Harnessing ANSYS Digital Twin Technology for Industries
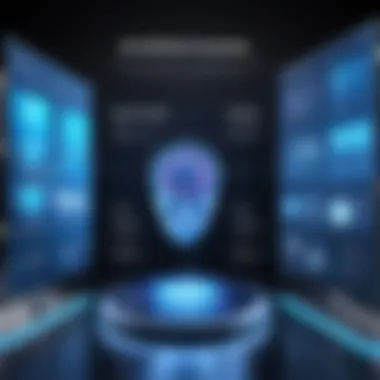
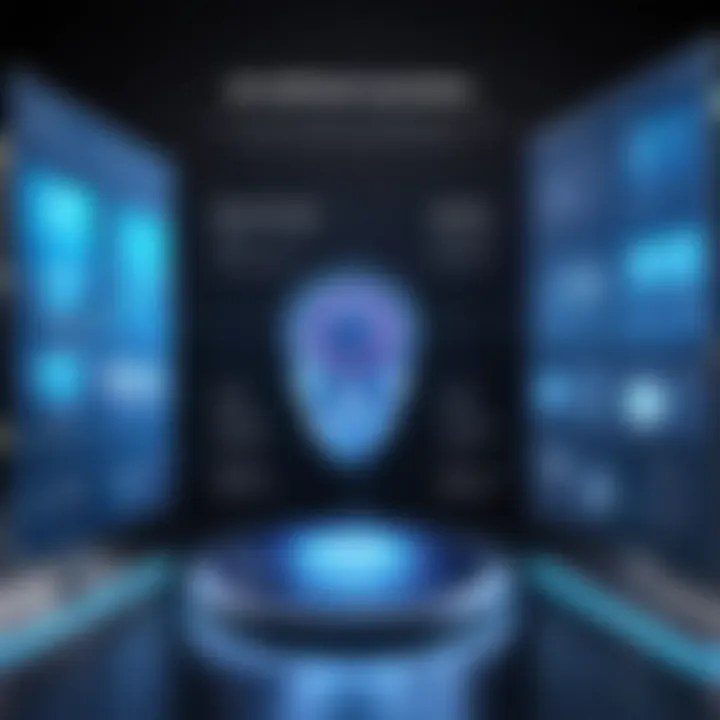
Intro
In the realm of technological advancements, Digital Twin technology is carving out its niche as a game changer. In essence, a digital twin is a virtual representation of a physical object or system, created using real-time data to replicate its functionality and behavior. In the context of ANSYS, this technology becomes significantly powerful as it allows for simulation and optimization in various sectors such as manufacturing, aerospace, and healthcare. The implications of utilizing ANSYS Digital Twin are profound, as organizations see not just an acceleration in their processes but also an enhancement in decision-making capacity.
These models are the backbone of understanding complex systems and operations. They facilitate predictions about performance and provide insights into system diagnostics, thus functioning as a bridge between real-world phenomena and digital representations.
In this exploration, we dissect how ANSYS navigates the intricacies of adopting and integrating digital twins while focusing on the benefits forged through practical applications in key industries. We'll also confront the challenges that lie ahead, offering a thorough panorama that reflects not merely what is but what could be in the future of digital twin technology.
Understanding Digital Twin Technology
Digital Twin Technology is intricately woven into the fabric of modern industries. It's not merely a technical gimmick; it possesses profound implications for how organizations operate and strategize. As businesses embrace this technology, understanding its nuances becomes essential for decision-makers, IT professionals, and entrepreneurs alike.
In essence, digital twins serve as virtual replicas of physical entities or processes. This convergence allows firms to model real-world behavior, leading to informed decisions backed by simulated realities. The importance of this technology lies in its capability to provide a dynamic platform for analysis, trend prediction, and operational efficiency. These virtual models help in optimizing processes, reducing downtime, and, ultimately, enhancing stakeholder value.
Definition and Fundamentals
At its core, a digital twin is more than just a digital model; it’s a real-time digital counterpart to a physical object or system. This concept hinges on the seamless integration of data and physical entities. When a physical item is matched with a virtual one, it opens a conduit for continuous feedback loops that enrich the digital representation with current state information.
Key characteristics of digital twin technology include:
- Real-Time Data: Continuous assimilation of data from sensors and devices.
- Simulation: Opportunities to run models under various scenarios for better prediction.
- Feedback Mechanism: Adjustments can be made based on real-time insights from the virtual model, facilitating proactive decision-making.
For instance, if an aircraft component has a digital twin, engineers can monitor its performance metrics, weather conditions, and structural parameters. This holistic view helps in predicting failures before they occur.
Historical Context
To grasp the significance of digital twin technology today, it’s useful to take a step back and appreciate its roots. The concept of the digital twin emerged from the realms of aerospace and manufacturing engineering. Early iterations were basic simulations aimed predominantly at ensuring operational compatibility.
The transformation gained momentum with advancements in Internet of Things (IoT) technologies in the 2000s. As devices became increasingly interconnected, the ability to gather and analyze vast sets of data refined.
Over the course of the last two decades, industries have recognized the value of predictive analytics and data-informed decision-making. Accordingly, digital twins evolved into sophisticated models that now drive innovation across multiple sectors.
"Digital twins represent a bridge from the physical world to the digital realm, enabling resources to be managed with precision."
Understanding digital twin technology lays the groundwork for comprehending ANSYS’ role in developing these models and their application across various industries.
Foreword to ANSYS
The exploration of ANSYS in relation to Digital Twin technology provides a pivotal bridge for understanding how simulation tools can reshape industries. Recognizing the capabilities of ANSYS opens a vista into not just technological applications but also the enhancement of operational practices. ANSYS is more than just a software; it embodies a comprehensive approach to solving complex engineering problems. Its significance can't be overstated, especially in today's world where efficiency and agility are tantamount to survival in competitive markets.
Company Overview
ANSYS Inc., founded in 1970, has established itself as a cornerstone in the engineering simulation landscape. With its headquarters in Canonsburg, Pennsylvania, the company specializes in producing software that allows organizations to simulate various physical phenomena. This includes structural, fluid dynamics, thermal, and electromagnetic effects, making it a versatile tool for engineers across numerous fields.
ANSYS is widely recognized for its ability to enhance product development processes, providing insights that allow for better design and innovation.
The company's software solutions are utilized across a variety of sectors, including aerospace, automotive, healthcare, and more. Such diversity illustrates its tech's adaptability and effectiveness in tackling real-world challenges. The ongoing commitment of ANSYS to research and development ensures that it remains at the forefront of emerging technologies.
Core Technologies
At the heart of ANSYS's offering is a suite of core technologies that serve as key enablers for Digital Twin development. These technologies are designed to integrate various aspects of simulation and data analytics, forming a cohesive ecosystem where models can be rapidly developed and tested.
- Finite Element Analysis (FEA):
This technology allows engineers to predict how products will react to real-world forces. By breaking down complex structures into smaller, manageable elements, FEA provides detailed insights into stress, strain, and deformation. - Computational Fluid Dynamics (CFD):
CFD simulates fluid behavior to optimize interactions between fluids and solid surfaces. ANSYS utilizes advanced algorithms to enhance accuracy in predictions, crucial for industries like aerospace where aerodynamics is key. - Multiphysics Simulation:
This capability combines various physical phenomena in a single model, enabling users to study how different factors interrelate. This is particularly beneficial in environments where thermal, structural, and fluid dynamics converge. - Data Integration and Analytics:
The integration of powerful analytics tools allows for the processing and interpretation of vast amounts of data generated during simulations. With enhanced data visualization, decision-makers can gain clear insights into performance metrics.
These technologies not only empower users to create accurate Digital Twins but also support continuous improvement cycles, making ANSYS an invaluable partner in the digital transformation journey of industries.
How ANSYS Develops Digital Twins
Digital twin technology has emerged as a cornerstone for modern industries, and understanding how ANSYS harnesses this capability is essential. The processes involved in developing digital twins are not merely technical; they encompass strategy, vision, and practical application. Leveraging accurate models alongside real data ensures that businesses see substantial returns on their investment while also improving reliability and efficiency.
Model Creation Processes
Creating a digital twin is akin to sculpting a masterpiece. It begins with capturing extensive data on the physical object or system in question. ANSYS uses a variety of methods to gather this data, including sensors, simulations, and historical records.
- Sensor Data Collection: ANSYS harnesses real-time data from sensors embedded within equipment to monitor performance continually. This information serves as the backbone of the digital twin model.
- Simulation Models: The complexity of real-world designs often leads ANSYS to leverage simulation models generated through its software. These simulations can anticipate how a product will behave under diverse conditions, merging engineering principles with cutting-edge technology.
- Data Assimilation: The next step involves merging data from multiple sources, ensuring that every facet—from environmental conditions to operational parameters—is accounted for. This not only enhances the model's accuracy but also helps in forecasting future scenarios.
The iterative nature of refining these models means each digital twin evolves over time, becoming more precise as new information is added.
Data Integration and Analytics
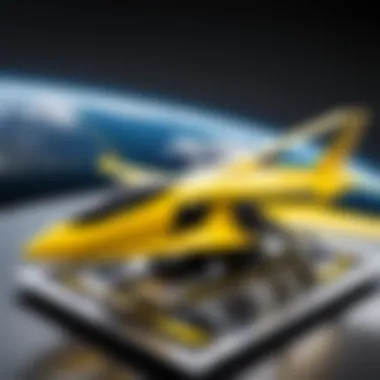
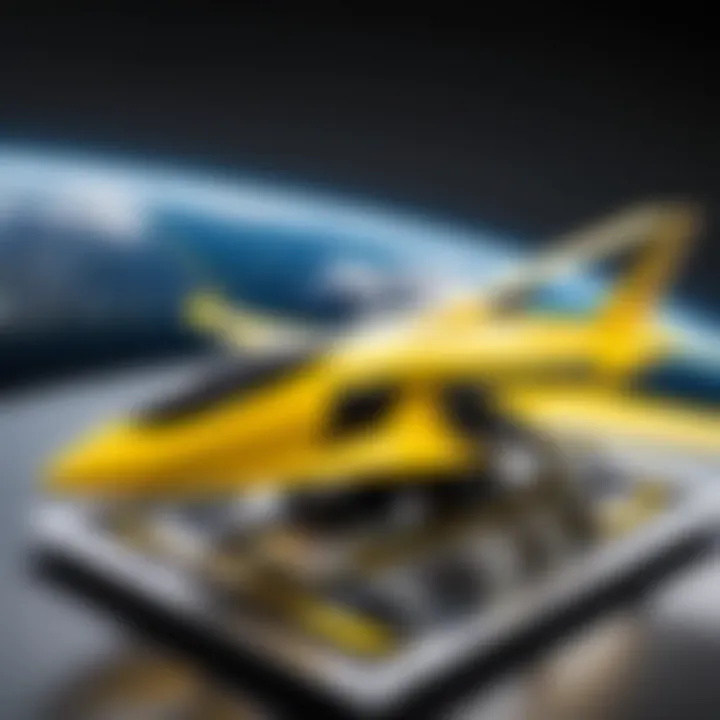
In the context of digital twins, data integration is pivotal. It lays the groundwork for insightful analytics that drive effective decision-making.
- Unified Data Framework: ANSYS employs a unified data framework that amalgamates diverse data types from numerous sources. By creating a centralized repository, stakeholders can access comprehensive insights.
- Advanced Analytics: Using sophisticated algorithms, ANSYS provides analytics that reveal underlying patterns and trends that you might miss otherwise. This capability aids decision-makers in identifying operational inefficiencies and potential performance issues.
- Predictive Insights: A standout feature of ANSYS's approach is its capacity to predict future states. By analyzing historical performance data against current parameters, ANSYS's digital twin technology can guide users towards corrective actions before issues escalate.
Real-Time Monitoring Capabilities
Real-time monitoring stands at the core of what makes ANSYS's digital twin effective. With live data feeding into the models, organizations gain immediate visibility into performance metrics.
- Dynamic Monitoring: ANSYS offers an interface wherein users can visualize real-time performance. This dynamic setup allows for instantaneous adjustments to operations based on current data.
- Alerts and Notifications: A notable advancement is the automated alert system, which flags any anomalies detected during operational processes. This ensures that teams can act swiftly to rectify deviations from expected performance levels.
- Continuous Feedback Loop: The integration of real-time monitoring creates a feedback loop, empowering constant enhancement of both the digital twin and the physical counterpart. As systems adapt and evolve, so too do the models, aligning closely with real-world performance.
Key Insight: The intricate dance between data collection, integration, and real-time monitoring encapsulates ANSYS's commitment to delivering accurate, actionable insights to its users.
Understanding how ANSYS develops digital twins unveils its transformative capacity across industries. Be it manufacturing, aerospace, or healthcare, these digital replicas facilitate not just efficiency but an overarching strategic advantage.
Applications Across Industries
The potential applications of ANSYS Digital Twin technology span a variety of fields, making it a transformative asset across numerous industries. The implications here are not just theoretical; they present tangible benefits that decision-makers and IT professionals can leverage for improved operational outcomes.
Digital twins are more than just virtual replicas of physical assets. They can analyze data in real-time, enabling companies to simulate scenarios and predict outcomes, thereby guiding strategic decisions. This allows businesses to optimize processes, enhance performance, and ultimately drive growth. Understanding these applications is crucial for any organization that aims to stay competitive in today’s fast-paced environment.
Manufacturing Sector
In the manufacturing industry, ANSYS Digital Twins are game changers. With the pressure to improve productivity and reduce costs, manufacturers are turning to these models to improve their operations. By creating a digital twin of a manufacturing process or a production line, companies can monitor performance, analyze inefficiencies, and test improvements in a risk-free environment.
Benefits of Digital Twins in Manufacturing:
- Real-time Monitoring: Understand how machinery and processes are performing at any moment.
- Predictive Analytics: Use historical data to anticipate failures before they happen, ensuring minimal downtime.
- Resource Optimization: Fine-tune resource allocation to maximize efficiency and reduce waste.
A great example of this can be seen in organizations that have employed digital twins to simulate production processes—identifying bottlenecks that were previously unnoticed. These insights lead to streamlined operations, saving both time and money.
Aerospace and Defense
In aerospace and defense, safety and efficiency are paramount, making ANSYS Digital Twins particularly relevant. By developing digital twins of aircraft and their components, engineers can conduct rigorous stress tests and performance evaluations long before physical prototypes are built.
How Digital Twins Enhance Aerospace and Defense:
- Safety Assurance: Know how modifications to aircraft design will affect performance under various conditions.
- Cost Reduction: Save on the expenses related to building and testing physical models.
- Regulatory Compliance: Ensure that designs consistently meet the stringent standards required in this sector.
Through virtual modeling, organizations can accurately predict the life cycle of components, enabling better design decisions and reducing the risk of unexpected failures.
Healthcare Innovations
The healthcare sector is another area ripe for digital twin applications. The ability to create a digital mirror of a patient’s health profile, or even the operations of a hospital, paves the way for personalized medicine. ANSYS Digital Twins can simulate treatments, allowing for tailored solutions that enhance patient outcomes.
Key Advantages in Healthcare:
- Personalized Treatment Plans: Create simulation models that adapt treatments based on individual patient data.
- Enhanced Operational Efficiency: Streamline hospital workflow through modeling of patient flow and care delivery.
- Drug Development: Safeguard the process of drug testing by using simulations that predict interactions and efficacy.
For instance, a hospital using digital twins to optimize patient pathways has witnessed shorter wait times and higher patient satisfaction rates.
Transportation and Logistics
In transportation and logistics, efficiency and real-time data are critical components for success. ANSYS Digital Twins support these objectives by providing insights into supply chain operations and vehicle performance.
The Impact of Digital Twins in Transportation:
- Fleet Management: Monitor vehicle conditions and optimize routes using real-time data.
- Supply Chain Optimization: Adjust for disruptions in logistics without impacting service levels.
- User Experience Enhancement: Simulate different transportation scenarios to create passenger-centric solutions.
For example, transport companies have used digital twins to analyze logistics pathways, adjusting delivery routes dynamically based on real-time traffic data, significantly improving delivery times.
"The future of industries lies in harnessing the power of data through innovative technologies like digital twins. They are not just a trend; they are a vital extension of our capabilities."
Overall, the vast applications of ANSYS Digital Twin technology across diverse sectors demonstrate not only its versatility but also its critical role in shaping the future of business processes. By incorporating this technology, industries are positioning themselves at the forefront of transformation and efficiency.
Case Studies and Real-World Implementations
Case studies play a crucial role in understanding the practical implications of ANSYS Digital Twin technology. When you look at real-world implementations, it's like shining a spotlight on how digital twins are not just theoretical constructs but rather tangible assets that drive innovation and efficiency in diverse industries. Notably, these cases encapsulate the transformative benefits of leveraging such technology, revealing its capabilities to streamline processes, enhance accuracy, and inform critical decisions.
Different sectors provide unique lenses through which to view the applicability of ANSYS Digital Twin models. The effectiveness of digital twins lies not just in their creation but in how organizations utilize them to glean insights that would otherwise remain buried beneath heaps of data. By dissecting these case studies, decision-makers gain a clearer picture of what digital twins can achieve, empowering them to adopt these technologies confidently.
Manufacturing Optimization Examples
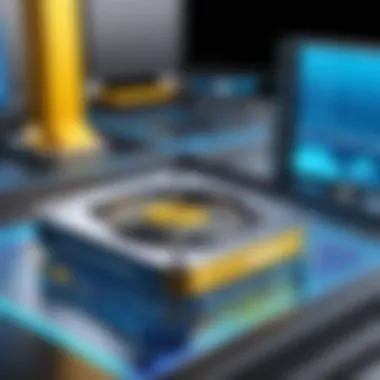
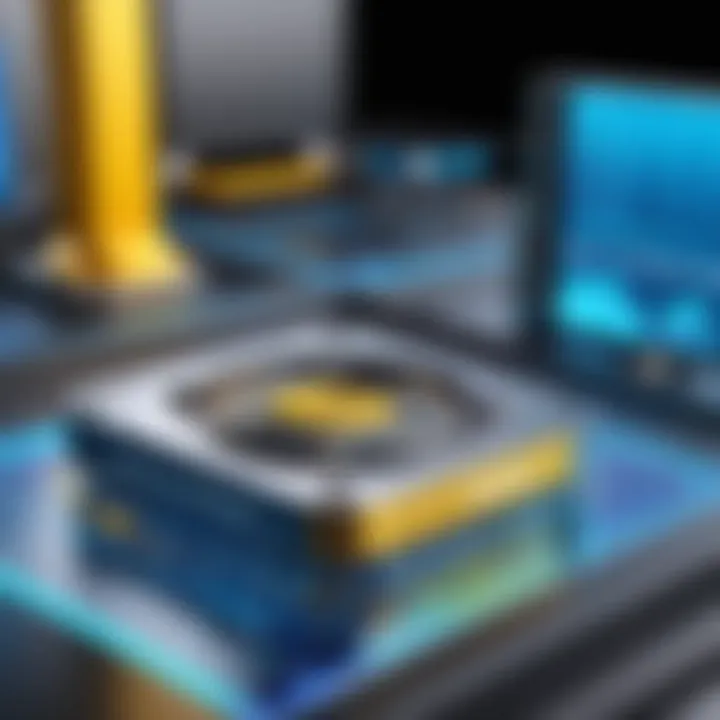
In the manufacturing sector, companies like Siemens have effectively used ANSYS Digital Twin technology to optimize their operational workflows. By creating detailed digital replicas of production lines, they can simulate various scenarios that affect output and efficiency.
- Predictive modeling: This helps in anticipating machinery breakdowns, thus allowing for smoother operation and reducing costs associated with downtime.
- Process adjustments: Simulation of changes in real-time ensures that resources are allocated efficiently, often leading to reduced waste.
- Quality control: Digital twins enable constant monitoring of product specifications, leading to reduced defects in the manufacturing process.
For instance, a large automotive manufacturer implemented a digital twin of its assembly line, resulting in an impressive 20% increase in production efficiency. With real-time feedback and adjustments made instantaneously, the manufacturer was able to optimize staffing and inventory levels.
Aerospace Efficiency Enhancements
In the aerospace realm, digital twins have become a game-changer, especially for companies like Boeing and Airbus. Creating hyper-detailed models of aircraft facilitates myriad benefits that go beyond mere simulation.
- Performance monitoring: Data from flights feeds back into the digital twin model, providing insights on wear and tear, which informs maintenance schedules. This proactive approach enhances aircraft reliability and safety.
- Design iteration: Engineers can test new designs in a virtual environment, significantly shortening development cycles and reducing costs.
- Operational analysis: Airlines can utilize digital twins to model entire fleets, optimizing fuel consumption and improving routing for cost savings.
Boeing, for example, reported a reduction in maintenance costs by 15% through their utilization of digital twins, translating to significant savings and enhanced trust from their stakeholders.
Healthcare Delivery Improvements
The healthcare industry has also embraced the principles of ANSYS Digital Twin technology to improve patient care and operational efficiency. Hospitals are now creating digital replicas of medical devices and even patient data to streamline service delivery.
- Patient monitoring: Digital twins can provide a real-time view of a patient’s vitals, helping healthcare providers intervene sooner if a patient’s condition deteriorates.
- Facility management: Utilizing digital twins for hospital layouts can help optimize space, leading to better patient flow and enhanced satisfaction.
- Equipment maintenance: Machines such as MRI and CT scanners can have their performance tracked through digital twins, ensuring timely maintenance and better operational uptime.
A notable example is that of Massachusetts General Hospital, which employed a digital twin of their cardiac monitoring system. They achieved a 25% improvement in diagnosis times, significantly enhancing patient outcomes while streamlining physician workflows.
"Case studies reveal not just data, but stories of innovation and resilience, showing how digital twins can turn challenges into actionable insights."
Through these explorations, it's evident that ANSYS Digital Twin technology provides not just theoretical benefits but creates substantial operational value when applied correctly. Each case study not only illustrates potential but also sets a benchmark for industries looking to adopt such transformative technologies.
Benefits of Using ANSYS Digital Twin
In a world increasingly driven by data and technology, the benefits of employing ANSYS Digital Twin technology cannot be overstated. This approach not only optimizes processes across multiple sectors but also radically transforms the way organizations operate. Decision-makers, IT professionals, and entrepreneurs stand to gain tremendously from integrating this technology into their workflows. The myriad benefits include improved decision-making, enhanced cost efficiency, and predictive maintenance capabilities that ultimately lead to sustainable growth.
Enhanced Decision-Making
Making informed decisions is the backbone of successful organizations. ANSYS Digital Twin provides a robust foundation for this by simulating real-world scenarios and processes in a virtual environment. This capability allows teams to visualize outcomes before they manifest, offering a clearer picture of possible futures. For instance, during product development, engineers can employ digital twins to assess the impact of design changes without needing physical prototypes.
Such simulations enable a dynamic approach to decision-making; instead of relying on gut feelings or past experiences, stakeholders can analyze current data reflected in the digital twin, thanks to the integration of real-time information. This proactive stance ultimately enhances strategic planning and reduces uncertainty in critical decisions.
Cost Efficiency and Resource Management
Cost containment and optimal resource allocation are perennial challenges in any industry. ANSYS Digital Twin technology tackles these issues head-on. Organizations can identify inefficiencies, minimize waste, and optimize resource utilization. The virtual representation enables a thorough analysis of processes and workflows, shedding light on potential improvements.
Key benefits of cost efficiency through digital twins include:
- Reduced Prototyping Costs: Traditional methods involve creating multiple physical models. With digital twins, simulations can replace several prototypes, saving both time and financial resources.
- Lower Operational Expenses: By predicting resource needs and maintenance schedules, companies can streamline operations and cut costs, leading to more effective budgeting.
- Optimized Supply Chains: Organizations can foresee supply chain disruptions in a digital landscape, allowing them to strategize better and avoid costly delays.
Predictive Maintenance Capabilities
One of the standout features of ANSYS Digital Twin is its predictive maintenance capabilities. This approach shifts maintenance from a reactive model to a proactive one. Instead of addressing issues after they arise, organizations can anticipate equipment failures and schedule maintenance before a breakdown occurs.
Imagine a manufacturing plant employing a digital twin of a critical machine. By continuously monitoring performance and wear through sensors, the digital twin can analyze patterns that signal impending failure. This information allows teams to carry out maintenance tasks just in time without unnecessary interruptions or costly repairs.
Utilizing predictive maintenance has several advantages including:
- Increased Equipment Lifespan: By addressing issues before they escalate, the life expectancy of machinery improves.
- Minimized Downtime: Predictive insights lead to planned downtimes, reducing unexpected interruptions in production.
- Enhanced Productivity: With fewer equipment failures, overall productivity remains high, aligning with business goals.
"Digital Twin technology has the potential to serve as a guiding compass in today's uncertain waters, steering firms towards a more efficient and foresighted future."
By recognizing these benefits, decision-makers can better position their organizations for success in an increasingly competitive market.
Challenges in Implementation
As industries rush to harness the capabilities of ANSYS Digital Twin technology, they confront a series of challenges that can be significant hurdles to its successful implementation. Understanding these challenges not only highlights the intricacies involved in integrating digital twins into existing frameworks but also the crucial considerations that decision-makers must address to ensure a seamless transition. This section will delve into three major challenges: data security concerns, integration with existing systems, and scalability issues.
Data Security Concerns
In today's digital landscape, where data breaches and cyber threats are rampant, security emerges as a paramount concern for any technology integration. When implementing digital twins, companies generate massive amounts of data, often including sensitive operational information and intellectual property. This data must be fiercely protected to prevent unauthorized access or breaches that could lead to devastating financial and reputational damage.
Efforts to secure this data involve:
- Implementing robust encryption protocols for data at rest and in transit.
- Utilizing multi-factor authentication (MFA) to protect against unauthorized access.
- Conducting regular audits and assessments to identify and rectify vulnerabilities.
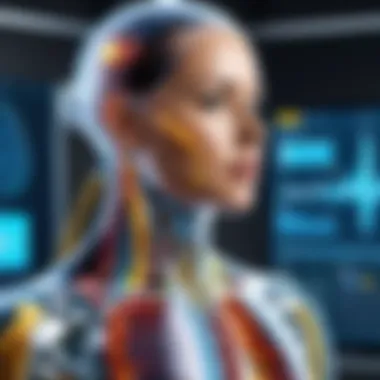
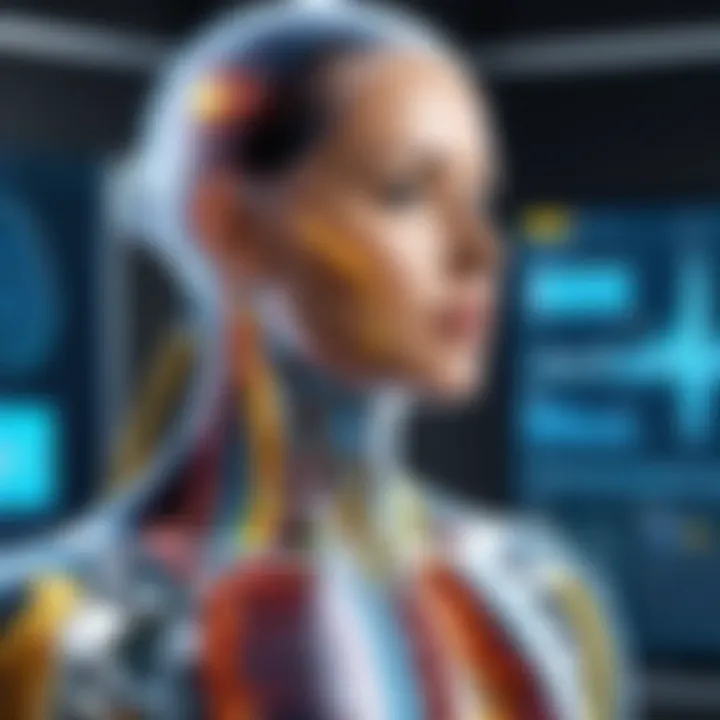
When organizations think about these layers of security, they can better manage the risks associated with data breaches. Furthermore, fostering a culture that prioritizes cybersecurity awareness among employees is essential as humans often represent the weakest link in the security chain.
Integration with Existing Systems
Integrating ANSYS Digital Twin technology with pre-existing systems can often feel like trying to fit a square peg in a round hole. Many companies already possess legacy systems that have been in place for years, sometimes decades. These systems may not have been designed to communicate with more modern technologies, which can lead to considerable integration headaches.
The integration hurdles include:
- Compatibility issues between different software and hardware solutions.
- Data silos, where information is trapped within one system and not easily shared across platforms.
- Employee training needed to manage new software a and workflows effectively.
To overcome these hurdles, businesses should consider a phased approach. This involves gradually implementing digital twins alongside existing systems, allowing for necessary adjustments and modifications to be made along the way. Ensuring that all staff involved are adequately trained can also contribute to a smoother transition.
Scalability Issues
As organizations grow and their operations evolve, the scalability of digital twin technologies must also be considered. A successful implementation needs to accommodate changes without excessive cost or effort. The challenge lies in ensuring that the digital twin model can scale up or down based on the organization's needs.
Key considerations regarding scalability include:
- Infrastructure requirements, which can change dramatically as data volumes increase.
- Cost management, as scaling might entail additional expenses in both hardware and software.
- Performance optimization to maintain efficient data processing as the system grows.
To tackle scalability issues, businesses can utilize cloud-based solutions that provide flexibility and can adapt to changing demands. Additionally, adopting modular architectures can facilitate easier scaling as companies can add components based on specific needs without overhauling entire systems.
The pathway to effective digital twin implementation is laden with challenges, yet these challenges present opportunities for strategic growth and innovation.
In summary, while the potential of ANSYS Digital Twin technology is promising, confronting challenges related to data security, integration, and scalability head-on is essential for businesses seeking to leverage its benefits fully. The ability to navigate these hurdles will ultimately determine the success of digital twin strategies in any organization.
Future Trends in Digital Twin Technology
The landscape of digital twin technology is evolving at a rapid pace, and keeping an eye on future trends is crucial for organizations looking to harness the full potential of these advanced systems. As industries become increasingly interconnected and reliant on data-driven decisions, understanding what's on the horizon can provide insight into the benefits and considerations associated with digital twins' future implementations. Here, we explore two primary trends: the integration of AI and machine learning and the advancements in IoT applications.
AI and Machine Learning Integration
The marriage of AI and machine learning with digital twin technology is reimagining how businesses operate and innovate. By embedding intelligent algorithms within these virtual replicas, organizations can glean actionable insights and reduce manual intervention. The fusion enhances predictive analytics, allowing enterprises to foresee potential failures or inefficiencies before they occur.
- Benefits of AI Integration: Automation: Processes can be automated, reducing human error and improving efficiency.
- Enhanced Predictions: AI helps predict outcomes using historical data, which allows for better resource allocation.
- Adaptive Learning: Systems can adapt based on new data inputs, ensuring the digital twin evolves with real-world changes.
Consider a manufacturing plant where an AI-enhanced digital twin continuously learns from machine behavior. If the twin detects a pattern indicating a potential malfunction in a machine, it can alert operators, essentially functioning like a crystal ball for maintenance.
"AI in digital twins is not just about predictions; it's about creating a living, breathing model that evolves with each data point." - Industry Expert
Advancements in IoT Applications
Internet of Things (IoT) applications are paving the way for more sophisticated digital twins by providing real-time data from physical assets. With more devices becoming interconnected, the amount of data generated is vast and growing. Digital twins can harness this data, allowing for detailed analysis of operations and performance.
- Impact of IoT on Digital Twins:
- Real-Time Visibility: Assets can be monitored in real-time, offering immediate insight into their performance.
- Improved Decision-Making: With access to up-to-the-minute data, decision-makers can make informed choices quickly, driving better outcomes.
- Seamless Integration: Digital twins can integrate with existing IoT platforms, creating a more cohesive system.
For instance, in the healthcare sector, a patient monitoring system utilizing IoT creates a digital twin of the patient's health metrics. Any significant changes trigger alerts to healthcare providers, ensuring timely intervention. This not only improves patient care but also optimizes resource usage.
The integration of IoT with digital twins holds immense promise for sectors seeking to leverage the wealth of data generated by connected devices. The careful alignment of technological advancements with organizational objectives will be pivotal in harnessing the full potential of digital twin solutions.
Ultimately, as the synergy between digital twins, AI, and IoT deepens, organizations poised to engage with these technologies stand to gain a competitive edge that could drive innovation and efficiency for years to come.
The End
In reflecting on the ANSYS Digital Twin technology, it is clear this innovation holds exceptional significance across multiple industries. The technology is not merely a trend; rather, it's becoming a cornerstone for enhancing operational efficiency, facilitating informed decision-making, and enabling predictive capabilities that were unthinkable just a few years ago.
Recap of Key Insights
Throughout this article, we explored the various facets of ANSYS Digital Twin technology. We began by defining the foundational concepts, setting the stage to recognize how pivotal this technology is in the modern industrial landscape. Key insights include:
- Integration of real-time data: By harnessing live data, businesses can optimize their processes in real time, observing system behaviors that help in refining operations.
- Application in diverse sectors: From manufacturing to healthcare, the versatility of ANSYS Digital Twin enables tailored solutions that can directly address sector-specific challenges.
- Case studies showcasing benefits: Real-life examples illustrated how organizations leveraged ANSYS to realize efficiency gains, reinforcing the tangible value of creating digital twins.
- Challenges that need consideration: Not all that glitters is gold; concerns surrounding data security, integration issues, and scalability must be adequately addressed for successful implementation.
The insights drive home the idea that while the potential of ANSYS Digital Twin technology is vast, a thorough understanding of its benefits and challenges is essential. This knowledge empowers decision-makers and IT experts to navigate the complexities of adopting such transformative technology.
Looking Ahead
The future of ANSYS Digital Twin technology appears promising. As industries continue to embrace digital transformation, the integration of more sophisticated technologies can be anticipated. Here are a few emerging trends worth keeping an eye on:
- Greater AI and machine learning integration: The combination of these technologies with digital twins will enable deeper insights and predictive analytics, fostering proactive rather than reactive decision-making.
- Advancements in the Internet of Things (IoT): An increased number of connected devices will facilitate richer datasets, enhancing the accuracy and reliability of digital twin simulations.
- Evolution in user interfaces: As the technology matures, user interfaces are likely to become more intuitive, broadening accessibility for non-tech users.
"In a rapidly advancing digital landscape, the organizations that adapt and evolve will lead the charge towards innovation and efficiency."
Continued exploration and investment in these technologies will not only shape how industries operate but will also redefine the standards of reliability and efficiency across a spectrum of applications. With the foundational knowledge outlined in this article, stakeholders can begin to leverage ANSYS Digital Twin technology, ensuring they are prepared for the challenges and opportunities that lie ahead.