In-Depth Analysis of Leading Warehouse Management Systems
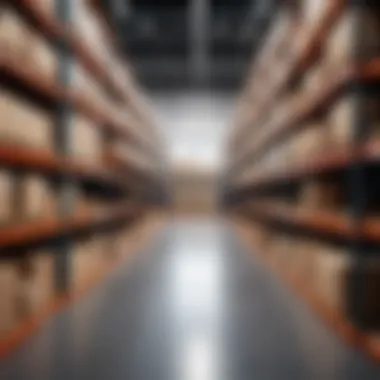
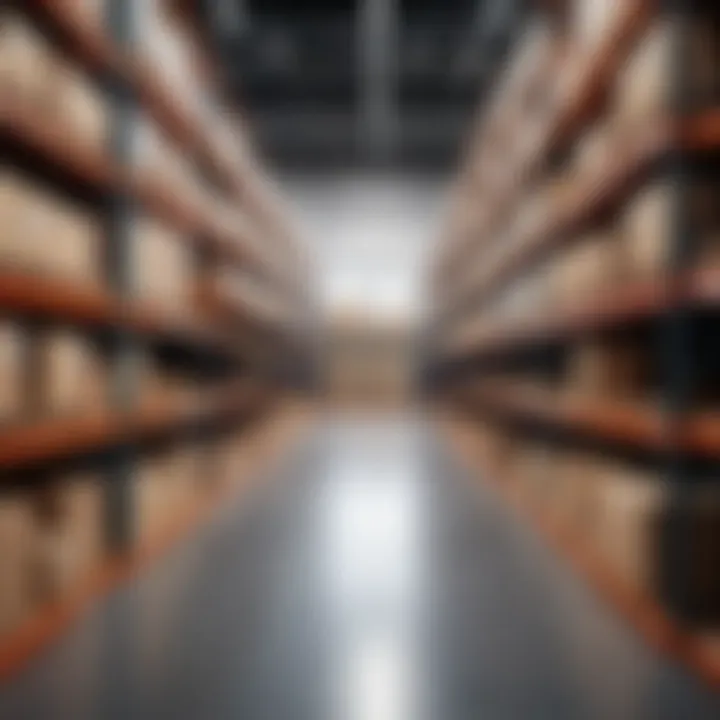
Industry Overview
The warehouse management system (WMS) industry plays a critical role in the logistics and supply chain sectors. This market has evolved significantly over the years due to technological advancements and changes in consumer expectations. Companies are looking for more efficient ways to manage their inventory and streamline operations. As such, the demand for robust WMS solutions has never been higher.
Current Trends in the Industry-specific Software Market
Organizations are increasingly adopting automation and artificial intelligence within their WMS. These technologies help in optimizing inventory management and streamlining the order fulfillment process. Additionally, cloud-based solutions have gained traction, allowing users to access data remotely while benefiting from real-time updates. This shift signifies a broader trend towards mobility and flexibility in warehouse operations.
Key Challenges Faced by Buyers in the Industry
Despite the advancements, buyers encounter several challenges while selecting a WMS. One major obstacle is the integration with existing systems. Many companies rely on legacy software which can be complex and costly to update. Furthermore, understanding the total cost of ownership is often opaque, leading to overspending or inadequate budgeting for future upgrades and support.
Emerging Technologies Impacting the Industry
Emerging technologies like Internet of Things (IoT) and machine learning are beginning to reshape the warehouse management landscape. IoT devices can monitor inventory levels in real-time, providing invaluable data for decision-making. Machine learning algorithms can analyze past data to predict future demand, allowing businesses to adjust their strategies proactively.
Top Software Options
In this section, we will explore the leading warehouse management system vendors to provide an overview of their offerings, features, and market positioning.
Review of Leading Software Providers in the Industry
There are several key players in the WMS space. Prominent vendors include SAP, Oracle, and Manhattan Associates. These companies offer comprehensive solutions that cater to various business sizes and needs. Smaller providers like Fishbowl and Zoho also hold significant market share among smaller enterprises, appealing to budget-conscious clients.
Feature Comparison of Top Software Solutions
When comparing software solutions, it is essential to consider functionalities such as inventory tracking, order management, and reporting features. Leading systems often come equipped with features such as:
- Real-time data access to track inventory levels
- Automated replenishment functions to maintain stock levels
- Analytics and reporting tools for better decision-making
Pricing Structures of Different Software Options
Pricing strategies vary widely among vendors. Major systems, like SAP, typically employ a subscription-based model, while others may charge based on the number of users or transactions. Understanding these pricing structures is crucial for companies to assess which option aligns with their budget and operational needs.
Selection Criteria
Identifying the right WMS solution requires careful evaluation of several factors.
Important Factors to Consider When Choosing Software
Key factors include:
- Integration capabilities with existing systems
- Scalability to grow with the business
- User-friendliness for employees at all levels
Common Mistakes to Avoid During the Selection Process
Common errors include failing to involve key stakeholders in the decision-making process or underestimating the importance of training and support. Ensuring that all relevant departments are onboard can lead to a smoother transition.
How to Determine the Right Fit for Your Business Needs
Conducting a thorough requirements analysis is vital. Organizations should outline their specific needs and expectations from a WMS before shortlisting vendors. Including a pilot program can also help assess whether the selected software meets operational demands.
Implementation Strategies
Transitioning to a new WMS can be challenging. However, adequate planning can ensure a seamless integration.
Best Practices for Smooth Implementation of Software Solutions
To guarantee success, follow these practices:
- Develop a clear action plan with timelines
- Allocate a dedicated team to manage the transition
Integration with Existing Systems and Processes
Integration is a critical step. Companies must prioritize compatibility checks with current systems to avoid disruptions.
Training and Support Resources for Successful Deployment
Providing comprehensive training programs will equip employees with the necessary skills to utilize the new system effectively. Supporting resources should also be readily available to address any issues during and after implementation.
Future Trends
The WMS industry is likely to undergo further transformations as technology advances.

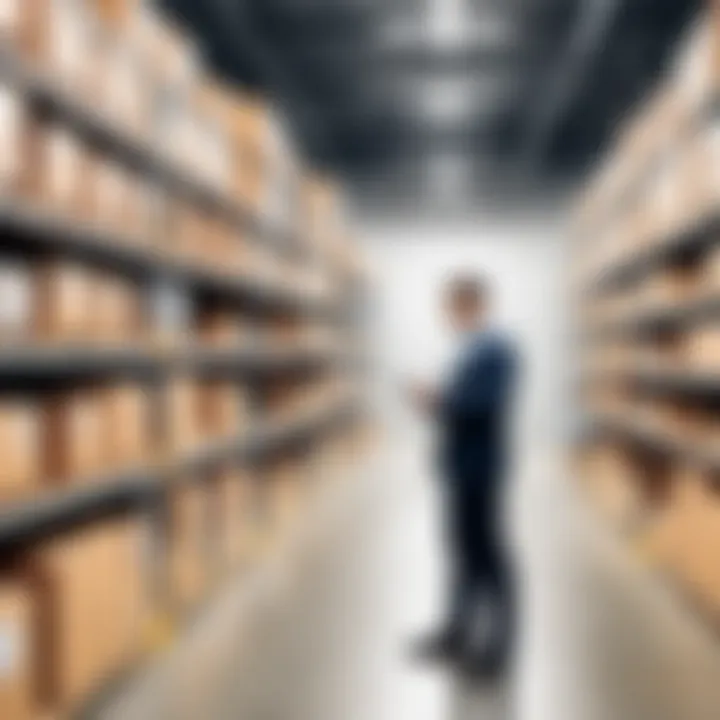
Predictions for the Future of the Industry-specific Software Landscape
Expect an increase in AI and automation, leading to more efficient and intelligent management solutions. Businesses will focus on enhancing user experiences with intuitive interfaces.
Upcoming Technologies Shaping the Industry
Technologies such as blockchain are being explored for tracking and securing transactions, promising enhanced traceability and transparency.
Recommendations for Future-Proofing Your Technology Stack
Choosing vendors that prioritize innovation and support for emerging technologies will help organizations maintain relevance in a rapidly evolving market.
Preface to Warehouse Management Systems
Warehouse Management Systems (WMS) stand as critical components in the modern supply chain. They are software solutions designed to optimize warehouse operations, track inventory levels, and manage the flow of goods within a facility. Understanding WMS is essential for organizations aiming to enhance their logistical efficiency and maintain competitive advantages in a dynamic marketplace.
Definition and Scope
A Warehouse Management System refers to a suite of software tools that allows businesses to control and manage warehouse operations. This includes tasks such as receiving inventory, storing products, picking goods for shipment, and tracking the overall movement of products. The scope of WMS encompasses basic functionalities like inventory control, as well as advanced features such as yard management, labor management, and task optimization.
The implementation of a WMS can result in increased accuracy in stock management, reduction in operation costs, and improved customer satisfaction by ensuring timely fulfillment of orders. Furthermore, WMS may serve various sectors, including retail, manufacturing, and e-commerce, making it a versatile tool in logistical operations.
Importance in Supply Chain Management
The role of Warehouse Management Systems in supply chain management cannot be overstated. As businesses face growing demand for faster deliveries and more efficient inventory practices, a robust WMS provides the necessary tools to address these challenges.
Key benefits include:
- Improved Inventory Management: WMS improves visibility into inventory levels and locations, reducing the chances of stockouts or overstock situations.
- Enhanced Operational Efficiency: Automated processes and real-time data access streamline operations, allowing staff to focus on value-added tasks rather than manual tracking and data entry.
- Cost Reduction: A well-implemented WMS minimizes labor costs and optimizes storage space utilization, leading to overall cost savings for the organization.
- Data-Driven Decision Making: By providing analytics and reporting capabilities, WMS empowers decision-makers with insights into performance metrics, helping organizations make informed strategic choices.
As stated in industry reports, “Investing in advanced WMS technology can lead to significant ROI, especially as e-commerce continues to transform logistical demands.” This highlights the necessity for businesses to not only adopt WMS but also adapt to the ongoing changes in supply chain dynamics.
Market Overview of WMS Vendors
The market overview of Warehouse Management System (WMS) vendors forms a critical part of understanding how these systems operate in today's fast-paced supply chain environment. An analysis of the current landscape offers insights into the performance and capabilities of various providers. This knowledge is useful for decision-makers who seek a system that meets specific operational needs and helps streamline processes. Moreover, understanding market dynamics aids in recognizing opportunities for growth as well as challenges in vendor selection.
Current Trends and Developments
Recent trends in the warehouse management sector highlight several important developments:
- Increased Automation: The rise of automation technologies is redefining warehouse operations. Many vendors now offer advanced robotics and automated retrieval systems that enhance efficiency.
- Cloud-Based Solutions: There is a strong shift towards cloud-based WMS solutions. These systems offer scalability and ease of access, allowing companies to adapt more quickly to market changes.
- Real-Time Data Analytics: The integration of data analytics tools enables enhanced visibility and decision-making. This trend allows organizations to analyze warehouse performance in real-time, leading to optimized inventory management.
- Mobile Solutions: The growing use of mobile devices in warehouses is changing how teams interact with WMS. Many vendors are now providing mobile-friendly interfaces that facilitate on-the-go access to WMS functions.
"Cloud technology and automation are at the forefront of transforming warehouse management systems, offering unprecedented flexibility and efficiency to businesses."
These trends indicate a significant evolution occurring within the warehouse management space, with vendors increasingly focusing on technology that provides deep integration with the entire supply chain.
Key Players in the Market
The landscape of WMS vendors is competitive, with several significant players dominating the market. Key vendors include:
- SAP: Known for its robust solutions and deep integration capabilities, SAP remains a leader. Its WMS offers comprehensive functionalities suited for large enterprises.
- Oracle: Oracle’s Supply Chain Management Cloud provides a complete view into the supply chain, with features heavily focused on data integration and analytics.
- Manhattan Associates: With a strong focus on multi-channel fulfillment, Manhattan's WMS is favored by companies tackling complex supply chain challenges.
- Softeon: This vendor provides flexible solutions that cater to various industries, making it a popular choice for those seeking customizable systems.
- HighJump: A strong player, especially for mid-sized businesses, HighJump offers cost-effective solutions with a focus on usability.
Each of these players brings unique strengths to their offerings. Understanding their market positioning and functionalities assists businesses in selecting the most appropriate WMS vendor to fit their needs.
Criteria for Evaluating WMS Vendors
Choosing the right warehouse management system (WMS) vendor is a critical decision for any organization. This choice directly impacts efficiency, productivity, and ultimately, business success. Evaluating WMS vendors requires a clear understanding of specific criteria that align with organizational goals. It is essential to focus on scalability, integration capabilities, and user experience. Each of these elements plays an integral role in ensuring that the WMS can meet current demands while adapting to future growth.
Scalability and Flexibility
Scalability refers to the ability of the WMS to handle increasing volumes of work. Flexibility, on the other hand, involves the system's capacity to accommodate various types of operations and processes. A scalable WMS is vital for organizations looking to grow. It allows for expansion without the need for an entirely new system. For instance, a retail business that experiences seasonal peaks must have a solution that can adapt without sacrificing performance.
Flexible systems can adjust to changes in warehouse layouts, product lines, and deployment strategies. These adaptable features are essential when considering long-term investments. Planning for growth requires analysis of how well a WMS can support an expanding or evolving operational scope.
Integration Capabilities
Integration capabilities are crucial for maintaining operational coherence. The WMS must work seamlessly with other software such as Enterprise Resource Planning (ERP) systems, Customer Relationship Management (CRM) tools, and other supply chain management solutions. Poor integration can lead to data silos and inefficiencies, undermining the potential benefits of implementing a WMS.
A system that allows for easy data exchange enhances overall supply chain visibility. This leads to better decision-making. When evaluating a WMS, it is essential to inquire about its compatibility with existing systems and the ease with which it can integrate new tools and technologies as needs evolve.
User Interface and Usability
The user interface (UI) and overall usability are often overlooked areas in the evaluation process. An intuitive UI can significantly reduce training time and enhance user satisfaction. Systems that are user-friendly minimize errors and enhance productivity. A complex system with a steep learning curve can frustrate employees and often lead to lower morale and productivity.
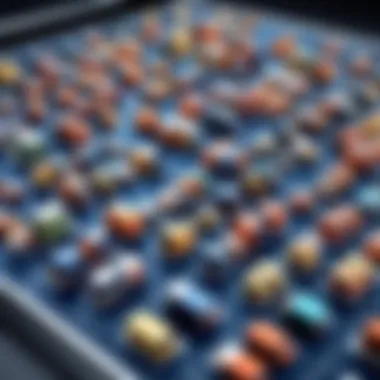
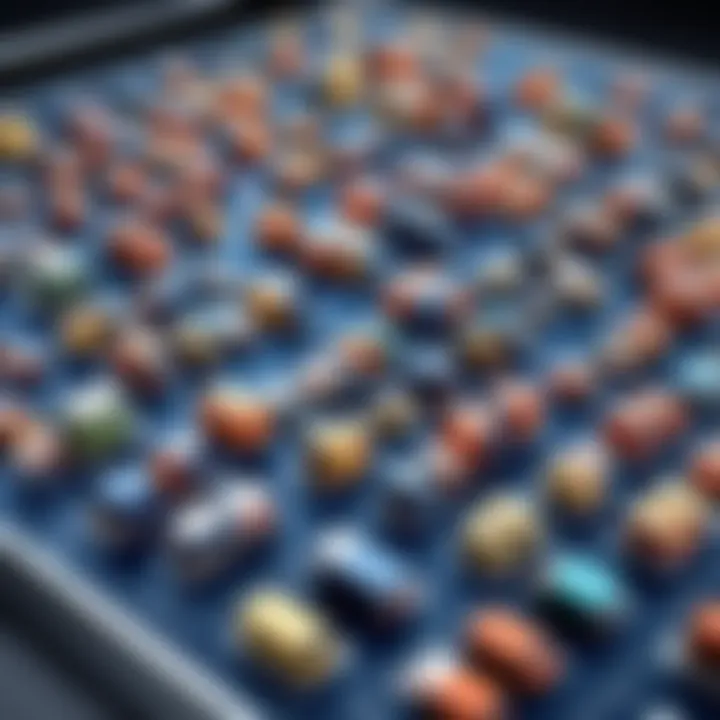
It is also important to consider the support provided for users. Well-designed onboarding processes and ongoing training resources can make a significant difference in how effectively a team utilizes the WMS. Decision-makers should prioritize systems that offer a positive user experience as this will have lasting implications for workforce efficiency and engagement.
Top WMS Vendors and Their Solutions
Understanding the offerings of various warehouse management system (WMS) vendors is pivotal for organizations striving to enhance their supply chain operations. Each vendor presents unique functionalities catered to different operational needs, affecting the decision-making process for potential users. The selection of a suitable vendor can lead to significant improvements in inventory accuracy, operational efficiency, and overall cost reduction. This section examines leading WMS vendors, their features, strengths, and positions in the market, highlighting the essential elements decision-makers need to consider when choosing a WMS solution.
Vendor A: Features and Benefits
Vendor A has emerged as a frontrunner in the WMS space, combining robust functionalities with user-centered design. Among its key features are real-time inventory tracking and automated replenishment processes. These capabilities ensure that businesses maintain optimal stock levels, thereby reducing the risk of stockouts.
Benefits of using Vendor A include:
- Seamless Integration: The system easily connects with existing enterprise resource planning (ERP) and supply chain solutions.
- User-Friendly Interface: The intuitive interface minimizes the learning curve for staff, facilitating faster adoption.
- Customizable Reporting: Users can generate tailored reports that provide insights into performance metrics, inventory levels, and operational efficiency.
Organizations leveraging Vendor A often see an increase in order accuracy, which helps build customer trust and satisfaction.
Vendor B: Strengths and Weaknesses
While Vendor B has notable strengths, it is essential to weigh these against its weaknesses. This vendor is well-regarded for its robust analytics capabilities. Users can access comprehensive data reporting that aids in informed decision-making. The strengths include:
- Scalability: Ideal for both small and large businesses, adapting quickly to evolving needs.
- Strong Customer Support: Vendor B provides extensive support options, including training and troubleshooting guides.
However, challenges exist:
- High Initial Costs: The upfront investment can be significant, which may turn away budget-constrained organizations.
- Complex Setup: Some users find the initial implementation process requires substantial time and effort to configure effectively.
Overall, Vendor B is suitable for organizations that prioritize data insights and have the resources to invest initially.
Vendor C: Market Positioning
Vendor C distinguishes itself in the market with a focus on cloud-based solutions. As businesses continue to migrate to the cloud, Vendor C's offering positions it strategically amidst competitors. Their cloud-based WMS facilitates remote access and real-time updates, allowing teams to operate effectively from various locations.
Key aspects of Vendor C's market positioning include:
- Cost-Effective: Because of its cloud model, companies can reduce expenditures related to on-premise infrastructure.
- Frequent Updates: Users benefit from continuous software updates, ensuring they always have access to the latest features and security protocols.
- Flexibility: It offers an adaptable framework that can grow alongside businesses, accommodating a wide range of warehousing needs.
Cost Considerations in WMS Selection
Cost is a critical factor when selecting a Warehouse Management System (WMS). Understanding the financial implications of adopting a WMS solution is essential for decision makers. It is not only about the initial payment but also about the long-term financial commitments involved. A comprehensive evaluation of costs includes both the upfront investment and ongoing expenses, such as maintenance, upgrades, and training.
Organizations must consider how these costs align with their operational goals. A detailed analysis will ultimately help businesses to avoid unforeseen expenses that can arise after implementation.
Initial Investment vs. Total Cost of Ownership
When discussing WMS cost, the distinction between initial investment and total cost of ownership (TCO) is significant. Initial investment refers to the upfront costs that companies face when setting up a WMS. This includes the purchase price of the software, hardware-specific needs, and installation fees.
On the other hand, the total cost of ownership encompasses all costs over the lifetime of the system, including:
- Ongoing support and maintenance fees
- Training and onboarding for staff
- Costs related to upgrades or system enhancements
Understanding TCO provides a clearer picture of what to expect financially. Many organizations might be enticed by a low initial investment but fail to account for the hidden costs that may surface later. Therefore, a thorough assessment is vital to ensure there are no financial surprises as the system evolves.
Return on Investment (ROI) Analysis
Evaluating the return on investment is another crucial part of selecting a WMS. A robust ROI analysis helps businesses determine if a WMS will deliver financial benefits that outweigh its costs.
To conduct an effective ROI analysis, organizations should consider:
- Efficiency Gains: Improved processes can lead to lower labor costs and reduced errors.
- Inventory Accuracy: Better inventory management minimizes losses and enhances customer satisfaction.
- Order Fulfillment Rates: Faster and more accurate fulfillment can drive revenue gains through better service delivery.
Ultimately, a positive ROI demonstrates that a WMS not only pays for itself over time but also adds significant value to the organization. As businesses evaluate WMS solutions, they must prioritize systems that align with their financial strategies, ensuring both short-term and long-term gains are realized.
Case Studies of Successful WMS Implementation
The significance of analyzing successful warehouse management system (WMS) implementations cannot be overstated. Case studies provide a window into how organizations across various industries have leveraged WMS technology to solve specific challenges, optimize processes, and improve overall efficiency. This section presents insights into industry-specific applications and encapsulates lessons learned from real-world scenarios. Through case studies, decision-makers can glean actionable insights that may inform their choices as they navigate the complex landscape of warehouse management.
Industry-Specific Applications
Different industries face unique challenges related to warehousing and logistics. A tailored approach to WMS implementation can significantly enhance operational efficiency. For example, in the retail sector, WMS plays a crucial role in managing stock levels and fulfilling orders swiftly. One case involves a leading global retail chain that implemented a WMS solution tailored for real-time inventory management. The result was a 30% reduction in stock discrepancies, leading to improved customer satisfaction.
In the pharmaceutical industry, compliance is paramount. Here, a case study involving a prominent pharmaceutical distributor highlights how their WMS not only optimized distribution but also ensured strict adherence to regulatory requirements. By automating tracking and reporting processes, they achieved a 40% reduction in compliance-associated errors.
In the manufacturing sector, integrating WMS with production schedules can streamline processes. One manufacturer successfully adopted WMS to sync its inventory with production lines, thus reducing lead times by 25%. This integration allowed the company to respond flexibly to changes in demand while minimizing wasted resources.
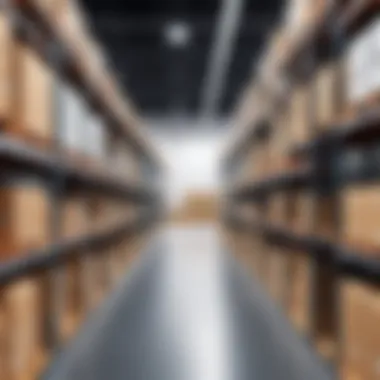
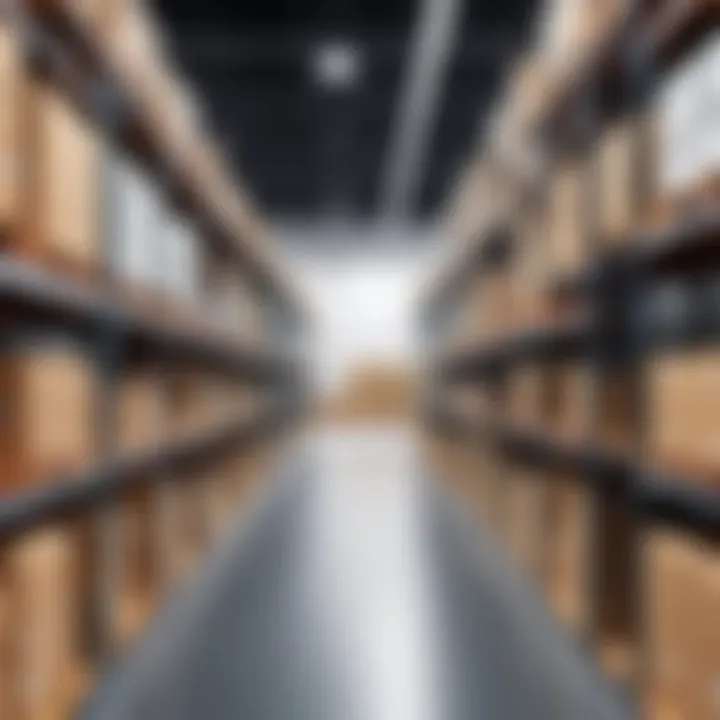
Lessons Learned from Real-World Scenarios
The insights gained from successful WMS implementations offer several key lessons for organizations considering similar projects. First, it is critical to ensure stakeholder involvement from the onset. Engaging various departments, including IT, operations, and finance, fosters a more comprehensive design and implementation process.
Second, organizations should prioritize modular implementation. A phased approach enables them to assess the efficacy of the WMS iterate and refine before a full roll-out. This iterative process minimizes disruption to daily operations.
"Case studies show how tailored implementations drive return on investment, mitigate risk, and ensure sustainability in operations."
Moreover, continuous training and support are essential. Companies that invested in training their staff reported a significant drop in resistance to change. Employees were more adept at using the system, resulting in improved output.
Lastly, it is crucial to maintain a focus on data analysis. Using a WMS not only improves operational efficiency but also generates valuable data. Organizations that routinely analyze this data can make informed decisions regarding inventory management and warehousing strategy.
In summary, case studies reveal the transformative potential of WMS technologies across various industries. By learning from others and understanding the specific applications relevant to their sectors, organizations can avoid common pitfalls and maximize their investment in warehouse management system solutions.
Challenges in Choosing the Right Vendor
Choosing the right warehouse management system (WMS) vendor is a pivotal decision in any supply chain operation. The implications of this choice extend far beyond the selection of a software provider—it affects efficiency, cost management, and ultimately, customer satisfaction. This section delves into the primary challenges encountered in this selection process, illuminating the critical considerations decision-makers must confront.
Technology Compatibility Issues
One of the foremost challenges is technology compatibility. Organizations often operate within a complex web of existing systems including enterprise resource planning (ERP) software, transportation management systems (TMS), and various other operational tools. Therefore, when assessing potential WMS vendors, it is essential to verify that the proposed solutions align seamlessly with these existing systems.
Incompatibility can lead to significant disruptions and increased costs. For instance, data silos may form if the WMS cannot effectively share information with other systems. This can result in operational inefficiencies and hinder supply chain visibility. Vendors should be evaluated based on their compatibility with current systems and the ease of integration. This assessment might involve technical demonstrations or pilot programs to ensure that the data flow remains uninterrupted and efficient across platforms.
Vendor Stability and Support
Another notable challenge is vendor stability and support. Businesses inherently face risks when they engage with technology providers. A vendor that lacks stability may be unable to support their software adequately, particularly in times of need. An important consideration for decision-makers is the long-term viability of the vendor. Start-ups in the WMS space may have innovative solutions but could lack necessary financial backing or market experience. Meanwhile, established vendors may offer reliability but could potentially be slower to innovate.
Support services are equally important. A vendor needs to provide robust customer support, ensuring timely assistance when issues arise. An absence of comprehensive support can lead to extended downtime and financial losses. Therefore, it's beneficial to investigate a vendor's track record in providing assistance and resolving compatibility problems.
While evaluating these aspects, decision-makers may consider the following points:
- Financial Health: Review the vendor's financial stability to gauge longevity.
- User Reviews: Seek feedback from current users on customer support experiences.
- Service Level Agreements (SLAs): Examine the SLAs offered by vendors for clarity on support guarantees.
"Effective vendor selection is not just about features but also about the relationship and assurance they can provide as partners in your supply chain journey."
In summary, organizations must navigate compatibility issues and vendor reliability carefully. These challenges require a thorough evaluation to promote sustainable performance in warehouse management systems. The decision should be informed by the organization's unique requirements and current technological landscape.
Future Trends in Warehouse Management Systems
Warehouse management systems (WMS) are evolving continuously. Understanding future trends is vital for organizations aiming to stay competitive in the fast-paced supply chain environment. By focusing on emerging technologies and methodologies, businesses can leverage these trends to enhance operational efficiency, reduce costs, and improve customer satisfaction.
Artificial Intelligence and Automation
Artificial intelligence (AI) is transforming warehouse operations. It streamlines processes by minimizing human intervention. Automation technologies, such as robotics and machine learning, are increasingly integrated into WMS.
Benefits of AI in warehouse management include:
- Improved Inventory Accuracy: AI tools analyze data to maintain optimal inventory levels, reducing overstocking and stockouts.
- Enhanced Order Fulfillment: AI algorithms can predict purchasing trends, allowing for more accurate order processing.
- Efficient Labor Management: Automation reduces repetitive tasks, enabling warehouse staff to focus on more strategic activities.
Adopting AI requires careful consideration of implementation costs and necessary employee training. However, the potential gains are significant, as these technologies can lead to faster, more reliable operations.
Evolution of Cloud-Based Solutions
Cloud-based solutions offer flexibility and scalability. Organizations increasingly prefer these systems due to their ability to adapt quickly to changing market demands. Updates and integrations are easier to manage, minimizing downtime and disruptions.
Key advantages of cloud-based WMS include:
- Cost-Effectiveness: Reducing the need for expensive on-premises hardware and software.
- Accessibility: Stakeholders can access the system from anywhere, facilitating better decision-making.
- Real-Time Data: Cloud systems enable real-time data sharing. This leads to improved collaboration among supply chain partners.
Businesses should assess their existing infrastructure to effectively transition to cloud-based solutions. Challenges such as data security and compliance must be addressed, but the benefits are clear.
"The integration of AI and cloud-based technology is not just a trend, but a shift in how warehousing will operate in the future."
To summarize, the future trends in warehouse management systems point towards increased automation and the adoption of cloud technologies. These developments can significantly enhance warehouse efficiency, lead to better resource management, and align operations with contemporary business demands. Decision-makers must remain proactive in assessing these trends to strategically position their organizations for future success.
Finale and Recommendations
Conclusion and recommendations play a crucial role in synthesizing the information presented in this article. As organizations navigate the complex landscape of warehouse management systems, it becomes essential for decision-makers to grasp the nuances in vendor offerings and how these align with their operational needs. The insights shared in this analysis aim to inform strategic choices and foster informed decision-making.
Importance of Conclusion and Recommendations
By offering tailored recommendations, businesses can ultimately minimize pitfalls associated with software selection. Decision-makers should consider factors like scalability, integration capabilities, and user-friendliness when choosing a WMS. These elements can significantly impact operational efficiency and, thus, the overall success of the supply chain.
The decisions made today regarding warehouse management software will have long-lasting effects. Therefore, thorough research and evaluation are paramount. Vendors vary widely in features, support, and pricing models. This underscoring the necessity of aligning the software capabilities with specific business requirements.
"Selecting the right warehouse management system is not just about the software itself; it is about optimizing the entire supply chain process to ensure success in a competitive landscape."
Strategic Considerations for Decision Makers
- Understand Organizational Needs: Every business has unique requirements. Before making a decision, leaders should conduct a needs assessment that identifies the specific functionalities crucial for their operations.
- Evaluate Vendor Reputation: Researching vendor history, customer reviews, and case studies can provide substantial insight into their reliability and service quality. Popular vendors often have established reputations that reflect their industry standing.
- Consider Future Needs: A forward-thinking approach is necessary. Scalability should be a key consideration. Vendors offering flexibility in features and pricing can make it easier for companies to adapt as they grow.
- Check for Integration Capabilities: The chosen WMS will likely need to interact with other systems. Therefore, decision-makers should verify that the WMS can seamlessly integrate with existing infrastructure to avoid complications down the road.
- User Training and Support: Efficient onboarding processes, user training programs, and quality customer support can greatly affect how well a system is implemented and used. It is advisable to confirm what support options are included in the contract before finalizing the selection.
By taking these strategic considerations into account, companies will be better poised to choose a warehouse management system that streamlines their supply chain operations and drives overall efficiency.