Unlocking Efficiency with Yardi Inventory Control
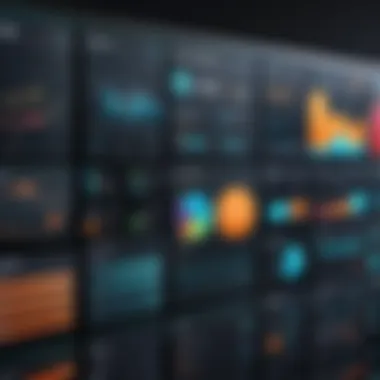
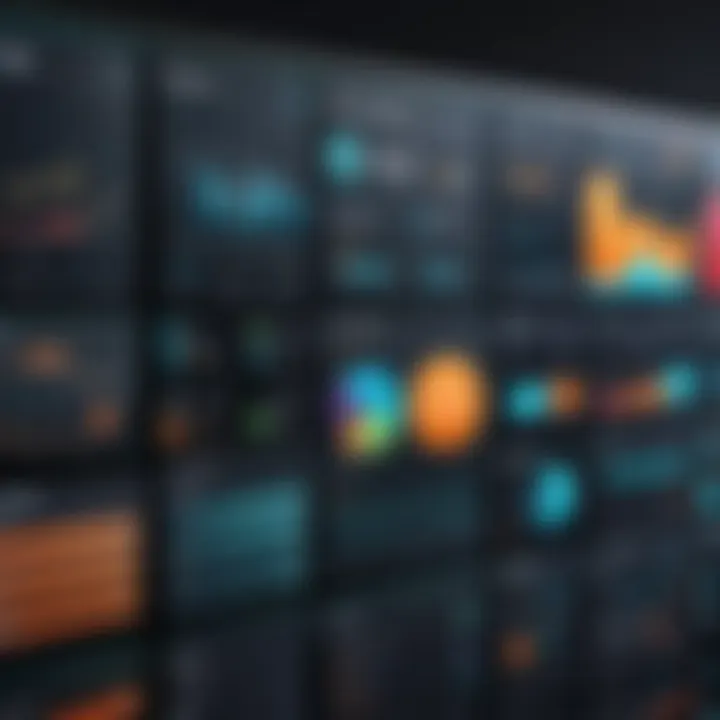
Intro
In today's fast-paced business landscape, managing inventory effectively can be the difference between success and failure. Yardi Inventory Control stands as a robust solution in inventory management, but what makes it particularly relevant for decision-makers? This guide will delve into its features and functionalities, exploring how businesses can leverage technology for better inventory tracking and management. The following sections will shed light on industry trends, challenges, key selection criteria, practical implementation strategies, and possible future advancements.
Industry Overview
Current Trends in the Industry-specific Software Market
As the business environment evolves, so does the demand for comprehensive inventory control solutions. Industry-specific software like Yardi has gained significant traction. Today’s organizations favor software that offers real-time tracking, analytics, and integration capabilities. Companies must adopt systems that enhance decision-making and improve overall efficiency.
Many are shifting to cloud-based services, enabling remote access and updating capabilities essential for modern businesses. The shift is largely fueled by increasing customer expectations for quick service and accurate inventory management.
Key Challenges Faced by Buyers in the Industry
While the growth of inventory management solutions is promising, buyers often face several challenges. One pervasive issue is data accuracy. Inconsistent or incorrect data can lead to poor decision-making, affecting profitability. Security concerns also prevail, as sensitive inventory data becomes a target for cyber threats. Continuous training for staff regarding software usage emerges as another critical challenge, which many companies overlook. Keeping employees up-to-date with tech changes can severely impact efficiency.
Emerging Technologies Impacting the Industry
Technologies such as artificial intelligence and machine learning are currently transforming inventory management paradigms. Predictive analytics now allow organizations to forecast demand more accurately, minimizing stockouts and excess inventory. Automation plays a crucial role as it reduces human error, accelerates operations, and ultimately saves costs. Companies integrating these technologies into inventory control systems stand better positioned to achieve competitive advantages.
Top Software Options
Review of Leading Software Providers in the Industry
The industry boasts several dominant players alongside Yardi, providing a wide range of functionalities and pricing structures. Notable names include Oracle NetSuite, SAP Business One, and Fishbowl Inventory. Each offers distinctive features that cater to different business needs; however, Yardi remains at the forefront due to its comprehensive Realty management capabilities.
Feature Comparison of Top Software Solutions
When evaluating software, features should drive selection.
- Yardi: Real-time tracking, analytics, customizable dashboards, and integration with other Yardi solutions.
- Oracle NetSuite: Multi-location management and complete financial visibility for larger enterprises.
- SAP Business One: Ideal for startups requiring broad financial oversight and easy customization.
- Fishbowl Inventory: Simple yet effective choices, particularly for manufacturing and warehousing.
Understanding these nuances can help organizations select the most appropriate software.
Pricing Structures of Different Software Options
Pricing for these tools varies greatly depending on the features provided and the scale of implementation. Yardi typically follows a subscription-based model with diverse packages tailored for different business sizes. On the other hand, Oracle and SAP might demand significant up-front investment accompanied by recurring costs as per user licenses. Therefore, careful budgeting becomes essential during the procurement of inventory software.
Selection Criteria
Important Factors to Consider When Choosing Software
Adopting new inventory management software isn't trivial. Organizations must assess various factors, such as:
- Scalability: Ensure that software can grow with the demands of the business.
- Usability: A user-friendly interface can mitigate training time and improve team adoption.
- Customer Support: Availability of assistance and training resources are critical during and post-implementation.
Common Mistakes to Avoid During the Selection Process
Many decision-makers trip in the selection process, often a result of:
- Underestimating Integration Needs: Every buyer must analyze how well new solutions fit with existing systems.
- Ignoring Long-Term Viability: Long-term support and updates from software vendors become equally crucial to avoid future complications.
- Lack of Stakeholder Involvement: Not involving staff early in the process may lead to future resistance to change.
How to Determine the Right Fit for Your Business Needs
To identify the perfect software fit, organizations should conduct:
- Requirement Analysis: Clearly define what you need.
- Market Research: Investigate different options available.
- Trial Programs: Engage trial offerings if possible before full commitment.
This structured approach helps in making informed decisions.
Implementation Strategies
Best Practices for Smooth Implementation of Software Solutions
Once a choice is made, proactive implementation becomes essential. Successful software rollouts can result from planning ahead through key practices like:
- Comprehensive Testing: Before full deployment, test in controlled environments to identify potential issues.
- Involvement of end-users: Include staff in piloting functions they will need to manage.
Integration with Existing Systems and Processes
Ensuring software works coherently with what’s already in place is necessary. APIs and other integration strategies should align seamlessly to prevent data silos and inefficiencies.
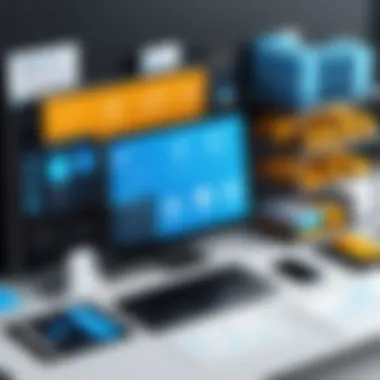
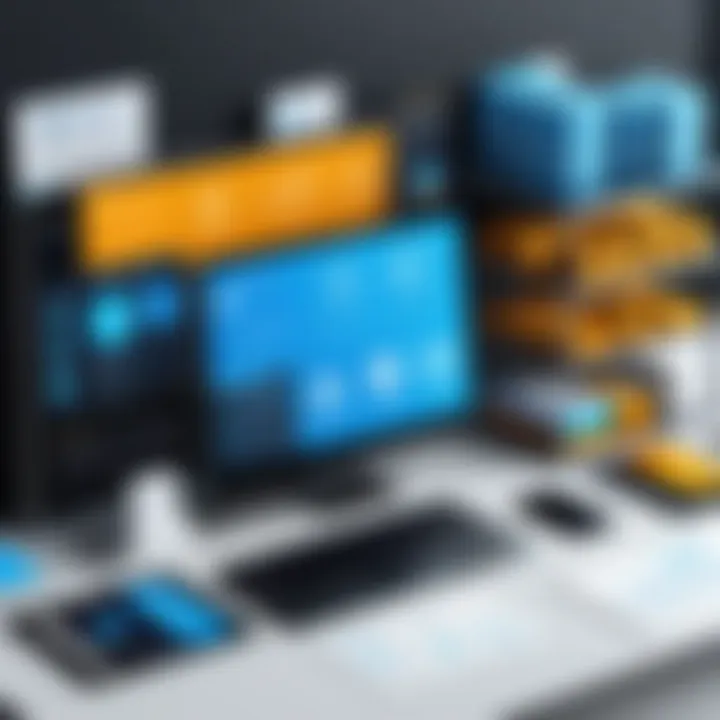
Training and Support Resources for Successful Deployment
Allocate enough time and resources for training. Tailored programs can boost confidence and competency among users. Offering ongoing support reduces potential roadblocks post-launch.
Future Trends
Predictions for the Future of the Industry-specific Software Landscape
The movement toward greater automation in inventory management is undeniable. Predictive analytics and AI-driven solutions will best represent upcoming advancements, aligning accuracy with cost reduction. As more businesses prioritize data-driven decision-making, future advancements will likely see deeper learning integrations.
Upcoming Technologies Shaping the Industry
Technology interactions will evolve in procurement networks. IoT integration is expected to drastically change inventory monitoring through enhanced traceability and real-time data exchange. These technologies will begin to form real-time supply chains, shifting approaches dramatically to simplify inventory processes.
Recommendations for Future-Proofing Your Technology Stack
To future-proof against rapid changes, companies should:
- Invest in adaptable software that can evolve with needs.
- Enhance cybersecurity to protect against burgeoning threats.
- Maintain strong vendor relations to stay informed on upgrades and services.
By focusing on these recommendations and implementing Yardi Inventory Control, businesses can seamlessly navigate the complexities of inventory management.
For professionals exploring advanced software solutions, a comprehensive understanding of Yardi Inventory Control, from effective integration to future trends, is paramount. Each strategic decision plays a vital role in driving operational excellence and sustainability.
Foreword to Yardi Inventory Control
Inventory control is a core piece in the management puzzle for many businesses. Understanding how to manage inventory effectively is vital for success. This guide will tackle how Yardi Inventory Control tools fit into this landscape. Yardi's solutions offer advanced options for tracking, which can greatly enhance operational efficiency. By adopting such tools, organizations can simplify processes, optimize resource allocation, and minimize wastage.
Understanding Inventory Control
Inventory control involves keeping track of stock and supplies in the most efficient way possible. This is not just about knowing how much is available. It's about knowing when to reorder, predicting future needs, and avoiding excess stock that ties up capital.
Key aspects of inventory control include:
- Tracking of Items: You need to know the location and quantities of all inventory items.
- Reordering Process: Establish points where new orders should be made.
- Reporting: Generate reports to understand trends and inventory turnover.
With better control, firms can forecast their needs more accurately, mitigating risks associated with overstocking or stockouts.
Overview of Yardi Systems
Yardi's suite of systems offers a comprehensive approach to inventory management. It integrates real-time tracking with automation features that significantly reduce manual tasks.
Yardi provides several elements that enhance inventory control:
- Real-Time Data: Access to live inventory levels helps make quicker decisions.
- Automation Tools: Automate workflows for replenishment and notifications, minimizing delays.
- Reporting Capabilities: Helpful insights from historical data will guide future spending and ordering scenarios.
Organizations that leverage Yardi's systems typically observe an improvement in operational efficiency. These tools are tailored for professionals seeking to invest in effective and systematic inventory management approaches.
To conclude, Yardi Inventory Control acts as a pivotal resource, allowing organizations to comprehend their inventory performance accurately, and, as a result, make informed decisions that align them with their broader business strategies.
Features of Yardi Inventory Control
Understanding the features of Yardi Inventory Control is essential for companies looking to optimize their inventory management processes. This section delves into the specific functionalities that Yardi offers, each delivering unique advantages in enhancing efficiency and decision-making capabilities for management professionals. These features are critical not only for tracking assets but also for ensuring that businesses remain agile and competitive in today’s fast-paced market.
Real-Time Inventory Tracking
Real-time inventory tracking is one of the standout features of Yardi Inventory Control. It allows businesses to continuously monitor stock levels, ensuring accurate information is readily available. This technology reduces the chances of stockouts or excess inventory, which can significantly affect a company’s bottoms line. With real-time data, users can make informed decisions on procurement, manage stock movement, and improve operational efficiency.
Key elements of real-time inventory tracking include:
- Instant updates: All changes in inventory levels are immediately reflected in the system.
- Mobile accessibility: Users can monitor inventory from anywhere, ensuring prompt actions are possible even outside conventional working hours.
- Data analytics: The system integrates analytical tools that help in forecasting trends based on current inventory movements.
This feature is increasingly vital in a world where consumer demand can shift rapidly, making it essential for businesses to be responsive and informed.
Automated Reordering
Automated reordering is another defining feature of Yardi that transforms the inventory management experience. This feature automatically triggers replenishment orders based on pre-set thresholds, ensuring that stock levels remain optimal without requiring constant manual oversight. Implementing automated reordering can lead to time savings, reduce the strain on human resources, and help eliminate errors often associated with manual data entry.
When considering automated reordering, it offers:
- Stock optimization: Businesses can prevent both surplus and shortage situations.
- Time efficiency: Reduces the hours spent on inventory checks and manual ordering.
- Supplier relationship management: Cultivates stronger relationships with suppliers due to predictable ordering patterns.
By utilizing automated reordering strategies through Yardi, organizations can enhance supply chain operations and focus valuable human resources on strategic initiatives.
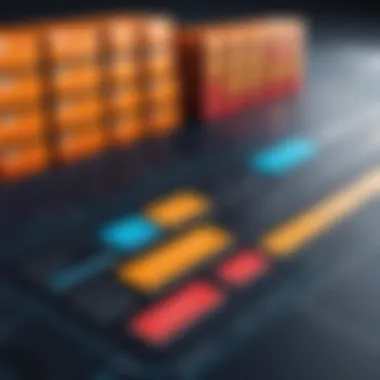
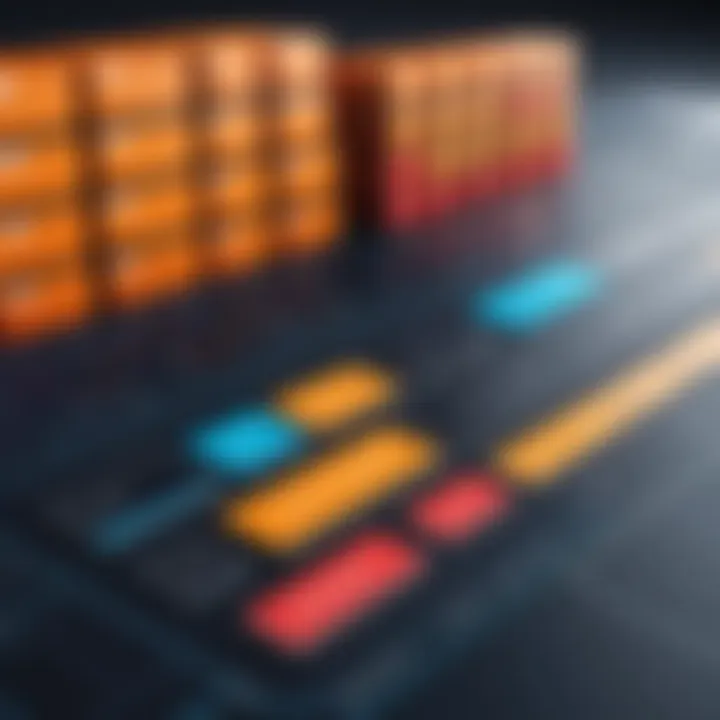
Integration with Other Yardi Modules
Integration with other Yardi modules is crucial for organizations already utilizing Yardi's suite of software. This feature allows seamless interaction across different functions, enhancing overall management of operations. It eliminates silos often present in inventory data and creates a unified information dashboard that improves strategic planning and execution.
Benefits of this feature include:
- Comprehensive performance tracking: Integrating financial and project management data provides deep insights into financial performance tied to inventory management.
- Improved forecasting capabilities: The synergy among modules facilitates more accurate demand forecasting, aligning inventory practices with future growth strategies.
- Streamlined workflows: When different modules communicate effectively, it reduces redundancy and improves operational coherence.
Employing Yardi's integrated approach enables organizations to harness powerful data analytics tools, providing an edge in a competitive marketplace.
Integration enhances the strategic decision-making process and overall operational effectiveness when utilizing Yardi Inventory Control.
Benefits of Using Yardi Inventory Control
Yardi Inventory Control brings a range of significant benefits to organizations aiming to enhance their inventory management processes. The impact of efficient inventory control extends beyond basic tracking. It influences overall business performance. Understanding these benefits can guide decision-makers in leveraging the system to optimize logistics and operations.
Increased Efficiency
One primary advantage of utilizing Yardi Inventory Control is increased efficiency in project execution. Time-slots are crucial in managing inventories. Yardi automates numerous manual processes. This automation allows staff to focus on high-value tasks rather than wasting hours on data entry or error checking.
- Streamlining Operations: Yardi facilitates a seamless flow of information. Stakeholders can monitor stock levels, usage rates, and ordering schedules in one platform.
- Faster Decision-Making: Immediate access to real-time data allows decision-makers to act quickly. A company can quickly reorder low-stock items before exhaustion.
Automated notifications regarding stock levels are another efficiency-enhancing feature. Alert systems will notify relevant team members about stock shortages or expirations, allowing time for corrective actions. Consequently, organizations can minimize delays caused by information gaps.
Cost Reduction Strategies
Using Yardi Inventory Control effectively can lead to substantial cost savings for companies. Cost reduction in inventory management impacts overall profitability significantly.
- Minimized Stock Levels: Through sophisticated data analysis, Yardi recommends optimal inventory levels to maintain. Less overstock minimizes unnecessary holding costs.
- Reduction in Waste: Avoid approximate ordering has substantial benefits. Optimized ordering reduces perishable stock waste, particularly beneficial for industries managing timelimited materials.
Besides, integrating inventory with budgeting features can aid in tracking variable expenses closely. Understanding expenditures allows companies to pinpoint areas where reductions are possible. This approach harmonizes business goals with financial health.
Improved Accuracy in Reporting
The precision of inventory data directly affects organizational planning and decision-making. Yardi ensures improved accuracy in many ways.
- Real-Time Tracking: Regular updates are provided within the system, reflecting true inventory status. Decision-makers can access the right data at the right time.
- Historical Data Analysis: Yardi captures data over time. By analyzing trends, businesses can derive accurate forecasts to refine purchasing activities.
Improvest inventory reports create a strong basis for internal accounting principles. Correctly structured data eliminates discrepancies and eases audit processes.
It's critical to note that boosting data accuracy leads to better strategic planning. With sound statistics, companies could streamline operations, reduce risk, and make precise forecasts for future growth.
In summary, the benefits illustrated demonstrate the foundational value of including Yardi Inventory Control in an organization's inventory processes. Increased efficiency, combined with cost-saving measures and improved data reporting, makes a robust case for adopting Yardi’s solutions.
Yardi Inventory Control in Practice
Yardi Inventory Control plays an essential role in practical inventory management. Merely having a reliable system is often not enough; the application of its features within different working environments demonstrates real-world value. Understanding how Yardi works in practice allows companies to maximize efficiency and adapt technology for unique needs. Additionally, comprehension of user experiences and appropriate settings creates a solid foundation for future usage.
Case Studies of Successful Implementation
Examining case studies can unveil best practices and common pitfalls when utilizing Yardi Inventory Control. For example, a retail chain implemented Yardi and found that significant waste reduction occurred through real-time stocking data. This enhancement helped minimize overstock situations by better forecasting usage and trends. Consequently, this company enjoyed greater cost savings and more efficient warehouse operations.
Similarly, a property management firm adopted Yardi to manage maintenance supplies more effectively. This implementation allowed for streamlined tracking and automated reordering processes that directly influenced operational capabilities. Staff members noted less time spent on inventory checks, enabling a refocus on critical tasks related to property health and amenities. Such findings underscore the importance of user training and solid onboarding to ensure proper use of the Yardi platform.
Key Learnings from Case Studies
- Real-time data leads to better stock management.
- Staff competence can transform operational effectiveness.
- Regular monitoring and evaluations ensure system adaptability.
Common Industry Applications
Yardi Inventory Control's versatility reveals several industry-specific applications. In the property management sphere, Yardi proves invaluable for tracking resources across multiple locations. This adaptability represents an outstanding benefit, especially for administrators managing vast portfolios.
Another sector where Yardi shines is the hospitality industry. In hotels and resorts, managing supplies such as toiletries and linens can make a significant dent in operational costs. Utilizing Yardi's tracking features streamlines ordering and inventory checks, promoting better guest experiences.
Furthermore, construction companies leverage Yardi for materials tracking across job sites. Projects often transition across various stages, and having immediate access to material availability helps to mitigate delays caused by unexpected shortages.
Most Frequent Applications Include:
- Resource management in property management.
- Supply control in hospitality settings.
- Material tracking in construction environments.
Challenges in Inventory Management
Effective inventory management is crucial for organizations that rely on maintaining stock levels, fulfilling orders, and minimizing waste. Robust inventory systems prevent financial losses, streamline operations, and improve customer satisfaction. Yet, despite these significant advantages, many organizations encounter several challenges in managing their inventory processes. Understanding these difficulties is essential for decision-makers, IT professionals, and entrepreneurs, as it unveils areas of potential improvement in operational efficiency and effectiveness.
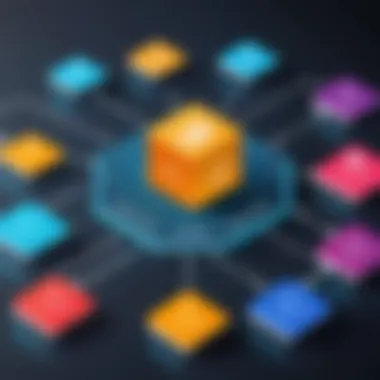
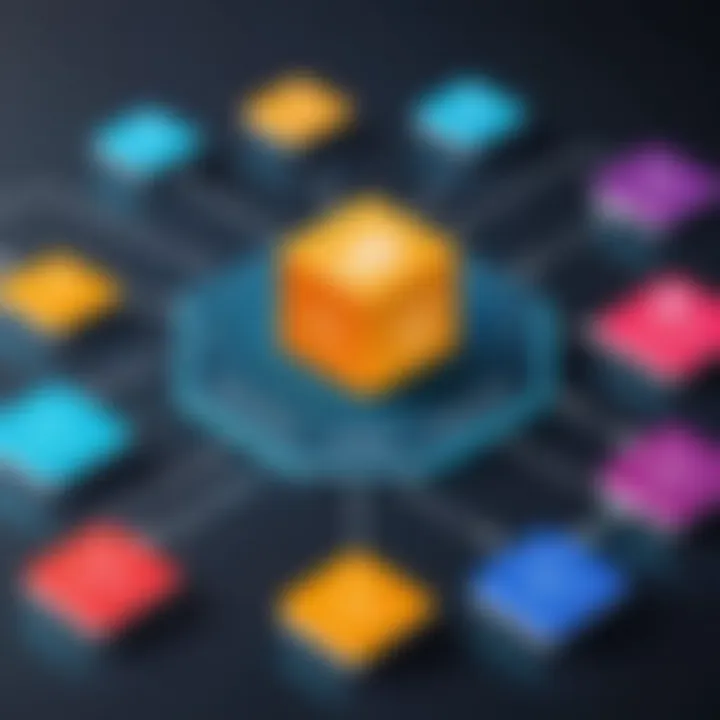
Data Management Issues
Data management stands out as a core challenge in inventory management. With the immense volume of data that modern organizations generate, ensuring data accuracy becomes increasingly complex. Inadequate data collection methods may lead to inaccurate inventory records, causing restocking errors or product shortages. Similarly, ineffective data integration from various sources can mislead decision-making processes. Businesses relying on manual inputs are especially vulnerable to errors, resulting in discrepancies that can fake the legitimacy of reports.
Moreover, centralized data systems are difficult to maintain, especially when diverse inventory types across multiple locations exist. This situation often leads to version control issues, where outdated or conflicting data resides in various departments, impacting overall coherence in inventory oversight. Addressing these challenges requires investment in robust data management systems and comprehensive training for the staff involved in inventory tracking. High-quality data creates an invaluable foundation for making informed decisions, optimizing inventory, and mitigating financial risks.
Technology Adoption Barriers
The acceptance of new technology within organizations presents another significant hurdle. Even the most advanced inventory control systems, such as Yardi Inventory Control, may face resistance from staff. This reluctance often stems from members feeling overwhelmed by changes or being unconfident in using technology. Consequently, inefficiencies may persist despite the implementation of superior tools.
A lack of comprehensive training adds to this problem. Organizations may implement new systems without adequately preparing their teams, leading to confusion. Employees must be confident in adopting and utilizing these systems, as this ensures effective operational support. Additionally, organizations must align their technology strategies with overall business objectives, emphasizing the relevance of adaptable methods as they evolve within marketplace trends.
To combat technology adoption barriers, a phased implementation approach may facilitate smoother transitions. This involves seeking employee perspectives during strategy formulation and being proactive in addressing concerns around privacy or operational changes. Engaging staff during early stages fosters buy-in and commitment to technology evolution, ultimately leading to greater inventory management success and supporting a seamless operational flow.
Best Practices for Effective Use of Yardi
Effective use of Yardi Inventory Control involves strategic practices that optimize its capabilities. Understanding these best practices is essential for any organization aiming to enhance its inventory management procedures. Implementing these methods can unlock significant advantages while addressing common pitfalls that stem from insufficient training or support. This section outlines vital best practices that can increase productivity and accuracy.
Training and Support for Staff
Training represents one of the cornerstones of successfully implementing Yardi Inventory Control. Staff members must understand not only how to navigate the software but also grasp the underlying principles of inventory management. Lessons should cover the full spectrum of the system's features, ensuring they are well-prepared to utilize all functions effectively.
Carrying out regular training sessions holds multiple benefits:
- Enhanced Proficiency: Familiarity boosts employee confidence and productivity.
- Reduced Errors: When staff understand processes, errors in inventory counts decline significantly.
- Incorporation of New Features: Continuous training aids in leveraging updates Yardi introduces.
Providing accessible support also contributes to streamlined operations. Support could be in the form of detailed documentation, dedicated help desks, and electronic forums, ensuring users do not feel overwhelmed or abandoned during usage.
Routine System Evaluations
Conducting routine evaluations of the Yardi system is another pivotal practice. Ensuring the software runs optimally can help identify issues before they escalate into larger problems. This might involve regular checks on data integrity, software updates, and user feedback collection.
A recommended approach is:
- Establishing a Regular Schedule: Monthly reviews can harbor timely problem identification.
- Utilizing Performance Metrics: Gathering data benefits the organization on overall operation and staff use efficiency.
- Adjusting Based on Feedback: Keep the evaluation dynamic; adapt systems based on user experiences and challenges.
Through immediate identification of potential setbacks, the organization can maintain a forward-leaning approach in its inventory management, ensuring the prowess of Yardi solutions is continuously being harnessed.
Effective training and regular evaluations are essential attributes to maximizing investments in Yardi Inventory Control. Ongoing commitment in these areas can open pathways to sustained operational excellence.
The Future of Inventory Management
The landscape of inventory management is evolving rapidly. As technology advances, businesses must adapt to new tools and practices. Understanding the future of inventory management is essential for decision-makers, IT professionals, and entrepreneurs.
Organizations that pay attention to these trends will likely gain a competitive edge. A significant focus in the future is on accuracy and real-time data access. Adaptability becomes essential in a world where market demands fluctuate frequently.
Trends in Inventory Technology
Inventory technology continues to shift with advancements in integration and automation. Notable trends include:
- Cloud-Based Solutions: These offer flexibility as businesses can manage assignments from anywhere.
- IoT Implementation: Nanotechnology enables devices that give companies real-time data painted. These devices will autonomously monitor and segregate inventory counts smoothly.
- Artificial Intelligence: Algorithms analyze historical data and improve forecasting to avoid shortages or overstock.
- Blockchain Relations: This technology can increase transparency and security in transactions involving inventory. Preventions against tampering become a proactive measure in many examples.
Businesses looking to adapt must also revise their overall inventory strategies. Workflow rethinking is necessary for hardware and software integrations.
Predicted Developments in Yardi Solutions
Yardi Solutions, known for excellence in property management technology, has a bright chance to innovate within inventory control. Future developments may include:
- Enhanced Integration: As dependencies on data grow, seamless syncing across multiple systems will become vital. Expect Yardi to refine cross-platform communicational features.
- User Experience Overhaul: Developers might focus more on user-centered dynamics for easier navigation. The result= better user adoption, enhancing overall satisfaction.
- Advanced Analytics: Future updates may introduce more sophisticated data analytics. Users will benefit including deeper insights through predictive algorithms optimizing performance.
- Mobile Capabilities: As the workforce becomes compliant with mobile technologies’ proliferation, Yardi may expand mobile functionalities for ease in management and operations.
Adapting to these predictions prepares organizations for the trends that shape their industries, fostering consistent growth.
The integration of futuristic technology into inventory management will cost less inefficiency and provide significant improvements in operations.
Closure
The conclusion of this article serves as a crucial segment in synthesizing the extensive insights gathered about Yardi Inventory Control. As the discussion unfolds, it reveals how a well-implemented inventory control system impacts several key areas such as operational efficiency, cost management, and error reduction in reporting. Those in decision-making roles must appreciate these influences to leverage technology and achieve their organization’s goals. Understanding this technology not only offers benefits in daily management but also serves as a tool for strategic growth.
Summary of Key Takeaways
- Importance of Real-Time Tracking: Continuous visibility into inventory has proven benefits, helping businesses react swiftly to stock levels and market demand.
- Automation Makes Life Easier: Yardi’s automated reordering capabilities are invaluable in maintaining appropriate stock levels and preventing shortages without manual intervention.
- Integration is Key: Utilizing other modules from Yardi enhances the effectiveness of inventory control, fostering a more unified data approach.
- Training and Regular Evaluation: Continuous staff training and system evaluations ensure ongoing improvement and adaptability to any changes in regulatory requirements or managerial strategies.
"Dedicating attention to optimizing inventory processes with Yardi could define business success in a competitive marketplace."
Final Thoughts on Yardi Inventory Control
Looking ahead, Yardi Inventory Control is not just a tool but a cornerstone of efficient business operations. Businesses that understand and adapt to its features harness the potential for streamlined operations and better decision-making. From minimizing understock and overstock scenarios to assuring that financial decisions are based on precise data, Yardi presents enhancements that go beyond mere functionality. Companies aiming for sustained growth will find that effectively managing inventory is not a choice but a necessity in today's fast-paced economic environment.
Being aware of this dual nature of Yardi’s influence — where operational efficacy meets strategic foresight — equips organizations to navigate their paths with confidence and clarity.