Comprehensive Insights into Warehouse Stock Management
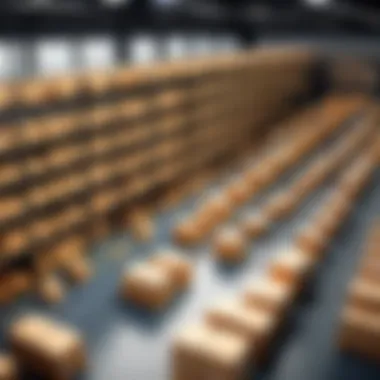
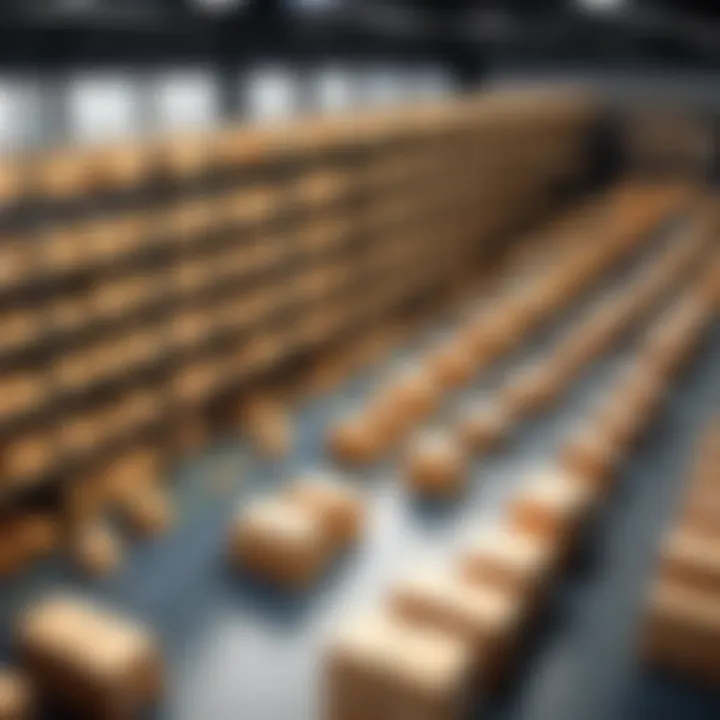
Intro
The management of warehouse stock can make or break a business. It's like navigating a ship through foggy waters—you need a keen eye for detail and the right tools to keep everything on course. In today’s fast-paced market, the importance of efficient warehouse stock management systems can't be overstated. As businesses strive for operational excellence, understanding these systems becomes a vital cog in the machinery of profitability.
Effective stock management helps organizations reduce costs, improve customer satisfaction, and maintain a sturdy edge over their competition. Amidst the chaos and complexity of inventory control, it’s essential to understand both the theoretical underpinnings and practical applications of stock management systems. This article unfolds the essential features, challenges, and innovations within the realm of these systems that decision-makers like you need to consider for a more streamlined operation.
"In the world of warehousing, stock management isn't just about keeping track of what's where; it's about creating value and solving problems before they arise."
Industry Overview
An understanding of the landscape in which warehouse stock management systems operate is crucial. The industry has undergone considerable transformation due to technological advancements and changing consumer demands. More businesses are shifting toward automation and adopting software that integrates seamlessly into their operations.
Current Trends in the Software Market
As noted, one significant trend in the warehouse management industry is the increasing reliance on cloud computing. Organizations find cloud-based solutions offer flexibility, scalable resources, and lower upfront costs. This makes it easier for small to mid-sized enterprises to have access to powerful tools that were previously available only to larger firms. Additionally, artificial intelligence and machine learning are becoming prevalent, allowing businesses to analyze inventory data more effectively and predict future trends.
Key Challenges Faced by Buyers in the Industry
However, it’s not a smooth ride for everyone. Buyers often encounter several hurdles when selecting appropriate warehouse stock management software. The sheer number of options available can create paralysis by analysis; it’s not just about finding software that works, but also about ensuring it meets current and future demands.
- Compatibility with existing systems
- User-friendliness for staff
- Hidden costs associated with software updates or scaling down the line
Emerging Technologies Impacting the Industry
Emerging technologies, like IoT (Internet of Things), are revolutionizing warehouse management. Sensors now track inventory in real-time, reducing manual errors. Moreover, augmented reality applications are beginning to streamline picking processes, allowing workers to locate products more swiftly. Such innovations pave the way for greater efficiency and accuracy.
In this rapidly evolving sector, awareness of recent developments and market shifts equips professionals to make informed decisions that will stand the test of time.
Prolusion to Warehouse Stock Management
Managing warehouse stock effectively is a crucial part of any thriving business. In this fast-paced era, where customer expectations are at an all-time high, having a robust stock management system can be the backbone of supply chain logistics. It’s not just about knowing what’s on the shelf; it’s about making sure that the right products are in the right place at the right time. When firms overlook this, it can spell disaster—from overstocked items gathering dust to critical stock-outs that keep customers from getting what they need.
Definition and Scope
At its core, warehouse stock management is about overseeing the flow of goods in and out of storage spaces. This encompasses various activities including tracking inventory, organizing storage space, and ensuring efficient shipping and receiving practices. Stock management extends beyond mere inventory counts; it involves a thorough understanding of processes that tie together procurement, storage, and distribution. It integrates technology, such as barcodes and RFID tags, which are essential for real-time inventory tracking. Furthermore, a well-defined scope includes linking inventory management not only with warehouse operations but also upstream suppliers and downstream customers to create a synchronized supply chain.
Importance in Supply Chain Management
In the grand scheme of supply chain management, warehouse stock management is like the hub of a wheel. All spokes, from suppliers to customers, hinge on effective stock management practices. Without it, businesses can find themselves wading through costly inefficiencies and operational bottlenecks. For example, excess inventory ties up capital that could otherwise be utilized, while inadequate stock can result in lost sales and diminished customer trust. Businesses gain a competitive edge when they precisely manage their stock levels, ensuring timely fulfillment and ultimately boosting customer satisfaction.
"In the world of e-commerce and fast delivery, your ability to keep a pulse on your inventory could very well determine your business's fate."
Ultimately, embracing technology within warehouse stock management not only contributes to cost reductions but also fosters agility in responding to market fluctuations. By aligning stock management systems with broader business strategies, companies can navigate demand volatility with ease, ensuring success in a competitive landscape.
Core Components of Stock Management Systems
Understanding the core components of stock management systems is key to ensuring that warehouses function smoothly and effectively. These elements not only streamline operations but also enhance accuracy in inventory control. Several factors come into play, including tracking methods, data management strategies, and system integrations, which all contribute towards a holistic stock management solution.
Inventory Tracking Mechanisms
Efficient inventory tracking mechanisms are the backbone of stock management systems. They help businesses ascertain the precise quantity and location of their stock at any given moment. Traditional methods like manual counts can be error-prone and time-consuming, creating headaches down the line.
- Barcode Systems: An easy-to-implement tracking technology, these systems assign unique barcodes to items. They increase speed in both receiving and shipping processes. When a barcode is scanned, the system automatically updates inventory levels.
- RFID Technology: This method uses radio waves to automatically identify objects. It allows for real-time tracking of items moving through the warehouse, enhancing visibility and reducing data entry errors. For many organizations, the upfront investment is well worth the ongoing efficiency gained.
- Cycle Counting: An ongoing inventory audit process that enables businesses to maintain consistent accuracy in stock levels. By frequently counting a subset of items rather than all at once, companies can detect discrepancies early, reducing potential losses.
The choice of tracking mechanism depends on budget constraints, item variety, and operational needs. The ultimate goal is to eliminate blind spots in inventory visibility so that decision-makers can act confidently and quickly.
Data Management and Analysis
Data may be the new oil, but in the realm of warehouse stock management, it’s more like the glue that holds everything together. Proper data management allows businesses to make informed decisions by analyzing historical trends and forecasting future needs.
- Centralized Databases: These are indispensable for real-time access to inventory levels, order history, and supplier information. By having all essential data in one place, teams can react adeptly to changing circumstances, such as sudden spikes in demand.
- Analytics Tools: Employing analytics and business intelligence tools can yield insights that drive operational efficiencies. Decision-makers can assess things like inventory turnover rates and identify slow-moving items, essentially refining procurement strategies and enhancing cash flow.
- Reporting Capabilities: Customizable reporting features help issues bubble to the surface and allow employees to stay ahead. Regular reports support continuous monitoring of key metrics, making it easier to identify potential bottlenecks or inventory excess.
Harnessing data correctly provides a significant competitive advantage. When teams are equipped with the right information, they can optimize operations and respond proactively to challenges.
Integration with Other Systems
A warehouse stock management system doesn't operate in a silo. Instead, it needs to integrate seamlessly with other essential systems within an organization. This synergy not only improves efficiency but also enhances transparency across the supply chain.
- ERP Systems: Integrating warehouse management with Enterprise Resource Planning (ERP) software allows for synchronized data flow from procurement to sales. This ensures that stock levels reflect sales trends accurately, preventing overstocking or stockouts.
- Customer Relationship Management (CRM): Connecting CRM with stock management provides sales teams instant access to inventory levels. It enhances their ability to fulfill client requests, improving customer satisfaction while ensuring that sales promises are kept.
- Shipping Solutions: Linking to logistics providers helps streamline the shipping process. Automating order shipments reduces human error and accelerates dispatch times, both of which directly impact delivery performance.
The seamless integration of systems is a game-changer for progressive organizations. When all components communicate effectively, it allows for better resource planning and achievement of broader business objectives.
In sum, the core components of stock management systems are fundamental to driving efficiency, accuracy, and overall performance in a warehouse environment. Each element serves a differing purpose but contributes collectively to a more transparent and agile supply chain.
Types of Warehouse Stock Management Systems
Understanding the various types of warehouse stock management systems is crucial for optimizing inventory control. Each type offers unique features, benefits, and challenges that influence operational efficiency. In today’s fast-paced market, selecting the right system can make or break a warehouse's performance. It’s about more than just keeping track of items; it’s about how each system fits into the larger puzzle of supply chain efficiency.
Manual Systems
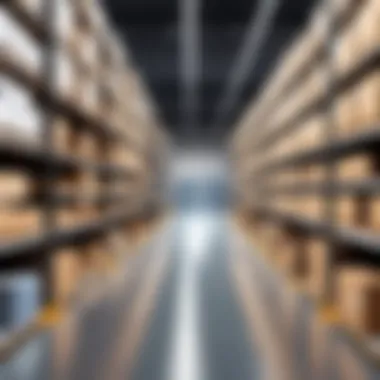
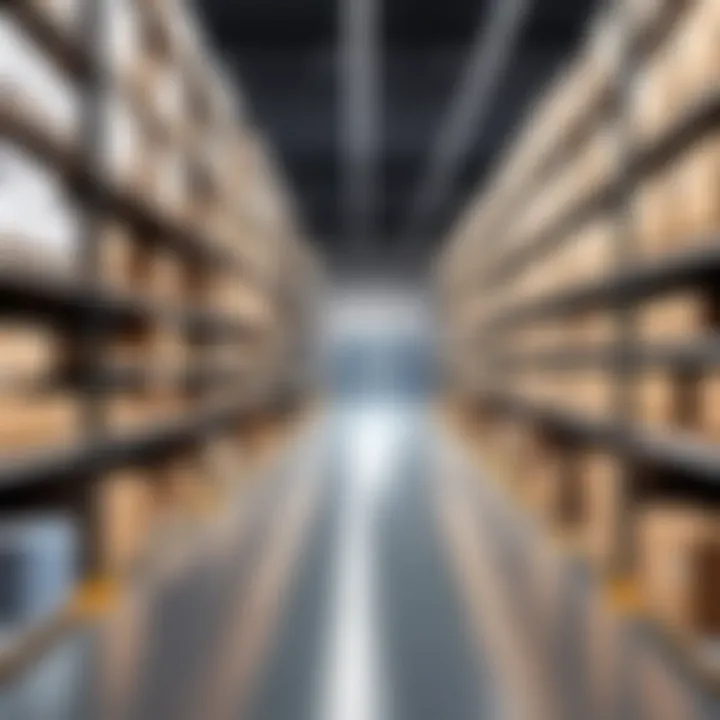
Manual stock management systems rely heavily on human oversight and record-keeping. In a typical setup, staff record inventory levels and transactions on paper or using basic spreadsheet software. While there is a sense of simplicity with manual systems, they come with a hefty cost when it comes to accuracy and efficiency.
Benefits of Manual Systems
- Low Initial Cost: Since it does not require sophisticated software, the setup costs are generally low.
- Simplicity: Easy to understand, even for those not technically savvy.
- Flexibility: Can be customized to fit unique warehouse requirements without software limitations.
Drawbacks to Consider
- Labor Intensive: Requires significant time investment for data entry and tracking.
- Increased Errors: Manual processes are prone to human error, leading to stock discrepancies.
- Limited Reporting Capabilities: Can be challenging to generate in-depth analytics without additional tools.
Automated Systems
Automated warehouse management systems leverage technology to efficiently oversee inventory. These systems often utilize barcode scanners and RFID technology for accurate tracking, allowing for real-time data updates.
Advantages of Automated Systems
- Increased Accuracy: Automated data entry significantly reduces errors compared to manual methods.
- Time Efficiency: Faster processing of shipments and inventory, leading to improved turnaround times.
- Comprehensive Reporting: Users can easily access reports on stock levels, sales trends, and profitability, facilitating informed decision-making.
Challenges with Automation
- Higher Initial Costs: The technology and infrastructure needed for an automated system can be expensive.
- Maintenance Requirements: Ongoing support and periodic updates can add to the operational budget.
- Training Required: Staff may need thorough training to adapt to new systems effectively.
Cloud-Based Solutions
Cloud-based stock management systems provide a modern alternative, allowing businesses to access inventory data from anywhere with an internet connection. This flexibility suits the needs of businesses operating across multiple locations or those that require a remote workforce.
Key Benefits of Cloud-Based Solutions
- Scalability: As the business grows, the system can easily expand to accommodate increased inventory.
- Real-Time Data Access: Stakeholders can access up-to-date inventory information at any time, improving responsiveness.
- Cost-Effectiveness: Lower upfront costs through subscription models while reducing the need for extensive IT infrastructure.
Potential Downsides
- Dependency on Internet Connectivity: Access issues can arise in case of network problems.
- Data Security Risks: Vulnerabilities associated with storing sensitive information online require robust security measures.
- Integration Challenges: Aligning cloud systems with existing software can sometimes be a daunting task.
Selecting the right warehouse stock management system involves weighing the pros and cons of each option against the specific needs of the business. This decision could significantly impact overall financial performance and operational efficiency.
Implementing a Warehouse Stock Management System
Implementing a warehouse stock management system is a pivotal undertaking for any business reliant on effectively storing and distributing goods. As the dynamics of consumer demand evolve, companies face rising pressures to streamline operations. A robust stock management system not only enhances inventory turnover but also fosters improved customer satisfaction, as accurate stock levels enable timely deliveries. Thus, this section delves into crucial components involved in this implementation, highlighting considerations, benefits, and best practices that decision-makers need to keep in mind.
Assessment of Needs
Before diving headfirst into system implementation, a thorough assessment of needs is essential. Companies must evaluate their current workflow, inventory challenges, and future growth objectives. Questions to ask include:
- What are the specific pain points in the current system? Identifying issues such as overstocking or stockouts helps in tailoring the new system to mitigate these problems.
- What volume of inventory is handled? Understanding inventory dynamics aids in selecting a system that can appropriately manage stock levels.
- What level of integration is needed with existing processes? Ensuring the new system can seamlessly mesh with current workflow creates smoother transitions and minimizes operational disruptions.
Gathering this information allows businesses to customize solutions to their individual circumstances. Such meticulous groundwork sets the stage for choosing a system that truly aligns with organizational goals.
Choosing the Right System
Once the needs are assessed, the next step is selecting the right warehouse stock management system. This process can be likened to finding the right pair of shoes—what works for one person may not work for another. There are several options available, and understanding the underlying differences can guide informed decision-making:
- Manual Systems: While these may seem fiscally attractive at first, they often lead to errors and inefficiencies in the long run.
- Automated Systems: Leveraging technologies such as barcode scanning or RFID, these systems can significantly reduce human error and improve speed.
- Cloud-Based Solutions: Providing flexibility and scalability, these systems are particularly suitable for businesses anticipating growth or fluctuating demands.
A careful comparison of these options, based on specific needs and resources, can help businesses choose a fitting solution that supports growth rather than hindering it.
Training and Onboarding Staff
After selecting an appropriate system, proper training and onboarding for staff is critical. Without effective training, even the most sophisticated system can become a source of frustration. Here are some considerations for successful staff onboarding:
- Comprehensive Training Programs: Facilitating workshops or hands-on training sessions ensures that employees are comfortable and capable of utilizing the new system's features.
- Ongoing Support: Establishing a support structure helps employees navigate challenges that arise post-implementation.
- Feedback Loops: Encouraging suggestions for system improvement from staff provides significant insights into usability and functionality, facilitating continued development of operational processes.
Moving forward, well-prepared staff play a vital role in the successful adoption of the new warehouse stock management system. Without their buy-in, even the best-laid plans can go awry.
"Successful implementation isn’t just about the technology; it’s about the people using it."
Summing it all up, implementing a warehouse stock management system is a multifaceted decision that requires careful planning and engagement from various stakeholders. By addressing the assessment of needs, judiciously selecting the right system, and ensuring thorough staff training, organizations can set themselves up for enhanced efficiency and operational success. With a solid system in place, businesses not only gain control over their inventory but also bolster their overall supply chain strategy.
Technological Advancements in Warehouse Management
In today’s fast-paced market, technological advancements play a pivotal role in streamlining warehouse operations. These advancements not only enhance efficiency but also improve accuracy, reduce operational costs, and bolster the overall agility of inventory management systems. With the inventory landscape evolving continually, it's imperative for decision-makers and IT professionals to remain abreast of these changes.
Use of RFID Technology
Radio Frequency Identification, commonly known as RFID, has redefined how inventory is tracked and managed in warehouses. Unlike traditional barcodes, RFID tags can be read without direct line of sight, enabling automatic data capture. This means that large volumes of items can be scanned rapidly, minimizing human error and accelerating checkout processes.
Operations efficiency grows when RFID technology is in play, as warehouses can achieve real-time visibility over their stock levels. This transparency allows for better decision-making, especially when eerie discrepancies in inventory levels arise. By employing RFID, companies can:
- Reduce labor costs: Automating inventory tracking minimizes manual input.
- Enhance accuracy: RFID dramatically cuts down errors related to human oversight.
- Boost supply chain responsiveness: Immediate data access permits faster restocking and order fulfillment.
"With RFID, we're not just counting our inventory; we’re syncing it with our operations in real-time," says a leading warehouse manager from a major retail chain.
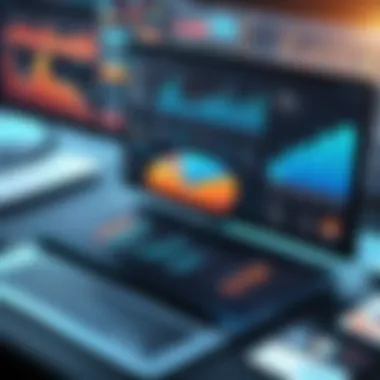
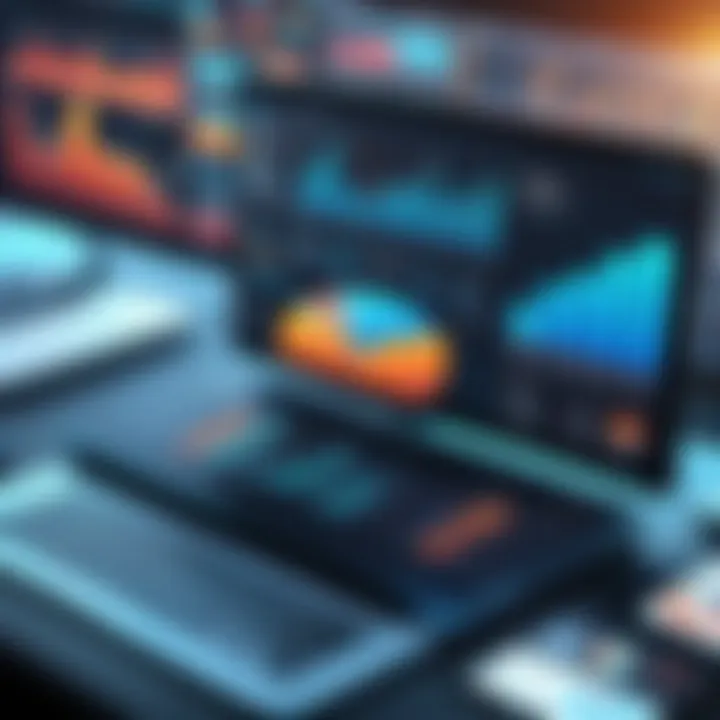
Artificial Intelligence Applications
Artificial Intelligence (AI) has found its niche in optimizing warehouse management processes. By leveraging machine learning algorithms, businesses can make data-driven choices that are far superior when compared to conventional methods. AI applications in warehouses can assess inventory trends, predict demands, and allocate resources accordingly.
One of the remarkable benefits of AI is its ability to analyze copious amounts of data swiftly. This capability allows for:
- Predictive analytics: Anticipating stock needs based on trends helps in avoiding overstocking or stockouts.
- Enhanced personalization: AI-driven insights facilitate tailored inventory management strategies for specific customers or departments.
- Robust decision-making: AI systems can simulate various operational scenarios, providing managers with a clearer view of potential outcomes.
As technology advances, the integration of AI in stock management will continue to merge strategic foresight with operational execution.
Internet of Things (IoT) Integration
The Internet of Things (IoT) has introduced a new layer of connectivity in warehouse operations. Through IoT-enabled devices, every item in a warehouse can relay information about its condition and location in real-time. This constant data flow promotes a smart warehouse environment.
Consider these IoT benefits for warehouses:
- Connected equipment: Devices operate in sync, reducing downtime and maintenance costs.
- Environmental monitoring: IoT sensors can detect temperature, humidity, and other conditions to preserve product integrity.
- Enhanced tracking: Smart devices ensure precise tracking of assets from arrival at the dock to the final shipping point.
Best Practices for Effective Stock Management
Navigating the complexities of warehouse stock management can be a daunting task. However, adhering to best practices can significantly smooth the ride. Best practices in stock management are the backbone of efficient operations. They help in reducing errors, improving inventory accuracy, and ultimately boosting the bottom line. Ensuring that these practices are top-of-mind can create a more organized and dependable warehouse environment, keeping you ahead of the game in a competitive market.
Regular Audits and Reconciliation
Carrying out regular audits is not just a checkbox on a to-do list; it’s critical for maintaining the integrity of your inventory. These audits serve as a reality check, matching what’s on the shelves to what’s recorded in the system. This process helps identify discrepancies that could stem from various reasons—be it human error, theft, or misplaced items.
When audits are performed routinely, they can reveal trends over time that may signal larger issues. For instance, if a particular product consistently appears missing, it could prompt an investigation into whether staff training needs to improve or if there’s a problem with the receiving process. Implementing a structured reconciliation process—where discrepancies are meticulously investigated—also provides valuable insights into operational inefficiencies. Keeping track of these inconsistencies helps refine business strategies and optimize stock levels.
Steps for effective audits:
- Conduct audits at regular intervals
- Compare physical stock with recorded levels
- Investigate and document discrepancies
Cycle Counting Techniques
Cycle counting is an informative approach that focuses on counting a subset of inventory in rotation, allowing for regular validation without interrupting warehouse operations. This method is not only efficient but also versatile. It allows for targeting specific areas of concern, whether it's high-value items or those known to have frequent discrepancies.
Workers can be trained to conduct these counts during regularly scheduled downtimes, or by incorporating them into daily routines, spreading the workload. This approach leads to ongoing accuracy, as opposed to a single end-of-year exercise that might not accurately reflect reality.
Benefits include:
- Continual accuracy in inventory records
- Reduced disruption to warehouse operations
- Enhanced employee engagement in inventory management
Optimizing Warehouse Layout
A well-organized warehouse layout makes all the difference. The layout can significantly impact inventory handling and storage efficiency. Understanding the flow of goods, from receiving to storage to shipping, is vital.
By analyzing movement patterns and the types of products stored, you can maximize space and reduce unnecessary travel time for employees. Consider the principle of proximity; placing fast-moving items closer to packing areas can lead to quicker order fulfillment. Using tools like flow charts may help visualize the current layout and identify bottlenecks or obstacles that can be improved.
Key considerations for layout optimization include:
- Understanding product velocity
- Eliminating bottlenecks
- Using vertical space effectively
The truth is, a well-thought-out warehouse layout pays off in both time and cost saved in the long run.
Challenges in Warehouse Stock Management
The effectiveness of any warehouse largely hinges on how well it can manage its stock. Yet, the road can get bumpy with a multitude of challenges that can derail operations. Understanding these hurdles is crucial for leaders and stakeholders who aim to streamline their inventory processes. This section delves into three major challenges: inaccurate inventory records, managing seasonal fluctuations, and cost control issues. Each of these elements has its own unique dimensions that play a significant role in the overall stock management system. By addressing them head-on, companies can improve their resilience and operational efficiency.
Inaccurate Inventory Records
When we talk about inaccurate inventory records, what we often see is a bit like a snowball effect. It starts small with a few minor discrepancies, but before you know it, it becomes a significant issue. The consequences are as serious as they come, affecting everything from order fulfillment to financial forecasting.
The problem can arise from various factors, such as human error, system malfunctions, or even miscommunication between departments. For instance, if the warehouse staff fails to update the stock count after a shipment arrives, it leads to miscalculations that can easily cascade through the supply chain.
To combat this issue, organizations can implement regular audits and utilize technology like RFID for real-time tracking. By maintaining an accurate record, they not only enhance decision-making but also reduce wasted time and resources, driving overall efficiency.
"The key to surviving in a competitive market is to ensure that your inventory reflects reality."
Managing Seasonal Fluctuations
Every industry feels the tug of seasonal fluctuations, and warehouses are certainly no exception. Depending on the location and the type of products held, some warehouses may face drastic variations in demand throughout the year. For example, a warehouse storing holiday decorations might find that its activity spikes dramatically in November and December, while it struggles to keep busy in the summer months.
This can create a tricky balancing act for warehouse managers. They have to meet peak demands without overstocking, which leads to wasted space and capital. One method to handle this is through implementing flexible staffing plans and utilizing temporary storage solutions during peak seasons. This way, the warehousing staff can adapt to sudden changes in demand without being caught off guard.
Moreover, forecasting demand using data analytics can be a game changer. By analyzing past trends and customer behavior, warehouse managers can plan better for seasonal changes.
Cost Control and Budgeting Issues
Cost control is akin to walking a tightrope—too much cutting back can drain morale and service quality, while too little can put a strain on the budget. Thus, establishing a clear budgeting strategy is essential for long-term success in warehouse management. Warehouse operation costs can often mount up due to utilities, labor, maintenance, and inventory losses, and without prudent management, these expenses can spiral out of control.
To effectively control costs, it's critical for decision-makers to analyze expenditures continuously. Maintaining a balance between maintaining stock levels and keeping inventory costs low is key. Using technologies such as stock management software can help in automating re-order levels and optimizing storage solutions, ultimately aiding in cost efficiency.
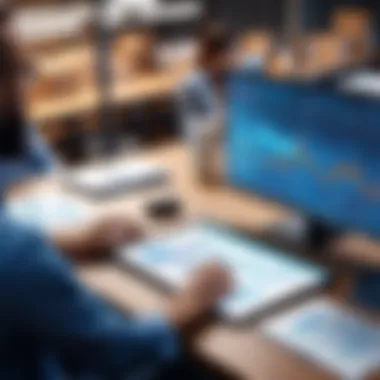
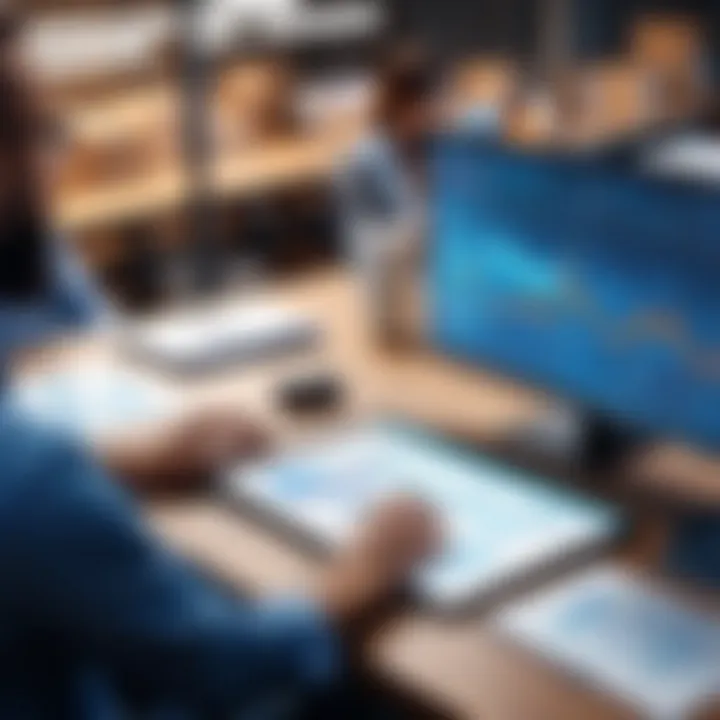
Furthermore, conducting a thorough cost-benefit analysis for new initiatives is a smart move. This way, companies can decide where to invest and where to save, leading to a more robust financial strategy.
In summation, these challenges, while formidable, are not insurmountable. By addressing inaccurate inventory records, managing seasonal fluctuations, and controlling costs, warehousing operations can adapt and thrive even in the face of adversity.
Evaluating System Performance
Evaluating system performance is critical in ensuring that warehouse stock management systems function optimally. For any organization, it’s a strong indicator of how well resources are being utilized, how efficiently inventory is managed, and how effectively the overall supply chain operates. By focusing on specific measurements and thoughtful analysis, businesses can make informed decisions that enhance productivity and reduce costs. In this section, we’ll delve into essential components of system performance evaluation, exploring the benefits and considerations that surround this crucial aspect of warehouse management.
Key Performance Indicators
When it comes to warehouse stock management, Key Performance Indicators (KPIs) serve as the backbone for assessing system effectiveness. These metrics not only provide tangible data but also allow organizations to benchmark their performance against industry standards. Generally, KPIs can help in the following ways:
- Inventory Turnover Rate: Measures how frequently inventory is sold and replaced over a specific period. A higher rate indicates efficiency.
- Order Accuracy: Reflects the percentage of orders correctly fulfilled. High accuracy translates into better customer satisfaction.
- Receiving Performance: Deals with the efficiency of product receipt and storage. This metric looks at the time taken from receiving goods to their availability for picking.
By keeping an eye on these KPIs, businesses can identify areas needing improvement. It becomes easier to establish targets, ensuring that everyone in the organization works towards the same goals.
Return on Investment Analysis
The return on investment (ROI) analysis plays a pivotal role in evaluating system performance. It quantifies how effectively the resources invested in a stock management system are generating returns. Factors to consider include:
- Initial Costs: The upfront expenses related to implementing the system, including software, hardware, and staff training.
- Operational Savings: Assessing reductions in labor costs, errors, and waste can provide a clearer picture of savings achieved post-implementation.
- Increased Revenue: Analyzing enhancement in sales due to improved inventory management or faster processing can demonstrate positive ROI.
Ultimately, a solid ROI analysis not only reflects the financial implications of the stock management system but also provides a case for future investments in technology or system upgrades to further optimize performance.
User Feedback and Continuous Improvement
The opinions of users cannot be underestimated in the evaluation process. Collecting user feedback offers invaluable insights into the practical operation of warehouse systems. Here’s how businesses can foster a culture of continuous improvement:
- Feedback Loop: Establish regular channels for employees to share their experiences with the system. This can be through surveys or informal discussions.
- Training Opportunities: Identify areas where users struggle and tailor training programs to address these challenges.
- Update Cycles: Use insights from feedback to inform software updates or operational changes, ensuring that the system evolves according to actual user needs.
"User engagement is not just a process; it's a pathway to innovation. Without understanding the user experience, systems may stagnate, leading to inefficiencies that could easily be avoided."
Prioritizing user feedback helps organizations stay responsive and adaptable, leading to enhanced system performance and, ultimately, greater operational efficiency.
Future Trends in Warehouse Management
In the ever-evolving landscape of warehouse management, staying abreast of future trends is not just a good practice—it's a necessity. Adopting forward-thinking strategies can make all the difference in operational efficiency, cost reduction, and sustainable practices. Decision-makers, IT professionals, and entrepreneurs alike must understand the importance of these trends. Embracing these changes often leads to better inventory control and enhanced overall performance across the board.
Sustainability Initiatives
Sustainability has become more than just a buzzword; it’s a vital factor in shaping future warehouse strategies. Companies are increasingly realizing that implementing eco-friendly practices significantly reduces waste and saves costs in the long run. For example, optimizing packaging materials or employing green energy sources can substantially lower carbon footprints.
Moreover, using a sustainable approach can differentiate a business in a crowded market. Customers today are more conscientious about the environmental impact of their purchases. Thus, brands actively engaging in sustainability often enjoy better loyalty and market share.
Also, sustainable initiatives such as optimizing transportation logistics or implementing waste reduction techniques not only benefit the environment but also improve the bottom line. Investing in these areas enhances brand reputation and helps align with regulatory requirements, which are becoming stricter.
Advanced Robotics in Warehousing
Another trend that is reshaping warehouse operations is the integration of advanced robotics. Robotic systems are increasingly deployed in warehouses to automate repetitive and time-consuming tasks. From picking and packing to sorting and transportation, robots can perform these functions with a level of precision that is hard to match.
For instance, using collaborative robots, or cobots, allows human workers to focus on more complex tasks while robots handle the grunt work. This symbiotic relationship can lead to enhanced productivity and reduced error rates. Robotics also presents the potential for significant savings on labor costs over time.
Indeed, automation does not mean eliminating the workforce; it's more about augmenting human capabilities. Employees can be retrained to manage and maintain these robotic systems, opening new career paths and opportunities for skill development within the workforce.
Blockchain for Inventory Integrity
Blockchain technology is emerging as a powerful tool for ensuring inventory integrity. Unlike traditional databases, blockchain offers a decentralized and tamper-proof ledger, making it ideal for tracking goods as they move through the supply chain. This transparency provides an accurate record that can help mitigate common issues like counterfeit products or discrepancies in inventory levels.
Utilizing blockchain can enhance trust among stakeholders—suppliers, distributors, and retailers— as everyone has access to the same reliable data. Imagine being able to trace the origin of a product with absolute certainty or confirming that quantities are accurate at every point along the supply chain. These capabilities minimize losses and improve overall accuracy in inventory management.
Furthermore, as data privacy concerns grow, blockchain can help secure sensitive information while maintaining the integrity of inventory data. The reduced friction in transactions and real-time visibility into stock can empower businesses to respond more swiftly to market demands.
"By adopting advanced technologies like robotics and blockchain, enterprises will not only improve their warehouse operations but also accentuate their competitive edge in a challenging marketplace."
Adopting these future trends in warehouse management is essential for staying relevant. The blend of sustainability, advanced robotics, and innovative technologies like blockchain holds substantial promise for enhancing the efficiency and effectiveness of stock management systems. As the industry continues to evolve, those who leverage these trends will likely find themselves at a significant advantage.
Culmination
In wrapping up our exploration of warehouse stock management systems, it becomes clear that these systems are not mere tools, but vital components in the machinery of effective supply chain operations. Without a robust stock management system, businesses can find themselves in a tricky situation—like a ship lost at sea, devoid of navigation. The various facets of these systems, from inventory tracking to technological integrations, underscore their significance.
Recap of Key Points
To reiterate what has been discussed:
- Definition and Scope: We defined what warehouse stock management systems are and their crucial role in the broader supply chain.
- Core Components: The systems include mechanisms for tracking inventory, data management techniques, and their integration with other operational systems.
- Types of Systems: We categorized warehouse systems into manual, automated, and cloud-based, highlighting their respective advantages and disadvantages.
- Implementation Steps: Understanding your needs, choosing the right system, and effective training are essential for success.
- Technological Advances: RFID, AI, and IoT are reshaping how warehouses operate, making them smarter and more efficient.
- Best Practices: Regular audits, cycle counting, and optimizing layouts help maintain accuracy and efficiency.
- Challenges: Recognizing issues like inaccurate records and seasonal fluctuations is key in devising solutions.
- Performance Evaluation: Key performance indicators, ROI analyses, and user feedback create a feedback loop for ongoing improvement.
- Future Trends: Sustainability initiatives, advanced robotics, and blockchain are paving the way for innovative practices in the industry.
Future Outlook
Looking ahead, we can see that warehouse stock management is on the brink of significant transformation. Sustainability efforts are gaining traction as companies face pressure to minimize their environmental footprint. Advanced robotics are likely to revolutionize picking and packing, making processes faster and more reliable. Moreover, blockchain could enhance inventory integrity, creating an unchangeable ledger for products, thus increasing trust across the supply chain.
The future does not simply belong to technology alone; it will also require a cultural shift within organizations. Training staff to adapt to new tools and practices will be paramount. Embracing a mindset of continuous improvement will enable firms to not just respond to current changes but anticipate future needs as well.
In this evolving landscape, staying informed and agile will be key for decision-makers. It’s not just about keeping the lights on anymore; it’s about creating systems that illuminate the path forward.
"To stay ahead, one must not only keep pace with change but also become a catalyst for it."
Embracing these trends will arm businesses with the tools and strategies necessary to navigate tomorrow's challenges in warehouse stock management.