Dynamics of Large Manufacturing and Digital Change
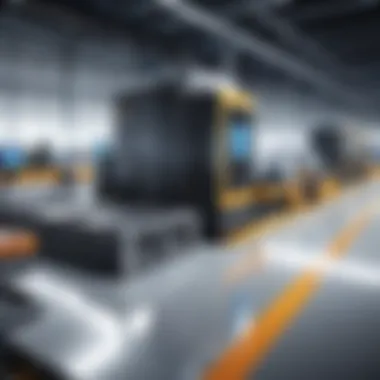
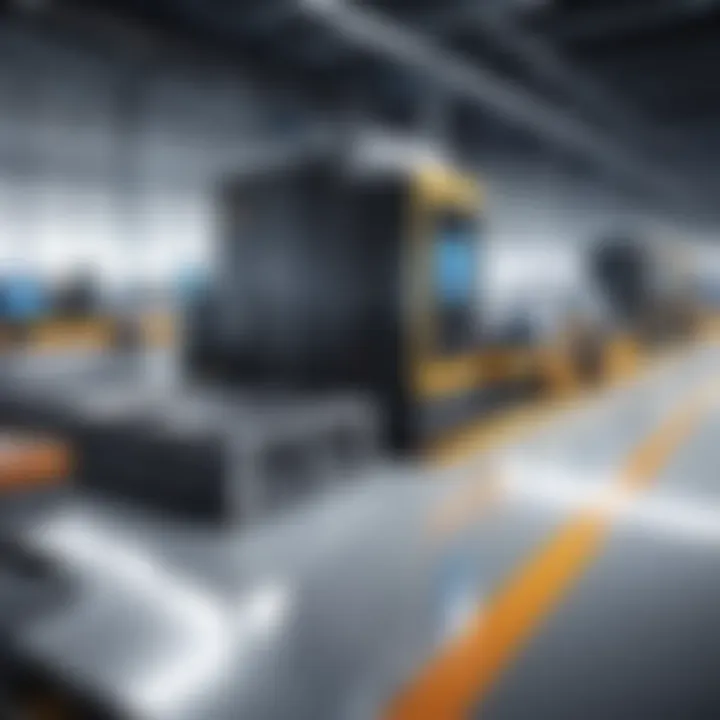
Intro
Navigating the landscape of large manufacturing companies reveals a realm both complex and dynamic. These entities donât merely churn out products; they drive economies, innovate processes, and adapt to incessant market shifts. With the onset of digital strategies, understanding their operational intricacies becomes paramount for decision-makers, IT professionals, and entrepreneurs alike.
Industry Overview
Large manufacturing companies operate at the intersection of technology and traditional practices. In an era where efficiency and responsiveness dictate success, the sector has witnessed a wave of digital transformation. The sheer size of these manufacturers often translates into unique challenges.
- Current Trends in the Industry-specific Software Market: The software landscape is shifting with tools designed to optimize supply chain management, enhance production scheduling, and streamline logistics. These solutions often leverage data analytics to provide insights that were previously unattainable, allowing for real-time decision-making that can reduce waste and improve output. The emergence of cloud-based solutions enables manufacturers to access their systems from anywhere, simplifying operations and communication.
- Key Challenges Faced by Buyers in the Industry: Many buyers grapple with understanding the multitude of available software options, which can lead to analysis paralysis. Furthermore, integrating new systems with legacy setups can be fraught with difficulties. Concerns around cybersecurity are paramount, too, as manufacturers become more digitally connected, exposing themselves to potential breaches that could disrupt operations.
- Emerging Technologies Impacting the Industry: Technologies like artificial intelligence, Internet of Things (IoT), and robotics are revolutionizing production lines. IoT devices, for example, allow for unprecedented connectivity between machinery, providing data that enhances predictive maintenance. AI algorithms can analyze this data to forecast trends, thus helping companies to manage inventory levels more efficiently.
Top Software Options
In light of this digital shift, it's crucial to look at the array of software solutions available. From enterprise resource planning systems to specialized manufacturing execution software, the choices can be overwhelming.
- Review of Leading Software Providers in the Industry: Industry leaders such as SAP and Oracle offer robust platforms designed to integrate various business functions into a single interface. Meanwhile, niche players like Plex and Epicor cater distinctly to manufacturing sectors, offering tailored solutions that address specific needs.
- Feature Comparison of Top Software Solutions: It's vital to compare features such as scalability, ease-of-use, and customizability. For instance, while SAP excels in comprehensive ERP solutions, Epicor might shine in manufacturing-specific functionalities.
- Pricing Structures of Different Software Options: Pricing can vary tremendously depending on the features and scale of implementation. Some solutions operate on a subscription model, while others might entail a hefty upfront licensing fee followed by maintenance costs.
Selection Criteria
Determining the right software solution is not a one-size-fits-all approach. Factors must be considered keenly.
- Important Factors to Consider When Choosing Software: Itâs essential to assess how the software aligns with your current and future business needs. The degree of support provided by the vendor, along with the community around the solution, can also impact your long-term satisfaction and utilization.
- Common Mistakes to Avoid During the Selection Process: A prevalent error is neglecting to involve end-users in the selection process. Their insights can offer a perspective that might be overlooked by decision-makers.
- How to Determine the Right Fit for Your Business Needs: Conducting a thorough needs assessment and comparing it against the features of potential solutions will help you gauge what matches your operations best.
Implementation Strategies
Once a software solution is selected, the implementation process looms. Hereâs how to navigate it effectively.
- Best Practices for Smooth Implementation of Software Solutions: Start small and scale as you gain confidence with the solution. Pilot programs can mitigate risk and allow for adjustments before a full rollout.
- Integration with Existing Systems and Processes: Many manufacturers have intricate legacy systems. Ensuring compatibility between new and old technologies is critical, not just for functionality but also for employee adaptation.
- Training and Support Resources for Successful Deployment: Invest in training sessions for all levels of users; not just the tech-savvy. Ongoing support from the provider can help with troubleshooting early on.
Future Trends
Looking ahead, the landscape of manufacturing is set to evolve rapidly.
- Predictions for the Future of the Industry-specific Software Landscape: As technologies mature, software will become more intelligent, potentially handling transactions autonomously and providing foresight into operations in ways weâve only begun to scratch the surface of.
- Upcoming Technologies Shaping the Industry: Concepts like quantum computing may play a role in data processing, providing deeper insights faster than current systems allow.
- Recommendations for Future-Proofing Your Technology Stack: Stay engaged with industry trends and be proactive in evolving your technology needs. Regular assessments should be conducted to ensure your stack is not left behind in a world thatâs moving at lightning speed.
Digital transformation is no longer optional. Itâs the lifeblood of survival in the manufacturing sector, and those who embrace it will thrive.
Prolusion to Large Manufacturing Companies
Large manufacturing companies significantly influence global economies and local industries. Understanding these enterprises is crucial for decision-makers, IT professionals, and entrepreneurs who aim to navigate the complex landscape of modern manufacturing. As these organizations evolve, they adapt to new technologies and market dynamics, emphasizing the need for a robust grasp of their operational intricacies.
Defining Large Manufacturing Enterprises
Large manufacturing enterprises can be defined as organizations that produce goods on a substantial scale, often utilizing advanced technologies and processes. Typically, they have a significant workforce, capital investment, and reach across international borders. Common characteristics of large manufacturers include:
- Capital Intensity: High investment in machinery, technology, and facilities.
- Scale of Operations: Production outputs that meet or exceed specific thresholds defined by national or international standards.
- Global Presence: Operations that span multiple countries, often involving intricate supply chains and distribution networks.
For instance, companies like General Motors or Siemens not only manufacture products but also drive innovation through R&D, market strategies, and global collaboration. Understanding what defines a large manufacturing enterprise can provide insight into their role in the economy and the challenges they confront.
Historical Context and Evolution
The landscape of manufacturing has undergone a seismic shift since the Industrial Revolution. Initially, manufacturing was characterized by handcrafting and localized production. As technology advanced, so did the scale and complexity of manufacturing processes. The rise of assembly lines in the early 20th century introduced a new era where efficiency and volume became paramount.
In recent decades, the emergence of computerization and automation has further transformed manufacturing. Companies are now leveraging technologies such as Artificial Intelligence, robotics, and IoT to streamline operations and enhance productivity. This transition reflects a broader trend toward digital transformation in the sector.
A quick glance at history highlights these crucial milestones:
- Industrial Revolution: Birth of mechanized production.
- World War II: Innovation accelerated by wartime production needs.
- Post-War Era: Expansion and globalization of manufacturing.
- Late 20th Century: Introduction of lean manufacturing and just-in-time inventory systems.
- 21st Century: Digitalization and sustainability becoming central themes.
Understanding where large manufacturing companies have come from is key to grasping their current dynamics and future trajectory. These historical insights not only frame the industryâs evolution but also shed light on strategic considerations that decision-makers face today.
"In the world of manufacturing, adapting is not just a choice; it is a necessity to thrive amid constant change."
Through recognizing these foundational aspects, stakeholders can better position their strategies to align with ongoing shifts in technology, market demands, and operational efficiencies.
Economic Influence of Large Manufacturing Companies
The economic clout of large manufacturing companies is undeniable. They donât just produce goods; they serve as the backbone of many economies, driving job creation, innovation, and global trade. The significance of examining economic influence is multifaceted, touching upon global supply chains, national economy contributions, and the rippling effects of manufacturing on various industries. It encapsulates the ways in which manufacturing shapes economic landscapes, underlining its relevance for policymakers and entrepreneurs alike.
Global Supply Chains and Trade
Manufacturing giants are at the heart of global supply chains. Their operations often span across continents, fostering a network that links raw materials, labor, and markets. Successful large manufacturers rely on an intricate web of suppliers, logistics, and distribution channels. Each link in this supply chain serves as a conduit for trade, enhancing the flow of capital and goods worldwide.
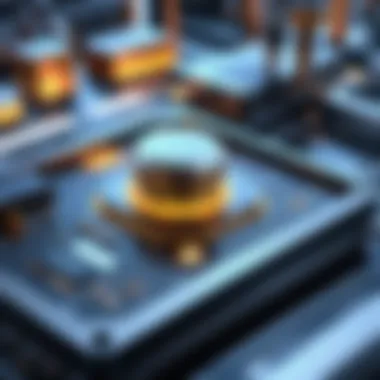
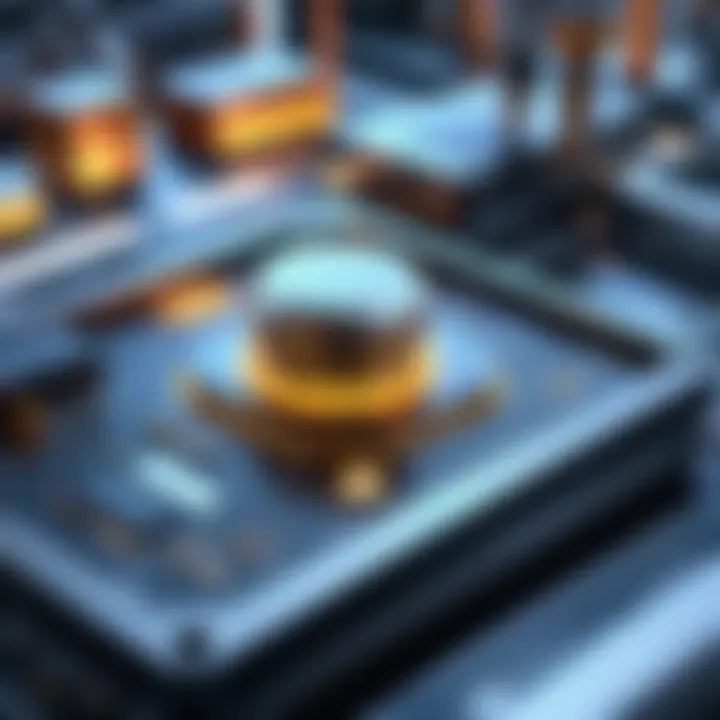
For instance, a company such as Boeing not only produces aircraft but also sources parts from various manufacturers globally, creating jobs in many countries while establishing a global footprint. This reflects a high degree of interdependence among markets, making it essential for countries to cooperate in trade agreements and regulations.
- The advantages of this interconnectedness include:
- Market Efficiency: Optimized production processes and distribution reduce costs.
- Risk Diversification: Spreading suppliers across regions mitigates risks associated with local disruptions.
- Innovation Sharing: Collaboration fosters tech advancements by sharing knowledge and expertise among partners.
However, complexities arise as companies navigate tariffs, regulatory barriers, and geopolitical tensions. The recent pandemic illustrated how vulnerable supply chains can be to external shocks, necessitating a reevaluation of dependencies and processes.
Contribution to National Economies
Large manufacturing firms contribute significantly to their respective national economies. They do so in various ways, helping to create a robust economic framework. The very act of producing goods translates into jobsâ from factory workers to managerial positionsâsignificantly influencing domestic employment rates. This contributes to disposable incomes, stimulating consumption across other sectors.
Moreover, large manufacturers often engage in significant investments in infrastructure, research and development, and community development. Companies like General Motors and Samsung not only provide jobs but also drive local economies. Consider the beneficial effects:
- Increased Tax Revenue: Large manufacturers generate substantial tax contributions, which fund public services and infrastructure.
- Technology Transfer: By investing in R&D, manufacturing companies often lead advancements that can spill over into other industries, enhancing overall productivity.
- Global Competitiveness: A strong manufacturing sector can elevate a country's presence in international markets, facilitating export growth.
"Large manufacturers are key to not just producing goods; they play a critical role in creating economic stability, innovation, and growth."
As these firms continue adapting to market demands, their economic influence is bound to evolve, presenting ongoing challenges and opportunities for stakeholders engaged in manufacturing or related sectors.
Operational Structures of Large Manufacturing Firms
Understanding the operational structures of large manufacturing firms is crucial for several reasons. These structures not only determine how effectively a firm can deliver products but also influence its adaptability to changing market conditions. By having a clear sense of divisions, specializations, and supply chain management, firms can optimize resources, enhance productivity, and ultimately drive profitability.
Divisions and Specializations
Large manufacturing companies often organize themselves into various divisions. This segmentation allows for specialized focus, enabling different parts of the organization to harnass their strengths in certain areas. For instance, a car manufacturing firm might have divisions dedicated to design, production, quality control, and logistics.
Specialization fosters efficiency, helping companies attain a higher level of expertise in each aspect of their production cycle. However, it's not just about dividing labor; it's also about creating connections among these divisions for a cohesive workflow. Itâs like a well-orchestrated symphony, where each instrument - or division - plays its part while contributing to the overall harmony of production.
- Key Benefits of Divisions:
- Enhanced expertise in specialized functions.
- Better resource allocation.
- Improved accountability and performance tracking.
While divisions provide clarity and efficiency, they also present a challenge. Poor coordination among divisions can lead to inefficiencies and miscommunication. Therefore, the effective integration of these specialized teams is essential, requiring strong leadership and communication protocols.
Supply Chain Management Dynamics
The dynamics of supply chain management in large manufacturing firms are equally critical. A robust supply chain is like the backbone of the manufacturing process. It ensures that materials are sourced timely, production processes are aligned, and finished goods reach the market without unnecessary delays.
Supply Chain Considerations:
- Supplier Relationships: Cultivating good relationships with suppliers is key. Companies often employ negotiation strategies to ensure favorable terms and quality materials.
- Logistics Management: This includes the movement of goods from suppliers to manufacturing plants and then from plants to customers, which can be complex and requires meticulous planning.
- Inventory Control: Proper inventory systems can prevent situations where production halts due to lack of materials or, conversely, where excess inventory ties up crucial cash flow.
"A well-structured supply chain acts as a lifeline for manufacturing firms, directly influencing their ability to respond to market demands."
Moreover, technology now plays a significant role in managing supply chains more effectively. The integration of tools like ERP systems allows a firm to gather data, analyze trends, and anticipate supply chain issues before they become critical problems. Keeping a pulse on the supply chain dynamics helps firms not just to respond but to proactively plan for future demands
It's evident that the operational structures within large manufacturing firms, particularly their divisions and supply chain management practices, directly impact their overall success. Navigating these complexities demands not just strategic insight but also a deep understanding of each facet of the operation, underscoring the importance of continual evaluation and adaptation in an ever-changing landscape.
Technological Advancements in Manufacturing
In today's fast-paced environment, the significance of technological advancements in manufacturing cannot be overstated. The incorporation of cutting-edge technology into manufacturing practices has become indispensable for ensuring efficiency and maintaining competitiveness. By leveraging advanced tools and methodologies, companies can streamline operations, reduce production costs, and enhance product quality. Amidst the challenges posed by a rapidly evolving market landscape, embracing technological innovations is not merely a choice; it's a necessity.
The Role of Automation and Robotics
Automation and robotics are at the forefront of manufacturing innovations. These technologies significantly transform the landscape of production, offering myriad benefits that range from efficiency boosts to safety improvements.
The Benefits of Automation
- Increased Efficiency: Automated systems can operate continuously without fatigue, allowing for higher output rates. This translates into faster production times and the capacity to meet growing consumer demand swiftly.
- Consistency and Quality Control: Robots excel in performing repetitive tasks with precision. This consistency helps in minimizing defects, thus enhancing the overall quality of products.
- Labor Cost Savings: While the initial investment can be steep, long-term savings on labor costs often justify the expenditure on automation technologies. Moreover, reallocating human workers to more strategic roles can lead to improved job satisfaction and productivity.
Automation is not a one-size-fits-all solution, however. Implementing these systems requires careful planning and consideration of existing workflows. Companies like Fanuc and ABB, known for their innovation in robotics, have provided frameworks for effective transitions to automated environments. Industry players must remain vigilant against over-automation, which can reduce flexibility and adaptability.
"Innovation is the ability to see change as an opportunity â not a threat."
â Anonymous
Integration of IoT in Manufacturing Processes
The Internet of Things (IoT) has ushered in a new era in manufacturing, where devices and machinery communicate seamlessly. Integrating IoT into manufacturing processes offers remarkable advantages and insights.
Specific Benefits of IoT
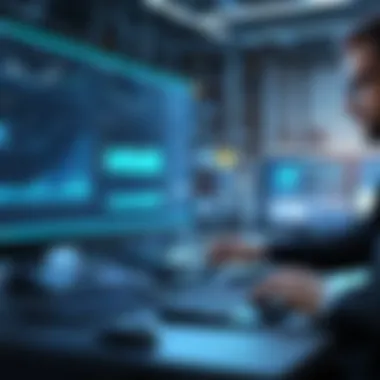
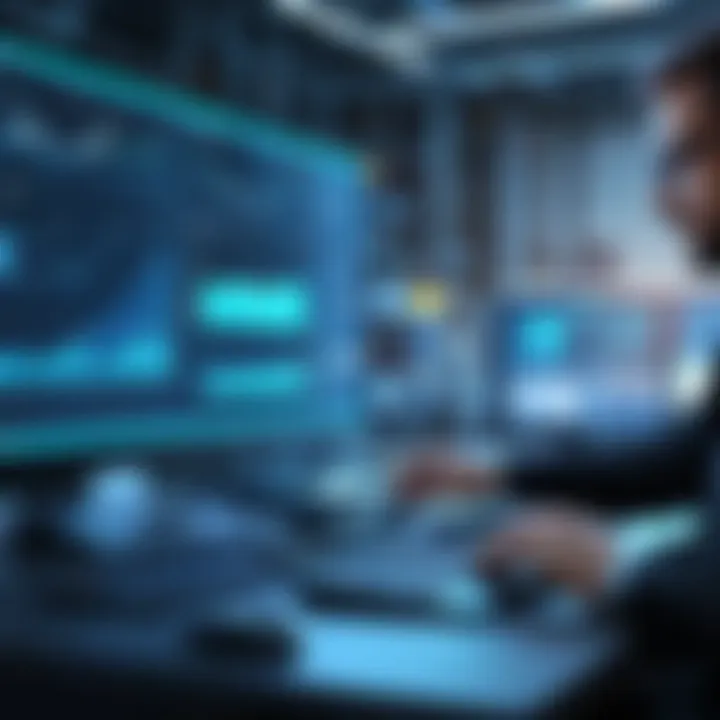
- Real-time Monitoring: IoT devices facilitate continuous oversight of production processes, making it easier to spot issues before they escalate into costly problems.
- Predictive Maintenance: Sensors on machinery can predict when a part is likely to fail, allowing for proactive maintenance that minimizes downtime and improves longevity.
- Data-Driven Decisions: The data collected through IoT devices empowers managers to make informed decisions based on solid metrics, improving efficiency and reducing waste.
IoT implementation comes with its challenges, too. Issues like data security, system integration, and the need for skilled personnel to interpret data analytics must be addressed. Companies such as Siemens and General Electric exemplify organizations that are leveraging IoT successfully to transform traditional manufacturing systems into smart factories.
Challenges Faced by Large Manufacturing Companies
In the evolving landscape of manufacturing, large companies stand to gain or lose based on how effectively they navigate challenges. The capacity to adapt to various pressures not only dictates their operational viability but also shapes their overall strategic direction. Manufacturing is rife with hurdles, from compliance demands to the pressing need for sustainability. Understanding these challenges is vital for stakeholders who are crafting policies and strategies that will be effective in an increasingly complex industrial environment.
Compliance and Regulatory Issues
Large manufacturing companies often tread a fine line when it comes to compliance and regulatory frameworks. These regulations vary widely by country, and failing to adhere can lead to severe penalties. They impact everything from health and safety to environmental standards. Larger firms, given their vast operational scope, must ensure that their practices align across different jurisdictions.
Moreover, the evolving nature of regulations adds another layer of complexity. For instance, recent trends show a growing focus on data privacy and cybersecurity. The General Data Protection Regulation (GDPR) in Europe has set a bar that manufacturers must meet, or risk hefty fines.
- Key considerations for compliance include:
- Tracking multiple regulatory standards across different regions.
- Implementing training programs to ensure all employees understand compliance obligations.
- Utilizing technology solutions like Compliance Software to monitor and adapt to changes in regulations.
Ultimately, the stakes of regulatory compliance are high. Companies that prioritize this not only ward off legal consequences but also foster trust with clients and consumers.
Sustainability and Environmental Concerns
Environmental sustainability is no longer an optional add-on; itâs a central pillar of modern manufacturing. Stakeholdersâincluding investors, customers, and governmentsâdemand greater accountability when it comes to environmental practices. Large manufacturing firms often find themselves under intense scrutiny for their carbon footprints. Being a major contributor to industrial emissions, their impact is noteworthy.
Strategies for addressing sustainability vary, but several common trends can be identified:
- Adopting Green Technologies: From renewable energy sources to cleaner production techniques, investing in greener technologies has become essential.
- Circular Economy Practices: Many manufacturers are now rethinking their processes, aiming to reuse materials and minimize waste. This not only helps in regulatory compliance but can also lead to cost savings.
- Supply Chain Transparency: Stakeholders are increasingly interested in where and how products are made. Companies must ensure that their supply chains are sustainable as well, evaluating partnersâ environmental practices.
"Companies that ignore environmental concerns do so at their peril. Sustainability is not just a trend; it's the future of manufacturing."
By actively addressing environmental issues, large manufacturing firms can not only enhance their brand image but also contribute positively to larger ecological goals.
In sum, the crossroads of compliance and sustainability presents significant challenges for large manufacturing companies. Navigating these elements demands strategic foresight and a willingness to adapt. By adopting a proactive approach, firms can turn these challenges into opportunities for growth and innovation.
Digital Transformation in Manufacturing
Digital transformation has emerged as a linchpin in evolving the landscape of large manufacturing companies. With the advent of advanced technologies, firms are rethinking their operational models to remain competitive on a global scale. This transformation is not merely about integrating new tools; it signifies a fundamental shift in how businesses operate and deliver value. By leveraging digital technologies, companies can significantly enhance productivity, improve efficiency, and foster innovation.
In essence, digital transformation in manufacturing catalyzes several key changes:
- Improved Data Utilization: Companies now collect vast amounts of data through sensors and IoT devices. The ability to analyze this data streamlines decision-making processes.
- Operational Efficiency: Automation minimizes human error and speeds up production. As such, firms adopting such practices benefit from reduced costs and increased output.
- Enhanced Customer Experience: With digital solutions, companies can better understand customer needs and preferences, tailoring their products accordingly. This agility can differentiate a manufacturer in a crowded market.
Embracing these changes requires consideration of various factors, including staff training, technology investments, and long-term strategy alignment.
Embracing Industry 4.
Industry 4.0 represents the next phase of industrial revolution characterized by smart technology and automation. It's not just a trend but a transformation that often involves an array of technological advancements such as artificial intelligence, machine learning, and advanced robotics.
For large manufacturing companies, embracing Industry 4.0 can yield several key advantages:
- Increased Adaptability: Companies can respond quicker to market changes and consumer demands.
- Service Optimization: Predictive maintenance and real-time analytics mean less downtime and better resource management.
For firms willing to invest in these innovations, the rewards can be far-reaching, reshaping their product lines and operational efficiencies.
Software Solutions for Enhanced Operations
In the era of digital transformation, software solutions play a critical role in the enhancement of operational processes within manufacturing firms. These systems facilitate everything from inventory management to production scheduling, paving the way for streamlined operations. Two prominent software solutions include Enterprise Resource Planning (ERP) systems and Manufacturing Execution Systems (MES).
Enterprise Resource Planning (ERP) Systems
ERP systems are transformative tools for integrating core business processes across various departments. They consolidate data and streamline information flow, which is pivotal in making informed decisions. A critical characteristic of ERP systems is their ability to:
- Centralize Data: With everything stored in one place, teams can access real-time metrics, reducing the likelihood of errors that arise from scattered information.
- Facilitate Collaboration: Different departments can work together smoothly, with visibility into cross-departmental operations.
However, ERP systems come with their unique challenges, including high implementation costs and the need for robust user training. Companies must weigh the advantagesâlike improved efficiencyâagainst these factors.
Manufacturing Execution Systems (MES)
On the other hand, MES focuses on optimizing production processes on the shop floor. It acts as a bridge between enterprise-level ERP systems and real-time production data. A key feature of MES is:
- Real-Time Monitoring: This allows managers to track production in real-time, leading to faster adjustments and better overall output.
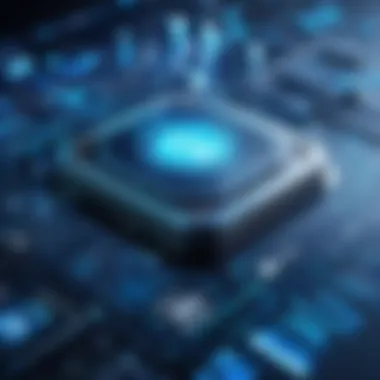
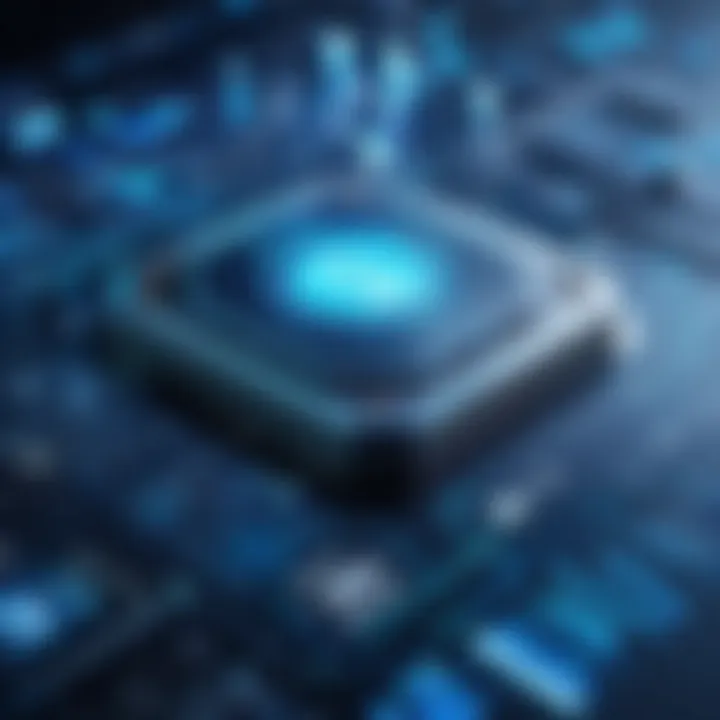
While MES can significantly enhance operational efficiency, challenges can arise related to integration with existing systems. Firms must approach the adoption of MES carefully to align it with their long-term operational goals.
"Digital transformation is not a project or a destination, but a continuous journey towards harnessing technology for better operational efficiency and customer satisfaction."
In summary, the role of software solutions like ERP and MES is critical in navigating the complexities of digital transformation in large manufacturing firms. By making informed choices about these systems, decision-makers can better position their companies for future challenges and opportunities.
Strategic Decision-Making in Large Manufacturing Firms
Strategic decision-making serves as the compass for large manufacturing firms, guiding them through the complexities of the industrial landscape. In an age where rapid change is the norm, the ability to make informed, data-driven choices is essential. Companies that hone their decision-making processes are better equipped to navigate market fluctuations, resource challenges, and evolving consumer demands.
One of the pivotal elements of strategic decision-making is the integration of data-driven processes. In this digital era, vast amounts of data are generated daily, from production metrics to customer feedback. Harnessing this data allows firms to gain invaluable insights into their operations. By analyzing trends and identifying patterns, manufacturing companies can make informed adjustments that optimize efficiency and productivity.
Additionally, effective strategic decision-making involves utilizing robust benchmarking and performance metrics. By comparing their operations against industry standards, companies can identify gaps in performance. This can lead to actionable strategies for improvement, ensuring they remain competitive. Performance metrics guide organizations by setting measurable goals which can be consistently tracked.
In summary, the significance of strategic decision-making extends beyond mere operational management. It shapes the future direction of manufacturing companies, ensuring they adapt, evolve, and thrive in a challenging business environment.
Data-Driven Decision Processes
The foundation of a successful decision-making strategy lies in the utilization of data. Data-driven decision-making is about more than just collecting numbers; itâs about transforming information into knowledge. When manufacturers leverage data analytics, they can pinpoint inefficiencies, forecast future trends, and tailor their offerings to meet market needs.
For instance, consider a large automotive manufacturer analyzing supplier lead times through data analytics. By doing so, the firm can identify which suppliers consistently delay shipments. These insights allow the company to possibly renegotiate contracts or find alternative suppliers, effectively reducing downtime in production.
- Benefits of Data-Driven Processes:
- Enhanced accuracy in forecasting
- Quick identification of market trends
- Smarter, more strategic resource allocation
With these benefits, it's clear that data-driven processes are not just an option but a necessity for large manufacturers aiming to stay competitive.
Benchmarking and Performance Metrics
In the world of manufacturing, knowing where you stand relative to your peers can be a game changer. Benchmarking provides a clear view of how a company performs compared to industry standards. Companies often gather data on various performance indicators such as production efficiency, defect rates, and inventory turnover.
Performance metrics serve as a roadmap; without them, companies could wander aimlessly. By focusing on specific KPIs (Key Performance Indicators), manufacturers can direct their efforts in a concerted manner.
"Without data, you're just another person with an opinion." - W. Edwards Deming
Key performance indicators help in tracking progress and help in making necessary adjustments to meet organizational goals. For example, if a manufacturer sets a target to decrease defect rates by 10% within a quarter, performance metrics allow them to track their progress and make informed decisions that lead to better product quality.
Ultimately, effective benchmarking and thorough understanding of performance metrics empower manufacturing firms to make solid strategic choices, paving the way for long-term profitability and sustainability.
The Future of Large Manufacturing Companies
In an era where technology intertwines seamlessly with traditional methods, the future of large manufacturing companies is a captivating subject. This discussion is vital as it shines a light on how these companies can adapt to challenges and seize opportunities presented by advancing technologies and evolving market demands. The significance of understanding future trends aids decision-makers in crafting strategies that not only respond to the here and now but also anticipate the shifts in landscape. By exploring the crucial elements of these forthcoming trends, stakeholders can align their operations for sustainable growth.
Trends Shaping the Industry
The manufacturing space is witnessing a whirlwind of changes. Some of the paramount trends include:
- Smart Manufacturing: This incorporates the latest buzzwords like AI and machine learning, which help in streamlining operations. Companies are increasingly leveraging data analytics to create a more integrated and informed manufacturing process.
- Sustainability: Manufacturers are under pressure to cut emissions and use eco-friendly materials. This is no longer just a trend but a fundamental shift towards corporate responsibility.
- Customization: Today's consumers are demanding personalized products. Manufacturers are adapting to this by allowing more flexible production methods that can cater to diverse needs without resulting in excess waste.
- Remote Monitoring and Control: The rise of IoT devices enables managers to keep an eye on their operations from anywhere, leading to real-time adjustments that boost efficiency.
These trends, while promising, come with their own sets of challenges as companies must balance between embracing innovation and dealing with legacy systems that may hinder progress.
Adapting to a Rapidly Changing Environment
To remain competitive, large manufacturing firms must also rethink their strategies. Adapting to changes is not just about shifting to new technologies, it involves a more holistic approach. Here are some considerations that can be highlighted regarding adaptation:
- Cultural Shift: Embracing change starts from within. Organizations need to cultivate a culture that promotes agility and innovation among employees. This means fostering an environment where ideas can flow freely.
- Collaboration: Manufacturers can benefit from working closely with tech companies and educational institutions. Such collaborations can lead to innovative solutions that may not have been possible in isolation.
- Continuous Learning: The landscape of manufacturing is continuously evolving. Companies need to invest in training and upskilling their workforce to stay abreast of new technologies.
- Investing in Research and Development: Companies that undertake R&D initiatives are better positioned to anticipate market trends. This proactive approach can define their future success.
"In the face of change, the companies that dare to innovate today will be the leaders of tomorrow."
Ending: The Path Forward for Large Manufacturing Companies
As we reach the culmination of our exploration into large manufacturing companies, it is crucial to underscore the relevance of this discussion in todayâs fast-evolving industrial landscape. These companies stand at a pivotal point, facing both opportunities and challenges that could dramatically reshape their trajectories. Navigating this path forward mandates a clear understanding of innovations and strategic shifts that can effectively guide their transformation efforts.
Innovations and Opportunities
One of the most significant aspects of the modern manufacturing landscape is the rapid pace of technological innovations.
- Automation and AI: Companies are harnessing automation not just to speed up production but also to enhance precision. Incorporating artificial intelligence into these processes allows for real-time data analytics that drive efficiency.
- Sustainability Practices: Todayâs consumers are increasingly conscious of the environmental impact of production. Companies that adapt through the adoption of green technologies can not only meet regulatory standards but also tap into a market that values sustainability. Implementing eco-friendly practices opens new avenues and fosters brand loyalty.
- Digital Twins: This innovation allows companies to create digital replicas of their operations. With simulations, manufacturers can predict outcomes, optimize efficiencies, and even pre-empt potential issues before they affect production.
"Innovation is the ability to see change as an opportunity, not a threat."
â Unknown
These advancements are not mere enhancements; they are essential for survival in a competitive global market. Pragmatically, the integration of these innovations can reduce costs significantly, ensure quicker workflows, and promote agility that legacy systems simply canât match.
Key Takeaways for Industry Stakeholders
For decision-makers in large manufacturing firms, understanding these dynamics is not optional but a necessity. Here are several key points to consider:
- Invest in Technology: Prioritize investments in emerging technologies that drive productivity and efficiency. This means not only upgrading machinery but also investing in the digital capabilities of the workforce.
- Adaptability is Crucial: As trends shift, so must strategies. Organizations need the flexibility to pivot and respond to emerging market demands and technologies.
- Collaborate and Build Ecosystems: Rather than going solo, forging alliances with tech firms and startups can provide access to innovations that enhance manufacturing processes.
- Assess and Implement: Regular evaluations of operational structures and strategies allow for the implementation of best practices adapted to current market conditions.
- Culture of Continuous Improvement: Foster a mindset that prioritizes ongoing learning and adaptation within the workforce. This cultural shift is imperative for embracing technological changes and remaining competitive.