Understanding CMMS in Maintenance Management Strategies
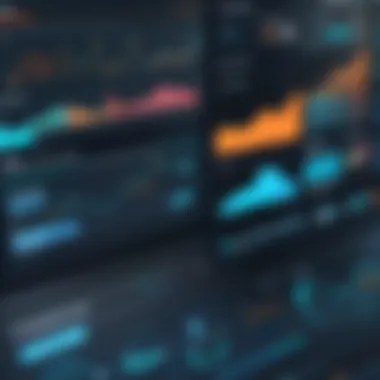
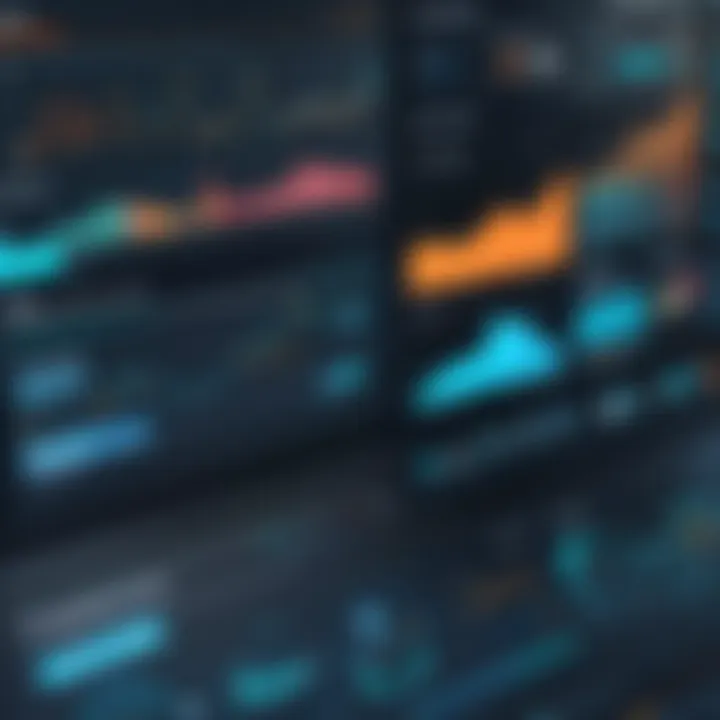
Intro
In today's fast-paced business environment, the management of maintenance activities has become a meticulous balancing act. With operational costs rising and the expectation for downtime reduction growing, organizations must shift from a reactive to a proactive approach. This is where Computerized Maintenance Management Systems come into play, offering essential tools to streamline maintenance processes, improve resource utilization, and, ultimately, enhance the bottom line.
The significance of CMMS cannot be overstated. It goes beyond just doing maintenance tasks; it's about transforming the entire upkeep strategy to maximize efficiency. Imagine a ship sailing smoothly through unpredictable waters— that's what implementing a CMMS can achieve in the world of maintenance management. As we dig deeper into this topic, we will explore its core functionalities, the landscape of available software, and strategies for successful implementation.
Let's dive headfirst into the Industry Overview, setting the stage for our journey through the complexities of CMMS.
Foreword to CMMS
Computerized Maintenance Management Systems, or CMMS, have become a pivotal aspect of maintenance management in various industries. The significance of introducing CMMS in this article lies in understanding how these systems are revolutionizing maintenance strategies. Businesses are increasingly aware that effective maintenance management is not merely about preventing equipment failures but also about optimizing productivity, increasing asset longevity, and reducing operational costs.
A well-implemented CMMS leads to better visibility of maintenance activities, streamlining workflows and providing intuitive access to vital data. Decision-makers who grasp the importance of CMMS can empower their organizations to make smarter maintenance choices, enable real-time monitoring of assets, and adopt preventive practices.
In today’s fast-paced business environment, the proactive management of assets is vital for survival. Companies embracing CMMS create pathways for sustainability and reliability in their operations, ensuring that maintenance is not an afterthought but an integrated component of their strategic planning.
Definition of CMMS
At its core, a Computerized Maintenance Management System is a software solution designed to simplify maintenance management tasks. It serves as a centralized hub where all data related to asset maintenance, work orders, and inventory can be tracked and managed efficiently. From scheduling preventive maintenance to generating reports on asset performance, CMMS offers a suite of functionalities that enhances decision-making and boosts organizational efficiency.
In plain terms, think of CMMS as an intelligent assistant that keeps the maintenance department organized and informed. It collects data on various factors like equipment usage, repair histories, and parts inventory, all of which help in planning maintenance activities and allocating resources effectively.
Historical Evolution of Maintenance Management
The journey of maintenance management has been anything but linear. It has undergone significant transformations over the decades. Initially, maintenance practices were largely reactive; companies waited until equipment failed before repairs were made. This approach led to unexpected downtimes and skyrocketing maintenance costs.
As industries evolved, so did the notion of maintenance. The introduction of computerized systems in the late 20th century marked a turning point. Organizations began adopting software solutions to manage their maintenance functions better.
"The evolution of maintenance management from a reactive to a proactive approach epitomizes the technological advancements that have powered organizational efficiency."
In essence, the rise of CMMS was a response to the growing complexity of maintenance operations. With advances in technology, maintenance practitioners now have tools that enhance predictive analytics, enabling them to anticipate equipment needs before they become pressing issues. This historical evolution reflects not only a shift in practice but a broader understanding of maintenance's critical role in operational success.
Core Components of CMMS
The landscape of maintenance management is constantly evolving, and at its heart lies the Computerized Maintenance Management System, or CMMS. Understanding the core components of CMMS isn't just a technicality; it's fundamental for organizations aiming to enhance their maintenance strategies. Each element plays a crucial role in improving efficiency and reliability, making it possible to transform chaotic maintenance efforts into streamlined operations.
Asset Management
When it comes to maintenance management, Asset Management is akin to having a well-organized toolbox. Organizations hold an array of physical assets - machinery, equipment, and facilities. With a CMMS, every asset can be cataloged, tracked, and assessed effectively. This enables decision-makers to know the status, location, and overall health of each asset in real-time. The importance of proper asset management cannot be overlooked. A well-managed inventory helps to prevent unnecessary downtime by highlighting which assets require attention and when.
Imagine a factory where maintenance personnel can quickly find detailed information about a crucial piece of machinery. They can run a diagnostic check, geometric specs, or historical maintenance records with just a few clicks. This clarity not only boosts morale but leads to better resource allocation and efficient planning.
Work Order Management
Work Order Management acts as the beating heart of a CMMS. Each time an issue arises, whether it’s an emergency repair or a scheduled task, it's recorded as a work order. This systematization keeps everyone on the same page.
One important aspect is the prioritization of tasks. Not every problem is a fire to be extinguished immediately. Work order management allows teams to categorize issues by urgency, ensuring that critical repairs are done without delay while minor fixes can wait their turn. This level of organization prevents confusion and reduces the risk of duplicated efforts.
Key benefits include:
- Streamlined Communication: All staff can see the status of work orders, facilitating updates and coordination.
- Enhanced Tracking: It allows for streamlined tracking of job completion, helping to hold teams accountable.
Preventive Maintenance Scheduling
Preventive Maintenance Scheduling is the proactive side of maintenance management. It’s not just about fixing what’s broken but ensuring that it doesn't break in the first place. A solid CMMS will enable organizations to set up clear routines, helping them stick to an effective maintenance schedule.
Being ahead of the game can significantly reduce unforeseen breakdowns and extend the life of equipment. Consider this: a manufacturing plant that implements regular checks as per the machine’s operational hours sees a marked reduction in case of major repairs compared to one that waits for issues to arise. This not only saves money but enhances operational reliability.
Inventory Management
Last but not least, there's Inventory Management. In any maintenance setting, spare parts and maintenance tools are crucial. A CMMS maintains a detailed inventory of parts, which signifies faster repairs and minimized delays.
Keeping tabs on inventory ensures that parts are available when needed. It also prevents overstocking, which can tie up capital unnecessarily. For instance, a maintenance supervisor discovering they have 10 of a particular bearing when they only need one can markedly waste resources. Instead, a CMMS helps optimize inventory, aligning stock levels with actual needs.
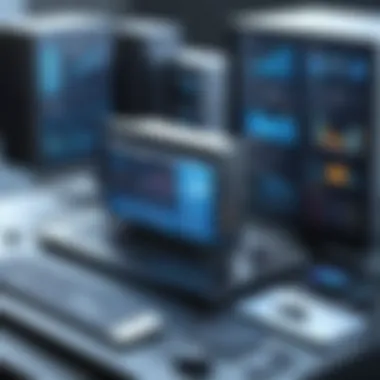
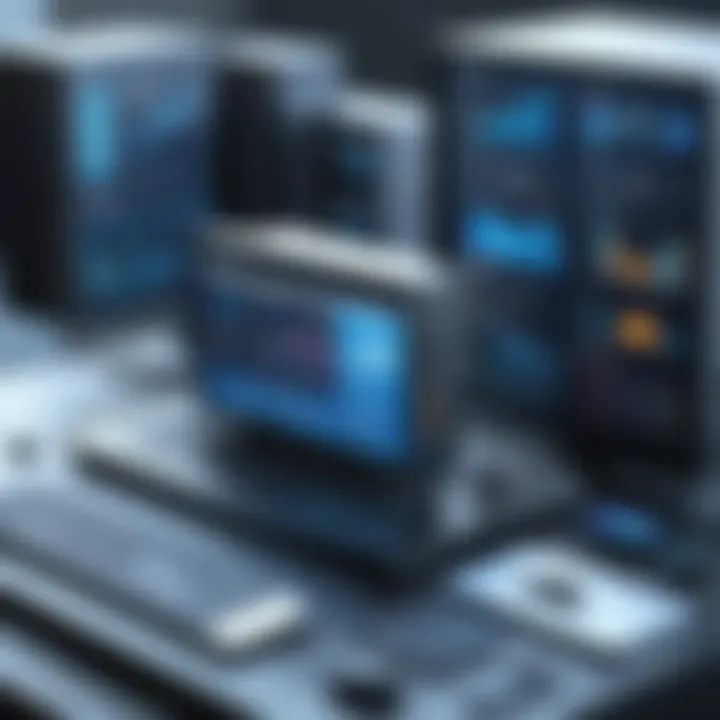
"An effective CMMS doesn’t just streamline processes; it creates a culture of proactive maintenance workflows."
These components together create a cohesive unit that drives efficiency in maintenance management. Having the right tools in the maintenance toolkit can transform the way organizations approach upkeep and task management, paving the way for enhanced performance and reduced costs over time.
Benefits of Implementing CMMS
The implementation of a Computerized Maintenance Management System (CMMS) is not merely a tech upgrade; it's a strategic leap toward optimizing maintenance operations across various sectors. Such systems are invaluable for organizations looking to redefine their maintenance landscape while maximizing asset utility. A well-implemented CMMS can bring forth a wealth of benefits that directly contribute to the smooth functioning of day-to-day operations, making it a worthwhile consideration for any maintenance manager or decision-maker.
Increased Efficiency and Productivity
One of the most significant advantages of a CMMS lies in its ability to boost efficiency and productivity. With traditional methods, managing maintenance tasks often involved a great deal of paperwork, spreadsheets, and manual tracking, which are prone to errors and incomplete data.
A CMMS simplifies this process. Tasks can be scheduled and managed digitally, enabling maintenance teams to prioritize their workload effectively. For instance, instead of wasting valuable time searching for service records or maintenance logs, technicians can quickly access this information at the click of a button.
- Automated reminders for maintenance schedules keep everyone in the loop.
- Technicians can receive work orders on their mobile devices, reducing downtime.
This switch not only streamlines operations but also mitigates downtime caused by unexpected equipment failures. Consequently, operational costs can be significantly reduced, and productivity can soar as workers concentrate on their core tasks rather than being bogged down by administrative burdens.
Cost Reduction
Cost control is a constant challenge in maintenance management. Traditional practices can lead to overspending on repairs and inefficient use of resources. A CMMS can be a game-changer in this regard. By systematically tracking assets and maintenance history, organizations can make informed decisions about resource allocation.
- Availability of historical data allows for better forecasting and preventive maintenance strategies.
- This proactive approach can drastically cut down on expensive emergency repairs since issues can be addressed before they escalate.
Furthermore, optimized inventory management—another key feature of CMMS—ensures that parts are available when needed without overstocking. By reducing excess inventory costs while improving parts procurement, a CMMS enables companies to keep a tighter grip on their budgets.
Enhanced Compliance and Reporting
Regulatory compliance is an intricate aspect of maintenance in sectors ranging from manufacturing to facilities management. Maintaining accurate records and fulfilling compliance requirements can be daunting but crucial for legal and operational credibility.
A CMMS simplifies compliance through automated reporting functions. Data entry errors are minimized, and the system maintains a comprehensive log of all maintenance activities, which can be easily accessed during audits.
- Real-time dashboards provide insights into compliance metrics.
- Scheduled reports can be generated without additional effort, saving time and effort on administrative tasks.
In essence, enhanced compliance leads not only to smoother audits but also fosters a culture of accountability and transparency, integral elements for building trust in both internal and external operations.
Key Features of Modern CMMS Solutions
When looking at a CMMS, one can’t ignore the pivotal role that its features play in modern maintenance management. These features not only streamline processes but also enable organizations to adapt to the fast-paced technological landscape. With continuous advancements, the right CMMS can become a game-changer, providing a foundation for efficiency and data-driven decision-making. Let's explore the key features that modern systems offer.
User-friendly Interface
A user-friendly interface is a cornerstone of any effective CMMS platform. The intuitive design of the software enables users—from field technicians to upper management—to easily navigate through functions. When a CMMS is complex or cluttered, it can create roadblocks.
Consider an organization where many staff members are not tech-savvy. Without a clear, easily workable interface, these users may overlook essential features simply due to usability issues. An effective interface allows users to access information quickly, which means faster response times during maintenance emergencies. A well-designed layout often leads to higher levels of user satisfaction and increased adoption rates across the organization.
Moreover, modern CMMS interfaces often emphasize customizability. This means organizations can tailor their dashboards to prioritize the data relevant to their operations. This personal touch ensures that the information is not just easily accessible but also pertinent. With training that is minimal and straightforward, organizations can focus more on what matters: getting maintenance work done efficiently.
Mobile Accessibility
In today's world, mobility is crucial. A CMMS that offers mobile accessibility brings significant advantages, particularly for organizations with field personnel. Technicians can access real-time data, update work orders, or check inventory right from the warehouse or while on-site with a client. Gone are the days of waiting to return to the office to upload critical information.
Having this mobile functionality reduces response times. If a technician finds a fault during an inspection, he or she can immediately log the issue and request spare parts with a few taps on their mobile device. This immediate action can save not just time but also money. Decisions are made on-the-go, and overall operational efficiency sees a substantial uptick.
Furthermore, the ability to use a CMMS over mobile devices can mitigate communication gaps. With alerts and notifications sent straight to technicians’ phones, everyone stays on the same page, possibly avoiding misunderstandings and delays in maintenance tasks.
Data Analytics and Reporting Tools
Lastly, data analytics and reporting tools are fundamental components of a modern CMMS. These functionalities allow organizations to collect and analyze data pertaining to assets, work orders, and maintenance schedules. By leveraging this data, organizations can gain insights into their maintenance activities—spotting trends, predicting future failures, and ultimately improving decision-making.
For instance, let's say an organization notices a recurring fault in certain equipment. With integrated analytics, the CMMS can generate reports that will highlight this pattern. Managers can then decide to adjust maintenance schedules or invest in replacement parts ahead of time.
In addition, the reporting feature can help in compliance and audits. Organizations can quickly pull reports that show adherence to regulatory requirements, ensuring they stay on the right side of laws and regulations. Access to accurate, real-time data means organizations can back up claims with evidence, further enhancing their credibility.
"Data is the new oil, and having the right tools means it can fuel operational decisions." - Unknown
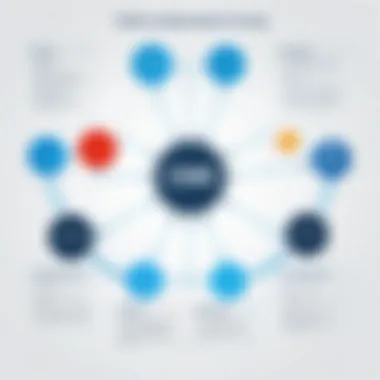
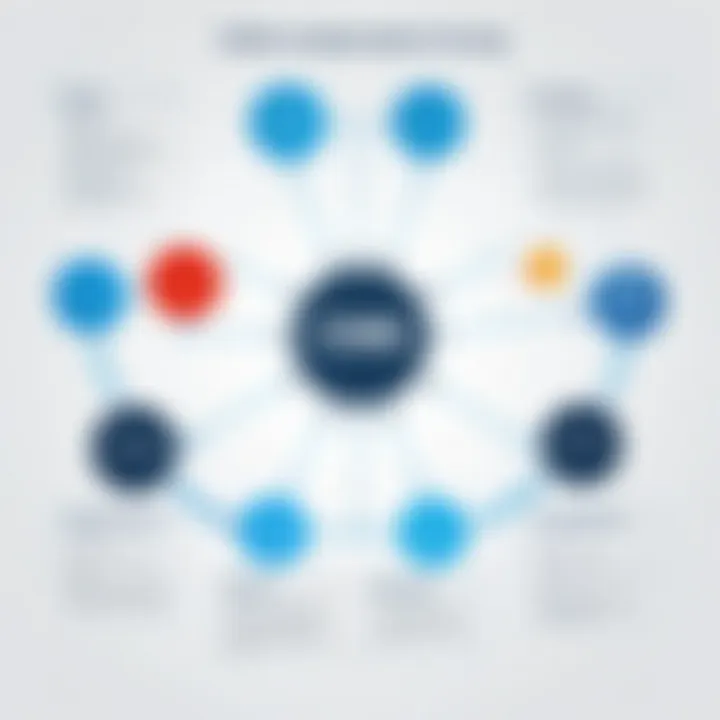
In summary, the crucial features of modern CMMS solutions lay the groundwork for enhancing maintenance management. A user-friendly interface, mobile accessibility, and strong data analytics are not just nice-to-haves—they are essential for any organization looking to thrive in a competitive landscape. As the world moves forward, these features will become even more integral to maintenance operations, setting the stage for future advancements.
Challenges in CMMS Adoption
Adopting a Computerized Maintenance Management System (CMMS) is not all rainbows and butterflies. Many organizations face hurdles that can make or break the successful implementation of such systems. This section aims to shed light on the significant challenges encountered during CMMS adoption, providing insights to help stakeholders navigate potential pitfalls. Understanding these obstacles is vital, as addressing them head-on can lead to smoother transitions, improved operational efficiency, and ultimately, a more reliable maintenance framework.
Resistance to Change
Change often comes with its own baggage, and resistance is a common companion. Employees who have been accustomed to traditional methods may feel threatened when a new system is introduced. This resistance isn't merely about disliking the new software; it reflects fear of the unknown and concerns over job stability.
For example, consider a facility manager who has been manually tracking equipment maintenance for years. The shift to a cloud-based CMMS may feel like putting their very job on the chopping block. Here, communication is key. Leaders must not only explain the benefits of the new system but also involve team members in the planning and implementation process. Showing them how the system can actually make their day-to-day tasks easier can shift perspectives.
Cost of Implementation
Budget constraints can loom large when considering a new CMMS. Beyond the initial purchase cost, various expenses may spring up like weeds in a garden. There are licenses, training programs, customization needs, and even ongoing support costs. According to some studies, organizations can expect to invest a considerable amount in both time and budget if they seek a robust and tailored solution.
Moreover, hidden costs can catch decision-makers off guard. For instance, if the chosen CMMS requires extensive data migration and legacy system integration, the financial commitment can balloon quickly. A well-prepared financial strategy that anticipates both direct and indirect costs can mitigate these concerns. It's crucial for organizations to map out these costs during the assessment phase, ensuring that they have a clear understanding of the total investment needed to get the system up and running.
Data Migration Issues
Data migration can often feel like walking a tightrope without a safety net. The process of transferring existing maintenance data into a new CMMS can be fraught with complications. Companies might grapple with incomplete records, outdated formats, or incompatible data structures. In some cases, staff must revisit and cleanse data to ensure accuracy, which can consume valuable time and resources.
Frustration may mount when there are discrepancies between legacy systems and the new software’s requirements. To tackle these challenges, organizations should not just rely on a one-size-fits-all approach. Instead, a tailored migration plan that considers the particular data hurdles faced by the company can lead to a smoother transition.
"A well-thought-out data migration strategy can save endless hours of work and lead to fewer headaches in the long run."
In summary, while the adoption of CMMS offers improved maintenance management, organizations must be prepared to confront the challenges tied to resistance to change, financial ramifications, and data migration issues. Overcoming these challenges requires thoughtful planning, effective communication, and strategic financial foresight.
Steps for Successful CMMS Implementation
Implementing a Computerized Maintenance Management System (CMMS) is not just about deploying software; it’s about reshaping operational workflows which can have profound effects on the maintenance lifecycle. When organizations approach CMMS implementation, they must consider various steps to ensure the system meets their goals effectively. A strategic implementation leads to enhanced asset reliability, reduced downtime, and overall improved maintenance management. Thus, taking a structured route is crucial.
Conducting a Needs Assessment
The first step in the implementation process involves conducting a thorough needs assessment. This stage is akin to taking a long, hard look in the mirror—organizations need to understand their current maintenance practices, challenges, and goals. What are the glaring inefficiencies? Are there repeated issues with assets? Identifying these pain points is essential.
Several elements to keep in mind during this assessment include:
- Current Maintenance Practices: Review existing processes and pinpoint what is working and what isn’t. Analyzing work order completion rates or downtime incidents can reveal significant insights.
- User Requirements: Collect feedback from maintenance staff and management alike. Their input is invaluable; after all, they are the ones who will be using the system daily.
- Compliance Needs: Understanding any regulatory requirements specific to the industry may guide system specifications.
A well-rounded needs assessment can highlight the gaps and opportunities that the organization needs to address with CMMS. This stage lays the groundwork for the next steps, ensuring the CMMS solution is tailored to meet specific expectations.
Selecting the Right CMMS Solution
Once an organization has a clear picture of its needs, the next logical step is to select the right CMMS solution. The choices can be overwhelming, and it is crucial to evaluate various options critically. Not all CMMS are created equal!
When choosing, consider the following:
- Functionality: Does the software offer the features needed, like work order management, preventive maintenance, and asset tracking? This is the meat and potatoes of any CMMS.
- Scalability: As businesses grow, so do their needs. Opt for a CMMS that can scale and adapt. Nobody wants to switch systems every few years.
- User Interface: A system with a confusing interface is a recipe for disaster. Make sure it is user-friendly—intuitive enough that employees won't need a tech degree to navigate.
- Support and Training: Evaluate the level of customer support offered by the vendor. Having accessible training resources is also critical to ensure smooth transitions.
Each organization has unique needs, so it's best to narrow down options with a checklist specific to your requirements. A well-informed choice can make all the difference in the success of CMMS deployment.
Training and Support for Users
The final, but equally critical, step involves ensuring comprehensive training and support for users. No matter how robust a CMMS may be, it is only as effective as the people using it. Training should be seen as an ongoing commitment rather than a one-off event.
Key points to consider include:
- Tailored Training Programs: Different user groups, from front-line workers to management, will have distinct training needs. Tailor sessions accordingly to maximize understanding and engagement.
- Ongoing Support: Establish a support structure for ongoing assistance—whether it’s an internal help desk or vendor support—users must feel confident they can get help when they need it.
- Feedback Mechanisms: Encourage user feedback to understand issues they face during implementation. This information can help refine processes or training materials.
As users become more familiar with the CMMS features, the chances of harnessing the full potential of the system increase significantly, ultimately driving the desired results in maintenance efficiency and operational reliability.
Successful CMMS implementation is a dynamic process that goes beyond just installation; it’s about cultivating a culture of continuous improvement.
By understanding and executing these steps, organizations can facilitate a smoother transition to their new CMMS, paving the way for better maintenance outcomes.
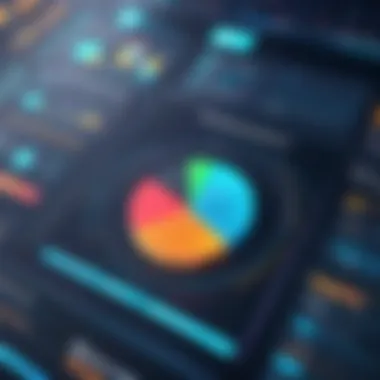
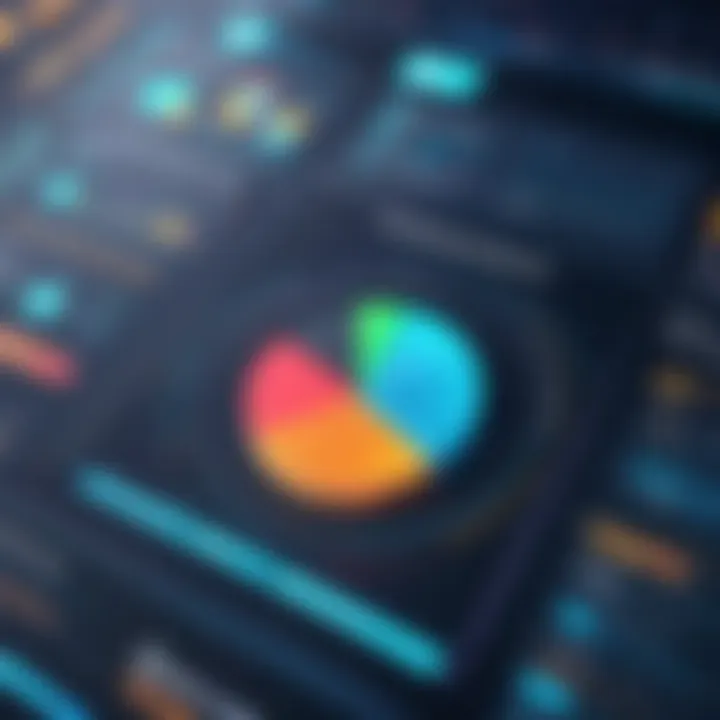
Evaluating CMMS Effectiveness
Evaluating the effectiveness of a Computerized Maintenance Management System (CMMS) serves a critical role in ensuring it meets the unique needs of an organization. It’s not just about buying software and hoping for the best; those systems require continuous review and adjustment. With businesses constantly evolving, staying ahead involves a proactive approach to assess whether the CMMS is delivering the intended benefits.
The assessment hinges on several factors, starting with Key Performance Indicators (KPIs). These are essentially the yardsticks by which organizations can measure improvements in maintenance processes. Just as a ship needs a compass to navigate, businesses need KPIs to point them in the right direction.
Additionally, implementing Continuous Improvement Strategies is vital. As the name suggests, this approach isn't a one-time deal. It's an ongoing process that allows teams to refine how they use CMMS. By constantly seeking ways to improve, organizations not just react to performance dips but also leverage insights to anticipate future needs and challenges.
"A CMMS is only as good as the insights it provides; regular evaluation transforms data into actionable strategies."
By weaving together KPIs and continuous improvement, companies can foster a culture where maintenance practices evolve. This synergy not only enhances operational reliability but also boosts overall efficiency and cuts costs in the long run. This makes evaluating the effectiveness of CMMS not just helpful but essential.
Key Performance Indicators (KPIs)
Measuring effectiveness through KPIs provides a tangible framework for assessing how well a CMMS performs. Common KPIs in maintenance management include:
- Mean Time To Repair (MTTR): It gauges the average time taken to repair an asset after a failure.
- Mean Time Between Failures (MTBF): This shows the average time between consecutive failures, giving insight into reliability.
- Work Order Completion Rate: Indicates how efficiently work orders are fulfilled over a certain period.
- Maintenance Costs: Tracking cost trends helps identify whether the expenditure aligns with budgetary constraints and whether the maintenance strategy is sustainable.
These metrics ground discussions in data rather than speculation, allowing organizations to pinpoint specific areas for improvement. Regularly examining KPIs can help establish benchmarks and clarify future goals.
Continuous Improvement Strategies
The journey of using a CMMS doesn't stop once it's implemented. After all, if a car isn't serviced regularly, it will break down eventually, right? That's where continuous improvement comes into play. Key strategies include:
- Regular Training Sessions: Keeping users updated ensures everyone is utilizing the system to its full potential.
- Feedback Loops: Cultivating a feedback culture allows staff to voice their experiences and suggest enhancements.
- Periodic System Review: Regularly assessing how the CMMS aligns with current business goals ensures it continues to provide value.
- Incorporating New Technologies: Embracing evolving technologies can enhance the capabilities of existing CMMS, driving innovation and efficiency.
Such practices can feel like running a treadmill—necessary but often overlooked. However, neglecting them could lead to stagnation, making it crucial for organizations to remain vigilant.
In sum, evaluating CMMS effectiveness via KPIs and adopting continuous improvement strategies offers organizations a roadmap to enhanced maintenance management. This ongoing evaluation cultivates resilience and adaptability in an ever-changing industry landscape.
Future Trends in CMMS Technology
The landscape of maintenance management is rapidly changing due to advances in technology. Understanding these trends is essential for any organization looking to stay ahead. Future trends in CMMS technology significantly impact how maintenance missions are carried out, helping organizations enhance their efficiency. With the integration of Internet of Things (IoT) devices and artificial intelligence, maintenance management is on the brink of a data revolution.
Integration with IoT
One of the most notable trends in the realm of CMMS is the integration with IoT. This concept refers to the interconnection of various devices and sensors that can communicate over the internet, paving the way for real-time monitoring of assets. Imagine a manufacturing plant where each piece of equipment has its own smart sensor that communicates its operational status to a central system. This sort of network allows for:
- Real-Time Data Collection: Live updates regarding asset performance and condition are transmitted directly to maintenance teams, allowing them to address issues before they escalate.
- Predictive Maintenance: By analyzing the data collected, CMMS can forecast when a piece of equipment is likely to fail. This capability means organizations can schedule maintenance before a breakdown occurs, saving time and preventing costly downtime.
- Enhanced Decision-Making: With comprehensive and accurate data at their fingertips, decision-makers can make informed choices about resource allocation and maintenance strategies.
Using IoT technology, organizations can transition from a reactive to a proactive maintenance approach. This shift not only reduces costs but also extends the lifespan of assets.
Artificial Intelligence in Maintenance Management
The infusion of artificial intelligence into CMMS is another trend that’s gaining traction. AI tools can analyze large data sets far more efficiently than humans can. By leveraging machine learning algorithms, AI can identify patterns and trends that might not be apparent to even the most experienced maintenance professionals. This progress leads to:
- Automation of Routine Tasks: AI can automate mundane tasks, allowing maintenance teams to focus on more strategic initiatives. For example, AI can schedule regular checks or generate work orders without human intervention.
- Improved Diagnostics: With AI's ability to process historical data from various sources, it can suggest the most likely reason behind a performance issue. This can drastically cut down on troubleshooting time and enhance response strategies.
- Optimized Resource Management: Organizations can align resources more effectively, ensuring that personnel and spare parts are only deployed when necessary, reducing wastage and improving logistical efficiency.
"Embracing new technologies is not a luxury but a necessity for organizations wanting to thrive in a rapidly changing environment."
Taking proactive steps towards integrating these technologies can lead to substantially improved operational reliability.
Ending
In closing, the exploration of Computerized Maintenance Management Systems (CMMS) reveals fundamental insights into their role in modern maintenance management practices. Considering the complexities of today's operational landscapes, CMMS emerges not merely as a tool but as an essential ally in optimizing maintenance strategies.
Summary of Key Points
To encapsulate the critical aspects discussed throughout this article, we can highlight several key points:
- Definition and Evolution: CMMS has evolved significantly from rudimentary systems to sophisticated solutions that incorporate mobile accessibility and data analytics.
- Core Functionality: Features like work order management, preventive maintenance scheduling, and inventory oversight enhance operational efficiency.
- Benefits: Organizations implementing CMMS experience marked improvements in productivity, reduced costs, and better compliance with standards.
- Challenges: Adoption of CMMS isn’t without hurdles such as resistance to change and data migration issues, which can derail implementation.
- Future Trends: The integration of IoT and artificial intelligence is likely to reshape maintenance management, bringing new levels of automation and intelligence to CMMS.
The above points not only serve as a reminder of the importance of CMMS but also reinforce its critical position in the ongoing quest for enhanced operational effectiveness.
Looking Ahead: The Future of CMMS in Maintenance
As we peer into the future of CMMS, it is apparent that the landscape of maintenance management will only become more dynamic. The burgeoning integration of Internet of Things (IoT) technology signifies a shift towards real-time data utilization. This will empower organizations with predictive maintenance, helping minimize downtime and streamline operations. Similarly, the incorporation of artificial intelligence can offer tailored insights, potentially revolutionizing decision-making processes.
In summary, businesses that proactively embrace CMMS technology, along with forthcoming innovations, position themselves for not just survival, but prosperity in an increasingly competitive market.
The convergence of these technologies suggests an exciting horizon ahead. For decision-makers, remaining informed and adaptable will be critical to harnessing the full potential of CMMS, paving the way for smarter, more efficient maintenance strategies. Through embracing these trends, organizations can ensure they are not just prepared for the future, but are at the forefront of it.