Exploring Warehouse Management Systems: A Detailed Comparative Analysis
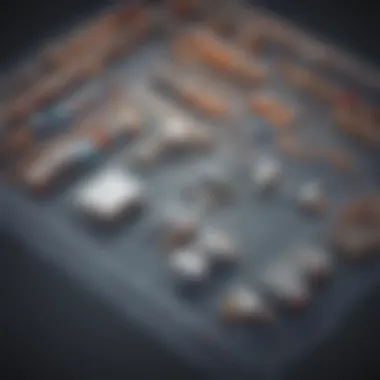

Industry Overview
Warehouse management systems (WMS) play a crucial role in the logistics and supply chain industry, optimizing operations and enhancing efficiency. Current trends in the industry-specific software market indicate a shift towards cloud-based solutions and automation. Key challenges faced by buyers in the industry include the complexity of choosing the right system that aligns with their specific requirements and budget constraints. Emerging technologies such as artificial intelligence and Internet of Things are making a significant impact, revolutionizing how warehouses are managed.
Top Software Options
When exploring warehouse management systems, it is essential to review leading software providers in the industry. Conducting a feature comparison of top software solutions enables decision-makers to evaluate functionalities critical to their operations. Pricing structures of different software options vary based on features and scalability, making it imperative for buyers to assess cost-effectiveness alongside system capabilities.
Selection Criteria
Selecting the right warehouse management system involves considering important factors such as scalability, integration capabilities, and user-friendliness. Common mistakes to avoid during the selection process include overlooking long-term scalability and failing to involve key stakeholders in the decision-making process. Determining the right fit for your business needs requires a thorough analysis of workflows, existing technology infrastructure, and future growth projections.
Implementation Strategies
To ensure a smooth implementation of software solutions, best practices involve conducting a detailed assessment of current processes and aligning them with the new system. Integration with existing systems and processes calls for seamless data migration and interoperability testing. Training and support resources are vital for successful deployment, empowering users to leverage the full potential of the new WMS.
Future Trends
Looking ahead, the future of the industry-specific software landscape is poised for further advancements fueled by data analytics and machine learning. Upcoming technologies shaping the industry include predictive analytics for demand forecasting and robotics for warehouse automation. Recommendations for future-proofing your technology stack revolve around flexible solutions that can adapt to evolving market demands and technological innovations.
Introduction
Warehouse management systems play a crucial role in modern logistics, revolutionizing the way businesses handle inventory, orders, and overall operations. In today's fast-paced and competitive environment, the efficient management of warehouses is paramount to meeting customer demands and streamlining processes. This section aims to delve into the intricate world of warehouse management systems, providing a comprehensive comparison that can aid professionals and businesses in making strategic decisions that align with their objectives and requirements.
Understanding Warehouse Management Systems
Definition of WMS
Warehouse Management System (WMS) refers to a software application that controls and manages the operations in a warehouse. The primary function of a WMS is to optimize warehouse functionality by monitoring inventory levels, storage locations, and order fulfillment. One of the key characteristics of a WMS is its ability to automate tasks, reducing manual errors and increasing overall efficiency within the warehouse setting. This aspect is particularly advantageous in environments where accuracy and speed are crucial for successful operations. The unique feature of a WMS lies in its real-time tracking capabilities, providing instant visibility into inventory movements and enabling quick decision-making processes. While the benefits of a WMS are numerous, including improved productivity and order accuracy, there are considerations such as implementation costs and training requirements that need to be evaluated meticulously.
Importance in Modern Logistics
The importance of Warehouse Management Systems in modern logistics cannot be overstated. With the rise of e-commerce and global supply chains, the need for efficient warehouse operations has become a top priority for businesses. A WMS plays a vital role in enhancing productivity, reducing order processing times, and optimizing inventory management. Its key characteristic lies in its ability to adapt to changing business needs and scale operations accordingly. This flexibility is a valuable asset in a dynamic market landscape where businesses constantly face new challenges and opportunities. The significance of a WMS in modern logistics is further emphasized by its integration capabilities with other software systems such as ERP and CRM, facilitating seamless data flow and enhancing decision-making processes. While the advantages of implementing a WMS are substantial, businesses must also consider factors like compliance standards and data protection measures to ensure the security and reliability of their warehouse operations.
Key Features Comparison
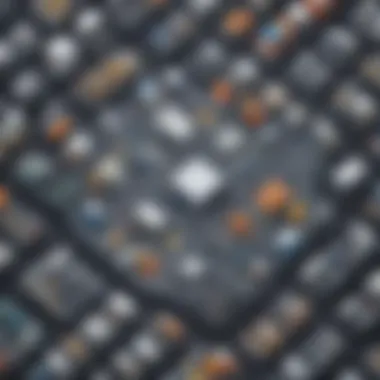

Warehouse management systems (WMS) play a pivotal role in modern logistics by efficiently organizing and optimizing warehouse operations. In this section, we will meticulously compare the key features of various WMS to help decision-makers and professionals choose the most suitable system for their business needs. Highlighting functionalities, integration capabilities, and scalability, this comparison will provide in-depth insights into the nuances of different systems.
Functionalities
Inventory Management
Inventory management is a crucial aspect of warehouse operations as it involves overseeing the flow of goods, optimizing stock levels, and ensuring accurate tracking of inventory. A robust Inventory Management feature within a WMS enables real-time monitoring of stock levels, efficient order fulfillment, and reduces carrying costs. Its ability to automate inventory processes and prevent stockouts makes it a valuable choice for businesses seeking operational efficiency. Despite its advantages, managing fluctuating demand and inventory accuracy could pose challenges when utilizing Inventory Management in some systems.
Picking and Packing
The Picking and Packing functionality within a WMS streamlines the process of fulfilling customer orders by efficiently picking items from inventory, packing them securely, and preparing for shipment. This feature enhances order accuracy, reduces picking errors, and increases productivity in warehouse operations. Its unique capability to utilize advanced algorithms for optimal picking routes and prioritize orders based on urgency makes it a preferred choice for businesses aiming for fast and accurate order fulfillment. However, the complexity of integrating this feature seamlessly with existing processes may present challenges in some WMS implementations.
Order Fulfillment
Order Fulfillment is a critical functionality in WMS that involves managing orders from receipt to delivery to ensure timely and accurate fulfillment of customer demands. This functionality streamlines the order processing workflow, enhances order accuracy, and improves customer satisfaction levels. Its unique feature of order tracking and real-time order status updates offers businesses a competitive edge in providing excellent customer service. Yet, the potential drawback lies in the complexity of synchronizing multiple orders and managing peak order periods efficiently.
Integration Capabilities
ERP Integration
ERP Integration is essential in connecting a WMS to Enterprise Resource Planning systems to streamline data flow, enhance visibility, and synchronize business processes seamlessly. This integration allows for real-time data exchange, improved decision-making, and cohesive operations across departments. Its unique feature of automating data entry and reducing manual errors enhances operational efficiency. However, challenges may arise in integrating different ERP systems and ensuring compatibility.
CRM Integration
CRM Integration enables the synchronization between WMS and Customer Relationship Management systems to centralize customer information, enhance communication, and improve customer service. This integration facilitates personalized order processing, targeted marketing campaigns, and effective customer engagement strategies. Its unique feature of customer data analytics and segmentation aids businesses in understanding customer preferences and behavior. Yet, limitations may include the complexity of integrating multiple CRM platforms and ensuring data security.
E-commerce Integration
E-commerce Integration links WMS with online sales platforms, automating order processing, inventory synchronization, and shipment tracking for seamless e-commerce operations. This integration enables real-time inventory updates, order visibility, and efficient order management for online retailers. Its unique feature of automated order routing and omnichannel fulfillment capabilities caters to the demands of e-commerce businesses aiming for operational excellence. However, challenges may arise in adjusting to varying e-commerce platforms' requirements and managing large volumes of online orders.
Scalability and Customization
Adaptability to Business Growth
Adaptability to Business Growth feature in WMS allows systems to scale according to evolving business needs, accommodating fluctuations in order volumes, warehouse size, and product diversity. This scalability ensures that the system can expand or contract based on market demands, supporting business growth and operational flexibility. Its unique feature of modular architecture and configurable settings offers businesses the flexibility to adjust the system to changing requirements. Nevertheless, challenges may exist in predicting future scalability needs accurately and ensuring smooth transitions during expansion phases.
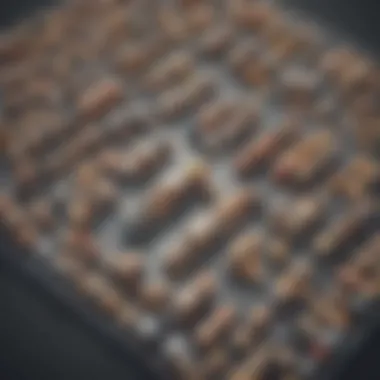

Customization Options
Customization Options in WMS provide businesses with the ability to tailor the system to meet specific operational requirements, industry regulations, and unique workflow processes. This feature allows for personalized settings, user interfaces, and reporting functionalities to align with the organization's objectives. Its unique feature of versatile configuration tools and customizable modules empowers businesses to optimize system performance and enhance user experience. However, complexities may arise in balancing customization with system stability and vendor support for bespoke solutions.
Performance Comparison
Importance of Performance Comparison
Performance Comparison is a crucial aspect in evaluating Warehouse Management Systems. It allows businesses to assess the effectiveness and efficiency of different systems, aiding in decision-making processes and optimization strategies. By comparing the speed and accuracy of tasks performed by these systems, organizations can identify the most suitable solution to meet their operational needs. The Performance Comparison section offers valuable insights into the tangible benefits and considerations of various WMS, enabling readers to make informed choices based on quantitative data and performance metrics.
Speed and Efficiency
Throughput Rate
Throughput Rate plays a pivotal role in determining the overall productivity and throughput capacity of a Warehouse Management System. It refers to the speed at which materials or goods flow through the system, impacting the efficiency of processes such as receiving, storing, and shipping. A high Throughput Rate signifies a system's ability to handle a large volume of tasks within a specified period, ensuring swift operations and minimal bottlenecks. However, excessively high Throughput Rates may strain resources and lead to errors, necessitating a balance between speed and accuracy for optimal performance in warehouse operations.
Picking Accuracy
Picking Accuracy is another critical factor in assessing the effectiveness of a Warehouse Management System. It measures the system's precision in selecting the correct items for order fulfillment, minimizing picking errors and reducing operational disruptions. High Picking Accuracy enhances customer satisfaction by ensuring accurate and timely deliveries, mitigating the risk of returns and replacements. While prioritizing accuracy is essential, excessively stringent accuracy requirements may slow down the picking process, affecting overall efficiency. Thus, striking a balance between speed and accuracy is imperative to maximize productivity and customer satisfaction in warehouse operations.
Cost Analysis
In the realm of warehouse management systems, cost analysis stands as a crucial component in the decision-making process for businesses and professionals. Understanding the financial implications of implementing a WMS is paramount to optimize operations while managing budgetary constraints effectively. Cost analysis delves into the monetary aspects associated with adopting a WMS, offering insights into initial investments, recurring expenses, and potential savings over time. By scrutinizing the financial intricacies, stakeholders can make informed decisions aligning with their operational needs and long-term strategic goals.
Initial Investment
Licensing Fees
Licensing fees represent a fundamental aspect of the initial investment required for implementing a warehouse management system. These fees entail the cost associated with acquiring the license to use the software, granting access to its functionalities and features. The pricing structure of licensing fees may vary, depending on factors such as the vendor, system complexity, and user requirements. Businesses opt for licensing fees as they provide legal access to the WMS, ensuring compliance with intellectual property rights and software usage regulations. The benefit of licensing fees lies in the assurance of receiving regular updates, patches, and technical support from the software provider, ensuring the system's smooth operation and security. However, one drawback of licensing fees is the potential for high upfront costs, which may pose financial challenges for small to medium-sized enterprises considering WMS implementation.
Implementation Costs
Implementation costs constitute another significant component of the initial investment in a warehouse management system. These costs encompass expenses related to system integration, customization, data migration, training, and ongoing support services. The key characteristic of implementation costs lies in their role in translating the theoretical benefits of a WMS into tangible operational improvements within the organization. Choosing the right implementation approach is critical to ensure seamless deployment and alignment with business objectives. Organizations opt for implementation costs to streamline processes, enhance efficiency, and maximize the system's potential to meet unique operational requirements. Despite the advantages of implementation costs in driving digital transformation and operational excellence, potential disadvantages include project delays, unforeseen expenses, and organizational disruptions during the transition phase.
Usability and User Experience
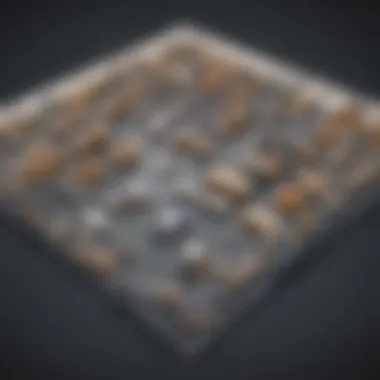

Warehouse management systems play a crucial role in modern logistics operations, where efficiency and precision are paramount. The usability and user experience of these systems are vital aspects that determine their effectiveness and adoption rates within organizations. In this article, we will delve into the significance of usability and user experience, highlighting how intuitive interfaces and streamlined processes can enhance operational productivity. Businesses are increasingly focusing on improving user experience to drive employee satisfaction and optimize workflow efficiency.
User Interface
User interface design is a critical component of WMS as it directly impacts the ease of use and functionality for end-users. In exploring the user interface of warehouse management systems, two key aspects stand out: intuitiveness and training requirements.
Intuitiveness
Intuitiveness refers to the ease with which users can navigate and interact with the system without the need for extensive training or guidance. A highly intuitive interface simplifies complex processes, reducing the learning curve for employees and accelerating task completion. The key characteristic of an intuitive interface is its user-friendly design, allowing users to perform tasks efficiently and without unnecessary complications. The advantage of intuitiveness in warehouse management systems lies in its ability to boost user adoption rates and overall operational efficiency.
Training Requirements
Training requirements denote the level of instruction or preparation needed for users to effectively utilize the system. Systems with low training requirements are desirable as they minimize downtime associated with onboarding new employees and allow for swift integration into existing workflows. The key characteristic of minimal training requirements is their ability to facilitate rapid user proficiency, ensuring a seamless transition to the new system. While low training requirements accelerate the deployment of WMS, they may sometimes lack in-depth training resources, necessitating supplementary guidance for complex operations.
Security and Compliance
In the realm of warehouse management systems, the aspect of security and compliance stands as a paramount concern. Addressing the critical need for safeguarding data integrity and complying with industry regulations, security and compliance measures play a pivotal role in ensuring operational efficiency and minimizing risks. Effective implementation of robust security protocols and adherence to stringent compliance standards are imperative for businesses aiming to safeguard sensitive information and maintain trust with customers and partners.
Data Protection
Compliance Standards
When delving into the realm of compliance standards within warehouse management systems, a key focus is on adhering to industry-specific regulations and guidelines. These standards serve as a benchmark for evaluating the system's ability to maintain data confidentiality, integrity, and availability. By aligning with established compliance standards such as GDPR or ISO certifications, organizations can demonstrate their commitment to data protection and regulatory compliance. The structure and rigor of compliance standards ensure that companies mitigate potential risks related to data breaches and non-compliance penalties while fostering trust among stakeholders.
Security Measures
Within the domain of security measures, the emphasis is on implementing comprehensive protocols to fortify the system against cyber threats and unauthorized access. Robust security measures encompass a multi-layered approach, including encryption, access controls, intrusion detection systems, and regular security audits. By prioritizing proactive security measures, organizations can defend against evolving cyber threats and prevent data breaches that can pose significant operational and reputational risks. The integration of advanced security technologies and best practices underscores the commitment to data security and resilience in the face of digital vulnerabilities.
Vendor Comparison
In this thorough exploration of Warehouse Management Systems, the Vendor Comparison section emerges as a pivotal aspect. Understanding the importance of selecting the right vendor in the intricate landscape of WMS solutions is crucial for businesses striving for operational excellence. Evaluating vendors entails scrutinizing various elements such as reputation, experience, support services, and cost-effectiveness. By delving into Vendor Comparison, organizations can mitigate risks, optimize system functionality, and enhance overall efficiency.
Market Leaders
Key Players
Delving into the realm of Market Leaders sheds light on the prominent Key Players in the WMS industry. These unrivaled entities exhibit exceptional prowess in delivering advanced solutions tailored to modern logistics challenges. Key Players stand out for their innovative approach, robust feature set, exemplary customer support, and seamless integration capabilities. Their solutions resonate with businesses seeking cutting-edge technology to streamline warehouse operations efficiently. While Key Players may come with a premium price tag, their reliability, scalability, and proven track record make them the preferred choice for forward-thinking enterprises. Leveraging unique features like predictive analytics, AI-driven automation, and real-time data visibility, Key Players empower organizations to achieve unparalleled efficiency and productivity.
Customer Reviews
The Customer Reviews segment provides valuable insights into the practical facets of utilizing WMS solutions offered by Market Leaders. Understanding customer feedback and experiences offers a nuanced perspective on the performance, usability, and overall satisfaction with the system. Customer Reviews serve as a compass for decision-makers, guiding them towards the solution that aligns best with their operational requirements. By dissecting these reviews, businesses can gain an understanding of the advantages and drawbacks associated with specific WMS offerings. Customer Reviews act as a testimonial to the effectiveness and reliability of Market Leaders, shedding light on real-world operational scenarios and the impact of implementing these cutting-edge solutions. Leveraging Customer Reviews allows organizations to align their expectations, identify potential challenges, and make an informed choice that drives digital transformation and operational excellence.