A Comprehensive Guide to Manufacturing Scheduling Software
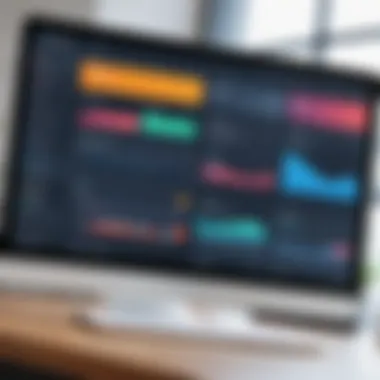
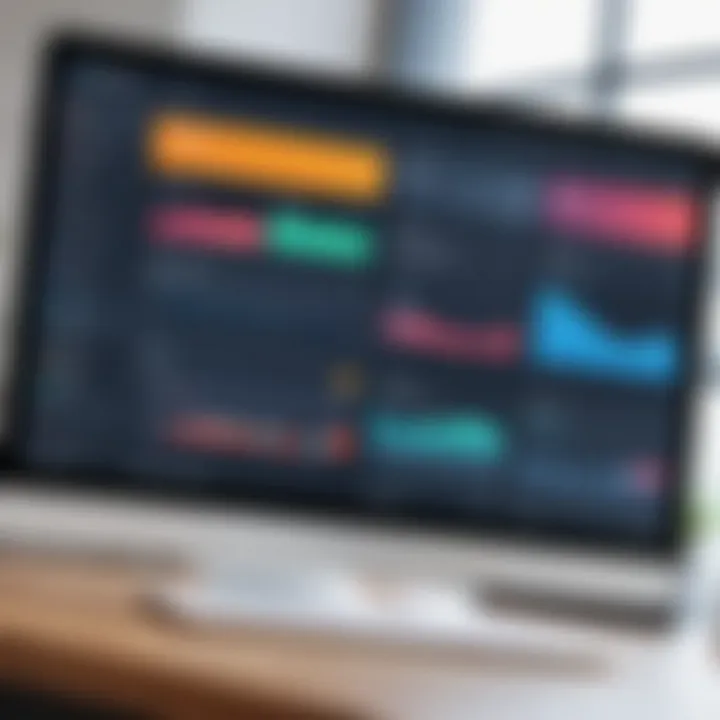
Industry Overview
The landscape of manufacturing employee scheduling software is complex and ever-evolving. As manufacturing processes become more intricate and demanding, the need for effective scheduling has escalated. Organizations seek tools that not only optimize labor allocation but also enhance productivity and minimize downtime. Scheduling software plays a crucial role in achieving these objectives.
Current Trends in the Industry-specific Software Market
In recent years, there has been a noticeable shift towards automation and data-driven decision-making in manufacturing. Companies are increasingly adopting cloud-based solutions, enabling real-time updates and enhanced collaboration across teams. This trend is propelled by the desire for greater flexibility and responsiveness to changing production demands.
Key Challenges Faced by Buyers in the Industry
Despite the advancements, buyers encounter several challenges when selecting employee scheduling software. Finding a solution that integrates seamlessly with existing processes is often difficult. Additionally, many buyers struggle to align software capabilities with specific operational needs. Cost considerations also play a significant role in decision-making, as manufacturers must balance investment against potential returns.
Emerging Technologies Impacting the Industry
Technologies such as artificial intelligence and machine learning are beginning to reshape employee scheduling capabilities. These advancements allow for predictive scheduling, where software can forecast labor needs based on historical data and trends. This proactive approach to scheduling not only improves efficiency but also enhances workforce morale by reducing last-minute changes to shifts.
Top Software Options
An array of software solutions exists in the market; each claims to provide the best features for manufacturing operations. Understanding the options available is essential for making an informed selection.
Review of Leading Software Providers in the Industry
Prominent software providers in the manufacturing scheduling space include Katanacreator, Samsara, and When I Work. Each vendor offers distinct functionalities and user experiences, catering to various manufacturing needs.
Feature Comparison of Top Software Solutions
When assessing these solutions, consider the following key features:
- User-friendly interface: Essential for quick adaptation by employees.
- Integration capabilities: Must connect with existing ERP systems.
- Mobile accessibility: Enables workers to access schedules on-the-go.
Pricing Structures of Different Software Options
Pricing models vary. Some software adopt a subscription-based model, while others offer one-time licensing fees. For instance, Katanacreator follows a tiered pricing structure based on user needs and company size, making it both flexible and scalable.
Selection Criteria
Choosing the right manufacturing employee scheduling software requires careful consideration.
Important Factors to Consider When Choosing Software
Evaluate flexibility, scalability, and user support when making your choices. A solution should cater not only to current needs but also anticipate future growth as your operations evolve.
Common Mistakes to Avoid During the Selection Process
Common pitfalls include insufficient user feedback during the selection process and failing to conduct a thorough needs analysis. By involving end-users early, manufacturers can ensure the selected software meets real-world requirements.
How to Determine the Right Fit for Your Business Needs
Conducting a thorough assessment of available options helps to establish a better fit. Customize demos and trials to gauge how well the software aligns with organizational workflows.
Implementation Strategies
Successful implementation of scheduling software is crucial for maximizing its benefits.
Best Practices for Smooth Implementation of Software Solutions
Begin with a clear roadmap for the implementation process. Include timelines and clearly defined milestones. Favor incremental deployment to reduce disruptions during transition.
Integration with Existing Systems and Processes
Ensure that the new scheduling software can integrate with current manufacturing systems. This reduces the adjustment period and fosters acceptance among staff.
Training and Support Resources for Successful Deployment
Investing in employee training is vital. Ensure that comprehensive training resources are available. This helps to maximize adoption and reduces resistance to new processes.
Future Trends
Looking ahead, the manufacturing industry will likely experience continued transformations in employee scheduling practices.
Predictions for the Future of the Industry-specific Software Landscape
Anticipate an increasing reliance on integrated platforms that connect scheduling with broader operations management tools. These solutions will provide more holistic insights into workforce needs and operational efficiency.
Upcoming Technologies Shaping the Industry
Emerging technologies, such as advanced analytics and IoT, are positioned to redefine scheduling practices. Connecting devices and systems will provide real-time data, enriching scheduling accuracy.
Recommendations for Future-Proofing Your Technology Stack
Align technology investments with strategic business goals. This foresight enables organizations to remain agile as new developments arise.
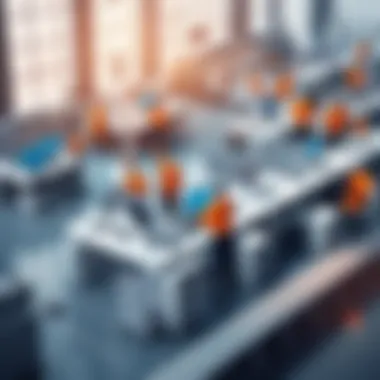
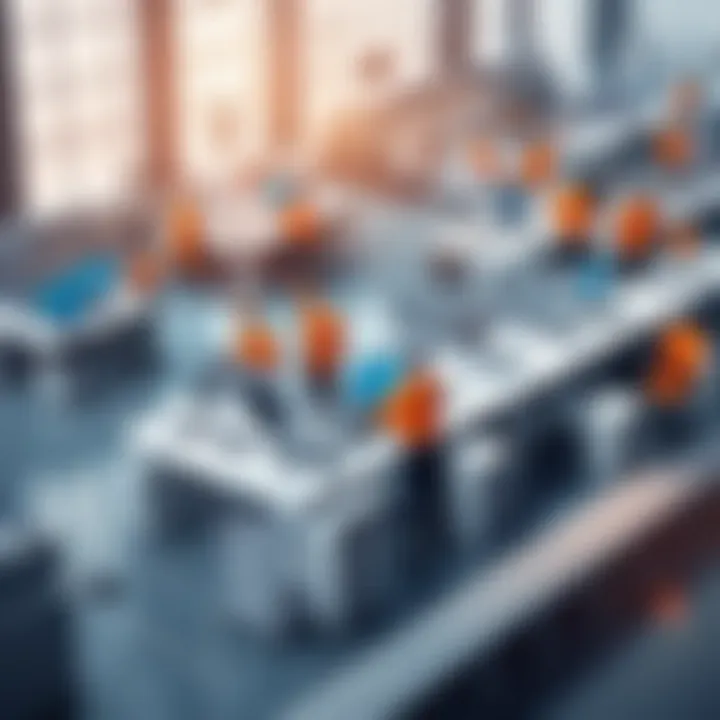
"The right software solutions can be a game changer for manufacturing operations, delivering efficiency and clarity in workforce management."
Integrating robust scheduling software into manufacturing processes stands as a pivotal step towards operational excellence. Engaging with the right solution today will prepare businesses for future challenges.
Understanding Employee Scheduling in Manufacturing
Effective employee scheduling in manufacturing is a critical element that contributes to operational success. Scheduling is not merely about assigning shifts; it involves balancing workforce needs with machine availability, optimizing production flows, and ensuring compliance with labor regulations. When executed efficiently, robust scheduling systems can enhance productivity, reduce costs, and improve employee satisfaction.
The Importance of Efficient Scheduling
Efficient scheduling directly influences productivity levels in a manufacturing setting. It ensures that the right number of employees with the right skills are working at the optimal time, creating a seamless production environment. For example, having too few workers can lead to delayed outputs, while overstaffing can increase labor costs unnecessarily. The goal is to achieve an ideal balance, where resources are allocated appropriately to match production demands.
Moreover, effective scheduling helps in minimizing overtime costs and employee burnout. By analyzing past production data and employee availability, managers can design rotas that not only meet the business needs but also respect worker preferences and personal situations. This can lead to higher morale among staff and lower turnover rates, which is especially beneficial in the manufacturing sector where skilled labor shortages can be an ongoing challenge.
Unique Challenges in Manufacturing Scheduling
The manufacturing sector faces unique challenges regarding employee scheduling. Firstly, high turnover rates can disrupt established schedules, leading to gaps in labor that impact production continuity. Replacing personnel requires rescheduling as firms must quickly integrate new staff with existing teams to maintain output levels.
Additionally, last-minute absences due to illness or emergencies can create immediate scheduling crises. These unforeseen situations necessitate swift adjustments to maintain production schedules, often requiring managers to deploy staff from other areas or implement overtime.
Compliance with labor regulations is another significant concern. Manufacturing environments must abide by various laws concerning working hours, breaks, and health and safety regulations. Failure to comply can result in legal penalties, further complicating the already challenging task of scheduling.
"Understanding the intricacies of scheduling can save manufacturing companies significant time and resources, transforming potential challenges into streamlined operations."
In summary, understanding employee scheduling in manufacturing is essential for optimizing productivity and ensuring regulatory compliance. Equipped with effective scheduling software, companies can tackle the unique challenges of this industry while improving overall operational efficiency.
Overview of Employee Scheduling Software
Employee scheduling software is a critical component for optimizing workforce management in the manufacturing sector. Its design and purpose are to facilitate the efficient allocation of labor resources, manage shifts, and ensure compliance with regulations. Companies increasingly recognize how automated systems can lead to significant operational enhancements. This section will explore what this software entails, its defining features, and the distinct benefits it provides, all aimed at ensuring a smoother workflow in manufacturing environments.
Definition and Purpose
The definition of employee scheduling software extends beyond simple timetabling. At its core, it is a tool that automates the planning of employee shifts, thereby maximizing productivity and covering labor necessary for meeting production goals. Its purpose is to address various scheduling needs, ranging from routine shift allocations to accommodating last-minute changes. By delivering a thorough overview of workforce availability, it aids managers in making informed decisions, mitigating risks associated with understaffing or overstaffing.
Key Functionality of Scheduling Software
The functionality of employee scheduling software is multifaceted. It encompasses a range of features designed to simplify scheduling processes. Understanding these functionalities helps decision-makers identify which software aligns best with their specific manufacturing needs.
User-Friendly Interface
A user-friendly interface is essential for any software, particularly for scheduling. It allows users to navigate the system with ease and reduces the learning curve for employees. This aspect enhances overall efficiency.
Key characteristic of a user-friendly interface is its intuitive design. This ensures that users can quickly find the necessary tools without extensive training. For instance, drag-and-drop features allow managers to adjust schedules in real-time with minimal hassle.
Unique feature of such interfaces is the visual representation of schedules. Color-coded shifts and clearly marked employee names contribute to quicker understanding of the workforce allocation, reducing errors in planning.
Automated Scheduling
Automated scheduling is a game changer in manufacturing. It leverages algorithms to optimize shift assignments, considering factors like employee availability and skills. This functionality can lead to better resource utilization.
One key characteristic of automated scheduling is its ability to quickly process large amounts of data. This analysis generates optimal shift configurations, freeing managers from tedious manual processes.
A unique feature is the capability to learn from historical data, which informs future scheduling decisions. This not only improves efficiency but also enhances employee satisfaction when their preferences are considered.
Real-Time Updates
In the context of manufacturing, real-time updates to scheduling are invaluable. They allow immediate response to changes such as absenteeism or sudden demand increases. This contributes significantly to operational resilience.
The key characteristic of this functionality is its ability to communicate changes instantly across the system. Notifications about shift changes can be sent automatically, ensuring all employees are informed promptly.
A unique feature here includes mobile notifications, which enable employees to receive updates on the go. This timely information helps maintain productivity and operational flow.
Integration with Existing Systems
Integration capability with existing systems is paramount for effective scheduling software. This feature allows for seamless communication between different platforms, such as HR, payroll, and production tracking tools.
The key characteristic of this functionality is its ability to centralize data gathering. This centralization aids accountability and ensures that managers have access to comprehensive information across various departments.
A unique feature is the facilitation of data synchronization. By ensuring that all systems are updated simultaneously, it reduces redundancy and potential errors in scheduling, leading to a more cohesive operation.
Proper implementation of these functionalities ensures that manufacturing operations run smoothly, improving not just productivity but enhancing employee engagement.
Features to Look for in Manufacturing Scheduling Software
Choosing the right manufacturing scheduling software is crucial. It can significantly impact your company's efficiency and productivity. The right features not only streamline scheduling but also help in managing the workforce effectively. Here are key features to consider:
Workforce Management Tools
A robust workforce management tool is essential. This feature enables managers to track employee availability, shifts, and tasks. It also allows for managing overtime and shift swaps. A good workforce management tool should facilitate:
- Ease of communication between team members
- Quick response to changing work conditions
- Visibility of each employee’s scheduling needs
With these capabilities, manufacturing companies can reduce scheduling conflicts and improve employee satisfaction.
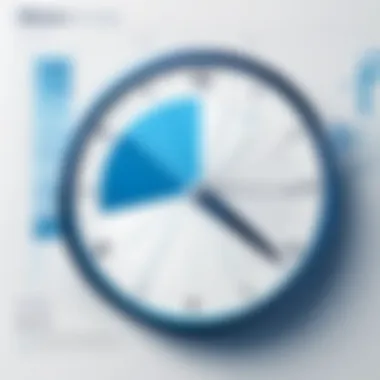
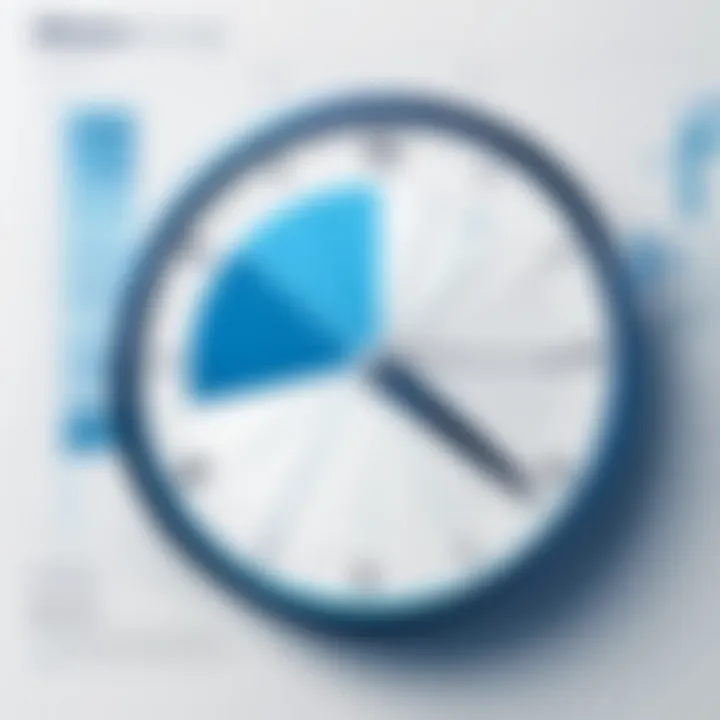
Reporting and Analytics
Effective reporting and analytics enhance decision-making. This feature provides insights into labor costs, productivity levels, and scheduling effectiveness. It becomes easier to:
- Identify trends and patterns within the workforce
- Pinpoint areas that need improvement
- Evaluate the performance of scheduling strategies over time
By analyzing this data, decision-makers can make informed choices to optimize scheduling processes. Reports should be easy to generate and comprehend, making information accessible to all relevant parties.
Mobile Accessibility
In today’s fast-paced environment, mobile accessibility cannot be overlooked. Employees should have the ability to check their schedules, make requests, and swap shifts using mobile devices. This feature contributes to:
- Greater flexibility for employees
- Enhanced engagement and accountability
- Real-time updates that keep teams aligned
By allowing access through mobile apps or responsive design, businesses foster a more empowered workforce, thus improving overall morale.
Compliance Tracking
Compliance with labor regulations is vital in manufacturing. Scheduling software should include compliance tracking tools. These tools help ensure adherence to:
- Labor laws concerning hours worked
- Safety regulations specific to the manufacturing industry
- Organizational policies on employee rights
Having monitoring capabilities allows companies to avoid legal repercussions. It also encourages a safer work environment. Noncompliance can be costly, and tracking these aspects reduces risks.
"Implementing the right scheduling software with these features is a game changer for manufacturers. It is not just about managing schedules but optimizing the entire workforce's performance."
In summary, when selecting manufacturing scheduling software, it is essential to focus on core features that facilitate efficient workforce management, enhance reporting capabilities, provide mobile accessibility, and ensure compliance with regulations. This thoughtful approach can lead to a more organized, productive, and engaged workforce.
Benefits of Utilizing Scheduling Software in Manufacturing
Implementing employee scheduling software in manufacturing brings many advantages that address operational challenges and elevate productivity. This section will clarify how businesses can harness these benefits to create more efficient and cost-effective systems.
Enhanced Productivity
One of the most significant advantages of utilizing scheduling software is the enhancement of productivity across the organization. Manufacturing environments often involve complex processes and varying labor requirements. By using scheduling software, managers can optimize shift allocations based on personnel availability and production needs. This leads to a more streamlined operation, where each worker's skills are utilized efficiently.
Automated scheduling tools can analyze historical data and trends, allowing for adjustments that can improve output. Furthermore, being able to quickly adapt to changes or spikes in demand reduces downtime. Employees can also update their availability through the software, helping to mitigate scheduling conflicts that could disrupt work flow. Ultimately, better scheduling directly correlates with increased overall productivity.
Reduced Labor Costs
Reducing labor costs is a focal point for many manufacturing companies. Employee scheduling software provides detailed insights into labor expenses, enabling precise control over staffing levels. Businesses can analyze when there are excess personnel during low-demand periods and adjust staffing accordingly.
Moreover, accurate scheduling minimizes overtime and ensures that the company complies with labor regulations, preventing unexpected costs. Using data from the software, manufacturers can identify patterns that lead to more informed decisions about temporary hires or part-time staff. This intelligent approach to workforce management results in lower labor costs without sacrificing output quality.
Improved Employee Satisfaction
Employee satisfaction plays a crucial role in the success of any manufacturing operation. Effective scheduling allows for more predictable work hours, which can help workers balance personal and professional responsibilities. Software platforms often facilitate requests for shift changes or time-off, providing employees with a sense of control over their schedules.
Additionally, greater transparency in the scheduling process leads to trust between management and staff. When workers feel that their needs and preferences are considered, it increases engagement and retention.
"Employee satisfaction is a key indicator of overall productivity and retention rates. When workers are satisfied, they are more likely to contribute positively to the organization."
Implementation Strategies for Scheduling Software
Implementing employee scheduling software is a critical step in enhancing operational efficiency in the manufacturing sector. The strategies chosen for deployment can significantly impact user adoption, overall functionality, and immediate gains from the software. It is essential for decision-makers to clearly define and understand the strategies that extend beyond mere software installation. This section delves into the key strategies for implementing scheduling software, ensuring a successful transition and optimal use of the tool.
Needs Assessment
A thorough needs assessment is the foundational step in implementing scheduling software. This involves identifying the precise requirements of the organization and understanding the unique challenges faced by the workforce. Businesses should conduct interviews, surveys, and workshops with employees and stakeholders to gather qualitative and quantitative data. Key considerations include:
- Workforce size: Understanding the number of employees who will use the software affects system capability.
- Work hours and shifts: Determining the current scheduling patterns helps identify areas for improvement.
- Regulatory requirements: Considering relevant labor laws ensures compliance from the start.
By defining these elements, organizations can better align software features with actual needs, reducing the chance of under- or over-investing in capabilities.
Choosing the Right Software
Selecting the appropriate scheduling software is crucial for achieving the desired outcomes. The market offers a wide array of options, but not every solution is suitable for every organization. Here are some factors to consider:
- Scalability: The software should grow with the organization without significant additional investment.
- User-friendliness: A simple interface ensures quick adoption among employees from various skill levels.
- Customization capabilities: Look for software that allows customization to meet specific needs.
After determining these factors, organizations can analyze available software and assess vendor support, pricing, and reviews to make an informed decision.
Training Employees
Training employees on the newly implemented scheduling software is often overlooked, yet it is paramount for success. A well-structured training program should cover:
- Basic functionalities: Employees must understand how to navigate the software and utilize its features.
- Advanced tools: Offering training on specific tools ensures employees can maximize the software's potential.
- Ongoing support: Providing access to help resources or support personnel can reduce frustration and enhance productivity.
Proper training fosters confidence among employees, leading to better utilization and satisfaction.
Integration into Existing Systems
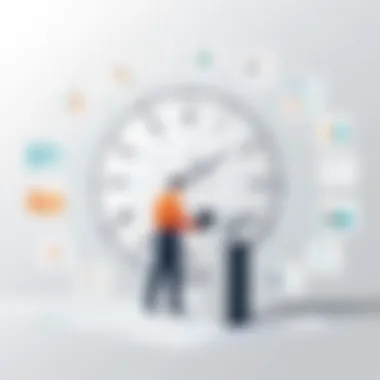
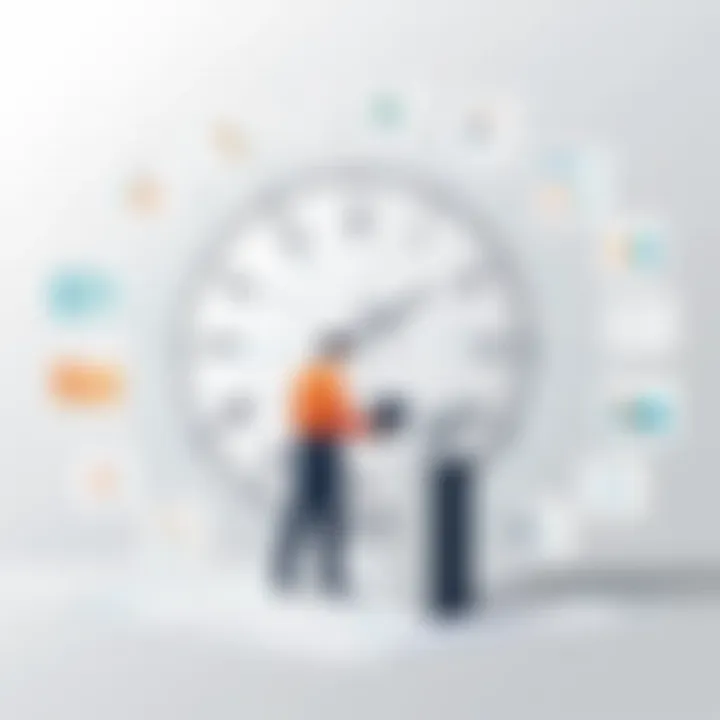
A successful implementation of scheduling software often requires integration with existing systems. This task can be complex, demanding careful planning. Here are steps to guide this process:
- Data migration: Ensure historical scheduling data is accurately imported into the new system.
- System compatibility: The new software should work seamlessly with current tools, such as payroll and HR systems.
- Testing: Conduct rigorous testing to ensure all features work as intended before a full rollout.
A seamless integration minimizes disruptions in workflow and helps in achieving immediate results.
"The right implementation strategies not only ensure a hallmark transitioning experience but also optimize the use of scheduling software in enhancing productivity."
By following these implementation strategies, manufacturing organizations can set a strong foundation for using scheduling software effectively, maximizing its benefits and minimizing the challenges often associated with such transitions.
Challenges in Manufacturing Employee Scheduling
Employee scheduling in manufacturing poses unique challenges that can significantly impact productivity, employee morale, and compliance with labor laws. Understanding these challenges is crucial for decision-makers who aim to implement effective scheduling practices. Acknowledging and addressing these challenges can lead to smoother operations and a more engaged workforce.
High Turnover Rates
High turnover rates in manufacturing can disrupt the scheduling process. Frequent changes in personnel mean that managers must constantly adapt schedules to accommodate new or less experienced employees. This can lead to inefficiencies and increased labor costs. Moreover, high turnover can fragment team dynamics, leading to a loss of institutional knowledge.
To mitigate this issue, it is crucial to analyze the reasons behind turnover. Factors such as inadequate compensation, lack of career advancement opportunities, and poor work-life balance often contribute to employees leaving their positions. By addressing these elements and creating a more employee-centric culture, companies can enhance retention rates. Additionally, utilizing software that allows for quick adjustments to schedules can help manage turnover more effectively.
Last-Minute Absences
Last-minute absences, whether due to unforeseen circumstances or planned time off, can complicate the scheduling landscape. In manufacturing, where operations often depend on precise staffing levels, these absences can lead to operational bottlenecks. Moreover, a sudden lack of personnel can place additional strain on remaining employees, which can affect their performance and morale.
To address last-minute absences, it is important to have a contingency plan in place. This might involve cross-training employees so that team members can fill in for one another as needed. Additionally, leveraging employee scheduling software that provides real-time updates can help managers find replacements quickly, minimizing disruptions.
Compliance with Labor Regulations
Compliance with labor regulations is a critical element of employee scheduling in manufacturing. Regulations regarding working hours, overtime, and rest periods vary across regions and must be strictly adhered to avoid legal repercussions. Non-compliance can lead to hefty fines and damage to the company’s reputation.
To ensure adherence to labor laws, companies should use scheduling software that incorporates compliance tracking features. This allows managers to see at a glance whether schedules adhere to relevant regulations. Regular audits and updates of scheduling policies with the changing legal landscape will further ensure that the organization remains compliant.
In summary, navigating the challenges of manufacturing employee scheduling requires a proactive approach. By understanding high turnover rates, preparing for last-minute absences, and ensuring compliance with labor regulations, organizations can optimize their scheduling processes.
Case Studies: Successful Software Implementations
Case studies serve as a practical lens through which the benefits and effectiveness of employee scheduling software can be assessed. They allow industry professionals to understand how real-world organizations have navigated their scheduling challenges, implemented software solutions, and derived tangible benefits. By examining these examples, decision-makers can gather actionable insights that inform their own strategies for adopting scheduling tools within their operations.
Company A: Reducing Downtime
Company A, a mid-sized manufacturer specializing in automotive components, faced significant issues with production inefficiencies. The primary challenge was balancing production schedules with labor availability. With frequent last-minute absences, the organization often found itself understaffed, causing costly downtime and increased operational costs.
After implementing a robust scheduling software solution, the company saw an immediate improvement. The software offered real-time visibility into employee availability and skills. This allowed managers to create responsive schedules that optimized labor use. The automated alerts notified supervisors of absences, enabling them to reassign tasks promptly. Consequently, Company A reduced its downtime by 25% within the first six months.
This case highlights the importance of real-time updates and automated scheduling features in manufacturing environments. The adaptability gained through using scheduling software allowed Company A to maintain steady operations, even in the face of unexpected challenges.
Company B: Enhancing Employee Engagement
Company B, a large food processing plant, struggled with low employee morale, partially due to rigid scheduling practices that did not consider employee preferences or lifestyles. Workers often faced unanticipated shifts leading to dissatisfaction and attrition. To address this, the company decided to invest in employee scheduling software that included features for better engagement.
The software provided employees with access to their schedules via a mobile app. They could submit shift preferences, request time off, and even pick up extra shifts when available. This transparency and control over their schedules significantly enhanced employee engagement. Over a one-year period, Company B reported a 40% increase in employee satisfaction scores. Moreover, the lower turnover rate translated into reduced training costs and a more experienced workforce.
The success of Company B demonstrates that scheduling software can do more than just optimize labor; it can also foster a positive workplace culture. Engaging employees in the scheduling process leads to greater job satisfaction, lower turnover, and ultimately, a more productive operation.
Future Trends in Manufacturing Scheduling Software
The landscape of manufacturing employee scheduling is undergoing significant transformation. Understanding the future trends in this domain is crucial for organizations aiming to stay competitive and innovative. Technology is evolving rapidly, and its integration into scheduling software is no exception. This section focuses on two critical trends: the incorporation of artificial intelligence and the integration of remote monitoring tools. These developments are set to revolutionize how companies approach workforce management.
Artificial Intelligence and Predictive Analytics
Artificial Intelligence (AI) is bringing forth a new era in employee scheduling. One of the most notable aspects is predictive analytics. This technology analyzes historical data and identifies patterns to forecast future workforce needs. For instance, it can predict busy periods or potential absences, allowing managers to allocate resources more effectively.
Implementing AI-driven scheduling also enhances decision-making. Management can make informed choices based on data rather than intuition, which reduces the likelihood of errors. Moreover, AI can facilitate automated scheduling. This streamlines the process, saving time and reducing administrative burdens.
Another advantage of AI is its adaptability. As conditions within the manufacturing environment change—be it new regulations or market fluctuations—the software can adjust. This flexibility ensures that scheduling aligns with the current operational landscape. According to industry experts, companies that embrace AI will see improved workflow efficiency and a reduction in labor costs.
"AI in scheduling is not just a trend; it’s an imperative for businesses wanting to gain a competitive edge in the manufacturing sector."
Integration of Remote Monitoring Tools
The second trend is the integration of remote monitoring tools into scheduling software. With the rise of smart manufacturing, many companies utilize sensors and IoT devices to collect real-time data. This data can inform scheduling decisions, such as monitoring machine availability and employee performance.
Remote monitoring enables a more responsive and agile scheduling system. If a machine goes down unexpectedly, the software can immediately alert managers, who can then reallocate tasks to ensure productivity is not hindered. Moreover, organizations can assess workforce capabilities remotely, identifying skill gaps that require urgent attention.
Additionally, integrating remote monitoring tools into scheduling promotes transparency and communication. Employees can access their schedules and updates directly from any device. This access not only enhances employee satisfaction but also encourages accountability. Workers can receive notifications for any last-minute changes or adjustments, ensuring they are always on the same page.
The End
In the ever-evolving realm of manufacturing, understanding the intricacies of employee scheduling software is crucial for maintaining operational efficiency. The conclusion synthesizes key learnings, emphasizing the relevant factors that decision-makers should consider when selecting and implementing such tools.
The Significance of Scheduling Software Scheduling software serves as a foundational element in managing workforce dynamics. Its ability to provide real-time updates, automate tedious processes, and integrate seamlessly with existing management systems can lead to enhanced productivity. The implications of these benefits directly impact both the bottom line and employee satisfaction.
Considerations for Selection
When choosing scheduling software, it is essential to evaluate features that address unique manufacturing challenges. This includes functionalities that enable:
- Automated scheduling to minimize human error.
- Mobile accessibility to manage schedules on-the-go.
- Compliance tracking features that ensure adherence to labor regulations.
Final Thoughts on Effectiveness
Implementing the right software is not a one-size-fits-all solution. Each manufacturing environment has its distinct needs that require tailored approaches. Thus, the importance of conducting a thorough needs assessment can’t be overstated.
Ultimately, the success of scheduling software in manufacturing hinges on its fit within the organizational strategy and its alignment with long-term business goals. Engaging all stakeholders from the onset ensures a smoother transition and maximizes the software's potential. By following these considerations, manufacturing firms can position themselves to reap significant benefits, streamline operations, and enhance overall workforce management.