Traksys MES: Boosting Manufacturing Efficiency and Quality
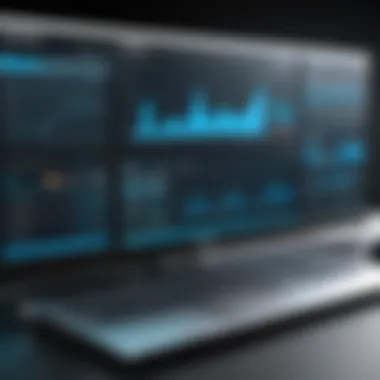
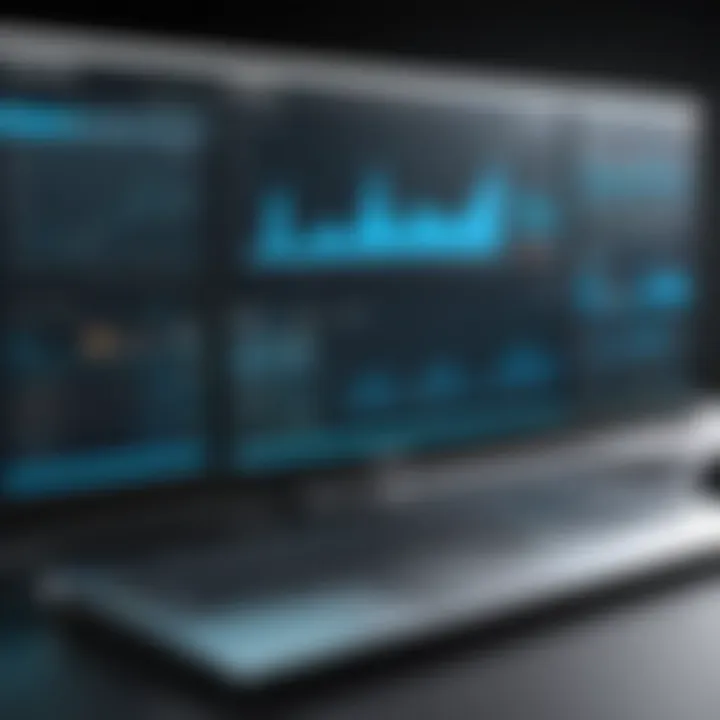
Intro
In today’s fast-paced manufacturing environment, efficiency is not just a bonus—it is essential for survival. The emergence of sophisticated technologies, such as the Traksys MES (Manufacturing Execution System), has revolutionized how manufacturing operations function. Businesses are often caught in a whirlwind of rising operational costs, quality control issues, and the pressure to adapt to rapidly changing market demands.
Traksys MES stands at the forefront, acting as a bridge between the shop floor and management, ensuring that data flows seamlessly across all levels of operations. This connection cultivates a more streamlined process, ultimately enhancing productivity and output quality. In this discussion, we will explore how Traksys MES is reshaping the landscape of manufacturing efficiency, tackling industry-specific challenges, and offering solutions that cater to unique operational needs.
As we dive deeper, we will navigate through an overview of the manufacturing industry, recent trends influencing technology adoption, key challenges buyers face, and practical implementation strategies using Traksys MES. This comprehensive guide aims to equip decision-makers and IT professionals with fundamental knowledge necessary for informed choices in software selection and deployment tailored to fit specific business contexts.
Industry Overview
As manufacturing continues to evolve, understanding the current climate of the industry is vital. The demand for technological integration has accelerated, with many businesses recognizing the necessity for advanced software solutions to optimize production processes. The manufacturing execution system market is seeing a significant uptick as companies strive to maintain a competitive edge—especially in an age where customer expectations are high.
Current Trends in the Industry-specific Software Market
The landscape of manufacturing software is shifting rapidly. We see trends such as:
- Real-time data analytics: Manufacturers are focusing on harnessing data insights to make quicker, educated decisions.
- Cloud-based solutions: Many organizations are moving to cloud-enabled systems for cost-effectiveness and improved accessibility.
- Automation and AI: The integration of automation technologies and artificial intelligence is reshaping traditional manufacturing practices, allowing for smarter production strategies.
These trends highlight how manufacturers are not merely adopting technology but are fundamentally changing the way they operate, guaranteeing agility and responsiveness.
Key Challenges Faced by Buyers in the Industry
While the need for advanced manufacturing solutions is clear, buyers often stumble upon several roadblocks:
- Cost concerns: Investment in robust software systems can be hefty, leading to hesitation amongst decision-makers.
- Integration issues: Many companies struggle with harmonizing new systems with their existing infrastructure, raising compatibility concerns.
- Change management: Employees may resist adopting new technologies, impacting overall effectiveness during the transition phase.
It’s crucial for stakeholders to recognize these challenges upfront and align their strategies accordingly to reduce friction during the adoption process.
Emerging Technologies Impacting the Industry
Just as trends shape the industry, emerging technologies are also playing a pivotal role. Some key influences include:
- Industry 4.0: The fourth industrial revolution emphasizes interconnectedness through IoT devices, fostering a more proactive manufacturing environment.
- Blockchain: Ensuring transparency and traceability in supply chains, blockchain technology can enhance trust among stakeholders.
- Augmented and Virtual Reality (AR/VR): These technologies provide immersive training experiences for employees, improving skill acquisition without the traditional risks associated with hands-on training.
Understanding these emerging technologies and their implications can be a game-changer for decision-makers looking to adopt systems like Traksys MES.
As we progress further into the nuances of Traksys MES, it will be essential to highlight its specific features, benefits, and the strategic importance these tools hold in enhancing not just individual operations but the overall manufacturing ecosystem.
Understanding Traksys MES
In the realm of manufacturing, understanding the intricacies of a Manufacturing Execution System (MES) like Traksys is crucial. MES serves as the backbone of operational efficiency, bridging the gap between enterprise resource planning and the shop floor. As production becomes increasingly complex, the necessity for robust solutions that optimize performance cannot be overstated. Traksys MES brings to the table a range of functionalities designed not just to monitor production but also to enhance it at every turn.
Definition and Purpose
Traksys MES can be defined as a system that facilitates the management of manufacturing processes on the shop floor. Unlike traditional methods that rely heavily on manual inputs and disparate processes, Traksys integrates various manufacturing functions under one platform, allowing for seamless communications and operations.
The primary purpose of Traksys MES is to enhance visibility throughout the production cycle. This means tracking everything from resource allocation to product quality in real-time. The benefit here is twofold: not only does it help in identifying inefficiencies, but it also enables swift corrective actions, helping to stave off larger issues down the line. Embracing a MES like Traksys equips organizations with the tools necessary to stay competitive, especially in sectors where margins are thin and customer demands are high.
Key Components of Traksys MES
When dissecting the architecture of Traksys MES, several key components stand out that contribute to its effectiveness:
- Real-time Data Collection: Traksys facilitates continuous data flow from various machines and systems, ensuring that decision-makers have access to the most current information.
- Production Scheduling: This component allows for dynamic scheduling based on available resources and real-time demand, making it easier to adapt to sudden changes in the production line.
- Quality Management: Integrated tools within Traksys help in monitoring product quality throughout the production process, enabling proactive quality control measures. By identifying potential defects before they reach the consumer, manufacturers can significantly enhance customer satisfaction.
- Integration Capabilities: Traksys excels in integrating with existing systems. Whether it's ERP software or specific manufacturing machinery, this flexibility is vital for businesses that have already established processes but want to enhance them with MES.
"Adopting an MES like Traksys isn't just about keeping up; it's fundamentally about future-proofing your operations to meet the demands of modern manufacturing."
- User-friendly Interface: The intuitive design of Traksys ensures that users, regardless of their technical expertise, can navigate its capabilities efficiently. This aspect plays a significant role in user adoption, which is paramount for the system's success.
In summary, understanding Traksys MES and its core functions is essential for utilizing its full potential. As the manufacturing landscape continues to evolve, having a system that not only enhances efficiency but also aligns with business objectives is indispensable. The blend of real-time insights, quality control mechanisms, and seamless integrations empowers manufacturers to thrive in a competitive market.
The Evolution of Manufacturing Execution Systems
Manufacturing Execution Systems (MES) like Traksys have become central to modern manufacturing processes, making it essential to understand their evolution. This journey is not just a mere technical upgrade; it reflects profound shifts in how manufacturers optimize operations, improve product quality, and meet client expectations. Understanding this evolution goes beyond historical events; it grasps the strategic importance of MES in navigating the challenges of today’s competitive landscape.
Historical Overview
Historically, manufacturing operated on the foundation of manual processes and isolated systems. In the mid-20th century, production was largely driven by paper-based systems, relying on physical logs and manual data entry. As businesses grew, inefficiencies started to bubble to the surface.
As production lines expanded, the bottlenecks of communication among teams became glaringly obvious. There was a clear need to integrate information flow, leading to the emergence of the first generation of MES. This initial phase aimed to connect enterprise systems with the shop floor, allowing for real-time visibility and control over manufacturing processes. Key players during this time included solutions like Rockwell Automation and Siemens, which pioneered early MES frameworks.
But let’s not stop there. By the late 20th century, the evolution picked up steam, influenced by the rise of technology. The introduction of computers and software enabled manufacturers to enhance operational efficiency substantially. Gradually, MES replaced the labor-intensive, paper-driven methods, bringing about a new era of data-centric decision-making. The transition from manual entries to automated data collection was pivotal. It empowered decision-makers and floor managers with timely information, revolutionizing how production was managed.
Technological Advancements
The leaps in technology during the 21st century have signified a watershed moment for MES. With advancements in Internet technologies, cloud computing, and data analytics, the role of MES has evolved dramatically. Here are some notable shifts:
- Cloud-Based Solutions: Manufacturers no longer rely solely on on-premises systems. For instance, scalability and ease of access from remote locations have made cloud-based MES increasingly popular.
- Real-Time Data Analytics: Access to real-time analytics has allowed for immediate decision-making. Companies can track production metrics live, leading to a quick identification of issues before they escalate. The agility combined with speed is an undeniable advantage.
- Integration with IoT: The integration of Internet of Things (IoT) has further advanced MES by connecting devices and machines. This technology enables a seamless flow of data from equipment to the MES, providing an unprecedented level of insight. The result? Manufacturers can predict maintenance needs and decrease downtime effectively.
- Artificial Intelligence: MES is beginning to incorporate AI for predictive analysis and automated decision-making. The potential for autonomous operational adjustments opens doors to efficiency levels previously thought unattainable.
In essence, the progression of MES from rudimentary manual systems to sophisticated, technology-driven solutions marks a monumental shift in the manufacturing landscape. Decision-makers and IT professionals alike must grasp this evolution to fully leverage the systems available today. Utilizing Traksys MES, for instance, aligns with this evolution, offering features that cater to the pressing demands of modern manufacturing.
Traksys MES Features and Capabilities
Understanding the features and capabilities of Traksys MES is crucial for organizations aiming to enhance their manufacturing efficiency. This system encompasses a broad array of functionalities that not only streamline production processes but also contribute significantly to overall operational productivity. From real-time monitoring to in-depth data analysis, each feature plays a pivotal role in shaping a more agile and responsive manufacturing environment.
Real-Time Monitoring
Real-time monitoring is one of the standout features of Traksys MES. In manufacturing, timing is everything. Having the ability to monitor processes as they happen makes all the difference. By keeping a close watch on machinery, workflow, and employee performance, decision-makers can identify bottlenecks on the fly. As a result, they can address issues before they escalate into larger problems.
- Immediate Insights: This feature enables manufacturing challenges to be identified and resolved swiftly, thus minimizing downtime.
- Enhanced Accountability: With all operations being tracked, team members are more likely to stay engaged and accountable for their tasks.
- Flexible Adjustments: If production starts veering off schedule, managers can make real-time adjustments to keep things on track.
"In the fast-paced world of manufacturing, the ability to react in real-time is what sets successful companies apart from the rest."
Data Collection and Analysis
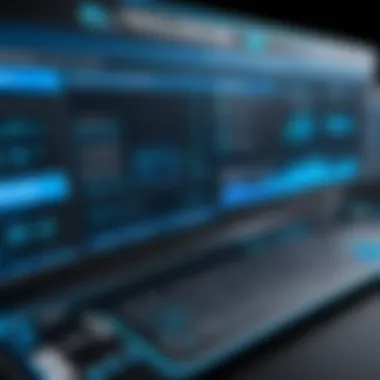
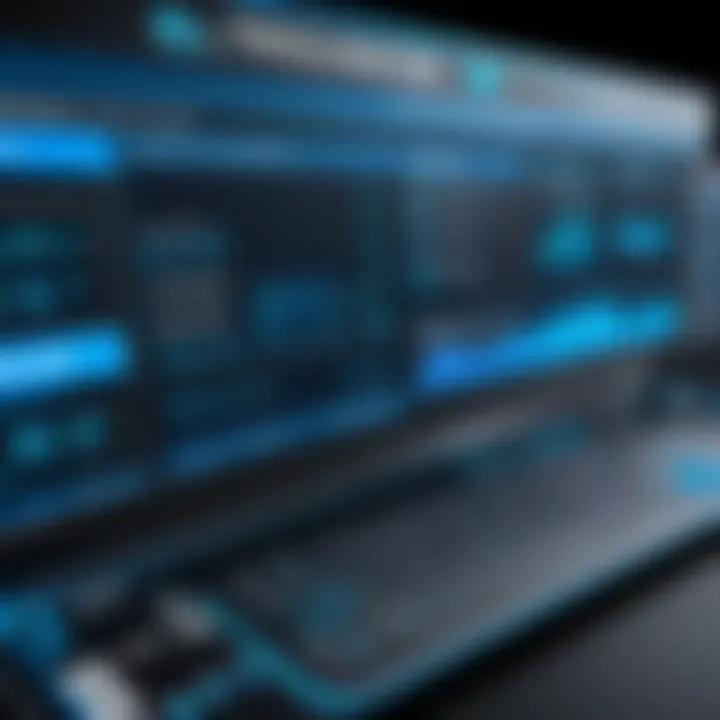
The functionality of data collection and analysis within Traksys MES is second to none. This system doesn’t just gather data for data's sake; it transforms raw numbers into valuable insights. In an industry where data is king, such tools are crucial. Here’s what makes this feature compelling:
- Comprehensive Data Capture: Traksys MES collects data from various machines and processes. This extensive collection paints a complete picture of operations, ensuring no detail slips through the cracks.
- Actionable Insights: Through analytical tools, it enables stakeholders to glean insights from the data, guiding decisions that can enhance both quality and efficiency.
- Predictive Analytics: By analyzing trends and historical data, businesses can anticipate issues before they arise, allowing them to maintain consistent operational flow.
Integration with Existing Systems
Another remarkable feature of Traksys MES is its capacity for seamless integration with existing systems. Many manufacturers use a diverse range of software and hardware solutions. Traksys MES recognizes this and facilitates integration across various platforms, which is essential for a harmonious work environment. Here’s why this matters:
- Unified Operations: The system acts as a bridge between different technologies, ensuring that all parts of the manufacturing process communicate effectively.
- Reduced Risk of Disruption: Implementing a new system often comes with risks. However, the ease of integration means less chance of disrupting ongoing processes.
- Optimized Workflow: Making different systems work cohesively helps streamline operations and enhances overall productivity.
Benefits of Implementing Traksys MES
Implementing Traksys MES in manufacturing environments isn't just a matter of upgrading technology. It's about revolutionizing how operations are conducted, which can yield significant benefits that permeate across various levels of the business. A thoughtful approach to its adoption can lead to transformative changes in efficiency, quality, and adaptability in the face of changing market demands. In this section, we'll dive into the specific advantages that Traksys MES brings to the table, focusing on enhanced operational efficiency, improved product quality, and increased flexibility and responsiveness.
Improved Operational Efficiency
One of the standout features of Traksys MES is its capacity to enhance operational efficiency. When production processes are executed with streamlined workflows and real-time monitoring, it leads to decreased downtime and quicker decision-making. For instance, consider a factory faced with inconsistent output due to machine malfunctions. With Traksys MES, operators can receive instant alerts and diagnostic information which allows for rapid corrective actions. This quick response ultimately minimizes production delays and keeps the wheels of industry turning smoothly.
Moreover, by automating routine tasks, it alleviates the burden on workers, allowing them to focus on more critical operations. An operator in manufacturing might spend hours collecting data for daily reports—data that the MES can gather and present instantly. Thus, this technology not only shortens the lapses between problem identification and resolution, but also enhances overall productivity.
Enhanced Product Quality
Quality assurance is an ever-present challenge in manufacturing, and Traksys MES addresses this by providing tools for improved oversight and adherence to standards. Imagine a food production line where each ingredient must meet stringent guidelines. Traksys MES can document every step of the process, ensuring compliance and traceability. By capturing data on product inspections and deviations in real time, the system allows manufacturers to take immediate corrective measures, reducing waste and safeguarding quality.
Additionally, data analytics embedded within Traksys MES can identify patterns and trends that might otherwise go unnoticed. For example, if specific production runs consistently yield defects, manufacturers can analyze the parameters surrounding those runs and adjust processes accordingly. Such proactive approaches lead to higher-quality outputs and satisfied customers, which in turn bolsters brand reputation.
Increased Flexibility and Responsiveness
In today’s dynamic market, flexibility and responsiveness can determine a company’s success. Traksys MES grants manufacturers the agility to pivot and adapt to shifting demands or unexpected challenges. For example, if a sudden uptick in demand occurs for a particular product, the system can help reorganize production schedules and allocate resources swiftly. This adaptability isn't just good for turnover, it’s a competitive edge.
Additionally, the integration of various data sources allows for a comprehensive view of operations that can be adjusted on the fly. Workforce management tools tied to the MES enable shift adjustments in real-time based on production needs, ensuring that resources are used efficiently. This kind of responsiveness not only helps in meeting customer expectations but also in maintaining employee morale, as workflows are designed to cater to changing needs instead of confines.
"The implementation of Traksys MES is not merely a technical upgrade; it's a strategic decision that can enhance the very fabric of your operational processes."
Challenges in Manufacturing Without MES
In the fast-paced realm of manufacturing, operating without a Manufacturing Execution System (MES) like Traksys can result in a host of challenges that not only impact productivity but also affect the bottom line. Understanding these challenges can illuminate the significant advantages that an MES can bring to an organization.
Inefficiencies in Production
Without an MES, manufacturers often find themselves grappling with inefficiencies that can be as subtle as a whisper or as glaring as a neon sign. For instance, a manufacturer working on a tight schedule might manually track production data, leading to time-consuming processes and human errors. It's like trying to catch water in a sieve—no matter how hard one tries, some of it will just slip through the cracks.
An MES provides a streamlined method for scheduling and managing production activities. When this system is absent, production plans can frequently collide with realities on the ground, causing delays and waste. Employees may be left wondering if they should work on one task or another due to shifting priorities without a reliable framework.
Data Silos and Lack of Visibility
Consider the scenario where different departments—like quality control, production, and logistics—operate in isolated data silos. Each team might be working diligently, yet they lack a cohesive view of the entire manufacturing process. Such fragmentation creates gaps in communication that can stifle workflow and delay critical decisions.
“A stitch in time saves nine,” but when communication isn’t flowing freely, it can feel like trying to patch a ship while it’s sinking. Without the centralized data management that an MES provides, decision-makers are left in the dark, making it nearly impossible to diagnose problems promptly or to make data-informed decisions. Detailed visibility into each step of the production process is crucial to optimizing efficiencies and driving improvement.
Quality Control Issues
The absence of an MES can make quality control akin to playing a game of whack-a-mole. When defects occur, identifying their root causes becomes significantly more complex without real-time tracking and historical data analysis. Suppose a defect arises in a production run; without an MES, tracing the issue back through the manufacturing steps is time-consuming, if not impossible.
An MES helps to ensure that quality checks and validations are integrated into the production process. Without such a system, companies may face increased returns or recalls, which are costly and damaging to brand reputation. Quality isn’t just about the end product; it’s also about ensuring each step of the process is aligned with industry standards and customer expectations. In an age where product integrity can make or break a business, neglecting quality control due to a lack of structured oversight can spell trouble.
Case Studies: Successful Implementations of Traksys MES
Understanding the practical applications of Traksys MES in real-world scenarios is essential for stakeholders considering adoption. Case studies provide invaluable insights into how different industries leverage the system to enhance operational efficiency and production quality. Exploring these implementations helps demystify the process, highlighting specific challenges faced, solutions adopted, and the outcomes achieved. Real-life examples serve not only to showcase the system's capabilities but also to inspire confidence in its efficacy for decision-makers and IT professionals.
Manufacturing Industry Example
In the manufacturing sector, let’s look at a fictitious case involving a medium-sized automotive parts manufacturer, AutoMakers Inc. Before implementing Traksys MES, AutoMakers dealt with a myriad of challenges, from production delays to inventory inaccuracies. Their operational inefficiencies were leading to increased costs and customer dissatisfaction.
After the integration of Traksys MES, AutoMakers experienced a dramatic transformation. Key improvements included:
- Real-time production monitoring: They were able to track production metrics in real-time, enabling swift adjustments to workflows. This constant monitoring meant that issues could be identified and rectified before blowing out of proportions.
- Data accuracy: By leveraging Traksys for data collection, errors caused by manual data entry were drastically reduced. This allowed management to make better-informed decisions regarding inventory and resource allocation.
- Enhanced collaboration: With the MES in place, everyone from the shop floor to upper management had access to vital information, fostering a culture of collaboration and prompt decision-making.
As a result, AutoMakers Inc. reported a 30% increase in productivity and a 20% reduction in operational costs, leading to improved customer satisfaction and higher retention rates.
Process Industry Example
Turning our eyes to the process industry, consider a fictional example of a chemical manufacturing facility, ChemCo Productions. Prior to adopting Traksys MES, ChemCo struggled with process inconsistencies and compliance issues that were eating into their profit margins.
The introduction of Traksys MES brought several notable benefits:
- Consistency control: The MES enabled ChemCo to standardize their production processes, ensuring that every batch met stringent quality metrics. By maintaining consistency, they minimized waste and rework.
- Compliance tracking: Traksys MES features helped automate compliance checks, instantly documenting adherence to industry regulations, thus avoiding hefty fines and legal complications.
- Predictive maintenance: With built-in analytics, the factory could predict equipment failures before they occurred, resulting in reduced downtime and maintenance costs.
These enhancements led to ChemCo seeing a 25% reduction in production costs and noticeable improvements in product quality, earning rave reviews from clients and industry regulators alike.
Both of these examples illustrate how implementing Traksys MES can transform operations across varied industries, driving efficiency, quality, and compliance. As industries continue to evolve, the insights gained from these case studies will remain pivotal in informing best practices and strategies for future adopters.
The Role of Data in MES
Manufacturing Execution Systems like Traksys MES operate at the intersection of real-time operational data and strategic decision-making. In modern manufacturing, the significance of data cannot be overstated. Data acts as the backbone of MES, forming a framework through which businesses can improve operational efficiencies and product quality. The ability to capture, analyze, and act on data effectively can determine a company's competitive edge in the market.
Importance of Data Integrity
Data integrity is fundamental when it comes to the effectiveness of any MES. It refers to the accuracy and consistency of data throughout its lifecycle. Without reliable data, organizations risk making poor decisions that can lead to inefficiencies—factors that could significantly affect production outcomes.
- Quality Assurance: High-quality data ensures that the information powering MES operations is trustworthy. Misleading data can result in errors in production planning, inventory management, and resource allocation.
- Regulatory Compliance: Many industries are bound by regulations that dictate data handling. Ensuring data integrity allows companies to maintain compliance with such guidelines, avoiding penalties that could arise from lapses.
- Operational Analytics: When data is consistent and accurate, organizations can perform better analytics. Good data enables the implementation of predictive maintenance schedules, optimizing production runs and reducing downtime.
In practice, maintaining data integrity involves regular audits, validation processes, and robust cybersecurity measures to protect against breaches, which can compromise quality and lead to distrust in the data itself.
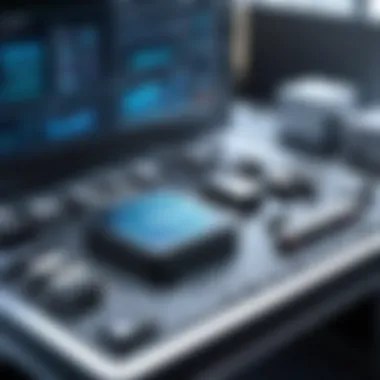
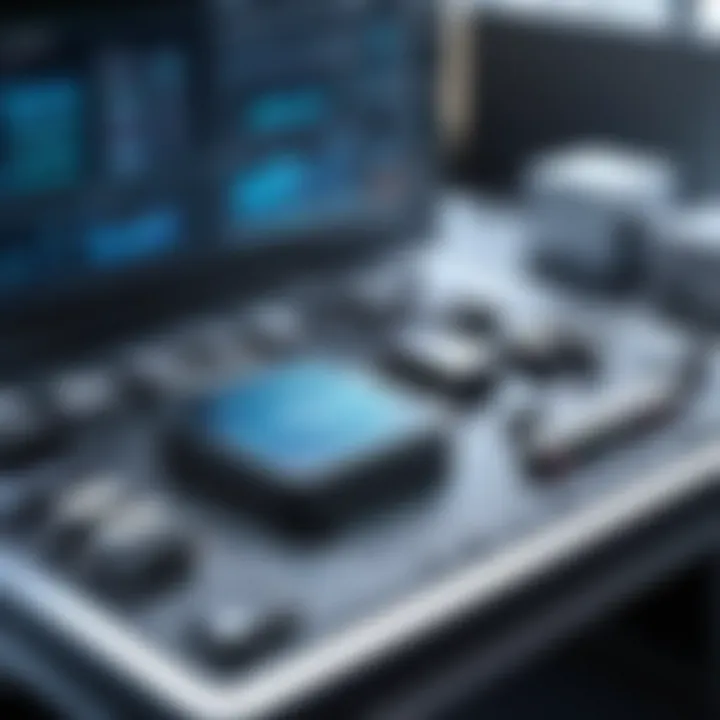
Data Analytics for Decision Making
Data analytics plays a pivotal role in decision-making processes within manufacturing environments. It transforms raw data into actionable insights, helping leaders to make informed choices based on what the data reveals about operational trends and performance metrics.
- Identifying Patterns: Advanced data analytics can uncover trends that may not be immediately apparent. For instance, identifying recurring issues in machinery can lead to more proactive maintenance schedules, significantly decreasing failure rates over time.
- Resource Allocation: With clear insights from data, organizations can align their resources better—whether it's manpower, materials, or machinery. This strategic alignment helps lower costs while maximizing production output.
- Performance Benchmarking: By analyzing historical data, organizations can set performance benchmarks. These benchmarks enable manufacturers to measure their output and efficiency against industry standards, pushing for continuous improvement.
"In the world of manufacturing, the data-driven approach is not just an advantage but a crucial necessity to thrive in a competitive marketplace."
Tools integrated within systems like Traksys MES harness this analytical power. By enabling real-time data flow, these systems support decision-making that can align closely with business goals. Companies that leverage data analytics effectively can not only enhance their immediate operational efficiency but also adapt to future challenges, ensuring sustainability and relevance in an ever-evolving industry.
Future Trends in Manufacturing Execution Systems
Understanding the future landscape of manufacturing execution systems (MES) is crucial for anyone in the manufacturing sector. As industries evolve, the way operations are managed must also adapt to meet new challenges and opportunities. This section delves into two pivotal trends: artificial intelligence and automation, alongside the integration of the Internet of Things (IoT). These trends not only enhance productivity but pave the way for smarter, more responsive manufacturing environments.
Artificial Intelligence and Automation
The rise of artificial intelligence (AI) in the manufacturing realm cannot be overstated. By implementing AI, businesses can automate several processes that were once manual and time-consuming. For example, predictive maintenance uses AI algorithms to anticipate equipment failures before they occur, minimizing downtimes and keeping productivity high.
AI can also analyze vast amounts of data generated on the production floor. This data analysis helps in recognizing patterns that might go unnoticed by human operators, leading to informed decision-making and operational improvements.
Furthermore, automation facilitated by AI enhances speed and accuracy. With robotic process automation (RPA), manufacturing tasks such as packaging, assembly, and quality inspection are not only faster but also more consistent. This automation means that employees can focus on more strategic tasks rather than repetitive actions. To illustrate, a company employing Traksys MES can utilize AI to fine-tune its production line adjustments in real time, reacting to fluctuations in demand or unexpected disruptions.
However, merging AI with human judgment is paramount. While machines can significantly enhance processes, the insights and creativity of human workers still play a critical role in innovation and strategy development. Many organizations are likely to see hybrid models in their operations, blending the efficiency of AI with the critical thinking that only human beings provide.
Internet of Things Integration
Another trend profoundly shaping MES is the integration of the Internet of Things. The IoT involves connecting devices and machines on the manufacturing floor through the internet, facilitating data exchange in real-time. This interconnectedness allows for a streamlined flow of information between systems, enhancing visibility across all levels of manufacturing processes.
For instance, consider a scenario where machines on the factory floor are equipped with sensors that track their operational status. This data can be relayed to Traksys MES, offering real-time updates on performance indicators and enabling immediate responses to potential malfunctions. As such, manufacturers can achieve a more proactive approach to maintenance and production management, reducing costs and enhancing operational efficiency.
Moreover, IoT devices can improve traceability in manufacturing, ensuring that every step is logged and can be reviewed as needed. This capability simplifies compliance with regulations, such as those in the food and pharmaceutical sectors, where product integrity is paramount.
However, IoT integration is not without challenges. Security concerns surrounding IoT devices must be addressed through robust cybersecurity measures. The more connected systems are, the more vulnerable they can be to potential breaches, making cybersecurity a top priority for manufacturers adopting these technologies.
Selecting the Right MES for Your Business
Choosing the right Manufacturing Execution System (MES) is crucial for any business aiming to optimize its manufacturing processes. It's not just about picking a software package; it's about ensuring that the system aligns with the unique needs of your operation, whether you’re in automotive, electronics, or food production. The right MES can enhance productivity, minimize waste, and improve product quality while ensuring compliance with industry regulations.
When selecting an MES, several key elements come into play. Taking the time to evaluate these aspects can lead to a smoother implementation and ultimately drive better operational performance. Here are important considerations:
Criteria for Evaluation
1. Scalability and Flexibility
Your MES should be able to grow with your business. It’s essential to choose a system that allows for easy upgrades and can accommodate increased production as well as changes in operational processes.
2. Integration Capabilities
A good MES must seamlessly integrate with existing systems like ERP, CRM, and supply chain management software. Compatibility with your current infrastructure can save time and money in the long run.
3. User-Friendliness
Complex software can lead to user frustration. The MES interface should be intuitive and easy to navigate for both managers and floor workers. The less time you have to spend training employees, the better.
4. Real-Time Data Management
You want a system that offers real-time visibility into your operations. This improves decision-making and allows for immediate responses to issues as they arise.
5. Cost of Ownership
Calculate not just the upfront cost, but also consider maintenance, training, and potential hidden fees down the track.
6. Vendor Support and Services
Evaluate the level of support provided by the vendor. Constant updates, customer service quality, and training resources can dictate how well the MES performs long-term.
By focusing on these criteria, companies can better align their needs with the features offered by the MES, aiding in a more strategic decision-making process.
Vendor Considerations
Engaging with the right vendor can make all the difference when implementing an MES. Here are several aspects to weigh:
1. Industry Experience
Look for vendors who have a strong track record in your specific industry. They will understand the challenges you face and can offer tailored solutions instead of a one-size-fits-all approach.
2. Customer References and Case Studies
Examine their reputation through third-party reviews or request customer testimonials. A vendor with proven success stories can provide confidence in their capability to deliver results.
3. Customization Options
Ensure the vendor offers solutions that can be customized to fit your specific processes. Rigid systems may not yield the optimal efficiency sought by your operations.
4. Ongoing Upgrades and Innovation
Technology evolves rapidly, and you need a vendor that prioritizes R&D for future-proofing their solutions. Discuss their roadmap for updates and how often they roll out enhancements.
5. Communication and Responsiveness
Communication is key; you want a vendor who understands your needs and maintains a dialogue throughout the implementation process. Prompt responses can save you lots of headaches.
The right MES can become the backbone of your manufacturing process, ensuring products flow smoothly from production to delivery.
Taking all these factors into account will help in selecting a tailored MES solution that fits your business's needs. After all, this investment is not merely about software—it's a decision that impacts the operational health of your entire organization.
Implementation Strategies for Traksys MES
Effective implementation strategies for Traksys MES not only determine the extent to which the system will enhance manufacturing efficiency but also establish a strong foundation for its long-term success. This section focuses on the nuances of both change management and training, two pivotal elements in fostering an environment where Traksys MES can truly shine. Without careful planning and execution in these areas, even the most advanced systems may not yield their intended benefits.
Change Management
Navigating the waters of change management can feel like sailing a ship through stormy seas. Engaging with the workforce during the transition to Traksys MES isn’t merely a checklist task; it’s crucial for reducing resistance and fostering buy-in.
The first step in effective change management involves clearly communicating the vision behind the implementation. Stakeholders must understand how Traksys MES fits into the larger picture of operational excellence and how it can address existing challenges. This realization can inspire enthusiasm rather than trepidation regarding the shifts in everyday work.
A few strategies to successfully manage changes include:
- Involve Key Stakeholders: Building support from leaders and influential employees in the early stages can leverage their influence to ease concerns among the broader workforce.
- Transparent Communication: Superiors should engage in open dialogues about what changes are coming, and explain the rationale behind them.
- Flexibility: Being ready to adjust implementation strategies based on feedback can significantly enhance acceptance. For instance, if employees suggest certain customizations to better suit their workflows, being willing to listen can go a long way.
Ultimately, organizational culture plays a significant role in how changes are accepted. Ensuring that employees feel valued and their input is appreciated can foster a climate of collaboration, rather than compliance.
Training and User Adoption
After laying the groundwork through change management, training becomes the next battleground in the push for effective adoption of Traksys MES. Training is not just about showing how to use new software; it involves empowering users to embrace it enthusiastically, thereby maximizing its capabilities.
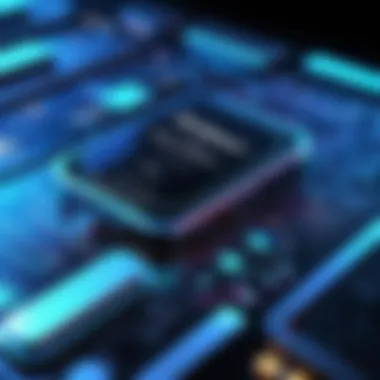
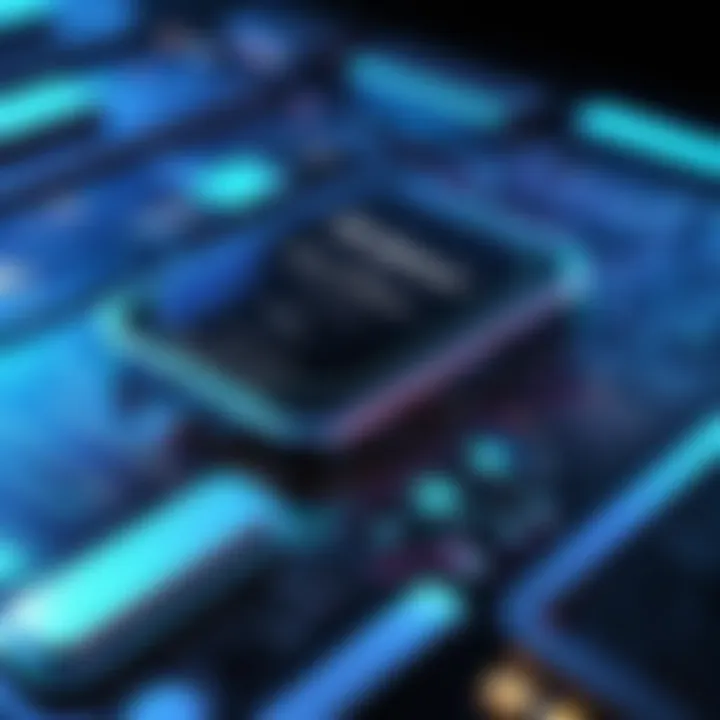
A few considerations in training efforts might include:
- Hands-On Workshops: Interactive sessions allow users to experiment with Traksys MES in a safe space, where they can explore its features without the pressure of actual operations.
- Tailored Learning Paths: Different departments might have varying needs and workflows. Customizing training sessions according to the specific responsibilities of each team can increase effectiveness and relevance.
- Ongoing Support: Implementing a support system, where users can seek help post-training, plays a critical role in building confidence. Access to resources such as FAQs, user forums, or even dedicated personnel can prove invaluable.
"User adoption is not about swaying with the winds; it's about anchoring the ship in calm waters for confidence in the journey ahead."
Emphasizing a culture of continuous learning can cater to a dynamic environment where users feel capable and competent in using Traksys MES. As manufacturers pivot towards real-time data-driven decisions, the role of well-trained staff becomes even more indispensable.
In summary, the implementation of Traksys MES cannot rest solely on technological advancements. By focusing efforts on change management and user training, organizations can realize the full potential of this sophisticated system, propelling themselves beyond ordinary operational capabilities into realms of heightened efficiency and productivity.
Traksys MES and Regulatory Compliance
In an increasingly complex manufacturing landscape, adherence to regulations is not merely an afterthought; it's a cornerstone of business operations. For companies utilizing Traksys MES, the intersection of technology and regulatory compliance becomes a key focus, as it directly impacts operational continuity and market credibility. Understanding the nuances of industry regulations and leveraging Traksys MES to ensure compliance can be a game-changer.
Understanding Industry Regulations
Regulations in the manufacturing sector can be as varied as the products being produced. Depending on the industry—whether pharmaceuticals, food and beverage, or electronics—companies face a maze of standards and protocols. These may include quality assurance requirements, environmental regulations, and safety protocols.
For instance, the FDA imposes stringent rules on pharmaceutical manufacturing that require detailed documentation and traceability of every ingredient. Likewise, the FDA’s Food Safety Modernization Act lays out specific guidelines for food manufacturers to prevent contamination. Adherence to these laws is critical, as failing to meet them can lead to significant penalties, fines, or even shutdowns. Companies that leverage Traksys MES can gain real-time insights into relevant metrics, simplifying the process of compliance with regulatory frameworks.
Ensuring Compliance Through MES
So, how exactly does Traksys MES facilitate compliance in such a convoluted environment? First, it offers real-time data tracking. This allows manufacturers to systematically record every stage of production, streamlining audits and inspections. The system's sophisticated analytics capabilities help identify compliance gaps before they become critical issues, allowing for swift corrective action.
Moreover, standard operating procedures can be embedded directly into the MES, ensuring every operator follows the necessary guidelines during production. Automation features also enhance compliance by minimizing human error, a common factor in regulatory infractions.
Key Benefits of Compliance with Traksys MES:
- Streamlined Audits: With all records readily accessible, audits shift from a daunting task to a straightforward review.
- Reduced Risk of Penalties: Proactively addressing compliance issues can significantly reduce the risk of incurring fines.
- Improved Product Quality: Following regulations often leads to higher quality products, which benefits customer satisfaction and loyalty.
- Enhanced Data Security: Traksys MES offers robust security features that protect sensitive regulatory information from breaches.
"Immediate compliance visibility can significantly reduce the burden of regulatory risk, allowing companies to focus more on business growth rather than simply keeping the doors open."
Traksys MES not only equips companies with the tools needed for navigating regulatory requirements but also fosters an environment where quality and efficiency become automatic practices rather than cumbersome tasks. As manufacturing continues to evolve, businesses employing MES solutions must prioritize regulatory compliance, turning challenges into opportunities for growth and leadership in their respective fields.
The Impact of MES on Workforce Dynamics
The intersection between a manufacturing execution system (MES) and workforce dynamics is one that can shape the future of any production environment. The introduction of Traksys MES brings not only technological advancements but also a transformational shift in how employees engage with their work. With every system, there’s a ripple effect on job roles, skill requirements, and ultimately, overall productivity. Understanding these changes is critical for businesses aiming to harness the full potential of their operations.
Shifts in Job Roles
When a sophisticated system like Traksys MES is implemented, the roles within a manufacturing team start to evolve. Traditionally, floor workers might have been primarily focused on manual tasks and direct oversight of machinery. With the introduction of MES, their roles often change to that of operators or supervisors utilizing the data provided by the system to enhance production efficiency.
The utilization of real-time data translates into greater responsibility for some positions. Operators are now expected to interpret metrics and leverage insights for quicker decision-making rather than just following preset instructions. This might seem daunting but ultimately leads to a more empowered workforce.
Moreover, managerial roles can also see change—where once they were focused on oversight, now they have more data at their fingertips. This allows for informed strategic planning and faster responses to potential issues, making their roles more dynamic and potentially more rewarding.
"The rise of technology in manufacturing brings new opportunities but demands a shift in mindset and roles for employees across the board."
Skill Development and Training Needs
As the job roles adapt, so do the necessary skills for each position. The workforce needs to upskill to meet the demands of a tech-driven workplace. Familiarity with the Traksys MES platform becomes crucial for operators, and training programs must be developed to ensure that all employees are equipped to handle new technologies effectively.
Training isn't just about understanding how to use the software—it encompasses critical thinking and data interpretation as well. Employees may need to engage in
- Workshops on data analytics
- Courses focusing on machine automation
- Certifications in quality management standards
The emphasis will also likely shift towards cross-training employees. With a variety of roles becoming more interlinked, fostering the ability to fill different positions will enhance flexibility in the workforce. This presents an opportunity for workers to diversify their skills, making them more adaptable in an ever-evolving job market.
Common Misconceptions About MES
The perception of Manufacturing Execution Systems, particularly Traksys MES, often comes laden with misconceptions. These misunderstandings can lead potential adopters to dismiss a system that could significantly enhance manufacturing efficiency. Knowing these misconceptions is vital for decision-makers and IT professionals, as understanding the truth can lead to smarter, more informed choices regarding the implementation of MES.
Cost Assumptions
One of the most prevalent misconceptions surrounding MES is the assumption that implementing such a system is prohibitively expensive. Often, stakeholders are led to believe that the initial outlay for software licenses, hardware, and training will take a considerable chunk out of their budget. However, this view can be shortsighted.
While it’s true that adopting Traksys MES requires an investment, it’s essential to consider the long-term savings it offers. Here's a closer look:
- Operational savings: Increased efficiency means fewer wasted materials and lower labor costs.
- Quality improvements: Reducing defects lowers costs associated with returns and rework.
- Scalability: As your business grows, the MES can adapt, potentially saving money on future upgrades.
- Quick ROI: Companies often see a return on investment within months after implementation, contradicting the view that the costs are excessive.
Stakeholders should conduct a thorough cost-benefit analysis rather than rely solely on initial financial impressions. Investing time to understand potential value can flip the perspective from costly to cost-effective.
Perceptions of Complexity
Another common myth is the perception that MES systems are inherently complex and difficult to implement. This lines up with a broader belief that technology will inevitably complicate operations rather than simplify them. Though any system's setup entails challenges, Traksys MES emphasizes user-friendly design and integration capabilities.
Consider these points:
- User-Centric Interface: Traksys MES often features interfaces designed with the end-user in mind, reducing the learning curve.
- Customization: Managers can tailor the system to meet specific operational needs, making it less daunting to use.
- Support and Training: Many vendors, including those providing Traksys MES, offer ongoing training and support to ease this transition.
Ultimately, the notion that adopting an MES is excessively complex may stem from unfamiliarity with the technology. A proactive approach to familiarizing teams with the software can mitigate concerns entirely.
"Understanding the myths about MES is as important as understanding the system itself. Knowing what’s fact and what’s fiction helps pave the way for a smoother transition and greater success."
Embracing Traksys MES equips manufacturers with the tools to streamline their processes. By overcoming these misconceptions, stakeholders can focus on leveraging MES to its fullest potential.
Ending
In wrapping up the discussion around Traksys MES, it’s crucial to recognize its position as a game-changer in modern manufacturing. As industries face increasing pressure to optimize operations, adopt new technologies, and meet rigorous quality standards, systems like Traksys MES provide no-nonsense solutions that tackle these challenges head-on.
Summarizing Key Takeaways
- Operational Efficiency: Traksys MES streamlines processes, reducing bottlenecks and ensuring that production runs smoothly. The integration of real-time monitoring and analytics provides the insights necessary to maintain peak operational performance.
- Quality Assurance: By incorporating effective data collection mechanisms, companies can maintain high product quality. With rigorous monitoring, any deviations can be detected early, preventing costly defects.
- Flexibility: Adaptability is a significant advantage in today’s fast-paced environment. Traksys MES allows manufacturers to pivot quickly based on market demand or operational requirements.
Future Outlook for MES Technology
Looking ahead, the trajectory for MES technology, particularly Traksys, appears promising. Emerging technologies, such as artificial intelligence and the Internet of Things, are poised to profoundly influence how MES systems function. As these technologies evolve, we can expect:
- Advanced Predictive Analytics: Companies may leverage AI to not just gather data but to predict trends and potential disruptions well before they occur.
- Increased IoT Connectivity: As more devices become interconnected, the need for seamless integration will grow. Traksys MES, by adopting these advancements, can offer even greater visibility into manufacturing processes.
In summary, the importance of continuing to evolve along with these technologies is clear. Companies that invest in robust MES systems like Traksys will be better prepared to tackle the complexities of modern manufacturing, thereby securing a competitive edge in their respective industries.