Mastering Warehousing Management Systems for Efficiency
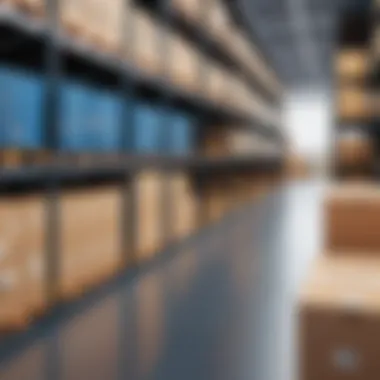
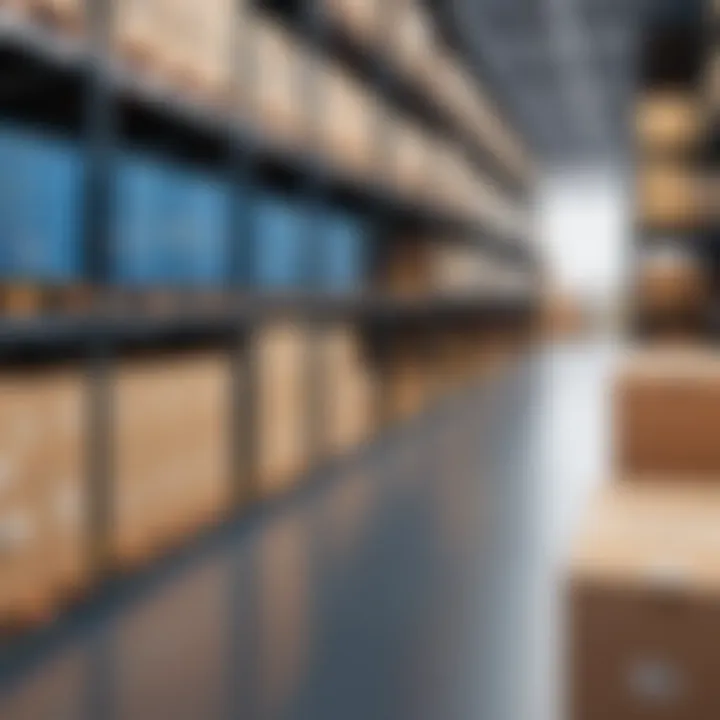
Intro
Warehousing Management Systems (WMS) play a pivotal role in the smooth operation of logistics and supply chain management. These systems act as the backbone of fulfillment strategies, helping businesses streamline their operations while drastically improving efficiency. The evolution of WMS reflects broader trends in technology and consumer expectation, resulting in systems that are no longer merely about storage but about optimizing every component of warehousing.
Understanding the complexities of WMS is crucial for decision-makers, IT professionals, and entrepreneurs in today's fast-paced market environment. A well-chosen WMS can lead to remarkable transformations in cost savings, inventory management, and customer satisfaction. As the demand for rapid delivery continues to rise, this guide aims to equip you with the insights needed to navigate this intricate landscape with confidence.
Industry Overview
To grasp how WMS fits into the bigger picture, one must first delve into the current state of the industry. Managed directly by software providers, the industry is continuously evolving. Companies are now turning towards innovative solutions that incorporate advanced technologies while maintaining user-friendliness at the forefront.
Current Trends in the Industry-specific Software Market
Several trends have emerged in the warehousing management field:
- Cloud Computing: Many businesses are transitioning from on-premises solutions to cloud-based systems for their flexibility and scalability.
- Automation: Automated systems are becoming paramount, with tasks like order picking and inventory tracking now commonly integrated into everyday operations.
- Mobile Technology: Using mobile devices for inventory management has become a norm, allowing for real-time data access and better communication across teams.
Key Challenges Faced by Buyers in the Industry
When selecting a WMS, buyers often encounter significant hurdles, including:
- Integration Difficulties: Merging a new system with existing technology can be complex and costly.
- Vendor Lock-in: Concerns about being tied to one provider can prevent businesses from making the best choice.
- Cost Overruns: Many underestimate the total investment required for implementation and ongoing maintenance, leading to unplanned expenses.
Emerging Technologies Impacting the Industry
With rapid advancements in technology, these innovations are notably shaping the WMS landscape:
- Artificial Intelligence: Utilizing AI can enhance predictability in inventory management, reducing costs by optimizing stock levels.
- Internet of Things (IoT): Smart sensors connected through IoT facilitate real-time inventory tracking and enhance operational awareness.
- Blockchain Technology: Increasingly used to enhance transparency and security in transactions across the supply chain.
"In today's world of logistics, a strategic WMS is akin to having a seasoned pilot at the helm of a ship navigating through turbulent waters."
In wrapping up this overview, it's clear that understanding these trends, challenges, and technologies is foundational for anyone looking to leverage warehousing management systems effectively. The groundwork laid here sets the stage for a deeper exploration into the various software options available, selection criteria, implementation strategies, and future trends that will continue to define this ever-evolving space.
Understanding Warehousing Management Systems
Understanding Warehousing Management Systems (WMS) is crucial for anyone involved in supply chain logistics today. The modern landscape of warehousing requires agility and precision, two qualities that a robust WMS can provide. It is not just about storing goods; it is about managing inventory in a way that optimizes workflow, reduces costs, and enhances accuracy.
A well-implemented WMS can streamline various operations, ultimately leading to higher customer satisfaction. The benefits extend beyond simple inventory tasks. Features like real-time tracking and automated reporting can transform how businesses perceive their operations.
When considering a WMS, one must weigh factors such as ease of integration with existing systems and scalability to grow with the business. As we dive into the details, keep in mind the significant shift that a WMS can bring to an organization's logistics. More than just software, it is a tool that redefines how warehouses operate, paving the way for smarter decisions and optimized resources.
Definition of Warehousing Management Systems
Warehousing Management Systems refer to software solutions that manage, control, and optimize warehouse operations. Simply put, it's like the brain of a warehouse that coordinates everything from receiving goods to shipping them out. These systems automate various processes, providing insights that help to make informed decisions.
Key functions of a WMS include:
- Inventory Management: keeping tabs on stock levels, locations, and status.
- Order Fulfillment: ensuring that orders are picked, packed, and shipped in an efficient manner.
- Labor Management: overseeing workforce performance as it ties to productivity.
A WMS not only reduces errors but also enhances the overall productivity of warehouse staff. Such systems can integrate with other business processes to create a seamless flow of information, which is vital for meeting client demands effectively.
Historical Background
The evolution of Warehousing Management Systems has been as dynamic as the logistics industry itself. Traditionally, warehouses operated manually. Workers relied on paper-based methods and spreadsheets, which often led to inefficiencies and errors. The introduction of technology, specifically in the late 20th century, brought about a significant change.
Initially, WMS were rudimentary tools that aided only basic inventory tracking. Over time, as globalization took shape and technology advanced, these systems grew more sophisticated. They began incorporating features like real-time data analytics, automated alerts, and even barcode scanning. This shift allowed warehouses to enhance accuracy in inventory management and better respond to market demands.
"A WMS is not merely a tool; it is a cornerstone for achieving operational excellence in warehousing."
Currently, WMS continues to integrate emerging technologies like Artificial Intelligence and machine learning. These advancements not only improve efficiency but also predict trends and consumer behaviors, making them invaluable in today’s fast-paced market. From a historical lens, the journey of WMS reflects the unyielding pursuit of efficiency and operational excellence in warehousing.
Core Functions of WMS
Understanding the core functions of Warehousing Management Systems (WMS) is crucial for any organization seeking to optimize its logistics and supply chain management. These systems are not just tools but vital components that help manage the intricate web of warehousing operations. They contribute significantly to the efficiency, accuracy, and overall performance of logistics operations. It’s important to delve into specific aspects like inventory management, order fulfillment, labor management, and reporting and analytics, as each function plays a distinct role in enhancing operational success.
Inventory Management
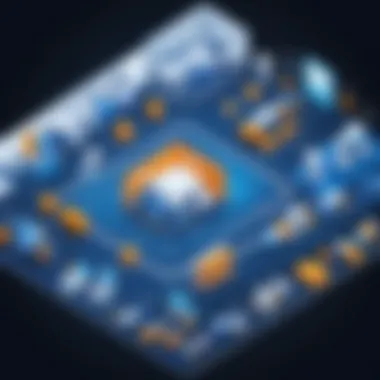
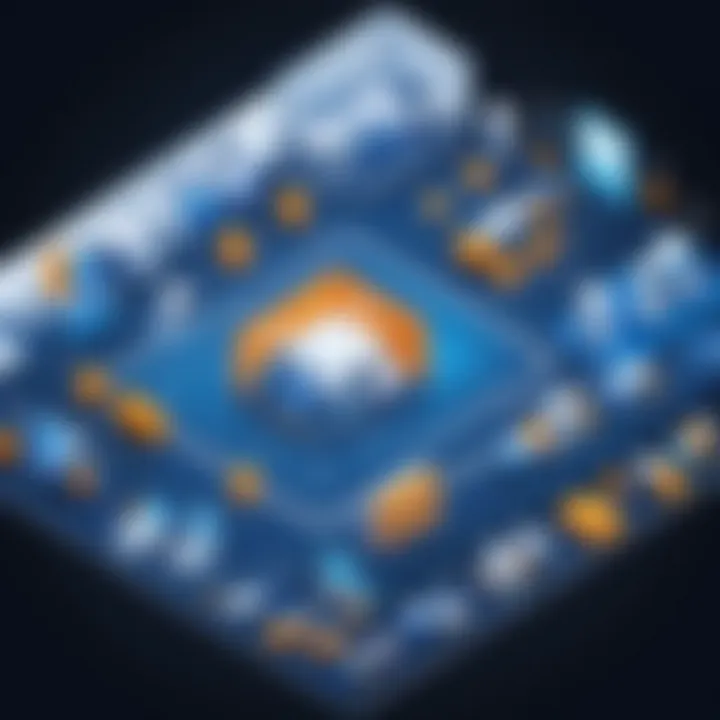
As one of the primary facets of WMS, inventory management ensures that products are adequately tracked and managed throughout their lifecycle within the warehouse.
Real-time Tracking
Real-time tracking is the heartbeat of effective inventory management. This capability allows businesses to monitor stock levels continuously, providing immediate visibility into what is available and what needs replenishing. The key characteristic of real-time tracking is its ability to reduce discrepancies caused by manual processes. This level of accuracy is a game-changer, especially for companies dealing with large volumes of products. The unique feature of real-time tracking is its integration with barcode scanning systems, simplifying the data collection process. However, despite its numerous advantages, the requirement for constant updates and the potential dependency on technology can pose challenges, especially if the system fails.
Stock Optimization
Stock optimization focuses on maintaining the right amount of inventory to meet demand without excess. This process minimizes carrying costs and ensures efficient use of warehouse space. The pivotal aspect of stock optimization is its data-driven approach, which helps determine reorder points and safety stock levels based on historical data and buying patterns. This capability is popular because it not only streamlines operations but also enhances customer satisfaction by ensuring product availability. A unique feature here is the application of algorithms that analyze patterns and suggest optimal stock levels, allowing businesses to tailor their inventory strategies effectively. However, companies must be cautious of over-reliance on technology, as miscalculations in predictive analytics can lead to stockouts or overstocks.
Cycle Counting
Cycle counting involves regularly checking a subset of inventory to ensure accuracy without halting warehouse operations for a full inventory count. It’s a key characteristic of cycle counting that it enhances accuracy while minimizing disruption. Organizations favor this method as it spreads inventory checks across defined periods, leading to more consistent auditing. A unique feature of cycle counting is its flexibility; it can be adjusted according to seasonal demand or various inventory characteristics. Nevertheless, the challenge lies in adequately training staff to perform counts efficiently without causing operational slowdowns.
Order Fulfillment
The order fulfillment process encompasses everything needed to meet customer orders, from picking to shipping. A well-coordinated order fulfillment strategy is fundamental in maintaining customer satisfaction and operational efficiency.
Picking and Packing
The picking and packing functions guide the process of retrieving items from inventory and preparing them for shipment. The key characteristic of this function revolves around efficiency—quick picking translates to faster shipping. WMS often employs various picking methods such as wave picking or batch picking, tailored to maximize productivity. The unique feature here lies in the ability to use mobile devices for scanning and tracking orders in real-time, making it a popular choice among warehouses. On the downside, a poorly organized system may lead to picking errors, which could disrupt entire operations.
Shipping Integration
Shipping integration ensures that outgoing deliveries align well with logistics providers. This function is essential as it enhances visibility from order placement to delivery. The key feature is the capability to manage various carriers seamlessly, allowing for optimized shipping routes and costs. A noteworthy aspect of shipping integration is its ability to automate shipment tracking and notifications, improving communication with customers. However, it can also present challenges; discrepancies between shipment data and inventory records can lead to confusion and inefficiency.
Returns Management
Returns management is a critical component, particularly in sectors with high return rates like e-commerce. Effectively managing returns ensures customer satisfaction and can even turn a potential loss into a growth opportunity. The key aspect of returns management is its focus on streamlining the process to minimize the impact on the warehouse. A distinctive feature is the use of specific workflows that can categorize returns to determine whether items should be restocked, refurbished, or discarded. However, reconciling returns can sometimes complicate accounting and inventory accuracy.
Labor Management
Labor management refers to how a warehouse manages its workforce efficiently. This function is important because it directly impacts productivity and cost control.
Workforce Scheduling
Workforce scheduling focuses on efficiently allocating human resources to correspond with fluctuating demand. Its key characteristic lies in improving productivity while ensuring employee satisfaction. By leveraging WMS to analyze historical workload data, organizations can create schedules that are both efficient and fair. A unique aspect of workforce scheduling is its ability to integrate with employee management systems to streamline shift swaps. Yet, aligning employee availability with optimal business operations can still pose challenges.
Performance Metrics
Using performance metrics is vital for evaluating labor efficiency and ensuring accountability. The key characteristic of this function is the ability to set clear benchmarks and measure individual and team performance. Organizations leverage various KPIs, like order picking rates and accuracy, to drive productivity improvements. A notable feature is the real-time feedback loop that can motivate workers and inform management about efficiency gaps. However, an overemphasis on metrics may lead to unnecessary pressure on employees, affecting morale.
Task Assignment
Task assignment is about efficiently allocating specific jobs to team members. Its significance lies in ensuring that the most suitable personnel are assigned to tasks based on their skills. The key characteristic of task assignment is its focus on optimizing labor resources based on real-time operational needs. A unique benefit is the flexibility it provides in adjusting task allocations quickly to meet sudden changes in workflows. However, if not managed well, it can result in overload for some employees while others may remain under-utilized.
Reporting and Analytics
This function encompasses gathering and analyzing data to facilitate informed decision-making. It’s indispensable for refining warehouse operations through insight-driven strategies.
Operational Insights
Operational insights focus on delivering actionable intelligence regarding warehouse performance. The key aspect of this function is its capacity to transform raw data into understandable reports. This plays a significant role in identifying bottlenecks and inefficiencies in operations. A notable feature is the ability to visualize performance metrics over time, which aids in strategic planning. Yet, without accurate data collection methods, the outcomes can be flawed or misleading.
Forecasting Trends
Forecasting trends involves analyzing data to predict future demands, which is crucial for efficient stock management. The key characteristic of forecasting is its reliance on historical data and market analysis to inform decision-making. Effective forecasting can result in improved inventory turnover and reduced costs. A unique benefit is that it allows organizations to adjust their inventory proactively, rather than reactively. However, reliance on forecasting can backfire if market conditions shift unexpectedly.
Performance Benchmarks
Setting performance benchmarks allows organizations to measure success against established standards and goals. The key aspect of performance benchmarks is fostering continuous improvement by identifying areas for enhancement. Unique to this function is the capacity to share benchmarking data with employees, fostering a culture of accountability. However, care should be taken to ensure benchmarks are realistic and achievable; otherwise, they may lead to discouragement among team members.
The Importance of WMS in Logistics
Warehousing Management Systems (WMS) are critical players in the field of logistics, shaping how businesses manage their operations from the ground up. Their importance goes far beyond simple inventory control. These systems act as the backbone of warehousing, integrating diverse functions and enabling streamlined processes that contribute to overall efficiency in supply chain management. In short, WMS are not just tools; they are strategic assets that help businesses remain competitive in an increasingly complex marketplace.
Enhancing Efficiency
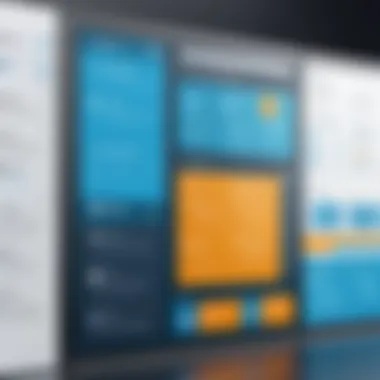
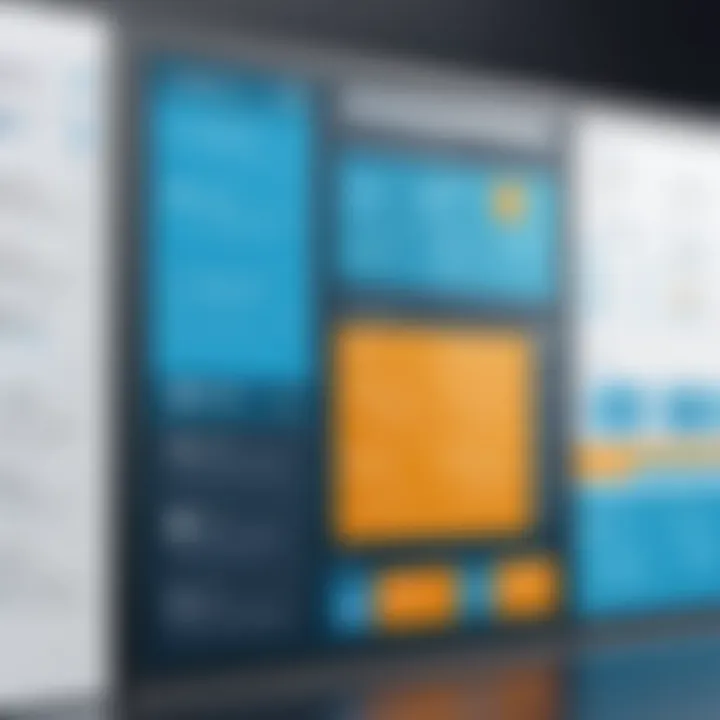
One of the foremost benefits of implementing a WMS is its capacity to enhance efficiency. A well-designed system tackles the bottlenecks often encountered in warehousing, allowing for smooth movement of goods and significantly reducing downtime.
- Automated Processes: Automation plays a huge role here. With features like automated picking and packing, businesses can speed up order fulfillment. For instance, utilizing barcode scanning ensures that the right items are picked accurately and swiftly.
- Optimized Layout: A WMS can also help design the physical layout of a warehouse. By analyzing data on inventory turnover rates, companies can arrange their storage to keep fast-moving items within easy reach, which cuts down on time wasted moving around.
- Real-Time Data: With real-time data tracking, decision-makers can align warehouse operations with demand forecasts. This agility is akin to dancing in rhythm; every move is informed by the music of demand, enhancing overall performance.
Cost Reduction
Cost is always a kingpin driving business decisions, and a WMS can provide substantial cost reduction. Here’s how:
- Labor Costs: By improving task assignment and automating repetitive duties, businesses can minimize labor costs. A reduced need for manual intervention can lead to lower personnel expenses.
- Inventory Holding Costs: Efficient inventory management helps in optimizing stock levels. By analyzing patterns, businesses can keep just enough stock to meet demand without overspending on storage space. This approach is like cooking with just the right amount of spice – too much can ruin the dish, too little can leave it bland.
- Reduced Errors: Errors in order fulfillment can have cascading effects. A WMS limits mistakes that can lead to returns or customer dissatisfaction, which would otherwise incur additional costs.
Improving Accuracy
Accuracy is another pillar where a WMS shines. The impact of a high level of accuracy in warehousing can be game-changing:
- Order Fulfillment Accuracy: By utilizing technology like RFID and barcode scanning, a WMS ensures that the right product goes out to the customer. Less discrepancies mean happier customers, which translates to repeat business.
- Inventory Accuracy: Real-time tracking minimizes discrepancies between physical stock and system records. Regular cycle counting facilitated by a WMS ensures that inventory records are always updated, leading to greater reliability in stock levels.
"A WMS isn't just technology; it’s the lifeblood of operational success in logistics."
- Data Reporting: Advanced analytics features provide insights into performance metrics, highlighting potential inaccuracies in the system. For decision-makers, this means being able to proactively address issues before they snowball.
Key Features to Look for in a WMS
Selecting the right Warehousing Management System (WMS) involves more than just ticking off boxes on a checklist. The key features of a WMS can significantly influence inventory control, order fulfillment speed, and overall operational efficiency within a warehouse environment. Decision makers must understand the unique functions and capabilities that contribute to a system's overall performance.
User Interface and Ease of Use
A user-friendly interface is at the heart of any effective WMS. If the system is overly complicated, it can slow down operations instead of streamlining them. Users should be able to easily navigate through the interface without the need for extensive training. An intuitive layout helps in quick access to important functions like tracking inventory status and managing orders.
Moreover, a well-designed dashboard can visually present critical data, helping warehouse managers make quick, informed decisions. Features that allow personalization can enhance usability even further, enabling users to prioritize the information that matters most to their specific roles.—
Integration Capabilities
Integrating the WMS with other business systems is crucial for a seamless flow of information. The ability to connect different software solutions can enhance data accuracy, reduce manual entry errors, and improve overall efficiency. Here are some specific integration points that stand out:
ERP Integration
Enterprise Resource Planning (ERP) Integration connects a WMS to the broader scope of business operations. This integration is popular because it allows for real-time data updates across different departments— from accounting to sales. A standout feature of ERP integration is its capability to synchronize inventory levels with customer orders automatically, ensuring that stock levels are accurate.
However, the trade-off often lies in complexity. Setting up and maintaining these integrations can be a resource-intensive process but the payoff often offsets the initial challenges. This integration is beneficial for companies looking to create a harmonized business environment.
Third-party Logistics Integration
Third-party Logistics Integration focuses on connecting WMS with external logistical services. This offers flexibility in warehousing and distribution options. A key characteristic here is the capacity for seamless data sharing which fosters collaboration between the warehouse and the logistics provider.
One unique feature of this integration is its ability to generate shipping labels and documentation directly from the WMS, drastically reducing manual involvement. On the downside, dependencies on third-party capabilities might introduce vulnerabilities, especially if the partner service experiences delays or issues.
API Support
API Support is another critical factor for integration capability. It allows for custom connections between the WMS and other applications. A key characteristic of API support is that it offers significant flexibility, allowing for easy future integrations as needed. This adaptability makes it a popular choice as businesses evolve and require additional functionalities.
However, the unique feature that API support provides is the potential for tailored solutions that meet specific business needs. While advantageous, the downside could be that businesses might need specialized technical expertise to effectively utilize APIs, which could add to operational costs.
Scalability and Flexibility
Scalability is essential for any growing business. A WMS must not only handle current demands but also scale to accommodate future growth. Think of it like a good pair of shoes— they shouldn’t just fit well now, but also provide room as you expand your operations. Flexibility goes hand in hand; the ability to customize functionalities based on changing needs can turn a good system into a great one.
Challenges in Implementing WMS
In exploring the complexities of warehousing management systems, it's vital to address the challenges that can arise during their implementation. For decision-makers and IT professionals, understanding these challenges can significantly influence the successful adoption of WMS. Each challenge stems from a combination of factors—ranging from financial considerations to the human element involved in organizational change.
Cost of Implementation
The cost of implementing a warehousing management system can often be a daunting hurdle. It's not merely about purchasing software; one must consider the entire ecosystem involved. Hardware, software licenses, infrastructure changes, and ongoing maintenance all contribute to the total cost.
- Initial Investment: High-quality WMS solutions typically come with a hefty price tag. This upfront expense can deter many organizations from making the leap, especially smaller businesses or startups.
- Hidden Costs: Some costs are easy to overlook, such as system integration, customizations to tailor the software to the specific needs of the warehouse, and the potential need for new hardware.
- Ongoing Expenses: Regular updates and tech support can lead to further expenditures, which can pile on over time.

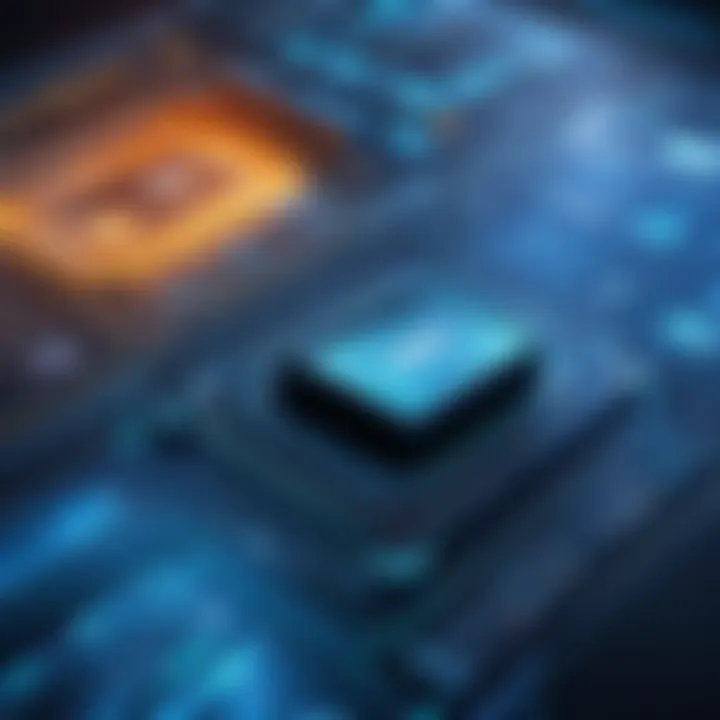
Organizations should conduct a thorough cost-benefit analysis to understand not just the immediate costs but long-term savings through improved efficiency. It’s a bit like fitting a square peg in a round hole—ensuring that the WMS aligns seamlessly with current operations is crucial to avoiding future headaches.
Change Management
Implementing a WMS isn't just a switch to new technology; it’s about altering how people work. Change management plays a pivotal role in ensuring the smooth uptake of a new system. Resistance to change can manifest in various ways:
- Cultural Resistance: Staff may be comfortable operating under existing processes and might view new systems with skepticism. Getting buy-in at all levels is essential to quell fears and foster an ecosystem open to innovation.
- Adaptation Period: Transitioning to WMS means changing workflows. Temporary dips in productivity might occur as employees adapt to the new system. It's crucial to communicate that this is a normal part of the process.
- Involvement of Staff: Engaging workers in the planning stages can mitigate resistance. When employees feel involved, they are more likely to embrace the change.
Ultimately, a detailed communication plan and the support of strong leadership are necessary to guide an organization through this transition while ensuring morale remains intact.
Training Requirements
One cannot overlook the training requirements associated with a new WMS. The success of a system heavily relies on the knowledge and skills of its users.
- Invest in Training: Initial training sessions are crucial and should not just scratch the surface. Companies need to provide comprehensive training that covers functionalities and processes.
- Ongoing Learning: It's not just a one-off event. Continuous training sessions can help staff stay knowledgeable about new features and functionalities. The tech world evolves rapidly, and regular updates ensure that employees remain proficient.
- Assess Training Needs: Each employee's role in the warehouse is different, thus their training should be tailored accordingly. A new hire, for example, might require extensive training, while a tech-savvy employee might only need a brief overview.
Training can often be the bridge that connects frustration with familiarity. As they say, "An ounce of prevention is worth a pound of cure," and investing time and resources into training can pave the way for a smoother transition to an efficient WMS environment.
Future Trends in Warehousing Management Systems
In today’s fast-paced logistics landscape, Warehousing Management Systems (WMS) are evolving at breakneck speed. The future trends in this sector are not just about keeping up with the competitors but also about harnessing technology to enhance operational efficiency and accuracy. Understanding these trends allows businesses to proactively adapt and position themselves favorably in the marketplace. As decision-makers, IT professionals, and entrepreneurs delve into this realm, they must appreciate how emerging trends can be leveraged to streamline operations, cut costs, and significantly improve customer satisfaction.
Automation and Robotics
Automation is no longer a sci-fi concept but a reality that is reshaping warehousing. Companies are increasingly adopting automation to minimize human error and maximize speed. Automated Guided Vehicles (AGVs) and autonomous mobile robots are being used for various tasks, from transporting goods to picking and packing.
The advantages of automation in warehousing include:
- Faster Processing: Automated systems can operate 24/7, drastically reducing the time required for inventory management.
- Cost Efficiency: Although the initial investment is substantial, the pay-off comes through lower labor costs and reduced operational overhead.
- Improved Safety: By delegating hazardous tasks to robots, the risk of injuries decreases significantly.
However, the journey toward automation is fraught with challenges. Integrating automated systems requires careful planning, comprehensive training, and sometimes a cultural shift among employees. Businesses must also consider the long-term implications of potential job displacement.
Artificial Intelligence in WMS
Artificial Intelligence (AI) stands at the forefront of the revolution in warehousing management. Integrating AI into WMS allows for real-time data processing and decision-making. With machine learning algorithms analyzing vast amounts of data, businesses can gain insights that were previously unimaginable.
The benefits of incorporating AI in WMS are manifold:
- Predictive Analytics: AI can forecast demand based on historical sales data, seasonal trends, and market fluctuations, ensuring that businesses maintain optimal inventory levels.
- Enhanced Customer Experience: By anticipating customer needs through data analysis, companies can improve order fulfillment processes and overall service delivery.
- Process Optimization: AI can identify inefficiencies in warehouse operations, suggesting optimizations that can lead to significant time and cost savings.
Despite its advantages, the integration of AI brings questions about data privacy and security. Organizations must ensure compliance with regulations while safeguarding sensitive customer information.
Cloud-based Solutions
Cloud technology is changing the way WMS are implemented and operated. Cloud-based WMS allow for scalability and flexibility, enabling businesses to adjust quickly to changing market demands. The shift to the cloud facilitates easier upgrades, reduces IT infrastructure costs, and enables access to information from anywhere.
Key benefits of cloud-based solutions include:
- Accessibility: Stakeholders can access real-time information across different locations, improving collaboration and decision-making.
- Cost-Effective: The need for extensive on-premises hardware is eliminated, reducing the upfront capital investment.
- Automatic Updates: Cloud providers often manage software updates, ensuring users always have access to the latest features.
However, going cloud comes with its own set of concerns. Organizations need to critically assess data security measures provided by the cloud vendor, along with any potential downtimes in service.
"Future-proofing your warehousing strategy means embracing automation, AI, and cloud solutions. Those lagging in these advancements risk being left behind in an increasingly competitive landscape."
Culmination
As we wrap up our exploration into Warehousing Management Systems (WMS), it's essential to underline the significance of effective warehousing practices in modern logistics. The operations within a warehouse, influenced by the functionality of a WMS, are the heart and soul of supply chain efficiency. An adept WMS offers businesses not just a tool but a comprehensive framework to streamline routine processes. The ebb and flow of goods—from the moment they arrive at the dock to when they're shipped out—can largely depend on the capabilities of the management system in place.
Recap of Key Points
Throughout this article, we've discussed several crucial elements underpinning WMS. Here’s a quick summary that highlights the key takeaways:
- Core Functions: WMS enhances inventory management, order fulfillment, and labor management, supporting vast operations with precision.
- Importance in Logistics: The systems enhance efficiency, reduce costs, and improve accuracy, creating a ripple effect that benefits the entire supply chain.
- Key Features: User friendliness, integration capabilities, and scalability are non-negotiable attributes that should be prioritized when choosing a WMS.
- Challenges: Recognizing the hurdles during implementation, such as costs and change management, can prepare organizations to face them head-on.
- Future Trends: Keeping an eye on advancements in automation, AI, and cloud technology will enable businesses to adapt and thrive in a competitive environment.
This synthesis of information is vital for decision-makers who are investing time and resources into optimizing their warehousing processes.
Final Thoughts on WMS
At the end of the day, the choice of a WMS can make or break a warehousing operation. In a world where efficiency is king, understanding the nuances of these systems is not just beneficial; it's crucial. Organizations need to approach their WMS selection and management with a strategic lens, taking into account their specific needs and operational intricacies.
"The right WMS is like a well-oiled machine—it not only saves time but also enhances the accuracy of every operation it touches."
As we stand on the brink of further technological advancements, the demand for responsive, adaptable warehousing systems will only increase. An effective WMS may very well serve as the bridge, connecting various parts of the supply chain into a seamless operation. Those who embrace this complexity with informed strategies will likely see the fruits of their labor reflected in operational excellence and customer satisfaction.