Enhancing Operational Efficiency Through Spare Parts Inventory Control Strategies
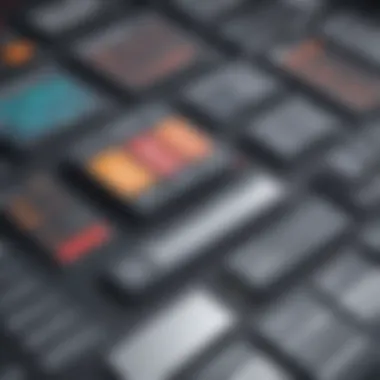
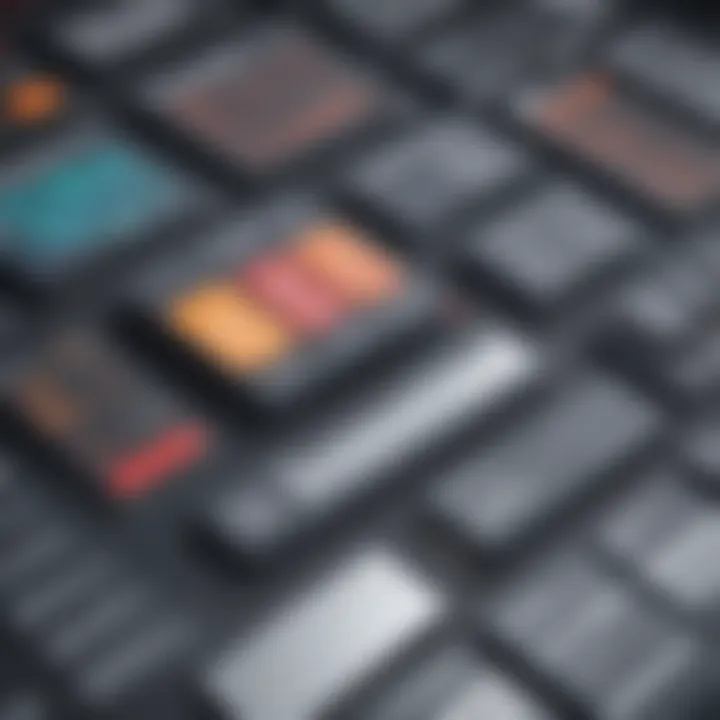
Industry Overview
In today's fast-paced business environment, the optimization of spare parts inventory management is crucial for enhancing operational efficiency. Efficiency in inventory control can directly impact production timelines, customer satisfaction, and overall business performance. By exploring innovative strategies, leveraging advanced technologies, and adopting best practices, organizations can streamline their inventory control processes and achieve optimal performance.
Current Trends in the Industry-specific Software Market
Within the industry-specific software market, there is a noticeable shift towards solutions that offer real-time visibility into spare parts inventory. Companies are increasingly investing in software that provides data analytics and predictive maintenance capabilities to minimize downtime and reduce operational costs. The demand for cloud-based inventory management platforms is also on the rise, allowing for greater flexibility and accessibility.
Key Challenges Faced by Buyers in the Industry
Buyers in the industry encounter several challenges when procuring inventory control software. These challenges include selecting a solution that aligns with their unique operational requirements, ensuring seamless integration with existing systems, and managing the complexities of data migration. Additionally, cost considerations, scalability, and user training pose significant hurdles for organizations seeking to optimize their spare parts inventory management.
Emerging Technologies Impacting the Industry
Emerging technologies such as artificial intelligence, machine learning, and Internet of Things (IoT) are revolutionizing inventory control for efficient operations. AI-driven predictive analytics can forecast demand patterns and optimize reorder points, while IoT sensors enable real-time monitoring of inventory levels. Leveraging these technologies empowers businesses to make data-driven decisions and proactively manage their spare parts inventory.
In the realm of industrial operations, the management of spare parts inventory plays a critical role in ensuring seamless functionality and cost-effectiveness. This article delves deep into the intricacies of optimizing spare parts inventory control to enhance operational efficiency. By exploring various strategies, incorporating technological solutions, and delving into best practices, this piece aims to offer valuable insights into streamlining inventory control processes for optimal performance.
Understanding Spare Parts Inventory Management
Definition of Spare Parts Inventory
Undoubtedly, the cornerstone of efficient spare parts inventory management lies in clearly defining what constitutes spare parts inventory. This pertains to the assortment of components and items kept in reserve to mitigate downtime and maintain uninterrupted operational continuity. The delineation of spare parts inventory sets the foundation for robust inventory control practices. Understanding the precise composition of spare parts inventory is crucial for efficient resource allocation and inventory optimization.
Importance of Efficient Inventory Control
Efficient inventory control stands as a pivotal factor in the smooth operation of industrial facilities. Optimal inventory control ensures that the right spare parts are available just when needed, minimizing equipment downtimes and bolstering overall productivity. The importance of maintaining an organized and streamlined spare parts inventory cannot be overstated, as it directly impacts operational performance and cost-effectiveness.
Challenges in Spare Parts Inventory Management
Despite its significance, spare parts inventory management poses various challenges that organizations must navigate. These challenges range from ensuring accurate demand forecasting to dealing with storage constraints and inventory wastage. Overcoming these obstacles demands strategic planning, agile inventory control systems, and proactive measures to address uncertainties in inventory management processes.
Significance of Effective Inventory Control
Impact on Operational Performance
Effective inventory control has a substantial impact on operational performance by optimizing resource utilization and ensuring timely availability of critical spare parts. Streamlined inventory control processes contribute to enhanced operational efficiency, reduced equipment downtimes, and increased overall productivity. By aligning inventory levels with operational demands, organizations can achieve seamless workflow and mitigate disruptions.
Cost Implications of Poor Inventory Management
Poor inventory management practices can lead to significant financial repercussions, including excess inventory costs, obsolete spare parts accumulation, and emergency procurement expenses. Inefficient inventory control can result in holding excessive stock levels or stockouts, both of which adversely affect the organization's bottom line. Implementing effective inventory control measures is crucial for cost savings and sustainable operational performance.
Customer Satisfaction and Service Levels
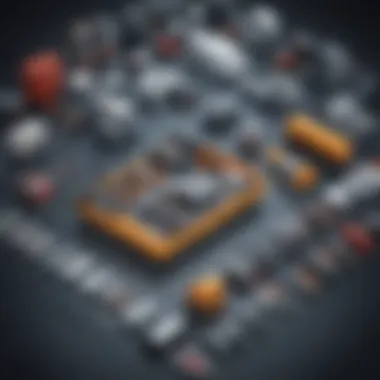
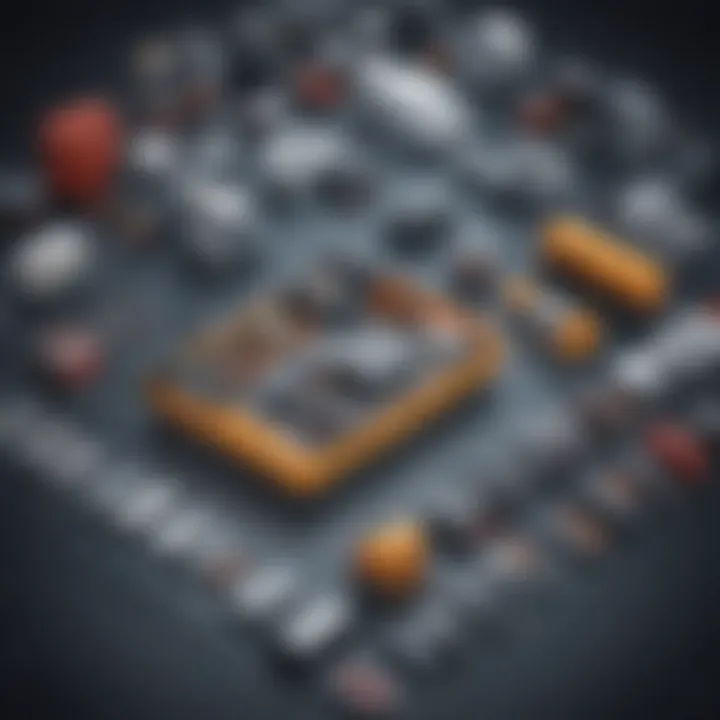
Maintaining optimal inventory control directly influences customer satisfaction levels and service quality. Timely delivery of products and services hinges on the availability of requisite spare parts, which is contingent upon efficient inventory control. Meeting customer demands promptly and ensuring service excellence necessitate a well-managed spare parts inventory system. Elevating service levels contributes to customer loyalty and strengthens the organization's competitive edge.
Strategies for Optimizing Spare Parts Inventory
In this section, we delve into the critical aspect of strategies for optimizing spare parts inventory. Efficient inventory management is crucial for operational success, minimizing costs, and enhancing customer satisfaction. By implementing robust strategies, organizations can streamline their spare parts inventory control processes, ensuring smooth operations and optimal resource allocation. These strategies encompass various elements such as forecasting, categorization, and optimization techniques. Emphasizing these aspects can lead to significant benefits, including improved inventory accuracy, reduced lead times, and enhanced overall efficiency.
Forecasting and Demand Planning
Utilizing Historical Data
The utilization of historical data plays a vital role in forecasting and demand planning. By analyzing past trends and consumption patterns, businesses can anticipate future demand more accurately, enabling proactive inventory management. Leveraging historical data helps in understanding cyclical variations, identifying seasonality effects, and forecasting demand fluctuations with greater precision. Despite its importance, historical data comes with limitations such as potential inaccuracies due to unforeseen events or irregularities that may skew predictions. It is crucial to validate historical data continuously to ensure reliability and optimize inventory planning efficiently.
Predictive Analytics for Demand Forecasting
Predictive analytics for demand forecasting integrates advanced algorithms and statistical models to predict future demand patterns. By leveraging predictive analytics, organizations can gain actionable insights into customer behavior, market trends, and external factors influencing demand. This predictive approach enhances forecast accuracy, minimizes forecasting errors, and empowers businesses to make informed decisions regarding inventory replenishment. However, the reliance on predictive analytics requires continuous data refinement, algorithm optimization, and adjustment to changing market dynamics to maintain forecasting precision.
Collaborative Planning with Suppliers
Collaborative planning with suppliers fosters a symbiotic relationship aimed at enhancing supply chain efficiency and inventory management. By engaging in cross-functional collaboration and information sharing, businesses and suppliers can align demand forecasts, production schedules, and inventory levels effectively. Collaborative planning promotes transparency, reduces lead times, and ensures timely replenishment of spare parts. While collaboration offers significant benefits, establishing and maintaining such partnerships require clear communication channels, mutual trust, and alignment of strategic objectives to achieve mutual success.
ABC Analysis and Categorization
In this segment, we explore the concept of ABC analysis and categorization as a fundamental approach to optimize spare parts inventory management. ABC analysis classifies spare parts based on their consumption value, with 'A' category items deemed most valuable and 'C' category items least essential. This categorization enables organizations to prioritize inventory management efforts, allocate resources according to part importance, and implement tailored control strategies. By segmenting inventory based on usage frequency or criticality, businesses can optimize stocking levels, minimize stockouts, and enhance resource utilization efficiently.
Classification of Spare Parts Based on Usage
The classification of spare parts based on usage provides a structured framework for inventory control, distinguishing between critical and non-critical items. By categorizing parts according to their importance in operational processes, organizations can allocate resources judiciously, maintain optimal stock levels, and prevent disruptions. This classification strategy enables businesses to streamline inventory management, reduce carrying costs, and ensure availability of vital spare parts when needed. However, oversimplification or misclassification can lead to inventory imbalances, inaccuracies in demand forecasting, and decreased operational efficiency.
Inventory Segmentation for Efficient Management
Inventory segmentation involves grouping spare parts based on common characteristics, such as consumption patterns, lead times, or criticality. By segmenting inventory into logical categories or segments, organizations can tailor their inventory control strategies, implement specific stocking policies, and optimize reordering processes. This segmentation approach enhances inventory visibility, facilitates demand planning, and enables agile inventory management. Nonetheless, effective inventory segmentation hinges on accurate data classification, consistent review of segment criteria, and alignment with operational requirements to avoid inefficiencies or mismanagement.
Allocation of Resources According to Priority
Allocating resources according to priority ensures that critical spare parts receive adequate focus and resources for effective inventory control. By assigning priorities based on part criticality, lead times, or production impact, businesses can optimize inventory levels, streamline procurement processes, and mitigate the risk of stockouts. This resource allocation method enhances operational resilience, promotes cost efficiency, and aligns inventory management practices with organizational objectives. However, the challenge lies in establishing clear criteria for resource prioritization, balancing conflicting priorities, and adapting resource allocation strategies to evolving operational demands.
Inventory Optimization Techniques
This section delves into various inventory optimization techniques essential for enhancing spare parts inventory management efficiency. By implementing effective optimization strategies, organizations can minimize carrying costs, optimize order quantities, and improve inventory turnover rates. These techniques focus on setting reorder points, calculating safety stock levels, utilizing economic order quantity models, and incorporating just-in-time inventory management principles.
Setting Reorder Points and Safety Stock Levels
Setting appropriate reorder points and safety stock levels is crucial for maintaining optimal inventory levels and preventing stockouts. Reorder points represent the inventory level at which new orders should be placed, considering lead times and demand variability. Safety stock acts as a buffer against unforeseen demand spikes, supplier delays, or quality issues. Balancing reorder points and safety stock levels requires a thorough understanding of demand patterns, lead times, and inventory holding costs to strike a balance between stock availability and carrying costs. Organizations can enhance order fulfillment reliability, minimize stock shortages, and improve customer satisfaction by fine-tuning reorder points and safety stock levels effectively.
Economic Order Quantity (EOQ) Model
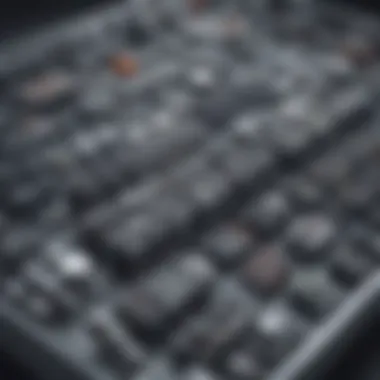
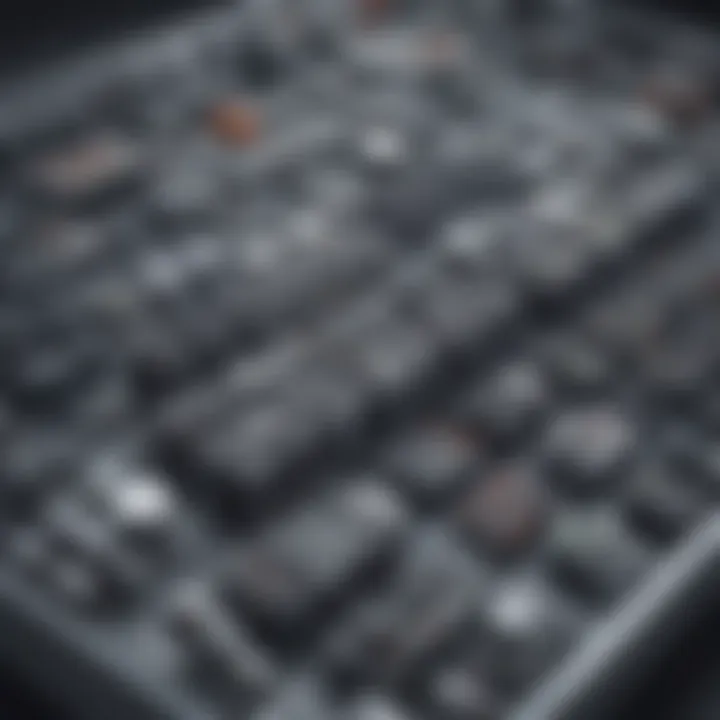
The Economic Order Quantity (EOQ) model presents a mathematical approach to determining the optimal order quantity that minimizes total inventory costs. By considering factors such as order costs, holding costs, and demand variability, organizations can calculate the most cost-effective order quantity that balances ordering and holding costs efficiently. Implementing the EOQ model helps businesses optimize inventory replenishment cycles, reduce excess inventory, and improve inventory turnover rates. However, the EOQ model assumes constant demand, stable lead times, and uniform ordering costs, which may pose challenges in dynamic or fluctuating supply chain environments.
Just-in-Time (JIT) Inventory Management
Just-in-Time (JIT) inventory management emphasizes achieving a smooth production flow and minimizing inventory holding costs by receiving goods only when needed in the production process. JIT principles focus on eliminating waste, reducing lead times, and enhancing production flexibility through synchronized supply chain processes. By adopting JIT inventory management, organizations can streamline operations, improve resource utilization, and respond quickly to changing customer demands. Despite its benefits, JIT implementation requires robust supply chain coordination, reliable supplier relationships, and stringent quality control to mitigate potential risks such as supply disruptions or demand fluctuations.
Technological Solutions for Inventory Control
In the realm of inventory management, technological solutions play a pivotal role in enhancing operational efficiency. By integrating advanced technologies, businesses can streamline their spare parts inventory control processes for optimal performance. These solutions encompass a wide array of tools and platforms designed to facilitate seamless inventory management and minimize operational disruptions. Leveraging technology in inventory control offers businesses the opportunity to improve accuracy, reduce lead times, and enhance overall productivity.
Inventory Management Software
Features and Benefits
Inventory management software is a revolutionary tool that revolutionizes how businesses manage their spare parts inventory. With its comprehensive features and benefits, this software enables organizations to automate inventory tracking, optimize stock levels, and streamline replenishment processes. One key characteristic of inventory management software is its ability to provide real-time visibility into inventory levels, ensuring better decision-making and inventory control. The unique feature of this software lies in its capacity to generate accurate demand forecasts, facilitating proactive inventory management and cost savings. While it offers numerous advantages, such as improved efficiency and inventory accuracy, businesses must also consider factors like scalability and integration capabilities to maximize its benefits.
Integration with Enterprise Resource Planning (ERP) Systems
The integration of inventory management software with Enterprise Resource Planning (ERP) systems is a game-changer for businesses looking to achieve seamless inventory control. This alignment ensures synchronization between inventory data and other critical business functions, enabling efficient resource utilization and enhanced operational visibility. By integrating with ERP systems, organizations can streamline data management processes, eliminate redundancies, and bolster decision-making capabilities. The key characteristic of this integration is its ability to centralize data management, minimizing errors and promoting operational efficiency. While this integration offers various benefits, such as improved data accuracy and process optimization, businesses should carefully evaluate factors like system compatibility and data security to leverage its full potential.
Real-time Tracking and Reporting Capabilities
Real-time tracking and reporting capabilities embedded in inventory management software are essential for maintaining inventory accuracy and optimizing operational performance. These capabilities allow businesses to monitor inventory movements, track stock levels, and generate reports in real time, facilitating effective decision-making and proactive inventory control. The key characteristic of real-time tracking and reporting is its ability to provide instant insights into inventory activities, enabling timely interventions and adjustments. The unique feature of this functionality lies in its capacity to customize reports and alerts based on business needs, enhancing operational visibility and control. While offering advantages like improved inventory accuracy and enhanced responsiveness, businesses must consider factors like data integration and system compatibility to leverage these capabilities effectively.
Internet of Things (IoT) in Spare Parts Management
Sensors and RFID Technology for Inventory Tracking
The integration of sensors and RFID technology in spare parts management revolutionizes inventory tracking processes, offering businesses unprecedented transparency and control over their inventory operations. These technologies enable real-time monitoring of inventory movements, automate restocking procedures, and enhance inventory accuracy. One key characteristic of sensors and RFID technology is their ability to provide granular insights into inventory locations and status, facilitating efficient inventory management and reduced lead times. The unique feature of these technologies lies in their capacity to automate data capture processes, minimizing manual errors and optimizing inventory control. While offering advantages like enhanced inventory visibility and operational efficiency, businesses should consider factors like initial setup costs and system compatibility when implementing these technologies.
Best Practices for Effective Spare Parts Inventory Management
Effective spare parts inventory management is crucial in ensuring smooth operations and cost-efficiency within a business. By implementing best practices, organizations can optimize their inventory control processes, leading to improved productivity and customer satisfaction. Key elements of best practices include establishing efficient supplier relationships, implementing robust lifecycle management strategies, and continuously monitoring performance indicators to drive impactful decision-making.
Supplier Relationship Management
Supplier Relationship Management plays a vital role in enhancing spare parts inventory management. Collaborative partnerships with suppliers enable streamlined procurement processes, leading to cost savings and timely inventory replenishment. By fostering strong relationships with suppliers, organizations can benefit from efficient communication channels, improved product quality, and innovative solutions tailored to their specific needs.
Collaborative Partnerships with Suppliers
Collaborative partnerships with suppliers involve mutual cooperation and shared goals to optimize inventory control. One key characteristic is the open exchange of information and resources, fostering a transparent and synergistic relationship. This partnership model is advantageous for this article as it promotes efficient inventory planning, reduces lead times, and ensures reliable spare parts availability. However, challenges may arise in aligning strategies and mitigating risks associated with external dependencies.
Vendor Performance Evaluation
Evaluating vendor performance is integral to assessing the effectiveness of supply chain partners. By monitoring key metrics such as on-time delivery, quality compliance, and cost-effectiveness, organizations can identify top-performing vendors and address underperforming ones. This evaluation process ensures that suppliers meet defined service levels, contributing to overall inventory optimization and operational efficiency. However, the subjectivity of performance assessments and evolving market dynamics present challenges in maintaining consistent vendor evaluations.
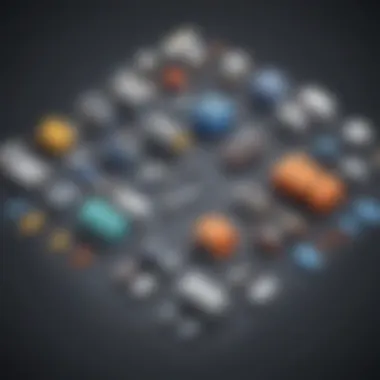
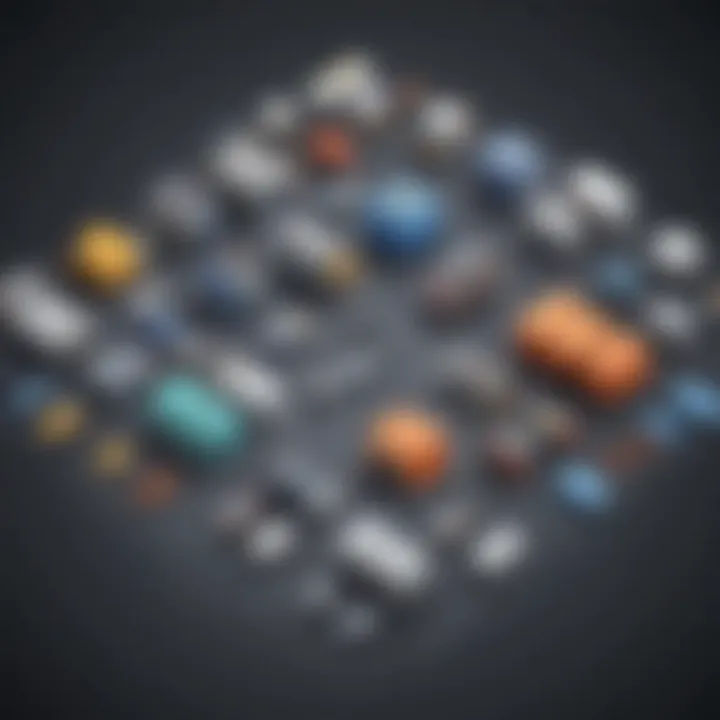
Effective Communication Channels
Efficient communication channels with suppliers are essential for proactive inventory management. Clear and prompt communication facilitates order adjustments, resolves issues promptly, and fosters trust between parties. The key characteristic of effective communication channels is the ability to relay information accurately and promptly, enabling smooth coordination in inventory transactions. This approach benefits the article by enhancing inventory responsiveness, reducing delays, and optimizing stock levels. Nonetheless, challenges such as language barriers and technological integration may impede seamless communication flow.
Lifecycle Management and Obsolescence
Lifecycle Management and Obsolescence strategies are critical for mitigating risks associated with obsolete inventory and ensuring sustained spare parts availability. By implementing proactive measures such as risk assessment, regular review protocols, and agile disposal strategies, organizations can minimize inventory write-offs and optimize resource allocation towards active stock items.
Managing Risks of Obsolete Inventory
Managing the risks of obsolete inventory involves identifying potential obsolescence triggers and implementing preventive measures. The key characteristic lies in conducting frequent stock assessments, tracking market trends, and promptly dispositioning slow-moving parts. In this article, managing risks of obsolete inventory offers the advantage of reducing carrying costs, optimizing storage space, and enhancing inventory turnover rates. However, challenges may arise in accurately predicting obsolescence timelines and balancing stock availability with demand fluctuations.
Regular Review and Disposal Strategies
Regular reviews and disposal strategies are essential components of effective lifecycle management. By conducting periodic audits, organizations can identify surplus or non-moving stock, enabling timely decision-making on disposal or repositioning. The key characteristic is the systematic assessment of inventory health and alignment with market demands, allowing for agile adjustments in stocking strategies. These strategies benefit the article by minimizing write-down losses, improving warehouse efficiency, and ensuring optimal spare parts availability. Nonetheless, challenges in disposal logistics and environmental impact considerations may pose obstacles to seamless implementation.
Lifecycle Planning for Spare Parts
Strategic lifecycle planning for spare parts involves forecasting product lifecycle stages and aligning inventory strategies accordingly. This proactive approach enables organizations to anticipate part discontinuations, lifecycle extensions, and technology upgrades, ensuring continuity of supply and uninterrupted operational support. The key characteristic is the adaptive planning based on product variations and market dynamics, leading to cost-effective inventory management and enhanced customer service levels. However, challenges such as rapid technological advancements and unpredictable market shifts may require organizations to maintain flexibility and agility in their lifecycle planning efforts.
Continuous Improvement and Monitoring
Continuous improvement and monitoring are vital for sustaining optimal spare parts inventory management practices. By establishing key performance indicators, conducting regular audits, and implementing feedback loops, organizations can proactively identify improvement opportunities, enhance operational efficiencies, and drive innovation in inventory control processes.
Key Performance Indicators (KPIs) for Inventory Control
Key performance indicators serve as benchmarks for evaluating inventory control effectiveness. By tracking metrics like inventory turnover, fill rates, and stockout rates, organizations can gauge their operational performance and responsiveness to demand fluctuations. The key characteristic of KPIs is their quantifiable nature and alignment with business objectives, allowing for data-driven decision-making and performance optimization. In this article, KPIs play a crucial role in enhancing inventory visibility, reducing stock holding costs, and maintaining service levels. Challenges may arise in defining relevant KPIs for specific inventory models and integrating disparate data sources for comprehensive performance measurement.
Periodic Audits and Inventory Checks
Periodic audits and inventory checks are proactive measures to ensure inventory accuracy and compliance. By conducting regular physical counts, cycle checks, and reconciliations, organizations can identify discrepancies, prevent stockouts, and comply with regulatory requirements. The key characteristic is the systematic review of inventory records and physical counts, enabling error detection and process refinement. These practices benefit the article by promoting inventory transparency, minimizing data inaccuracies, and safeguarding against stock discrepancies. However, challenges in resource allocation for audits and reliance on manual processes may limit the scalability and efficacy of audit routines.
Feedback Loops for Process Optimization
Implementing feedback loops enables continuous process refinement and optimization in spare parts inventory management. By soliciting feedback from stakeholders, analyzing performance data, and adapting strategies based on insights, organizations can drive continual improvement and adaptive supply chain practices. The key characteristic is the iterative nature of feedback loops, fostering a culture of learning and innovation within inventory control processes. This approach benefits the article by promoting operational agility, enhancing decision-making based on real-time insights, and fostering a culture of continuous improvement. Challenges may emerge in capturing qualitative feedback effectively and aligning improvement initiatives with overall business objectives.
Conclusion
Summary of Key Takeaways
Importance of Efficient Spare Parts Inventory Control
Efficient spare parts inventory control plays a pivotal role in the overall success of operational functions. By ensuring the availability of critical spare parts while minimizing excess inventory, businesses can operate smoothly and cost-effectively. The key characteristic of efficient inventory control is its ability to balance stock levels to meet demand without causing bottlenecks or shortages. This balance is crucial for maintaining operational continuity, reducing lead times, and maximizing resources for other essential tasks within the organization.
Impact on Operational Efficiency
The impact of efficient spare parts inventory control on operational efficiency cannot be overstated. By managing inventory effectively, organizations can streamline maintenance activities, prevent equipment downtime, and optimize workflows. The key characteristic of this impact is its direct correlation to improved productivity and resource utilization. Efficient inventory control ensures that operations run smoothly, deadlines are met, and costs are minimized, ultimately leading to enhanced profitability and customer satisfaction.
Future Trends in Inventory Management
Looking ahead, future trends in inventory management are poised to revolutionize the way businesses handle spare parts inventory. Key characteristics of these emerging trends include advanced technologies such as artificial intelligence, IoT integration, and predictive analytics. These trends offer substantial benefits such as enhanced predictive maintenance, real-time tracking capabilities, and automation of replenishment processes. While these trends hold the promise of boosting efficiency and reducing operational costs, organizations must also navigate challenges such as data security risks, technology integration complexities, and workforce upskilling requirements in adapting to these evolving inventory management practices.