Understanding Process Manufacturing Systems: Key Insights
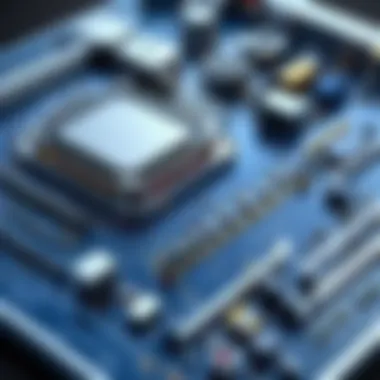
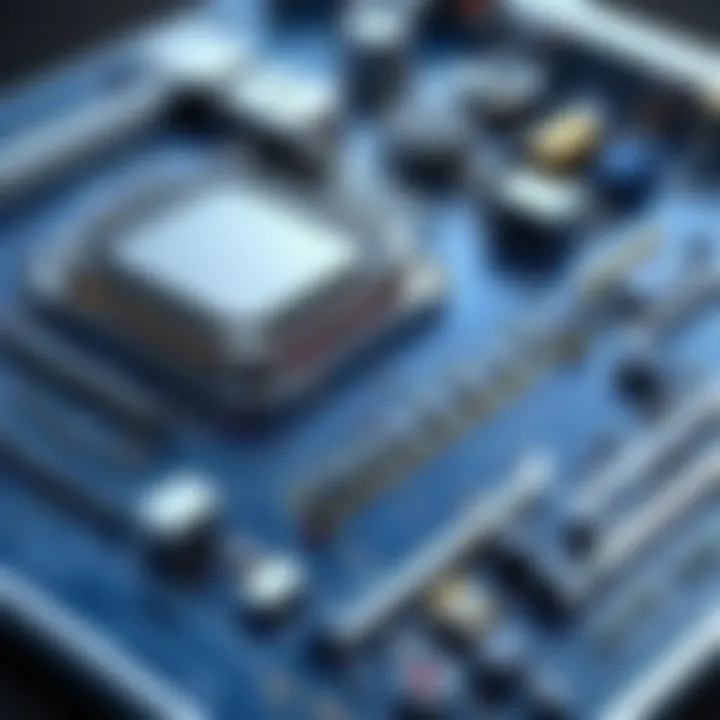
Intro
Process manufacturing systems are a critical backbone for numerous industries. They offer the framework that allows organizations to create goods through specific procedures. Unlike discrete manufacturing, where individual items are made, process manufacturing involves the creation of products that are typically made from combining various raw materials. This article will delve deeply into the intricacies of process manufacturing systems, exploring their significance, components, and the challenges businesses encounter.
Understanding process manufacturing systems can empower decision-makers and industry professionals with the knowledge to navigate the complexities of modern manufacturing. As these systems continue to evolve, trends emerge that shape the future of production. By fully grasping the principles, functions, technology, and implementation techniques, stakeholders can optimize their operations significantly.
Industry Overview
The domain of process manufacturing is distinguished by several vital components that characterize its complexity and necessity in contemporary commerce. These systems drive operations within sectors such as food and beverage, chemicals, pharmaceuticals, and more. Each of these industries faces unique challenges but follows the same fundamental principles of process manufacturing.
Current Trends in the Industry-specific Software Market
As businesses seek to enhance their operations, industry-specific software solutions have gained prominence. Key trends observed include:
- Increasing integration of AI for predictive analytics, enhancing efficiency.
- Adoption of cloud-based solutions, facilitating accessibility and collaboration.
- Focus on customization to meet unique organizational needs.
Key Challenges Faced by Buyers in the Industry
Organizations often face difficulties when selecting suitable systems. Some common challenges are:
- Onerous cost considerations during procurement.
- Insufficient compatibility between new and existing systems.
- Lack of skilled staff to manage new software tools.
Emerging Technologies Impacting the Industry
Innovation is at the forefront, with several technologies shaping the future of process manufacturing systems, including:
- Internet of Things (IoT) for improved monitoring and control.
- Blockchain for enhanced transparency in supply chains.
- Advanced analytics for real-time decision making.
Top Software Options
The growing market means there are numerous software options available. Leading software providers feature unique strengths and offerings.
Review of Leading Software Providers in the Industry
Prominent software solutions include:
- SAP Integrated Business Planning
- Oracle Fusion Cloud
- Siemens Opcenter
Feature Comparison of Top Software Solutions
Examining the features is essential for establishing suitability. Notable features often assessed include:
- Real-time data analytics
- Flexibility and scalability
- Compliance management tools
Pricing Structures of Different Software Options
Pricing models typically vary among vendors, impacting decision-making:
- Subscription-based pricing aligns costs with usage.
- Perpetual licenses can appear costly but offer long-term commitment benefits.
Selection Criteria
Choosing the right software is complex and critical. Various factors come into play:
Important Factors to Consider When Choosing Software
- Alignment with business goals.
- Usability for staff at different skill levels.
- Vendor support reputation.
Common Mistakes to Avoid During the Selection Process
- Ignoring support and training resources.
- Overlooking long-term upgrade costs.
- Underestimating integration challenges.
How to Determine the Right Fit for Your Business Needs
Conduct a thorough analysis of needs—identify both current processes and future vision before making a commitment. Focus on flexibility, as future growth might necessitate a scalable solution.
Implementation Strategies
Implementing process manufacturing systems requires a strategic approach. Best practices can minimize disruptions.
Best Practices for Smooth Implementation of Software Solutions
- Develop a clear project plan with timelines.
- Ensure all stakeholders are engaged and informed.
- Set measurable goals and performance metrics.
Integration with Existing Systems and Processes
Compatibility with legacy systems is critical. Ensure that data migration plans are realistic and supported by effective execution strategies.
Training and Support Resources for Successful Deployment
An essential part of implementation is effective training. Focus on offering comprehensive resources for various user levels, organizing regular feedback sessions for continual improvement.
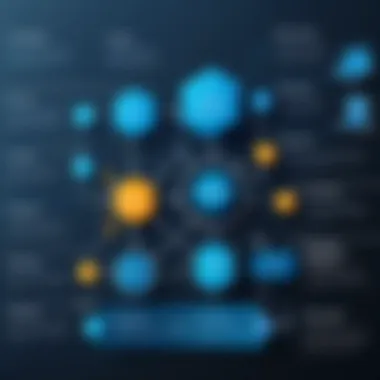
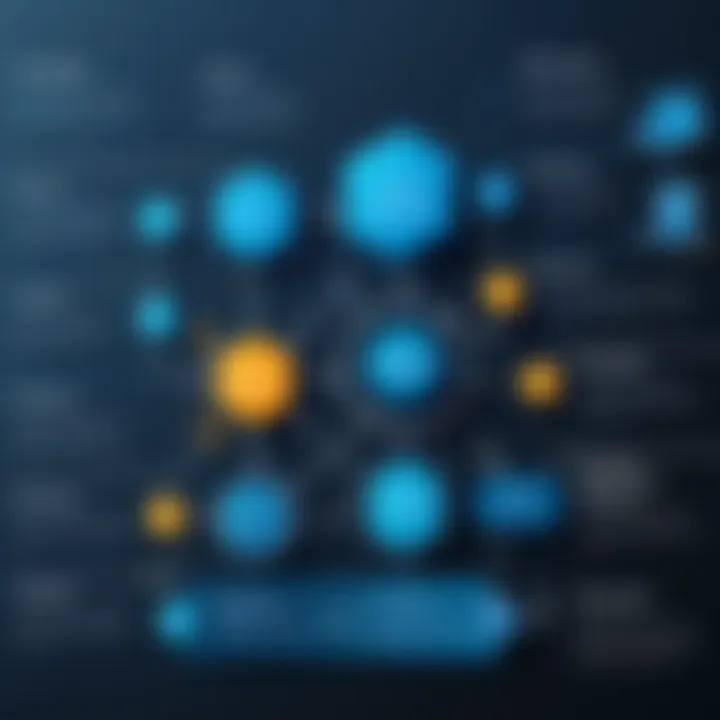
Future Trends
Understanding future trends will equip organizations for what’s next in process manufacturing technology.
Predictions for the Future of the Industry-specific Software Landscape
Predictions include:
- Growth in cloud-based applications enhancing remote monitoring capabilities.
- Seamless integration of artificial intelligence into everyday operations.
Upcoming Technologies Shaping the Industry
Monitor progress in several technologies:
- Augmented Reality (AR) for workforce training.
- Predictive maintenance tools to reduce downtime.
Recommendations for Future-Proofing Your Technology Stack
Businesses need to integrate technologies that provide adaptability over time. Evaluate technology regularly and stay informed of market trends, ensuring solutions continue to serve organizational goals.
In an ever-evolving marketplace, proactive engagement and analysis of emerging technologies can provide significant competitive advantage for players in the manufacturing sector.
Preamble to Process Manufacturing Systems
Process manufacturing systems are an integral part of the modern industrial landscape. They provide the framework for producing products that are fundamental to society, from chemicals to beverages. Understanding these systems enables industry leaders to optimize workflows, ensuring efficiency and quality control. This section will delve deeper into the definition and significance of process manufacturing systems, highlighting their advantages and the critical considerations when implementing them.
Defining Process Manufacturing
Process manufacturing involves the use of machinery, labor, and technology to produce products that are usually in bulk or follow a specific sequence. This contrasts with discrete manufacturing, where individual items are created and finished separately. Common industries using process manufacturing include food and beverage, chemical production, and pharmaceuticals. Here, products are often substances that undergo continuous transformation, which can involve mixing, heating, or other intricate procedures.
The success of process manufacturing lies in controllability and repeatability. By establishing standardized processes, companies aim to minimize variations and ensure product consistency. Automation also plays a critical role, allowing manufacturers to scale operations efficiently.
Distinction from Discrete Manufacturing
Differentiating between process and discrete manufacturing is key for decision makers. Process manufacturing produces continuous outputs, meaning the emphasis is on flow and transformation rather than discrete parts. A significant characteristic of this model is that once a batch is created or the process is started, it is often complex or impossible to revert the product to raw materials. For example, in oil refining, hydrocarbons must be through various linked processes to create the end products.
In contrast, discrete manufacturing facilitates the production of identifiable items, like cars or machinery, which can be easily counted and stored. Each process step generally culminates in a standalone product that can be inspected and modified easily.
By understanding these distinctions, organizations can adopt the most suitable methods for their operational needs, enhancing productivity and managing resource allocation. This awareness is crucial for the development of an effective manufacturing strategy in any competitive industry.
Key Components of Process Manufacturing Systems
Understanding process manufacturing systems involves that key components function as the backbone. Each component is critical to ensure a well-streamlined operation. These elements, including raw material management, process control systems, and differing processing methods, affect overall efficiency, quality, and costs.
Raw Material Management
Effective raw material management is paramount in any process manufacturing setup. This area focuses on the optimal use of materials from procurement to storage and eventually to the production line. Raw material decisions affect lead times, investment costs, and the entire production timeline.
A well-defined management system enhances visibility across stocks. Tracking the materials ensures that materials are available when needed and that wastage is minimized. Efficient raw material management also enables companies to optimize supplier relationships, promoting better terms and reducing costs.
Challenges include securing quality inputs and managing unforeseen shortages. Therefore, investing in robust systems to anticipate demands can mitigate notable risks that compromise schedules. The practice of just-in-time inventory is one approach adopted for maximizing efficiency while slashing excess inventory.
Process Control Systems
The role of process control systems cannot be understated in maintaining consistency and quality. Such systems utilize various tools and technologies to monitor and manage production processes dynamically. Consequently, they ensure the finished product meets industry standards while preserving your resources.
Designed to respond to operational variables, these control systems include sensors, control panels, and software applications. Not only do they aid in implementing automation, but they also support advanced diagnostics, real-time monitoring, and performance analysis. This constant visibility helps managers and professionals to pinpoint potential issues early on, minimizing risks and enhancing safety.
Integration with existing systems presents its impacts. Many companies face significant challenges, such as escalating complexity and costing time for detailed data management. An interface that consolidates several functionalities simplifies how teams engage accordingly.
Batch Processing vs.
Continuous Processing
Batch processing and continuous processing serve different manufacturing needs in the realm of process manufacturing. Each method comprises distinctive operational philosophies that work best under varying circumstances.
Batch processing involves creating products in distinct groups or lots. This allows for flexibility and quick adjustments based on immediate demand fluctuations, facilitating lower setup costs. Precision matters, assuring companies remain attentive to quality for each batch. However, transitions between different batches lead to downtime, negatively impacting overall efficiency.
On the other hand, continuous processing aims for persistent production, enhancing throughput and lowering operational costs over time. However, while this approach yields significant efficiencies, setup changes can be less responsive, and any conditions affecting the quality may create distressing cascading consequences. Thus, selecting between the two lies in understanding a business' specific production goals.
To encapsulate, insight into each component leads to informed decisions governing system design, resource optimization, and ultimately market competitiveness.
The Role of Technology in Process Manufacturing
Technology plays a pivotal role in shaping process manufacturing systems today. The integration of advanced tools enhances productivity, improves efficiency, and fosters innovation. To remain competitive, companies need to leverage these transformative technologies proactively. This section highlights crucial technological aspects influencing this field, including automation, data analytics, and software solutions. Each component helps organizations streamline operations and respond to market dynamics effectively.
Automation and Robotics
Automation in process manufacturing streamlines tasks that were traditionally manual. It minimizes the potential for human error and increases production rates. Robots, equipped with artificial intelligence, can operate in complex environments. They can adapt to various product changes with remarkable precision. For example, industries producing chemicals or beverages benefit from automated dispensing solutions that enhance accuracy.
Implementing automation requires careful planning. Organizations must consider the costs associated with initial capital and ongoing maintenance. Although investment can be significant, the long-term benefits often outweigh these costs.

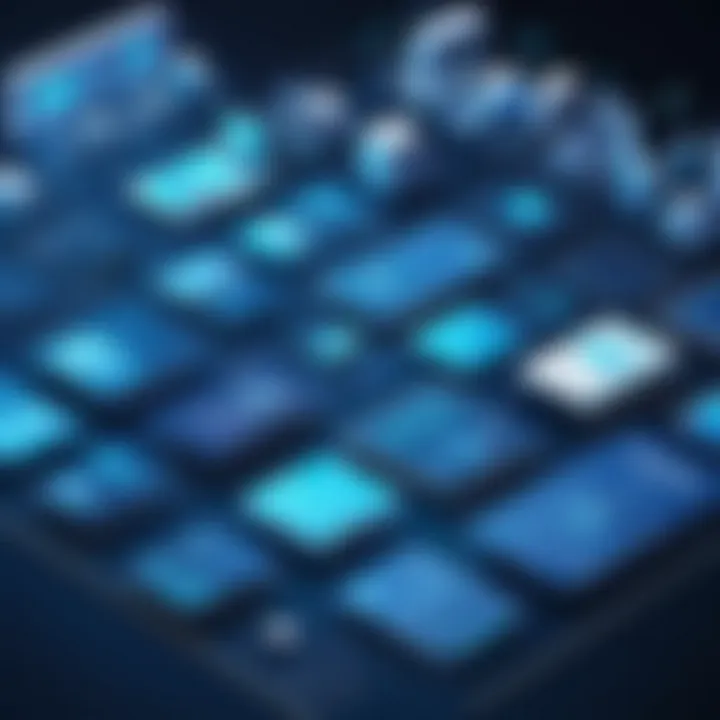
Some main advantages of automation include:
- Reduced operational costs due to decreased labor requirements.
- Elevated work safety and health standards, keeping workers free from hazardous environments.
- Increased efficiency, as machines produce consistently at high speeds without breaks.
Data Analytics and IoT Integration
In today's competitive landscape, data analytics serves as a valuable asset in process manufacturing. Companies collect massive amounts of data through operations. By implementing advanced analytics, organizations can transform raw data into insightful information, leading to better decision-making.
Internet of Things (IoT) also plays a key role in this equation. Machine-to-machine communication facilitates real-time monitoring of the manufacturing process. Integration of IoT devices helps companies track equipment health and performance. Ongoing analysis predicts maintenance needs, capturing opportunities for optimization. Some tangible benefits include:
- Enhanced resource management through monitoring usage patterns.
- Rapid response to anomalies, thus decreasing downtime significantly.
- Better insights into consumer behavior, enabling more effective delivery of goods.
Software Solutions for Process Management
Good software solutions are essential for effective process manufacturing. They provide a framework for managing operations smoothly. Solutions such as manufacturing execution systems (MES) enhance process management securely.
When selecting software, companies must validate the suitability for their specific environment. The right solution can optimize production runs, track inventory levels, and foster high levels of collaboration among teams. Here are several noteworthy aspects of software solutions:
- Improved data visibility across the manufacturing supply chain.
- Facilitated compliance with industry regulations by documenting processes and outcomes.
- Customized reporting helps stakeholders broadly understand and track progress.
Implementing technology within process manufacturing paves the way for operational excellence audits.
Benefits of Implementing Process Manufacturing Systems
Process manufacturing systems are critical for success in various industrial landscapes. When organizations adopt these systems, they unlock a range of benefits that include enhanced operational efficiencies, cost savings, and improved quality standards. This section explores these advantages in detail.
Enhanced Efficiency and Productivity
Process manufacturing systems streamline operations. They integrate various elements of production, allowing for smoother workflow. Automation plays a vital role here. For instance, tasks that were once performed manually can now be executed by machines.
Automation reduces human error, speeding up the overall process significantly. The capability to monitor and control operations in real-time enhances decision-making. Real-time data enables managers to identify bottlenecks quickly and remove them efficiently. Mass production becomes easier, allowing companies to meet demand without sacrificing quality.
- Fast Production Cycles: Reduction in cycle times through automation.
- Resource Optimization: Effective use of materials results in lesser waste.
- Flexible Operations: Ability to switch between various production lines without delay.
As a result, efficiency and productivity see drastic improvements.
Cost Reduction Opportunities
Cost efficiency is perhaps one of the most driving factors for companies considering a shift to process manufacturing systems. By optimizing resource utilization through various methodologies like lean manufacturing principles, organizations can greatly decrease operational costs.
Implementing automated reporting systems further diminishes costs related to labor. When redundancy is cut down, budgets can allocate funds to critical areas. Moreover, buying raw materials in bulk becomes possible when production cycles are consistent, decreasing the average material expense.
Benefits include:
- Lower Operating Costs: Reduction in overhead through automation.
- Material Savings: Maximize the usage of raw materials, consuming less lead time.
- Improved Negotiation Power: Solid data on production needs leads to better terms with suppliers.
Therefore, cost reduction emerges as a prominent benefit, allowing organizations to invest in future technological advancements.
Quality Control and Consistency
Quality control directly influences a company’s reputation and financial success. Process manufacturing systems ensure high levels of consistency across production lines. Defined recipes and processes create uniformity in end products.
Regular performance metrics utilize data analytics to identify areas that may lead to deviations in quality. This supports a disciplined approach to producing items while maintaining standards. By reducing variability in production, companies can enhance customer satisfaction.
- Standard Operating Procedures: Established guidelines ensure that every batch contains identical quality.
- Real-Time Monitoring: Data gathered during production enables instant quality control adjustments.
- Traceability: Any defects identified can be traced back easily, simplifying corrective actions.
In summary, these systems positively impact quality control and consistency. By focusing on maintaining high standards, businesses foster trust and loyalty among clients, further enhancing operational success.
The advantages of implementing effective process manufacturing systems are numerous and important for staying competitive in today’s market.
To explore further resources, you can visit Wikipedia or Britannica.
Challenges in Process Manufacturing Systems
Understanding the challenges inherent in process manufacturing systems is vital for industry professionals seeking effective solutions. Challenges jeopardizing seamless operations can arise anywhere. By identifying key challenges, organizations can devise strategies to overcome obstacles and enable a smoother path toward successful implementation.
Integration with Existing Systems
The entry point for many organizations into process manufacturing systems often involves integration with their established infrastructure. Inefficient data flow and lack of compatibility with older systems present considerable hurdles. Balancing legacy systems containing historical data is essential while ensuring operational continuity. To achieve integration successfully, businesses may need to:
- Assess current systems for capability and limitations.
- Like strategizing on middleware solutions may ease communication across multi-vendor environments.
- Design interfaces allowing seamless data transfers between systems while maintaining data integrity.
This integration should reflect companies’ specific operational needs while enhancing productivity.
Skill Gap in Workforce
Another pressing concern revolves around the skill gap within the workforce. Advanced manufacturing systems incorporate sophisticated technologies, demanding employees to possess not only basic operational skills but also an understanding of data analysis and technology insights.
Organizations can adopt several strategies to address this challenge:
- Implement ongoing training programs focusing on honing technical skills.
- Collaborate with educational institutions to bridge the hiring gap and encourage skill acquisition.
- Promote knowledge sharing within existing teams can help cultivate a more knowledgeable workforce
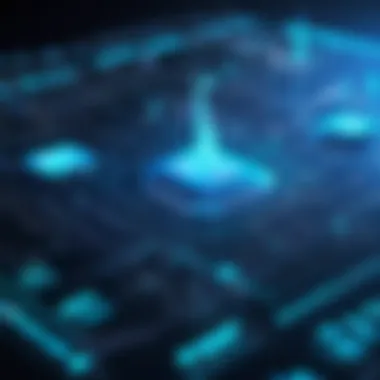
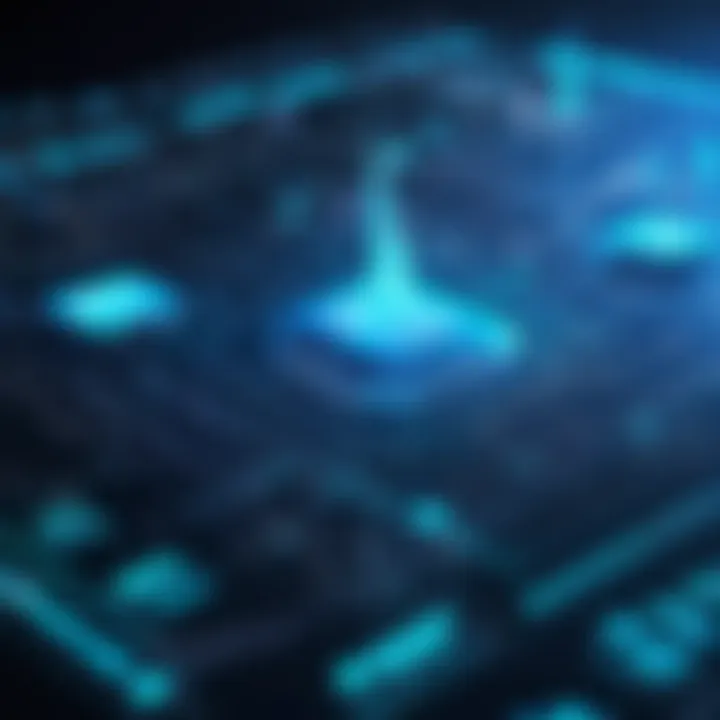
A skilled workforce is imperative for successfully navigating technological complexities inherent in modern process manufacturing.
Regulatory Compliance and Standards
Regulatory frameworks guide the manufacturing industry, ensuring quality, safety, and environmental responsibility. Adhering to industry regulations becomes particularly complex in process manufacturing, which often transcends multiple jurisdictions and standards. Failure to comply may lead to significant penalties and interruptions in operations.
Here are some ways to manage regulatory compliance effectively:
- Establish clear guidelines outlining specific regulatory requirements based on product types and geographical locations.
- Regularly audit processes to ensure they abide by current regulations.
- Cultivate a culture of compliance with designated roles spearheading continuous monitoring of regulatory changes.
Regulatory knowledge is essential to protect businesses from potential risks and maintain a positive reputation among stakeholders.
Understanding and addressing these challenges positions firms for success in an ever-evolving landscape of process manufacturing. The need for robust integration, skilled professionals, and compliance awareness cannot be overstated.
Best Practices for Effective Process Manufacturing
Implementing process manufacturing systems efficiently requires adherence to several best practices. These practices play a vital role in achieving manufacturing goals while maximizing productivity and minimizing waste. This section discusses various elements integral to improving process manufacturing outcomes.
Establishing Clear Objectives
Defining clear objectives is the bedrock of successful process manufacturing systems. Objectives provide a roadmap, guiding teams to align their efforts efficiently. Setting objectives often incorporates aspects like cost reduction, quality improvement, and productivity enhancement. When objectives are clear, every team member understands their role in the process. Here are some important points to consider:
- SMART Goals: Objectives should be Specific, Measurable, Achievable, Relevant, and Time-bound.
- Regular Review: Periodic reviews help adjust objectives in line with changing market conditions or technological advances.
- Stakeholder Involvement: Involving team members in defining objectives boosts morale and enhances accountability.
Continuous Improvement and Lean Strategies
Continuous improvement acts as a cornerstone for sustaining efficiency in proces manufacturing. Lean strategies often aim to minimize waste, improve flow, and enhance collaboration. By focusing on continuous enhancement, companies can create sustainable advantages in a competitive landscape. Consider the following approaches:
- Identifying Waste: Use tools like Value Stream Mapping to pinpoint inefficient areas within the processes.
- Kaizen Techniques: Implement methodologies like Kaizen for incremental, continuous transformations.
- Performance Metrics: Establish key performance indicators (KPIs) to monitor success, ensuring alignment with overall business strategies.
AdOPting lean strategies can reformat how organizations view waste, directing efforts toward a more productive, quality-driven environment.
Regular Training and Development
The workforce remains the most critical asset in any manufacturing system. Thus, regular training ensures that employees are equipped with current skills and knowledge in process manufacturing systems. Effective training can lead to reduced errors and an increase in employee confidence. Some strategies for implementing a robust training program include:
- Skill Assessment: Periodic evaluations can determine knowledge gaps, informing training initiatives.
- Interactive Learning Platforms: Use digital learning tools for immersive, engaging training experiences.
- Dual Apprenticeships: Foster skill development by pairing less experienced employees with seasoned professionals for hands-on learning.
Regular training intergrates knowledge continually, enhancing adaptability within a practice that thrives on precision and consistency in manufacturing.
Key Takeaway: Best practices in proccess manufacturing not only enhance operational performance but ultimately contribute to a company's long-term health and profitability.
Future Trends in Process Manufacturing Systems
As industries adapt to new challenges and consumer demands, process manufacturing systems evolve accordingly. Recognizing the future trends in this area is crucial for decision-makers, as these developments shape efficiency, sustainability, and technological adoption in the manufacturing landscape. By understanding these trends, organizations can maintain a competitive edge and optimize their processes to meet future needs. This section explores significant future trends including sustainability practices, the role of Artificial Intelligence (AI) and machine learning, and advancements in remote monitoring and control systems.
Sustainability and Green Manufacturing
The growing emphasis on sustainability cannot be overstated. Stringent regulations and rising public awareness are fostering a shift towards more eco-friendly practices in manufacturing. Process manufacturers are increasingly tasked with reducing their ecological footprint.
- Implementing energy-efficient processes reduces waste and aids in cost control.
- Utilization of renewable resources ensures supply chain resilience and promotes recycling initiatives.
- Technologies such as low-impact production methods further support sustainability goals.
Efforts here are often twofold. Not only do these practices meet regulatory demands, they also cater to consumer preferences for sustainably sourced products. Organizations pursuing these innovations can enhance their brand reputation. This positions them favorably in a market that increasingly prioritizes environmental consciousness.
Adoption of AI and Machine Learning
Artificial Intelligence and machine learning provide powerful tools for process manufacturers. By utilizing complex algorithms, organizations can analyze vast datasets to drive decision-making.
- Implementation of predictive maintenance minimizes downtime and maximizes resource allocation.
- AI-powered analytical models support supply chain optimization, ensuring materials and labor are used efficiently.
Furthermore, machine learning enables a deeper understanding of production trends, ultimately aiding in product quality control. Companies already adopting such technologies distinguish themselves in tight markets. It allows for not just improved production but also enhanced product offerings that align more closely with consumer demands.
Remote Monitoring and Control Advancements
The COVID-19 pandemic highlighted vulnerabilities within many industries, leading to greater interest in remote solutions. Advances in remote monitoring and control technology allow manufacturers to maintain operations while ensuring personnel safety.
- Sensor technologies enable real-time data capture, helping managers track operational parameters from afar.
- Cloud computing ensures that data is accessible anytime while supporting scalability benefit and minimized infrastructure costs.
Additionally, remote control capabilities grant operators the freedom to execute tasks without being physically present. This development is valuable not just for efficiency but is also crucial in maintaining health protocols in manufacturing environments. Companies leveraging these advancements often achieve increased flexibility in operations and reduce risk across processes.
Essence of Future Trends: Embracing these future trends is not merely an adaptation but rather a necessity to thrive in an increasingly competitive market. Successful integration of environmental, technological, and remote capabilities will undoubtedly shape the future process manufacturing landscape, encouraging an approach driven by mindfulness, responsiveness, and innovation.
The End
The conclusion of this article is vital as it encapsulates the essence of understanding process manufacturing systems. It is essential for comprehensible engagement, ensuring that readers can synthesize the insights gained throughout the discussion.
Summary of Key Insights
In brief, process manufacturing systems play a crucial role in multiple employments, from food and beverage to pharmaceuticals. Key aspects include:
- Principles and Objectives: Process manufacturing emphasizes efficiency, consistency, and peak performance.
- Technological Advancements: The integration of smart technologies promotes automation and enhances safety while lowering operational costs.
- Continuous Improvement: Organizations are urged to adopt lean strategies for optimal performance and better resource allocation.
Analyzing these highlights helps stakeholders assess the strengths and weaknesses of their current processes.
Final Thoughts on Process Manufacturing Systems
In concluding this exploration, process manufacturing systems demand careful thought and clear strategies towards implementation. As industries evolve, maintaining a focus on sustainability and technological integration should be at the forefront of priorities.
The ability to adapt and innovate will decide the long-term success of organizations in any sector using these systems. Understanding their framework is not just beneficial but necessary for thriving in today’s fast-paced commercial landscape. Additionally, companies must stay informed of emerging trends to actively leverage new enhancements. Insights gathered herein establish a robust foundation for decision-makers. They can now better navigate the intricate world of process manufacturing systems.