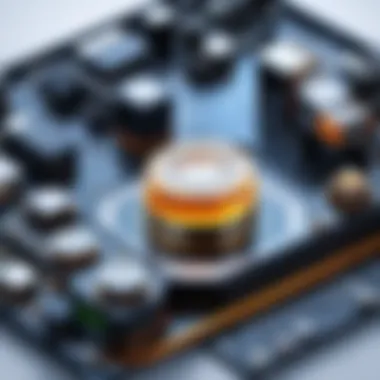
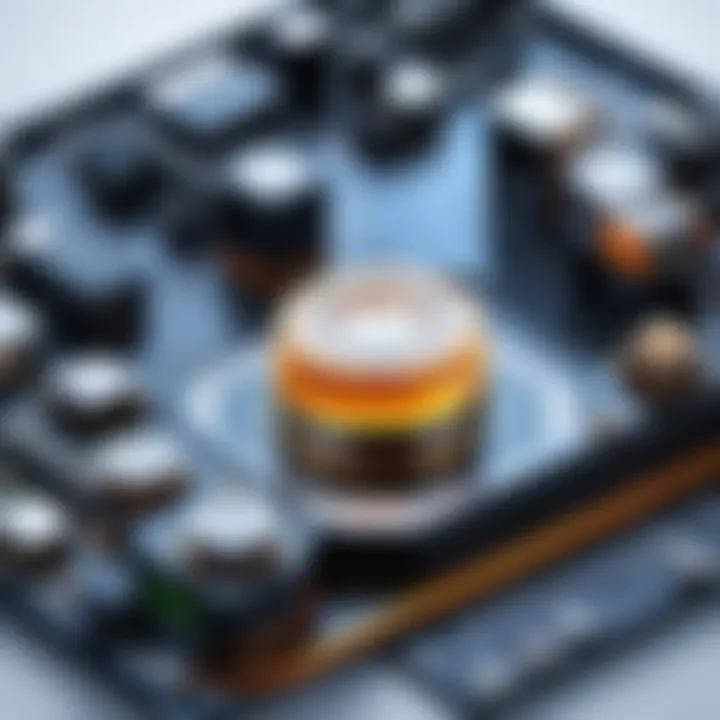
Intro
Manufacturing learning is becoming increasingly important for modern industries. In a landscape characterized by rapid technological advancements and continually changing market demands, organizations are compelled to adapt. This adaptability is largely informed by an effective understanding of manufacturing learning principles.
Understanding how to optimize processes and improve efficiency is vital. Continuous improvement allows businesses to enhance their performance while staying ahead of the competition. Nonetheless, the path to achieving real manufacturing learning is fraught with challenges. To help convey this complex subject, the following sections will delve into the industry's current state, top software solutions available in the market, and what decision-makers must consider when implementing learning initiatives.
Industry Overview
Current Trends in the Manufacturing Sector
The manufacturing industry is undergoing profound changes. New methodologies like lean manufacturing and agile processes gain popularity. These practices emphasize flexibility and efficiency, thus fostering a culture where continuous learning can thrive. Moreover, data-driven analysis enhances decision-making, empowering managers to adjust strategies based on real-time insights.
The rise of Industry 4.0 is greatly influencing this evolution. This revolution incorporates the Internet of Things (IoT), artificial intelligence (AI), and machine learning. These technologies help manufacturers optimize operations. Companies that embrace this digital transformation find it easier to implement effective learning systems.
Key Challenges Faced by Enterprises in Manufacturing Learning
Manufacturers do not face just technical hurdles. Organizational challenges also impede the success of learning initiatives. Factors such as resistance to change can create barriers. Engaging employees in the transformation is essential. Additionally, aligning learning objectives with overall business goals can be problematic. Misalignment often leads to poor outcomes.
Emerging Technologies Affecting Manufacturing Learning
Emerging technologies are reshaping manufacturing landscapes. AI is enabling unprecedented insights through data analytics. Meanwhile, Internet of Things (IoT) connectivity is allowing improved monitoring of operational processes. As these technologies evolve, integrating them effectively into manufacturing learning will pose both challenges and opportunities for organizations.
Top Software Options
Review of Leading Software Providers in Manufacturing Learning
Several platforms are making waves in this sector. Companies like Siemens and PTC provide systems that streamline not only operations but also the learning dimensions within firms. Their software often includes tools tailored to enhance collaboration, communication, and efficiency among teams. With proper utilization, these tools can significantly accelerate progress in manufacturing learning.
Feature Comparison of Various Software Solutions
The variety of options in manufacturing software means potential users must be attentive. Some of the most notable features to evaluate include:
- Customization options: Ensure the software can adapt to unique industry needs.
- User interface: A simple, intuitive design offers users a better experience.
- Data analytics: The ability to interpret data effectively is crucial.
Pricing Structures of Different Software Options
While pricing can be a barrier, itโs essential to acknowledge that higher costs do not always equate to greater value. Reviewing the financial requirements of various platforms allows for better allocation of budgets. It's prudent for organizations to evaluate return on investment rather than just upfront costs.
Selection Criteria
Important Factors When Choosing Software
Determining the right software for manufacturing learning requires careful consideration. Key factors are functionality, scalability, and integration capabilities. The platform should seamlessly integrate with existing workflows and technological infrastructures.
Common Mistakes to Avoid During the Selection Process
When selecting software, organizations often overlook critical assessments:
- Not involving end-users in the evaluation process.
- Underestimating the need for ongoing support and maintenance.
- Ignoring customization possibilities.
How to Determine the Right Fit for Your Business Needs
Targeted assessments and interactions with current users can illuminate this process. Conducting trials and soliciting feedback is invaluable. The selection must focus not only on features but also on how well the software can serve the companyโs capabilities in manufacturing learning.
Implementation Strategies
Best Practices for Smooth Implementation
Successful implementation of new software is not merely about technical setup. It requires well-planned project management methodology:
- Setting clear objectives from the onset.
- Ensuring effective communication between teams involved.
Integration with Existing Systems and Processes
Smooth integration is disruptively critical and should be prioritized. Organizations may find failure scenarios validated by looking at existing hardware. Compatibility among products directly impacts implementation success.
Training and Support Resources for Effective Deployment
When software is deployed, training cannot be neglected. A solid training program ensures people feel confident in using the new tools. Investing time into user education is essential for deriving anticipated benefits from the new software contribution.
Future Trends
Predictions for the Future of Manufacturing Learning
The manufacturing landscape will likely see increased reliance on AI-driven analytics. This will highlight ways to maximize efficiency and adaptability. Consequently, industries can expect that trends toward data utilization will continue. This will catalyze smarter decision-making frameworks in production lines.
Upcoming Technologies Shaping the Industry
As industries evolve, continuous digital transformations will influence educational methodologies. Ubiquitous connectivity through 5G mobile networks may enable undisrupted data access, further putting organizations at the forefront of learning initiatives.
Recommendations for Future-Proofing Your Technology Stack
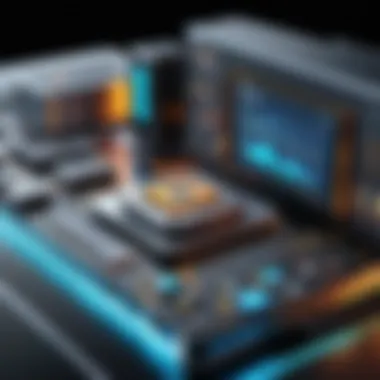
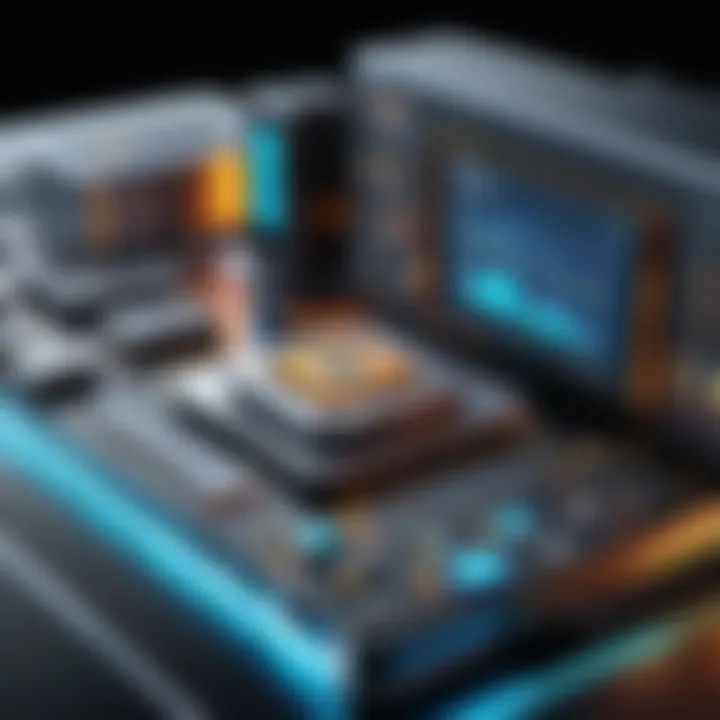
To safeguard technology investments, organizations could consider applying flexible methodologies in their choice of new solutions. Planning for scalability and prioritizing adaptable features will prove critical in sustaining competitiveness moving forward.
Overall, manufacturing is becoming an intricate blend of technology and human capital, and fostering an environment for effective learning is essential for success.
Prelims to Manufacturing Learning
Manufacturing learning has become a focal point of modern industrial practices. As companies adapt to changing market demands and technological advancements, understanding this topic is vital. The blend of skilled workers and advanced technology forms the backbone of this learning process. It enables organizations to refine their operations continuously.
In an environment where competition is fierce, the capacity to learn and adapt impacts productivity, quality, and innovation. A well-defined manufacturing learning framework encourages collaboration and progress across departments. This article addresses the critical elements that shape manufacturing learning, its implications, and how stakeholders can harness its potential for success.
Defining Manufacturing Learning
Manufacturing learning refers to the systematic approach to acquiring knowledge and skills related to manufacturing processes, equipment, and technologies. It encompasses various methods, tools, and practices that organizations employ to enhance their operations. This definition evolves with advancements in technology and shifts in workforce dynamics.
At its core, manufacturing learning promotes a culture of inquiry and exploration. Workers do not only follow standard operating procedures; instead, they learn from experiences and feedback. By implementing robust training methods and providing resources for ongoing education, manufacturers can achieve significant improvement.
Key Elements of Manufacturing Learning
- Continuous Education: Providing employees with the opportunity to upgrade their skills and knowledge.
- Feedback Mechanisms: Allowing for a regular assessment of performance, aiming at improvement.
- Technology Integration: Utilizing current technologies that facilitate learning and enhance production efficiency.
Historical Context
Understanding the historical context of manufacturing learning provides deeper insights into its evolution. The industrial revolution marked the beginning of a shift in learning approaches. Factories produced goods on a mass scale, resulting in a demand for skilled labor.
As industries progressed, the concept of workplace training emerged. Techniques such as apprenticeship began to take hold, offering a structured path for new workers to gain practical experience. Over the decades, as globalization set in, companies recognized the value of having well-trained employees who could adapt to different technologies and methodologies contexts.
In recent times, the attention has shifted towards creating learning organizations. Empowering employees to share knowledge and voice their insights helps cultivate a thriving learning culture. Those who understand these historical examples can better navigate workflows and initiatives that meld learning with efficient manufacturing practices.
The Importance of Learning in Manufacturing
In today's manufacturing landscape, embracing learning is no longer optional. It stands as a core element driving operational excellence and competitiveness. With rapid advancements in technologies, the need for continuous learning has manifested as a critical response to maintain relevance in the industry.
Learning leads directly to improvement in operational processes, efficiency, and product quality, making it indispensable.
Enhancing Productivity
Learning facilitates the ongoing refinement of processes every stage of production. When workers and management engage in training and development, productivity enhances substantially. First, training enables employees to utilize machinery and tools more efficiently. This minimizes downtime and reduces waste. Furthermore, knowledge about best practices can help streamline workflows, thus enabling quicker outputs against time constraints. Each improvement stacks cumulatively, showcasing significant productivity enhancements that resonate throughout the organization.
There are various proactive measures organizations can adopt:
- Training on newer technologies. Workers must become acquainted with the latest tools for optimal integration.
- Skill assessments. Identifying specific training needs leads to targeted workshops.
- Feedback channels. Establishing a continuous flow of information helps enhance process dynamics continually.
Adopting such methods not only affects individual performance but also creates an overall efficiency boost within manufacturing units.
Driving Innovation
Innovation often hinges on a culture of learning. Manufacturing is rife with challenges โ minimizing costs, enhancing products, and responding to market fluctuations. In this context, encouraging learning leads to problem identification and solution development. Employees trained to think creatively can suggest innovative processes or technologies that facilitate broader goals.
For companies, a firm grasp of learning can result in better adaptation of innovative practices such as:
- Lean manufacturing principles. When adopted, these significantly reduce waste while boosting productivity, paving the way for novel solutions.
- Collaborative teamwork. Empowering employees to contribute through education increases their engagement.
- Cross-disciplinary training. Encourages fresh perspectives across different roles leading to interconnected innovation.
This innovation is not merely theoretical. By fostering a team actively pursues improvements, manufacturing firms set themselves on a path to discovery, keeping them ahead in trends and customer expectations.
Improving Quality Control
Quality control acts as a linchpin within manufacturing. Continuous learning substantially influences how organizations approach quality management. It equips employees with the necessary tools to identify issues before they escalate.
Incorporating methodological training and learning on quality standards leads to clearer insights into which processes may falter. This enhanced knowledge base supports workers in ensuring rigorous quality assurance across products.
Effective learning strategies include:
- Regular onboarding sessions. Provide refreshers on quality protocols to maintain high standards.
- Utilization of data analysis. Assess feedback from previous manufacturing runs to inform and educate staff.
- Focus groups. Engage various teams in regular discussions on quality improvements, encouraging accountability.
As the workforce stays well-informed, the potential for errors reduces while quality climbs, thus establishing a stronger reputation and product reliability.
Learning in manufacturing doesn't exist harmoniously; it interfaces with efficiency, innovation, and quality โ the trifecta that sets successful entities apart.
Core Principles of Manufacturing Learning
Manufacturing learning is a strategic component of modern industry, essential for fostering enhanced operational efficiency. This section outlines pivotal core principles of manufacturing learning, emphasizing their significance, advantages, and considerations. It provides a foundation on which firms can build robust learning systems specifically within manufacturing environments.
Feedback Loops
Feedback loops are critical mechanisms within the fabric of manufacturing learning. They serve as continual communication pathways between production processes and the insights gained from those activities. Through effective feedback loops, operators can gather valuable data regarding equipment performance, process efficiency, and potential bottlenecks. This information promotes swift adjustments based on real-time input and outcomes.
Feedback loops contribute to agile methodologies. They ensure that refinements are constantly made based on an organization's performance measurement.
When designers and operators share information, advantageous shifts can occur. For example, if a particular equipment often requires maintenance, this data informs decisions on upgrades or redesign, fostering systemic enhancement. Importantly, feedback loops do not just improve current operations; they also shape future strategies by creating resilient and responsive manufacturing processes.
Continuous Improvement
Continuous improvement embodies the pursuit of enhancement over time. This principle, known as Kaizen, involves small, incremental changes that accumulate into substantial advancements. In manufacturing, fostering a culture that embraces continuous improvement is crucial. It alleviates the tendency to settle into complacency.
Implementing systems that emphasize ongoing evaluation fosters innovation. Establishing regular assessments within operations allows organizations to identify areas requiring adjustment efficiently. These small changes increase productivity and reduce waste. Furthermore, continuous improvement facilitates motivation and engagement among employees. When individuals witness the tangible effects of their contributions, a heightened sense of purpose and teamwork arises.
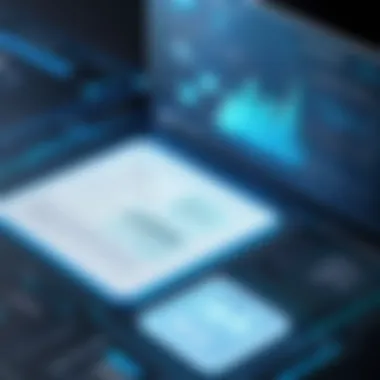
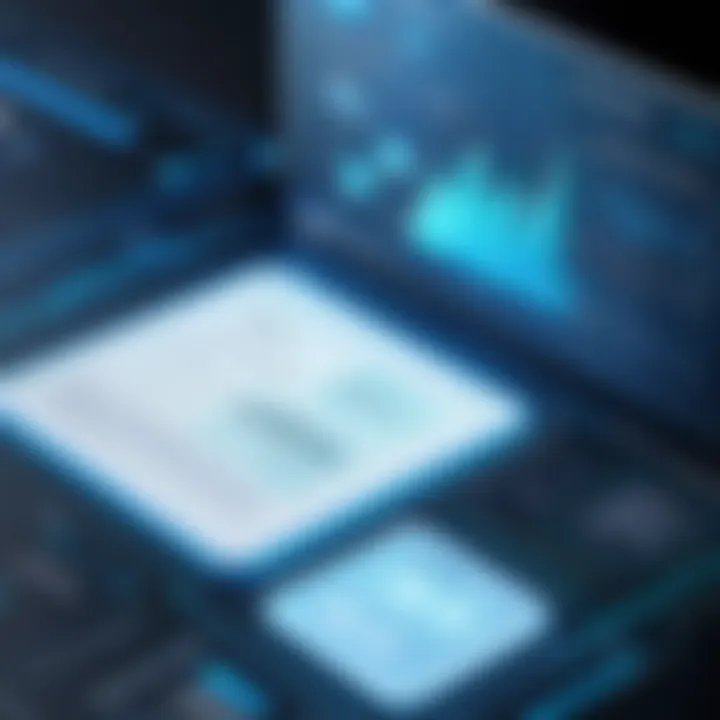
- Enhance workflow efficiency
- Minimize operational costs
- Strengthened employee morale
- Accelerated product development cycles
In summary, the return on investment for businesses adopting continuous improvement as a core principle is substantial.
Knowledge Sharing
Knowledge sharing stands as a vital principle within the realm of manufacturing learning. In highly complex environments, effective dissemination of skills and information among employees drives performance enhancement. This principle promotes an open culture where insights are shared across various levels within the workforce, fostering a collaborative atmosphere.
Organizations must concentrate on creating platforms for knowledge exchange. From face-to-face interactions to digital tools, resources must be made accessible to facilitate learning. Implementing systems such as mentorship or cross-training programs ensures that employees are better equipped to approach challenges. When knowledge is distributed adequately, skill sets broaden and innovation flourishes.
- Utilize collaborative platforms
- Encourage cross-department workshops
- Foster informal lunch-and-learn sessions
The accumulation of shared expertise undoubtedly leads to more capable teams and informed decision-making processes within manufacturing operations. By embracing these core principles of manufacturing learning, organizations position themselves for considerable growth and resilience in an ever-evolving industrial landscape.
Technological Innovations and Their Role
Technological innovations serve as a cornerstone in the evolution of manufacturing learning. These advances create pathways through which companies can amplify their operational efficiencies, adaptability, and ultimately their competitiveness. As manufacturing environments become more complex and competitive, the relationship between technology and learning becomes increasingly crucial. Innovations define how organizations respond to change and ensure they satisfy evolving market needs.
Automation and Learning Systems
The integration of automation into manufacturing processes can significantly enhance learning systems. Automated machines include a range of robotic processes that increase efficiency and precision in production. When these machines collect data, they contribute to improved learning by identifying successful processes and areas for optimization.
Studies show that companies employing automation report higher productivity and decreased error rates.
Incorporating automation into learning frameworks allows workers to focus on more complex tasks. As labor-intensive work diminishes, it becomes vital to direct workersโ energy toward decision-making and innovations. Automation supports the establishment of feedback loops which feed directly into continuous learning processes. To sum up, automation transforms traditional training environments into data-rich learning systems vital for growth.
Data Analytics in Manufacturing Learning
Data analytics represents another crucial technological innovation altering the manufacturing landscape. Companies can mine vast volumes of data collected from various processes. This data helps to identify inefficiencies and predict future trends. The ability to analyze statistics leads to smarter decision-making, backed by evidence rather than intuition.
- Companies utilizing data analytics can:
- Enhance operational efficiencies
- Develop predictive maintenance schedules
- Allocate resources more effectively
Each data-driven decision contributes back into the company's learning ecosystem. Gathering insights not only supports improved outcomes, but also sets the stage for a culture of institutional knowledge sharing wherein employees learn from analytics outcomes to apply best practices.
Artificial Intelligence Applications
The application of artificial intelligence (AI) in manufacturing learning provides an advanced layer of data processing and decision-making. With machine learning capabilities, AI systems can adapt over time based on new inputs. They not only accelerate data interpretation but also automate routine decision-making processes.
Utilizing AI leads to several benefits:
- Increased accuracy in learning outcomes.
- Enhancement of training programs tailored by AI constant assessments.
- Creation of real-time insights that empower leaders and managers to take informed decisions on-the-fly.
In summary, the evolving landscape of technological innovations provides a robust infrastructure for manufacturing learning. This shift towards integrating automation, advanced data analytics, and artificial intelligence symbiotically enhances productivity, fosters innovation and creates a learning framework wherein businesses can thrive.
Best Practices for Implementing Manufacturing Learning
To fully realize the potential of manufacturing learning, organizations must adopt best practices for implementation. These practices not only enhance the learning processes within companies but also encourage sustainable improvement. Effective implementation of manufacturing learning contributes substantially to overall productivity, innovation, and quality. These crucial best practices establish a smooth flow in operations and can address the complexity of integrating new learning strategies in manufacturing settings.
Creating a Learning Culture
A strong learning culture is fundamental for the success of any education initiative in manufacturing. It requires commitment at all levels, from top management down to the shop floor. Fostering this climate demands open communication, encouraging exploration and inquiry. This culture permits employees to voice questions, share experiences, and suggest improvements without fear of ridicule. The benefits are twofold:
- Employee Engagement: When employees feel valued and heard, they are more inclined to participate actively in learning programs.
- Knowledge Retention: A culture of learning enhances retention of vital operational knowledge, serving as a repository for best practices.
A learning culture yields higher effectiveness in training and nurtures individual growth, aligning with company objectives.
Training Programs and Workshops
Structured training programs are essential for formal knowledge transfer in manufacturing settings. They lay the foundation for employee skill development tailored to meet evolving job requirements. Organizing workshops regularly builds employee competencies while fostering teamwork. These sessions should be guided by current industry standards and include:
- Hands-on Learning: Practical application enables employees to see the transition from theory to real-world scenarios, which boosts confidence.
- Job Rotation: This exposes employees to diverse functions within the facility, enriching knowledge and experience across the board.
These initiatives ensure that skills are up to date and that each employee is equipped to contribute to their fullest potential.
Mentorship and Peer Learning
Mentorship plays a vital role in cultivating knowledge sharing and skills development. By pairing seasoned professionals with less experienced colleagues, firms encourage beneficial relationships that enhance personal and collective growth. Peer learning, meanwhile, promotes collaboration among team members. Organizations can enhance mentorship through the following:
- Regular Check-ins: Facilitating structured update sessions ensures guidance is on track and beneficial to both parties.
- Formal Mentorship Programs: Establish clear goals and expected outcomes, aiding both mentors and mentees in realigning objectives as necessary.
This type of structured learning network rewards informal learning while also contextualizing and formalizing experiences, allowing for steady advancement in employee capabilities.
Challenges in Manufacturing Learning
In the ever-evolving landscape of manufacturing, the importance of identifying and addressing challenges in learning cannot be overstated. Faced with rapid technological advancements and shifting market demands, companies must cultivate an adaptable workforce. However, several challenges obstruct effective manufacturing learning. These include resistance to change, resource constraints, and skill gaps.
Resistance to Change
One of the most significant hurdles is the resistance to change within an organization. Implementing new learning systems can be threatening. Employees may worry about job security or fear being replaced by technology. This leads to a chilling effect where individuals might avoid adapting to new processes or learning.
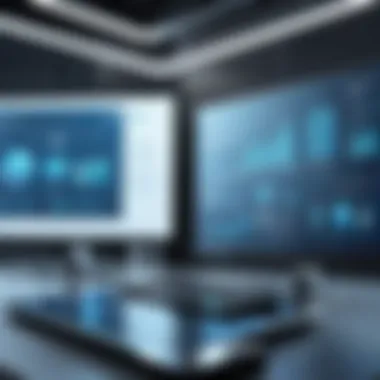
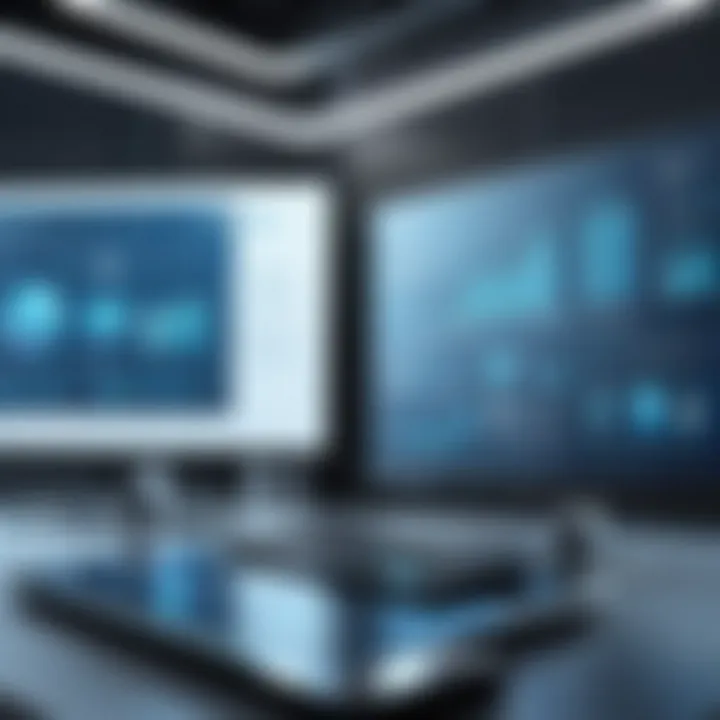
To overcome this challenge, companies must engage in thoughtful communication. Developing a clear vision and conveying the benefits of manufacturing learning is crucial. When employees understand how these practices improve safety, efficiency, and job fulfillment, they are more likely to buy-in. Leadership must lead by example, participating in training initiatives directly.
Resource Constraints
Resource limitations impact all sectors, and manufacturing is no exception. Organizations often face resource constraints related to time, personnel, and capital. With tight budgets and operations focused on production, allocating resources for training and development can seem impossible. The immediate need to meet production demands typically overshadows long-term investments in employee learning.
To address resource constraints, companies can opt for innovative solutions. Outsourcing training or leveraging online learning systems can reduce burdens on internal resources. Being selective with training programs offers maximum benefit with minimum cost. Careful planning can achieve significant impacts.
Skill Gaps in the Workforce
Lastly, skill gaps in the workforce present a considerable challenge. Manufacturing often necessitates specialized knowledge, and the evolving nature of this field requires continuous learning. Emerging technologies require a workforce that can adapt. Yet many workers do not possess the latest skills necessary. These skill discrepancies can lead to a decline in production quality and output. It becomes essential to assess current skill levels against market demands actively.
To bridge these gaps, robust training and development plans are required. Traditional methods may not suffice, hence reskilling and upskilling become vital. Creating flexible training options allows workers to learn while on the job. Additionally, partnerships with educational institutions can provide resources for targeted training programs.
"Addressing challenges in learning is not an option; it is a necessity for future readiness in manufacturing and better adaptability."
Recognizing these challenges is paramount. By acknowledging the resistance to change, assessing resource constraints, and addressing skill gaps, companies can develop concrete strategies. Implementing systemic changes empowers a manufacturing learning environment equipped for challenges ahead.
Case Studies of Successful Manufacturing Learning
The examination of case studies in manufacturing learning plays a crucial role in understanding the implementation and impact of learning initiatives within the industry. It illustrates real-world applications and validates processes that enhance operational efficiency and adaptability in dynamic market environments.
Leading Automotive Manufacturers
Automotive manufacturers have long been at the forefront of embracing innovative practices in manufacturing learning. A prime example is Toyota, which has effectively applied the principles of the Toyota Production System (TPS). This approach focuses on eliminating waste and continuously improving productivity. With an emphasis on feedback loops and employee involvement, Toyota's success highlights the value of incorporating learning as an integrated process rather than a separate task.
Furthermore, General Motors adapted its training programs to incorporate virtual reality simulations. This implementation ensures that employees can hone their skills in a safe environment, greatly reducing physical risks associated with on-the-floor training. The insights gained by these efficiency measures not only result in increased production outputs but also elevate the overall workforce skills. This approach provides a clear case as to how established automotive companies can harness technology for learning, setting a transformative precedent in their operations.
High-Tech Electronics Industry
In the high-tech electronics sector, Samsung stands out as an exemplar of effective manufacturing learning. The company's commitment to research and development is reflected in its ongoing training initiatives. By leveraging data analytics, Samsung identifies skill deficiencies and addresses them through tailored training modules. This strategic approach showcases the direct correlation between employee competency and innovation.
Moreover, companies like Intel invest heavily in knowledge sharing practices. They foster a culture where cross-departmental teams collaborate and share insights. This cooperative learning environment is vital for driving progress in complex manufacturing processes. By regularly conducting workshops and hackathons, these companies create collaborative forums that enhance learning outcomes across various dimensions.
The integration of real-time feedback and adaptive learning technologies are essential trends found in modern manufacturing case studies, ultimately driving efficiency and productivity.
Future Trends in Manufacturing Learning
As manufacturing evolves, the transformation of learning processes is essential to adapt to new challenges. This section intentionally explores future trends in manufacturing learning, evaluating their significance in modern operations. The adaptation to these trends is vital for staying competitive in an increasingly complex market landscape, enabling companies to optimize their workforce and innovations effectively.
The Rise of Adaptive Learning Systems
Adaptive learning systems are becoming more mainstream in manufacturing learning. These systems adjust the training approach based on individual employee performance and needs. In this way, it allows tailored learning experiences, making them more relevant and effective for employees.
- Benefits of Adaptive Learning Systems:
- It enhances engagement by aligning with each learner's capability.
- Workers receive real-time feedback, which accelerates their skill acquisition.
- Such platforms can integrate data analytics to keep materials updated, aligning with current technologies and practices.
Considering adaptive systems not only increases efficiency but also reduces the time to proficiency. Workers are empowered to learn at their pace while employers observe improved performance metrics, fostering a collaborative learning environment. Adoption of these systems poses some challenges, including required investments and sophisticated management of the technology, but the positives often outweigh the negatives.
"Adaptive learning can redefine skills training by personalizing the experience and promoting quicker adaptation among the workforce."
Integration of Augmented Reality
Augmented reality (AR) is making significant advancements in manufacturing learning. AR can be used to enhance practical skills through immersive experiences. With AR technology, employees can train with virtual equipment controlled by mobile devices or smart glasses. This method delivers a massive range of possibilities for skill development without the risks linked to real-world training.
The benefits of AR in manufacturing learning include:
- Immersive Simulations: Employees can practice complex tasks in a virtual environment.
- Safety Improvements: Risks during hands-on training are reduced, protecting both learners and equipment.
- Step-by-Step Guidance: AR systems can display guides directly onto equipment, simplifying operations regardless of experience levels.
As AR continues to mature, its potential will only broaden. Companies looking to incorporate AR should balance investments with the necessity of gradual implementation. Workforce adjustment to this technology will require ongoing support and fine-tuning of strategies for effective integration.
Ultimately, adaptive learning systems and AR reflect a pivotal shift in how manufacturing learning will evolve. These trends signal an approach emphasizing competency and personalized training, crucial elements for building a resilient manufacturing landscape as the industry progresses.
Epilogue
In the realm of manufacturing, learning stands out as not only advantageous but essential for sustained growth and innovation. This article has addressed various facets of manufacturing learning, emphasizing its importance in modern industrial contexts.
Summarizing Key Points
Manufacturing learning encompasses a broad range of strategies and practices that enhance knowledge acquisition, application, and overall industry advancement. Key points addressed include:
- The critical role of continuous improvement and feedback loops.
- The significant impact of technology, focusing on data analytics and automation.
- Case studies that provide realistic insights into successful applications in the industry.
- Strategies for overcoming obstacles like resource availability and skill gaps.
The interplay between human insights and technological support forms the bedrock of a resilient manufacturing ecosystem. Both components are necessary for companies wishing to navigate an increasingly complex market landscape.
Call to Action for Industry Stakeholders
It is imperative for decision-makers and industry stakeholders to invest in the principles of manufacturing learning. By fostering an environment of continuous education and adaptability, the benefits can be substantial.
Individuals and organizations should consider:
- Creating regular training programs addressing current and future needs.
- Promoting knowledge sharing and collaboration among teams.
- Incorporating modern technologies for enhanced learning experiences.
Proactive engagement with these methods ensures manufacturing firms not only keep pace with competition but potentially lead the market through innovative practices.
Establishing a culture where learning is prioritized will pave the way for significant improvements in productivity and quality control.