Unlocking the Power of Inventory Systems: A Comprehensive Guide with Examples
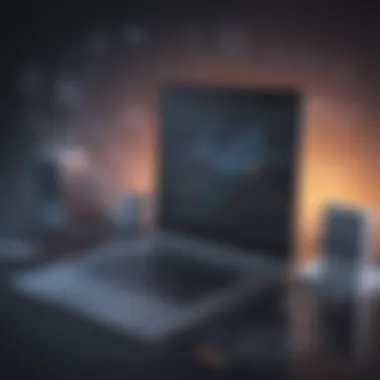
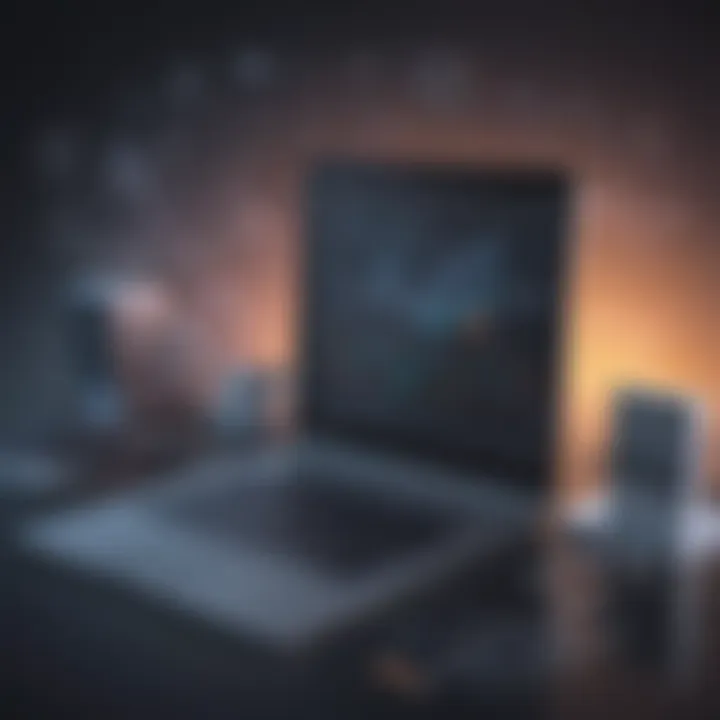
Industry Overview
To understand the importance of inventory systems in modern business operations, we must first delve into the dynamics of stock management. Effective inventory systems play a pivotal role in streamlining operations, cutting costs, and enhancing customer satisfaction. Through real-world examples and detailed explanations, readers will gain insights into the functioning and significance of inventory systems.
Industry-specific Software Market Trends
In the realm of inventory management, current trends revolve around the adoption of innovative software solutions tailored for different industries. Companies are increasingly seeking customizable inventory systems to meet their specific operational needs. Understanding these trends is essential for businesses aiming to implement efficient stock management practices.
Key Challenges in Inventory System Buying
Buyers in the inventory system market often confront challenges related to system compatibility, scalability, and data security. It is crucial to address these hurdles by selecting software providers capable of offering robust solutions that align with the business's requirements. Examining these challenges enables decision-makers to make informed choices.
Emerging Technologies Impacting Inventory Systems
Technological advancements, such as artificial intelligence and IoT integration, are reshaping inventory management practices. These innovations pave the way for more automated and data-driven approaches to stock tracking and replenishment. Keeping abreast of emerging technologies is imperative for businesses seeking to modernize their inventory control systems.
Top Software Options
Embark on a journey through the top software options available in the inventory system market. By reviewing leading software providers, comparing key features, and understanding pricing structures, businesses can make informed decisions when selecting an inventory management solution aligned with their operational objectives and budget.
Selection Criteria Considerations
Navigating the selection process for inventory software demands a keen focus on critical factors that ensure optimal compatibility and functionality. By avoiding common mistakes and accurately assessing business needs, organizations can determine the right software fit that enhances efficiency and effectiveness in stock management.
Implementation Strategies for Efficiency
Smooth implementation of software solutions is crucial for seamless integration with existing systems and processes. Best practices in training and support resources facilitate successful software deployment, ensuring operational continuity and minimizing disruptions. Following these strategies enhances the efficiency of inventory management systems.
Future Trends in Inventory Systems
Exploring the future landscape of inventory systems unveils upcoming technologies that will drive industry advancements. Predictions and recommendations enable businesses to future-proof their technology stack, aligning with evolving market trends and positioning themselves for sustained growth and competitiveness.
Introduction to Inventory Systems
In the realm of business operations, a critical element that cannot be overlooked is the management of inventory systems. Understanding inventory systems is paramount for organizations seeking to enhance their stock management efficiency. This article serves as a guide to unravel the intricate web of inventory systems, shedding light on their pivotal role in modern business practices. By delving into the depths of this topic, readers will grasp the fundamental principles and nuances essential for seamless operations in various industries.
Definition of Inventory Systems
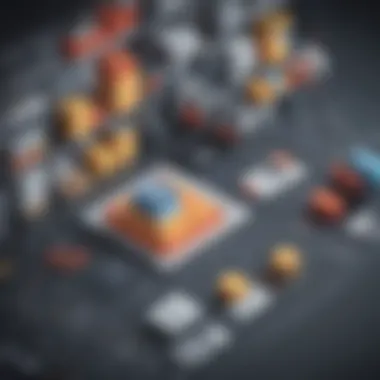
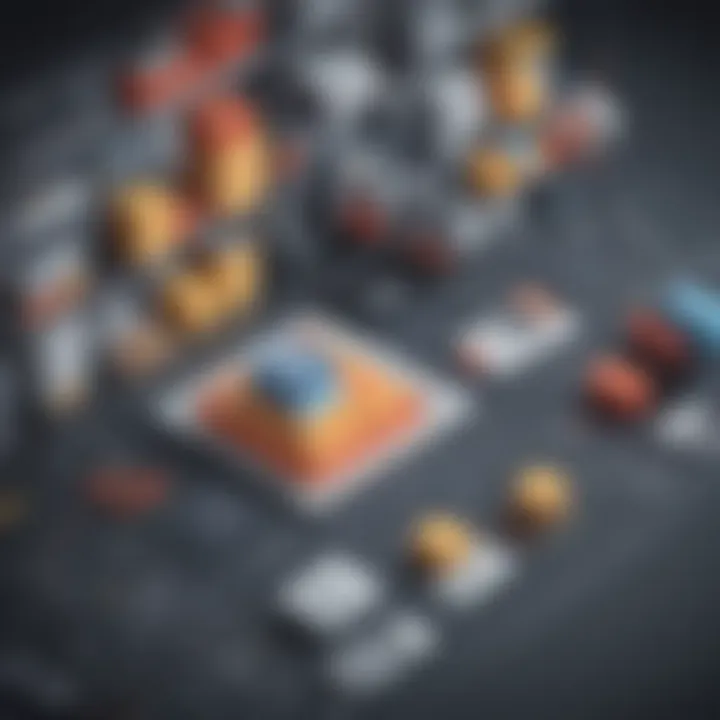
Inventory Management
Inventory management stands at the core of effective inventory systems, encompassing the supervision of stock levels, procurement, and storage within an organization's operations. The essence of inventory management lies in its ability to optimize stock flow, ensuring that products are available when needed while avoiding excess or shortage. This practice contributes significantly to streamlined operations, cost-effective stock handling, and improved customer satisfaction rates. However, challenges such as overstocking or stockouts may arise, requiring vigilant oversight to maintain equilibrium.
Stock Tracking
Stock tracking is a vital component of inventory systems, involving the monitoring and recording of stock movements throughout a supply chain. By leveraging modern tracking technologies like barcoding and RFID, businesses can efficiently track stock levels, reduce manual errors, and enhance inventory accuracy. The key advantage of stock tracking lies in its real-time visibility into inventory, enabling quick decision-making and preventing stock discrepancies. Nonetheless, investing in tracking systems demands a balance between cost and efficiency to maximize its benefits.
Supply Chain Optimization
Supply chain optimization plays a crucial role in inventory systems by focusing on aligning production, logistics, and distribution processes to enhance overall efficiency. This optimization strategy aims to minimize inventory holding costs, shorten lead times, and improve product quality. The primary benefit of supply chain optimization is the creation of a lean and responsive supply chain that adapts swiftly to market demands. However, achieving optimization may require investments in technology and training to synchronize disparate processes effectively.
Importance of Inventory Systems
Operational Efficiency
Operational efficiency is a key driver of effective inventory systems, emphasizing the need for streamlined processes and resource utilization. By employing robust inventory systems, organizations can reduce bottlenecks, eliminate wastage, and enhance productivity across various operational functions. The core advantage of operational efficiency lies in its capacity to minimize downtime and maximize output, fostering a more agile and competitive business environment. However, maintaining operational efficiency may demand continuous monitoring and analysis to pinpoint areas for improvement.
Cost Reduction
Cost reduction remains a pertinent objective for businesses, with inventory systems playing a pivotal role in managing expenditures related to stock holding and distribution. Through efficient inventory systems, organizations can minimize storage costs, lower the risk of obsolete stock, and optimize order fulfillment processes. The primary benefit of cost reduction initiatives is the enhancement of profit margins and financial viability, creating a sustainable business model. Nevertheless, cost reduction efforts must be balanced with inventory demand fluctuations and market dynamics to avoid supply chain disruptions.
Customer Satisfaction
Customer satisfaction emerges as a crucial outcome of well-managed inventory systems, as it directly impacts the quality of service and product availability for consumers. By maintaining optimal stock levels, businesses can meet customer demands promptly, reduce lead times, and enhance overall service delivery. The key advantage of prioritizing customer satisfaction within inventory systems is the establishment of brand loyalty, positive word-of-mouth, and repeat business. However, achieving high levels of customer satisfaction requires a customer-centric approach, proactive communication, and adaptability to changing consumer preferences.
Types of Inventory Systems
Perpetual Inventory System
The perpetual inventory system is a dynamic approach to stock management that maintains real-time tracking of inventory levels through continuous updates. This system offers enhanced visibility into stock movements, enables automatic reorder triggers, and minimizes the risk of stockouts. Its unique feature lies in its seamless integration with inventory tracking technologies, ensuring accurate and up-to-date stock information. The primary advantage of the perpetual inventory system is the ability to optimize stock control efficiently. However, the system's reliance on accurate data input and technology infrastructure may pose challenges if not managed meticulously.
Periodic Inventory System
In contrast to the perpetual system, the periodic inventory system involves periodic manual stock counts to determine inventory levels. This method relies on physical audits to update stock records at set intervals, offering simplicity and low initial costs. Despite its straightforward nature, the periodic system may lead to discrepancies between recorded and actual stock levels, requiring additional checks to ensure accuracy. The key advantage of this system is its ease of implementation and adaptability to small-scale inventory operations. Nonetheless, frequent stock audits may result in operational disruptions and delayed stock updates.
Just-In-Time (JIT) Inventory System
The Just-In-Time inventory system operates on the principle of receiving goods only as needed in the production process, minimizing inventory holding costs and waste. This system aims to synchronize production with demand, reduce lead times, and enhance production efficiency. Its unique feature lies in its lean inventory approach, where stock is replenished based on immediate requirements, optimizing storage space and resources. The primary advantage of the Just-In-Time system is its ability to minimize inventory carrying costs and respond swiftly to market fluctuations. However, maintaining JIT systems demands precise demand forecasting, reliable supplier networks, and robust production capabilities to avoid stock shortages or production delays.
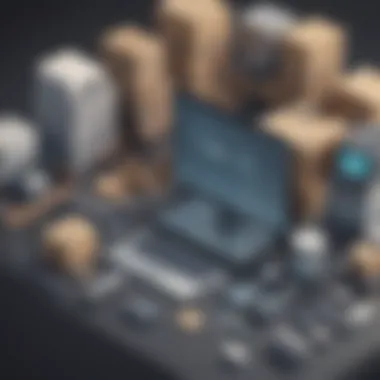
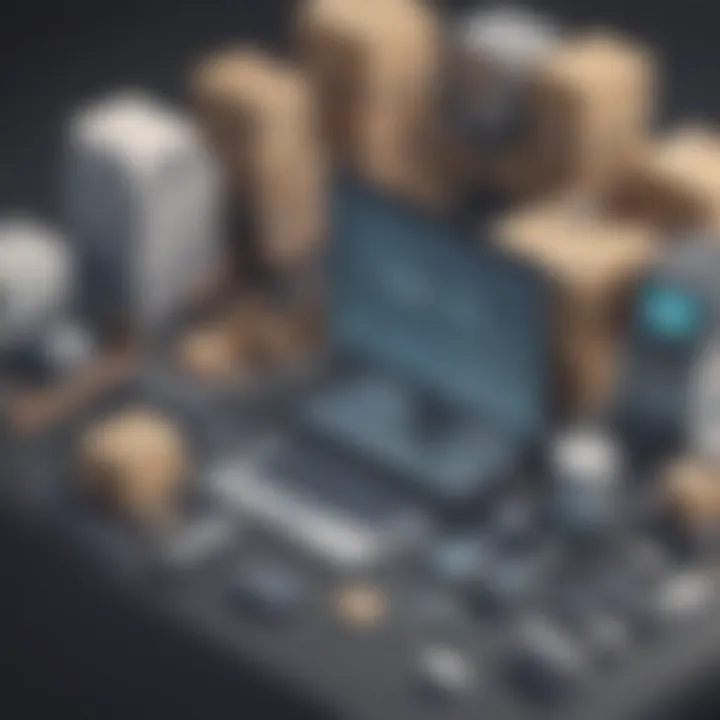
Components of Inventory Systems
Inventory systems play a pivotal role in the efficient management and tracking of stock within businesses. The components of inventory systems, including inventory control, stock valuation methods, and inventory tracking systems, are essential for optimizing operations and enhancing productivity. Effective inventory management leads to improved decision-making, reduced costs, and enhanced customer satisfaction. Understanding and implementing these components is crucial for businesses aiming to streamline their processes and achieve better outcomes.
Inventory Control
Inventory control is a fundamental aspect of inventory systems that encompasses various elements such as reorder point, order quantity, and ABC analysis. By setting optimal reorder points and order quantities, businesses can ensure a continuous supply of products while minimizing excess inventory and stockouts. ABC analysis categorizes inventory based on value and importance, allowing organizations to prioritize management efforts and resources efficiently.
Reorder Point
The reorder point signifies the inventory level at which a new order should be placed to replenish stock before running out. By calculating the reorder point accurately based on demand forecasts and lead times, businesses can avoid stockouts and maintain seamless operations. While setting the reorder point, factors like demand variability and supplier reliability must be considered to ensure timely replenishment.
Order Quantity
Order quantity refers to the number of units ordered each time inventory is replenished. Determining the optimal order quantity involves balancing carrying costs and ordering costs to minimize total inventory expenses. By employing economic order quantity (EOQ) models or quantity discounts, businesses can optimize order quantities and manage inventory efficiently.
ABC Analysis
ABC analysis classifies inventory into categories based on value, with 'A' items being the most valuable and 'C' items the least. By focusing on high-value items (A) and implementing different control measures for each category, businesses can allocate resources effectively, minimize stockouts of critical items, and reduce excess inventory of less important products.
Stock Valuation Methods
Stock valuation methods such as FIFO, LIFO, and weighted average cost determine how inventory is costed and valued on financial statements. These methods impact profitability, tax obligations, and financial reporting, influencing business decisions and performance evaluation.
FIFO (First-In, First-Out)
FIFO assumes that the first inventory items purchased or produced are the first to be sold. This method reflects the current market prices more accurately and is commonly used in industries where inventory spoilage or obsolescence is a concern. While FIFO results in higher net income during inflationary periods, it may lead to higher taxable income.
LIFO (Last-In, First-Out)
LIFO assumes that the most recently acquired inventory is sold first. This method aligns costs with current market prices but may not reflect the actual flow of goods. LIFO is suitable for businesses wishing to minimize taxable income, especially in times of rising costs or inflation.
Weighted Average Cost
The weighted average cost method calculates the average cost of inventory based on the unit costs of items available for sale. By averaging costs across all units, this method smoothens out price fluctuations and is straightforward to apply. While offering stability in cost allocation, it may not reflect the actual cost of specific inventory items, impacting decision-making.
Inventory Tracking Systems
Inventory tracking systems, utilizing technologies like barcode systems, RFID, and automated data collection, automate stock monitoring and movement tracking. These systems enhance accuracy, reduce manual errors, and improve inventory visibility, enabling businesses to make informed decisions and meet customer demands efficiently.
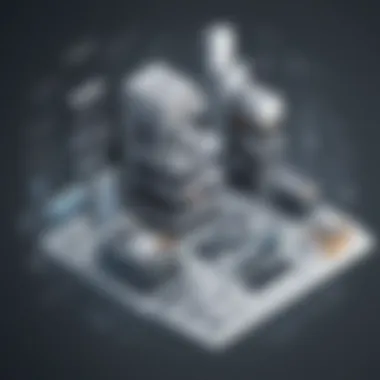
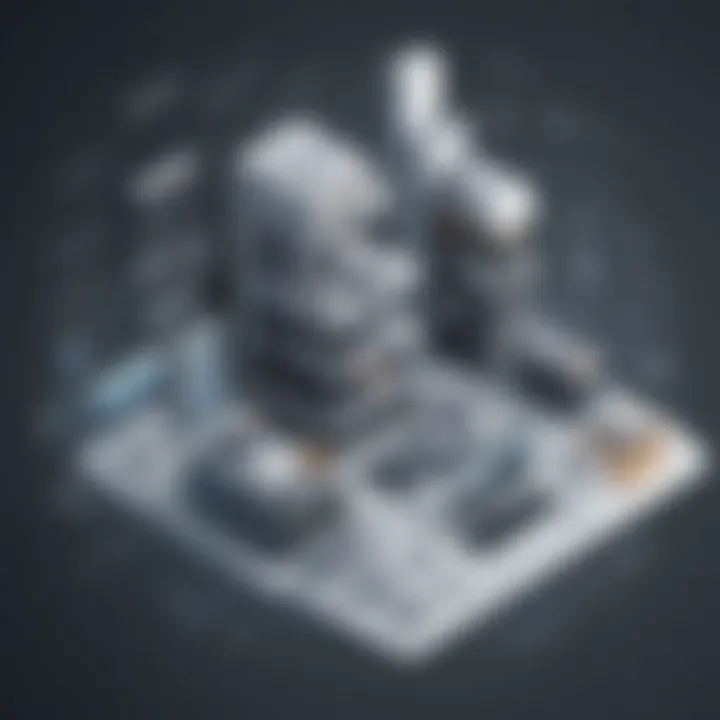
Barcode Systems
Barcode systems use unique codes assigned to products for identification and tracking. By scanning barcodes with handheld devices, businesses can update inventory records in real time, monitor stock levels accurately, and speed up operations. Barcode systems enhance efficiency, reduce data entry errors, and facilitate faster checkouts in retail settings.
RFID Technology
RFID technology employs radio-frequency signals to track and manage inventory items, offering a more efficient and automated approach compared to barcodes. RFID tags can be read wirelessly and at a distance, enabling quick inventory counts, reducing stock discrepancies, and improving inventory visibility throughout the supply chain. While RFID systems require initial investment, they provide increased accuracy and data accessibility.
Automated Data Collection
Automated data collection involves utilizing sensors, scanners, and IoT devices to capture inventory information automatically. By integrating these tools with inventory management software, businesses can streamline data collection processes, reduce human errors, and ensure real-time visibility into stock movements. Automated data collection systems enhance operational efficiency, minimize manual interventions, and support data-driven decision-making within organizations.
Examples of Inventory Systems in Practice
Inventory systems play a pivotal role in modern business operations, streamlining processes, cutting costs, and enhancing customer satisfaction. By delving into real-world examples, readers can grasp the significance of effective inventory control strategies. Understanding how these systems function in various industries provides valuable insights into optimizing stock management.
Retail Industry
Walmart's Inventory Management System
Walmart's Inventory Management System stands out for its efficiency and scalability. It leverages advanced technology to monitor stock levels, track product movements, and forecast demand accurately. The system's real-time updates enable Walmart to minimize excess inventory and reduce stockouts, ensuring customer demands are met promptly. However, the sheer size of Walmart's operations means the system must handle vast amounts of data efficiently to prevent bottlenecks and ensure seamless operations. Despite its complexity, Walmart's Inventory Management System serves as a model for cost-effective and customer-centric inventory control.
Amazon's Fulfillment Centers
Amazon's Fulfillment Centers epitomize agile inventory management practices in the e-commerce sector. Through automation and robotics, Amazon efficiently processes orders, swiftly fulfills customer demands, and maintains optimal inventory levels. The Centers' strategic location and advanced algorithms enable Amazon to offer quick deliveries and scale operations effectively during peak periods. However, reliance on automation poses challenges in adapting to sudden demand fluctuations, necessitating robust systems to ensure smooth order processing. Amazon's Fulfillment Centers set a benchmark for seamless inventory operations and customer service excellence.
Manufacturing Sector
Toyota Production System (TPS)
The Toyota Production System (TPS) revolutionized manufacturing efficiency with its emphasis on waste reduction and continuous improvement. TPS's key principle of 'Just-In-Time' production minimizes inventory holding costs, enhances production flexibility, and fosters a culture of lean operations. By empowering workers to identify and mitigate inefficiencies, TPS optimizes productivity and quality. Nonetheless, TPS requires a disciplined workforce committed to lean practices and proactive problem-solving to maintain its effectiveness in dynamic manufacturing environments. The system's structured approach to inventory control ensures operational agility and cost efficiency, making it a cornerstone of lean manufacturing.
Lean Manufacturing Principles
Lean Manufacturing Principles prioritize efficiency, quality, and customer value, shaping agile production processes. By eliminating non-value-added activities and focusing on continuous improvement, lean principles drive operational excellence and resource optimization. The principles' emphasis on standardization and waste reduction fosters a sustainable manufacturing ecosystem. However, implementing and sustaining lean practices necessitate comprehensive training, robust performance measurement, and organizational alignment. Despite the challenges, the benefits of lean manufacturing principles in enhancing productivity and competitiveness are undeniable.
Hospitality and Service Industry
Hotel Inventory Management Software
Hotel Inventory Management Software streamlines reservations, optimizes room allocation, and tracks inventory usage seamlessly. By integrating with booking platforms and monitoring guest preferences, this software enhances operational efficiency and revenue management. Its analytics tools provide valuable insights for catering, pricing strategies, and inventory optimization. However, deploying and maintaining the software requires adequate training, technical support, and data security measures. The software's ability to centralize inventory data and automate manual tasks elevates hotel operations and enriches the guest experience.
Restaurant POS Systems
Restaurant POS Systems automate order processing, streamline billing, and manage inventory in a dynamic dining environment. These systems enhance workflow efficiency, minimize errors, and expedite meal service. Their reporting capabilities aid in tracking sales trends, managing stock levels, and optimizing menu offerings. Yet, integrating POS systems with existing restaurant operations demands careful customization, staff training, and responsive technical support. The systems' role in enhancing customer satisfaction through prompt service and accurate order fulfillment underscores their value in modern restaurant management.