Microsoft Manufacturing Software: Comprehensive Insights
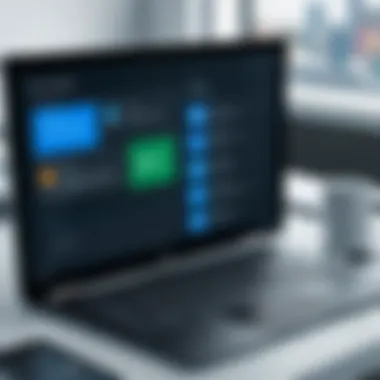
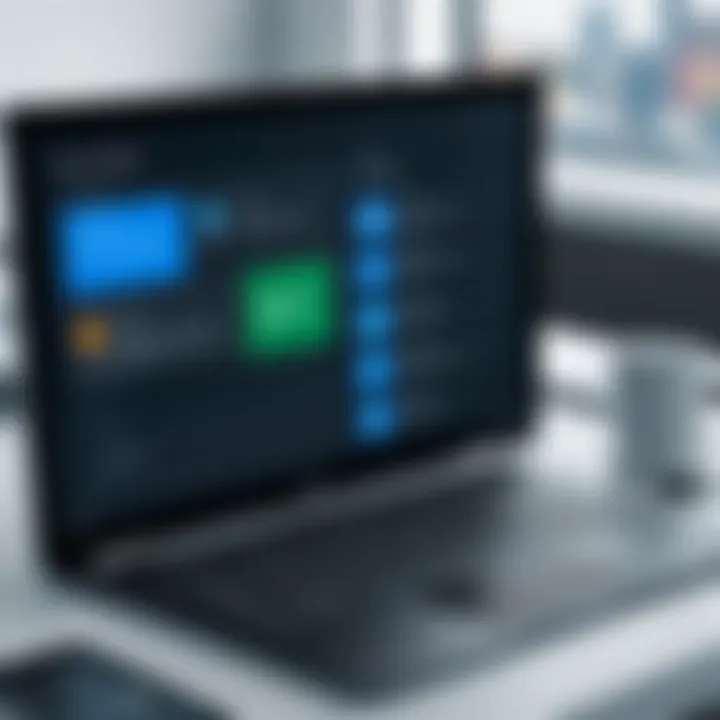
Intro
In the rapidly evolving landscape of manufacturing, staying ahead demands adaptability and innovation. Microsoft manufacturing software serves as a pivotal player for businesses seeking to refine their operations. This software does not merely facilitate processes; it actively transforms how entities design, produce, and manage their product flows. With the integration of advanced technologies bubbling up, like artificial intelligence and the Internet of Things, the scope and efficiency of manufacturing software are unprecedented. Hence, as decision-makers and IT professionals delve into this sector, understanding what Microsoft brings to the table is crucial.
Industry Overview
The manufacturing sector is undergoing significant change. Companies are migrating from traditional methods toward smarter, data-driven approaches. Microsoft’s focus on manufacturing software is ambitious—aiming to empower businesses with tools that drive productivity.
Current Trends in the Industry-specific Software Market
- Digital Transformation: Many firms are racing to digitize their practices, seeking software that bridges physical and digital realms.
- Automation: Increased reliance on automated processes is becoming the norm, where manual labor shifts towards machine operations.
- Customization: Customers now expect personalized solutions rather than one-size-fits-all programs, leading to a rise in bespoke software packages.
Key Challenges Faced by Buyers in the Industry
In the quest for suitable software, companies encounter various hurdles:
- Integration Difficulties: Existing systems may not mesh well with new applications, creating friction during upgrades.
- Cost Concerns: Balancing cost with functionality presents a quandary. Budgets often dictate choices, but compromise can lead to inefficiencies.
- User Resistance: Employees accustomed to familiar systems might resist adopting new software, affecting overall buy-in.
Emerging Technologies Impacting the Industry
Incorporating technologies such as:
- IoT: Devices linking to the network to provide real-time data, improving operational oversight.
- AI: Leveraging algorithms to enhance predictive maintenance and analytics, enabling better decision-making.
- Cloud Computing: Remote access to systems is becoming vital, offering flexibility and scalability without hefty investments in infrastructure.
Top Software Options
When it comes to manufacturing solutions, several key players are at the forefront. Below, a snapshot comparison can help elucidate the landscape.
Review of Leading Software Providers in the Industry
- Microsoft Dynamics 365: Comprehensive tool offering Enterprise Resource Planning and Customer Relationship Management, tailored for manufacturing.
- SAP S/4HANA: Robust platform that emphasizes data-driven management and agile operational flows.
- Oracle NetSuite: Cloud-based solution tailored to various industries, including manufacturing, focusing on automation and real-time analytics.
Feature Comparison of Top Software Solutions
Each software solution boasts unique features:
- Microsoft Dynamics 365: Integration with other Microsoft services, allowing seamless collaboration.
- SAP S/4HANA: Known for its native machine learning capabilities that enhance forecasting.
- Oracle NetSuite: Offers customizable dashboards to provide users with a tailored view of their metrics.
Pricing Structures of Different Software Options
Cost structures also vary significantly. For instance:
- Microsoft Dynamics 365 generally offers subscription-based pricing, appealing for businesses at different scales.
- SAP S/4HANA may require initial heavy investment but emphasizes long-term value through integrated systems.
- Oracle NetSuite often has tiered pricing based on required features and number of users.
Selection Criteria
Navigating through software choices can feel like finding a needle in a haystack. A few critical factors warrant consideration:
Important Factors to Consider When Choosing Software
- Compatibility: Ensuring new software can synchronize with current systems can save time and headaches.
- Scalability: Evaluate if the tool can grow with your business, accommodating future needs without forcing costly replacements.
- Support and Maintenance: Reliable after-sales support can make or break the experience post-implementation.
Common Mistakes to Avoid During the Selection Process
Navigation errors that might leave one in a bind include:
- Not thoroughly assessing the actual needs of the business before investing in software.
- Overlooking the importance of user feedback in the selection process.
- Ignoring the total cost of ownership, which can spiral beyond initial purchase price.
How to Determine the Right Fit for Your Business Needs
Alignment between software capabilities and organizational objectives is essential. Conducting needs assessments and involving relevant stakeholders can sharpen the selection process, sharpening focus on what really matters.
Implementation Strategies
Bringing a new software solution into play requires thoughtful strategies.
Best Practices for Smooth Implementation of Software Solutions
- Staging: Rolling out the software in phases may reduce overwhelm and allow for troubleshooting along the way.
- Stakeholder Engagement: Keeping all parties informed fosters a culture of collaboration.
- Milestone Tracking: Setting clear goals ensures the project stays on track and aligned with business objectives.
Integration with Existing Systems and Processes
Seamless integration is non-negotiable. Setting up API connections for data interchange can streamline workflows, allowing for fluid operation transitions.
Training and Support Resources for Successful Deployment
Robust training resources are paramount. This can include online tutorials, workshops, or on-site training sessions that cater to different learning styles, ensuring everyone is on the same page.
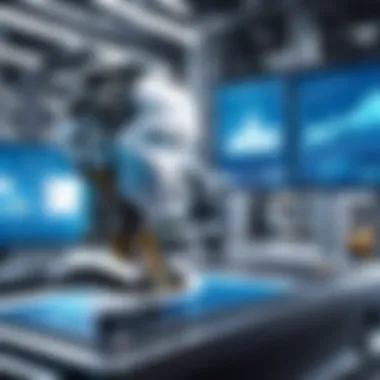

Future Trends
As manufacturing continues its evolution, several trends are poised to shape the industry landscape.
Predictions for the Future of the Industry-specific Software Landscape
- Greater Automation: Expect systems to take on even more complex tasks without human intervention.
- Data-Driven Insights: Software that can mine data for actionable insights will become a staple.
Upcoming Technologies Shaping the Industry
- AR/VR: Augmented Reality and Virtual Reality tools are expected to play a role in training and operational excellence.
- Blockchain: Finally, employing blockchain technology could enhance security and authenticity in manufacturing processes.
Recommendations for Future-Proofing Your Technology Stack
Investing in adaptable solutions that allow for periodic updates will be essential. Keeping an eye on technological trends will assist decision-makers in anticipating change and steering their companies in the right direction.
The pivotal takeaway is that manufacturers must adapt quickly. Those who fail to recognize the change stand at risk of being outpaced by competitors.
In summary, as we dive deeper into Microsoft manufacturing software, the insights provided here emphasize not just its immediate benefits but its long-term implications in an industry that is constantly transforming.
Intro to Manufacturing Software
Manufacturing software is not just a tool; it’s an essential component that revolutionizes how industries operate today. It serves as the backbone for managing processes, resources, and data efficiently. In this ever-evolving landscape of manufacturing, the integration of technology has shifted from being a luxury to a necessity. The complexities of modern manufacturing demand solutions that can streamline operations, reduce waste, and enhance decision-making capabilities—this is where software steps in.
The importance of software in the manufacturing sector can’t be overstated. Not only does it help in automating routine tasks, but it also provides valuable insights that can inform better strategic decisions. For example, think about a production line where machines need to be monitored in real time. Software can provide alerts for maintenance, optimize scheduling, and track inventory levels—all while minimizing human error.
There is substantial software available today, tailored specifically to meet diverse manufacturing needs. The benefits are clear: improved operational efficiency, lower costs, and ultimately, enhanced competitiveness in the market.
The Evolution of Manufacturing Software
Manufacturing software has come a long way from the early computerized systems that merely tracked inventory levels or produced rudimentary production schedules. Initially, these programs had limited functionalities and were often cumbersome to navigate. However, as technology progressed, software solutions evolved into comprehensive suite solutions.
With the dawn of concepts like the Industrial Internet of Things (IIoT) and big data analytics, modern manufacturing software now incorporates these cutting-edge technologies, influencing everything from inventory management to predictive maintenance.
Several pivotal developments marked the evolution:
- Early Automation: Initial software was primarily focused on automating repetitive tasks, such as order processing.
- Integration Capabilities: The introduction of ERP (Enterprise Resource Planning) systems allowed different functions within manufacturing to share data seamlessly.
- Real-Time Monitoring: Today’s software can aggregate data from various sources in real time, making it easier to make informed decisions on-the-fly.
Importance of Software in Modern Manufacturing
The relevance of software in the contemporary manufacturing landscape cannot be overstated. It acts not just as a facilitator but as a strategic ally. Consider the following points:
- Enhanced Data Management: Manufacturers are inundated with data—from supply chain logistics to customer feedback. Software systems provide the tools needed to manage this data effectively.
- Improved Productivity: Integration of automated processes and data-driven decision making leads to higher productivity levels. This results in products being manufactured faster and at a lower cost.
- Customization and Flexibility: Because every manufacturing operation is unique, custom software solutions have become essential. Companies can tailor these solutions to meet specific business needs, allowing for greater adaptability.
- Compliance and Quality Control: Regulatory standards are stringent in manufacturing. Software helps organizations maintain compliance and improve quality control through constant monitoring and reporting.
"In the age of digital transformation, manufacturing software is less about automation and more about intelligence."
In closing, as manufacturing continues to progress, software will be at the forefront of these advancements, shaping the way industries function and evolve. Understanding its evolution and importance lays the groundwork for appreciating the specific solutions that brands like Microsoft offer.
Microsoft’s Manufacturing Software Solutions
The significance of Microsoft’s manufacturing software solutions transcends mere functionality. These tools represent a paradigm shift in how manufacturing businesses operate, making processes smoother and more integrated. In an era where precision and efficiency reign supreme, Microsoft’s offerings empower organizations to harness data, optimize workflows, and enhance decision-making at every level. In this detailed examination, we’ll dive into two cornerstone solutions: Microsoft Dynamics 365 and Microsoft Power BI, showcasing their roles in transforming manufacturing practices today.
Microsoft Dynamics for Manufacturing
Overview of Dynamics
Microsoft Dynamics 365 serves as a robust platform that hosts a wide array of applications tailored for manufacturing. This software suite is particularly notable for its ability to combine enterprise resource planning (ERP) capabilities with customer relationship management (CRM). One of its most striking features is its modularity, allowing manufacturers to adopt only those modules that suit their immediate needs while giving them the flexibility to scale as their business evolves.
A critical characteristic of Dynamics 365 is its cloud-native architecture, which facilitates seamless updates and integrations. This ongoing enhancement means businesses have access to the latest tools without the headache of traditional software upgrade cycles.
Unique to Dynamics 365 is its AI-driven insights, which leverage machine learning to provide predictive analytics. This enables manufacturers to anticipate trends and make proactive adjustments rather than reactive changes. Still, challenges exist, such as the initial learning curve and integration complexities with existing systems.
Key Features for Manufacturers
Key features of Dynamics 365 set it apart in the market. One notable aspect is its real-time data synchronization, which ensures that information across various departments is consistent and up-to-date. This capability addresses the common issue of siloed information, fostering a more holistic approach to operational management.
Additionally, the software’s user experience stands out due to its intuitive interface. Users can navigate through it without needing extensive training, thus enhancing overall productivity. Nonetheless, it's worth mentioning that achieving full utilization of its capabilities can require an investment of time and resources, particularly in larger organizations.
Industry-Specific Solutions
Diving deeper into industry-specific solutions, Microsoft Dynamics 365 excels in customizing its offerings to meet specific sector demands. For instance, solutions tailored for automotive or aerospace manufacturing incorporate unique compliance and quality control features that address stringent regulatory requirements. This adaptability not only boosts operational performance but also aligns closely with evolving industry standards.
Furthermore, these tailored modules integrate seamlessly with core applications to provide a cohesive experience across different functions. The dual-edged sword here, however, lies in the necessity for ongoing management of these tailored solutions, requiring skilled personnel to ensure optimal performance as business needs grow.
Microsoft Power BI for Manufacturing Analytics
Data-Driven Decision Making
In the realm of manufacturing analytics, Microsoft Power BI spearheads the movement towards data-driven decision making. This powerful tool transforms raw data into actionable insights, allowing organizations to identify patterns and trends. At its core, Power BI’s visualization capabilities are particularly compelling, enabling users to create compelling reports that can surface critical operational insights in a user-friendly format.
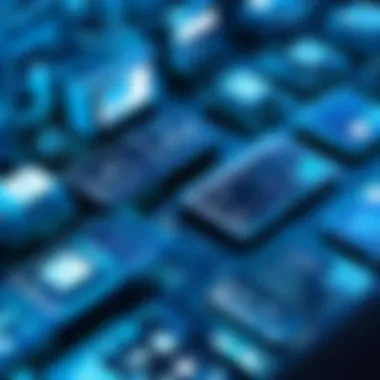
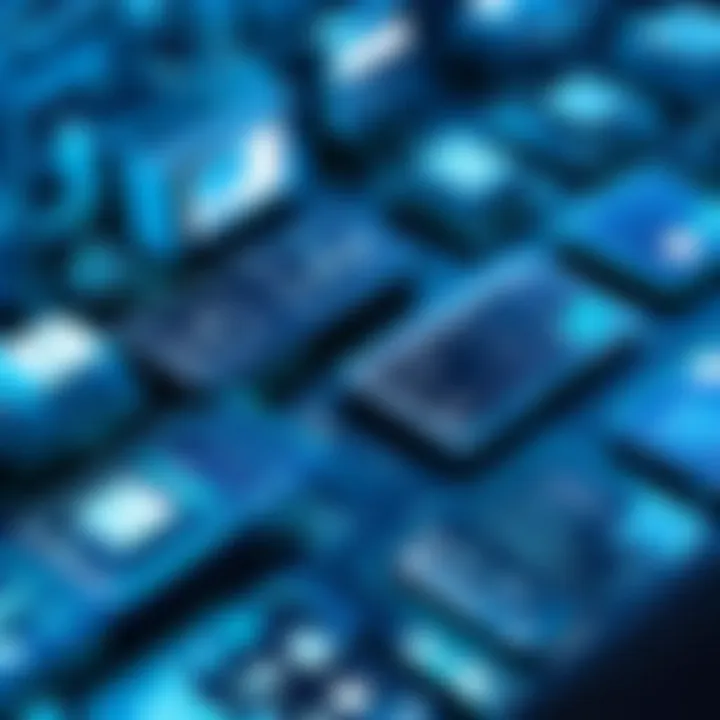
Moreover, its integration with existing data sources reinforces its value. Manufacturers can pull together disparate data from production lines, supply chains, and customer feedback, thus fostering a more rounded understanding of their operations. However, a potential downside is ensuring data accuracy across multiple sources, as poor data can lead to misguided decisions.
Integration with Manufacturing Data
Power BI shines in its capability to integrate seamlessly with various manufacturing data systems, like ERP systems or even legacy platforms. This ensures that manufacturing firms can harness comprehensive datasets for their analytical needs, leading to well-rounded conclusions.
The real brilliance lies in its ability to automate data refreshes, keeping reports current without manual intervention. Yet, companies must be mindful of the evolving landscape of data privacy laws, which can affect how they aggregate and utilize data.
Case Studies Demonstrating Impact
Delving into case studies highlighting Power BI’s impact reveals its transformative potential. For instance, a manufacturing firm that faced recurrent inefficiencies improved their operations dramatically after implementing Power BI for their analytics. The insights derived led to reducing downtime by over 20%, demonstrating a clear return on investment.
These examples underscore Power BI's ability to turn complex datasets into intuitive visuals that aid strategic decision-making. Yet, capturing and synthesizing data accurately remains a challenge that firms must proactively manage.
Through exploring these solutions, one gains a clearer picture of how Microsoft can effectively shape the future of manufacturing, bridging gaps between technology and ongoing operational excellence.
Key Features of Microsoft Manufacturing Software
In the contemporary manufacturing arena, having astute software solutions is no longer just a luxury; it’s a necessity. Microsoft’s manufacturing software encompasses a variety of features that empower businesses to optimize operations, ensure competitive edge, and respond adeptly to market demands. Understanding these key features can illuminate how the software not only streamlines processes but also aligns with broader strategic goals, making it paramount for decision-makers and IT professionals alike.
Real-Time Data Management
The value of real-time data management cannot be overstated in today’s fast-paced environment. Manufacturers must possess the ability to access and analyze information as it comes in. With Microsoft’s tools, organizations can track everything from inventory levels to production rates instantaneously. This immediacy allows for better decision-making, as potential bottlenecks can be identified and addressed before they escalate.
Additionally, having a pulse on current data can lead to:
- Enhanced Operational Efficiency: With real-time insights, firms can adjust schedules and resources swiftly, maximizing output.
- Informed Forecasting: Access to accurate data enables a more reliable prediction of future demands, thus reducing the risk of overproducing or underproducing goods.
"In the world of manufacturing, the only constant is change. Real-time data management equips businesses to adapt promptly."
Advanced Supply Chain Management
In today’s interconnected global economy, advanced supply chain management tools are indispensable. Microsoft’s software streamlines communication across different tiers of the supply chain, fostering collaboration among suppliers, manufacturers, and distributors. This ensures everyone involved is on the same page.
Key aspects of the advanced supply chain management functionalities include:
- Visibility Across the Chain: Organizations can track shipments and inventories at various stages, reducing instances of losses and delays.
- Risk Management: By utilizing predictive analytics, businesses can foresee potential disruptions and devise strategies to mitigate risks.
- Cost Reduction: Efficient supply chain operations can help in cutting down waste and lowering operational costs.
Adopting these advanced features not only brings about better efficiency but can significantly elevate the bottom line as well.
Integration with IoT and Automation
The integration of Internet of Things (IoT) technology and automation into manufacturing processes is reshaping the industry landscape. With Microsoft’s systems, manufacturers can connect machines, sensors, and devices, enabling a seamless flow of information. This integration leads to a cyber-physical system where data collected from IoT devices informs and enhances automation efforts.
Benefits of integrating IoT and automation include:
- Improved Maintenance: Real-time data allows for predictive maintenance, helping reduce downtime caused by equipment failures.
- Productivity Boost: Automated processes relieve human workers from mundane tasks, allowing them to focus on higher-value activities.
- Enhanced Quality Control: Constant monitoring of processes ensures that production standards are met consistently, leading to better product quality.
Embracing these modern technologies indeed presents a significant opportunity for manufacturers to not only innovate but also to stay ahead of the curve in a competitive marketplace.
Implementation Strategies
Implementing manufacturing software isn't just a technical shift; it's a change that can fundamentally redesign how a business operates. Understanding the importance of implementation strategies can’t be understated. Implementation strategies serve as a roadmap, guiding businesses through the complexities of transitioning to Microsoft manufacturing software. The right strategy can crystalize a company's goals and make the intricate journey smoother, effectively enhancing operational efficiency and productivity.
Some specific elements to prioritize include a genuine assessment of business needs, customization that aligns with those needs, and a robust training and change management plan. Each component plays a pivotal role in establishing a seamless integration with existing processes while minimizing disruption. The benefits? Improved employee engagement, smoother transitions, and more effective use of resources.
Assessing Business Needs
Before diving headfirst into implementation, a thorough assessment of business needs is essential. Companies should take a step back and evaluate their current operations and the gaps present. This requires serious reflection on several factors:
- Identify pain points: Are there recurring issues in production, inventory management, or other areas? Knowing what needs fixing is priority number one.
- Gather input from stakeholders: Engaging team members at various levels of the organization helps in acquiring diverse insights that will inform better decisions. Their perspectives can reveal crucial needs that higher management might overlook.
- Define specific objectives: Clearly outlining what the implementation needs to achieve will help align expectations across the board. Goals could range from reducing lead times to improving data visibility.
That said, this isn't merely about identifying challenges; it's also about recognizing strengths and building upon them. It's crucial to document these findings explicitly to create a solid foundation moving forward.
Customizing Software Solutions
Not all businesses are created equal. Hence, the right software must be tailored to fit like a glove. Customization is where companies can truly add value and ensure the software meets the specificities of their operations. This involves:
- Modifying modules and features: Microsoft’s solutions offer numerous options that can be tweaked to suit unique processes. Businesses should analyze which features cater to their operational demands effectively.
- Integration with existing systems: An effective implementation strategy involves ensuring that new software seamlessly interfaces with existing systems. This can bolster efficiency by eliminating data silos.
- User input in design: Including feedback from users who will engage with the software daily can lead to better configurations. User-friendly interfaces increase adoption rates and enhance productivity from the get-go.
It’s beneficial to maintain an open dialogue throughout the customization process to ensure that everyone is on the same page.
Training and Change Management
The hardest part of introducing new software can often be helping staff adapt. Change management goes hand-in-hand with training, like a partner dance where one influences the other's rhythm. Effective strategies in this area encompass:
- Developing a tailored training program: As staff will interact daily with the software, training must cater specifically to various roles. Hands-on workshops, online modules, or even shadowing can facilitate this.
- Encouraging a culture of adaptability: Employees must view the software not just as another tool, but as a valuable asset. Leaders should champion this mindset to ease the transition.
- Continuous support post-implementation: Implementing software is just the first step. Establishing channels for support—be it through internal IT help or external consultation—ensures that help is at hand when questions arise.
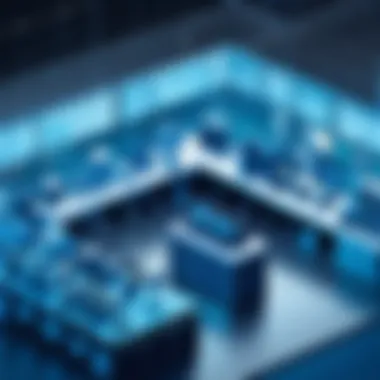
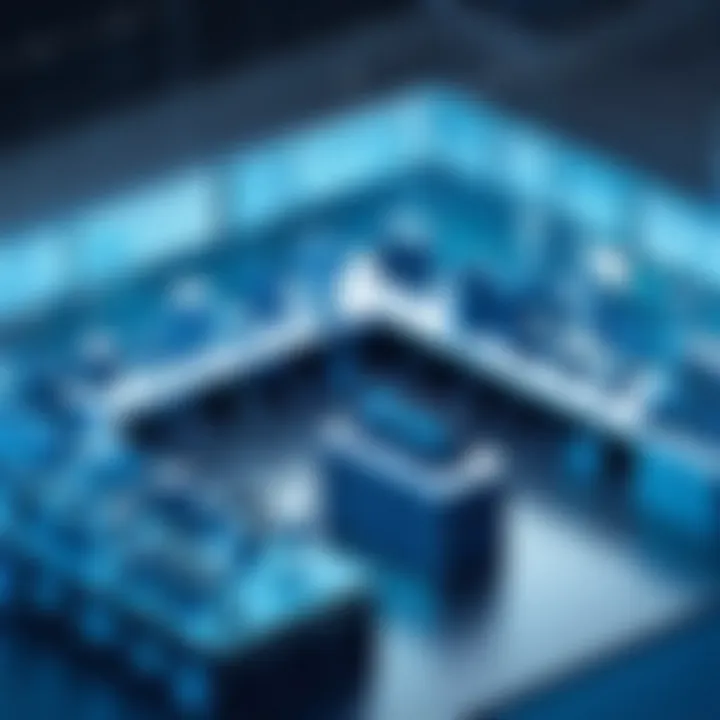
Effective training and change management can transform apprehension into enthusiastic adoption, unlocking the true potential of Microsoft manufacturing software.
Case Studies: Success Stories
Understanding real-world applications of Microsoft’s manufacturing software is essential. The case studies of successful implementations provide tangible evidence of how these solutions can transform businesses. They highlight specific challenges faced by organizations, the unique strategies employed to meet these challenges, and the resultant benefits realized over time. By exploring these success stories, decision-makers can gain insights into effective application, potential pitfalls, and the virtues of technological integration in manufacturing processes.
Global Manufacturing Corporation
Challenges Faced
Global Manufacturing Corporation encountered a myriad of complexities in its operations, particularly in supply chain visibility and production inefficiencies. The need for real-time data was paramount, as delays in information flow led to costly production downtimes. A fragmented IT landscape made it difficult to consolidate information from various departments, which slowed decision-making processes. These characteristics rendered their current systems far from adequate. This scenario firmly emphasizes the importance of aligning technology with operational needs to improve efficiency and effectiveness.
Solutions Implemented
In response, the corporation implemented Microsoft Dynamics 365, customizing the system to address their specific needs. This move facilitated better data management and integrated various functions, from inventory control to production planning. A crucial aspect of the solution was its ability to provide real-time analytics, allowing decision-makers to quickly understand production trends and supply chain dynamics. This seamless integration among departments painted a clearer picture of operations and boosted control over critical processes, paving the way for operational excellence.
Results Achieved
The results were striking. The corporation reported a 30% reduction in production downtimes within the first year of implementation. Key performance indicators improved markedly, supported by stronger communication between departments. The company's bottom line saw a significant bounce-back, driven largely by reduced operational costs and enhanced productivity. This unique feature of measurable outcomes showcases how effective software implementation not only resolves prevailing challenges but also propels businesses toward growth.
Local Artisan Workshops
Unique Needs Addressed
Local Artisan Workshops represented a vastly different landscape than larger corporations. Their unique needs revolved around personalization and flexibility in production. Often, they create bespoke products that require a delicate balance of creativity and efficiency. Hence, they sought customized solutions that could adapt to small batch runs while managing inventory efficiently. This aspect highlighted the software’s flexibility, making it an attractive choice for smaller-scale operations.
Application of Software
The implementation of Microsoft Power BI allowed these workshops to analyze customer preferences and inventory levels effectively. Tailored dashboards facilitated visual insights, helping artisans understand market trends and optimize production without complicating workflows. This intuitive application provided a direct connection between customer behavior and production decisions, reflecting a significant advantage in agile manufacturing practices.
Impact on Business Operations
The impact on business operations was profound. Artisans reported greater satisfaction in fulfilling custom orders while managing resources more strategically. The ability to make data-driven decisions led to higher customer loyalty, as products could be tailored to specific demands. Moreover, this integration fostered an environment where innovation could thrive, augmenting craft and technology alike, ultimately reshaping the artisan landscape.
By analyzing these success stories, one can appreciate how Microsoft manufacturing software has not only tackled existing problems but has also opened doors to enhanced efficiency, creativity, and operational success.
The Future of Manufacturing Software
The realm of manufacturing software is in a state of flux, adapting to the rapid pace of technological advancements and shifting consumer demands. As industries embrace digital transformation, understanding the future of manufacturing software becomes crucial for staying competitive. This perspective helps to grasp how next-generation tools not only streamline processes but also enable innovative solutions tailored to modern challenges.
Trends in Manufacturing Technology
The landscape of manufacturing technology is changing before our eyes. Here are some key trends:
- Increased Automation: Automation isn’t just a buzzword. It's integrating itself at every level, from assembly lines to supply chain logistics. Robots are now commonplace, handling everything from packing to inspections. The aim? Minimizing human error and improving efficiency.
- Advanced Data Analytics: With tools like Microsoft Power BI, manufacturers analyze extensive data sets to glean insights. Harnessing data helps in forecasting demand, optimizing inventory, and enhancing product quality. Industry players can make informed decisions fast, rather than getting caught in the web of guesswork.
- Cloud Computing Adoption: Companies are shifting towards cloud solutions not just for storage, but for operational flexibility. This shift allows real-time collaboration across various sites and devices. Additionally, it supports remote monitoring which has emerged as essential during unexpected global disruptions.
These trends demonstrate a clear roadmap towards a technologically intensive future, paving the way for smarter manufacturing processes.
The Role of Artificial Intelligence
Artificial intelligence is often touted as the game changer in manufacturing. Here’s why:
- Predictive Maintenance: A key advantage of AI lies in its ability to predict when equipment will fail, reducing unplanned downtimes. This is a fantastic way to save costs and time. By employing machine learning algorithms, systems learn from past data and predict future outcomes.
- Enhanced Quality Control: AI tools can analyze products in real-time, detecting defects with a level of scrutiny that surpasses human capability. Such precision leads to better products and fewer returns, thus increasing customer satisfaction.
- Streamlined Operations: From supply chain logistics to inventory management, AI can optimize numerous processes. It allows for better scheduling, ensuring that every component arrives just in time to keep production flowing smoothly.
Artificial intelligence not only enhances manufacturing efficiency but also sparks innovation that propels companies forward into previously uncharted territories.
Sustainability and Ethical Manufacturing
In today's world, sustainability is no longer an afterthought. The future of manufacturing software must encompass this essential aspect for several reasons:
- Resource Management: Advanced software solutions help companies manage their resources more wisely, reducing waste and optimizing inputs. This can mean less energy consumed and fewer raw materials thrown away, leading to a greener footprint.
- Supply Chain Transparency: Today's consumers demand transparency. Implementing software that tracks materials from origin to final product can enhance trust and demonstrate commitment to ethical sourcing and sustainability.
- Regulatory Compliance: With regulations around environmental impact tightening, having robust software helps manufacturers stay compliant. It can automatically update about changing regulations, ensuring it’s always one step ahead.
The growing awareness of environmental issues necessitates an approach that intertwines operational excellence with a commitment to ethical practices, setting the stage for a sustainable future.
"The future is not something we enter. The future is something we create."
Culmination and Recommendations
In wrapping up the exploration of Microsoft manufacturing software, it becomes clear that this technology serves as a cornerstone in modernizing industry operations. The integration of various software solutions not only streamlines processes but also enhances productivity, making it an invaluable asset for manufacturers around the globe. By understanding and harnessing the full capabilities of these tools, decision-makers can significantly influence their organizations’ performance.
Summary of Key Points
As we look back at the insights shared throughout this article, several key points emerge:
- Diverse Solutions: Microsoft offers a range of tailored solutions like Dynamics 365 and Power BI specifically designed for manufacturing contexts. These tools facilitate data management, enhance analytics, and provide industry-specific functionalities.
- Advanced Features: Real-time data management, the capability for advanced supply chain oversight, and smooth integration with IoT devices are some of the standout features that empower manufacturers.
- Implementation Strategies: Careful planning during the implementation phase, from assessing business needs to customizing software solutions, is essential. Ignoring this step can lead to wasted resources and unfulfilled potential.
- Case Studies: Success stories from companies like Global Manufacturing Corporation and local artisan workshops underline the software's adaptability and tangible results—from operational efficiency to increased competitiveness.
- Future Outlook: The role of artificial intelligence, sustainable practices, and adherence to ethical manufacturing cannot be overstated. Investing in these areas will likely shape the future landscape of manufacturing.
Final Thoughts on Microsoft Manufacturing Software
Microsoft’s approach to manufacturing software is not just about keeping pace with the industry; it’s about setting the standard for what’s possible. By leveraging advanced technology, manufacturers can improve their processes and adapt to the dynamic market conditions.
As organizations consider their next steps, they should focus on:
- Continuous Learning: Embrace an ongoing process of learning to stay updated with technological advancements.
- Collaborative Culture: Foster a work environment that encourages collaboration across departments; integrating software solutions effectively often requires a team effort.
- Stakeholder Engagement: Engage with all stakeholders, including employees, to ensure that the implementation of new tools aligns with their expertise and needs.
Ultimately, manufacturers that make informed and strategic decisions regarding their software investments will find themselves not only surviving but thriving in this rapidly evolving industry. The path is clear: to ignore these emerging technologies would be to risk falling behind, so embracing Microsoft’s innovative solutions could lead to groundbreaking advancements in production capabilities.